Throughout the past several months, the ferrous scrap market has seen unprecedented gyrations that have resulted largely in a significant upward trend.
The sharp jump in ferrous scrap prices also has rekindled talk of mergers, as recyclers and consumers try to lock into enough tonnage to meet their needs.
This bull market, many analysts say, will continue for the foreseeable future.
During a report at the recently concluded Institute of Scrap Recycling Industries Inc. (ISRI) 2008 Annual Convention, held in early April in Las Vegas, Eric Glover, an analyst with the investment firm Canaccord Adams, noted that the scrap metal market was in a strong, long-term growth pattern. As a result, the industry has been seeing better pricing and stronger demand for its material.
Prices for various grades of ferrous scrap and many grades of finished steel have jumped significantly during the decade. By way of illustration, Glover said the average scrap price had increased more than 250 percent since 2000.
Despite the well-documented problems in the U.S. economy, the global economy has held up nicely, creating a steady-to-strong demand for the raw materials, such as ferrous scrap, that are used to make steel.
Finished steel is needed to further develop infrastructures around the globe. For instance, demand from Brazil, Russia, India and China (often labeled BRIC countries), as well as the explosion in construction in the Middle East thanks to the infusion of petrodollars, requires steel. In turn, more ferrous scrap is needed in the steel manufacturing process.
During a presentation at the ISRI 2008 Annual Convention, Salam Sharif, president and CEO of Sharif Metals, a scrap metal company based in the United Arab Emirates, highlighted the significant infrastructure development occurring in the oil-rich UAE. The country’s evolution into a modern metropolis has led to a significant increase in its consumption of steel, which is needed to build much of its public works.
This growth is being replicated in other parts of the Middle East, which has helped keep steel mills around the globe running close to capacity.
Supporting the strong increase in Russia, Novolipetsk Steel (NLMK), the fourth largest steel producer in that country, recently noted that it expects steel prices to keep growing in the second quarter of this year before stabilizing during the middle of 2008. NLMK also notes that production among Russia’s steel mills is running at close to 100 percent of capacity.
Along with the jump in demand from modernizing countries, there is a shift among steel makers in some countries toward greater use of electric arc furnaces (EAFs), which require more ferrous scrap than steel production using basic oxygen furnace technology.
A CHANGING DYNAMICThe trend toward EAFs is not limited solely to overseas steel producers. In the United States, most of the newer steel mills coming online are designed with EAF technology. A report from Canaccord Adams notes that while approximately 55 percent of domestic steelmaking capacity presently comes from electric arc furnaces, within the next two years that number could increase to nearly 60 percent.
Additionally, with the manufacturing base in the United States shifting overseas, less ferrous scrap from industrial sources will be available within the United States.
Also, Russia and Eastern Europe, which have been exporters of ferrous scrap, are becoming large consumers of the material, adding to the overall global demand for ferrous scrap. In fact, Russia, the fourth largest steel producer, Canaccord Adams predicts to become a net scrap importer by 2015, as it finds its domestic supply of ferrous scrap dwindling.
Glover noted that Russia could be importing as much as 3 million to 4 million tons of ferrous scrap by 2015, making the country, along with Turkey, a key buyer of the material from the United States and Western Europe.
Anticipating the strength in ferrous scrap prices, many of the top steel producers have hiked prices for their finished product. According to a report by Deutsche Bank, leading flat steel producers have raised their prices for hot-rolled coil to approximately $1,000 per ton, compared to a price of nearly $525 per ton late last year.
These steel companies cite higher raw material costs, including scrap, as part of the reason for the increase in their finished steel prices. Along with higher scrap, iron ore, coal and coke prices, mills cited lean regional and global inventories, tight supplies and reduced inventory levels as contributing to finished steel price increases.
STRONG DEMANDSThe most recent figures from the International Iron & Steel Institute (IISI), Brussels, Belgium, indicate that world steel production increased by 7 percent last year to a total of 1.3 billion tons. The growth was driven by sharp production increases in Asia and China, which saw increases of 12 percent and 16 percent, respectively.
Meanwhile, a Deutsche Bank report notes that 60 percent of global steel demand is coming from China and other emerging markets, which should help improve the floor on prices for this year.
Glover notes that in addition to China, Turkey and Russia are playing more prominent roles in the scrap and steel markets. Turkey, the largest importer of ferrous scrap, is one of the key producers of the steel that is being used in the building boom in the Middle East.
Deutsche Bank also reports that benchmark scrap prices increased in April, with shredded auto scrap reaching $555 per ton compared to $309 per ton in December of 2007. The report quotes No. 1 busheling at $600 per ton compared to $334 per ton in December of 2007. Further, auto factory bundles recently settled at nearly $548 per ton, including the much-publicized $155-per-ton increase in March, compared to the December 2007 price of $298 per ton.
Higher scrap prices are supported by constrained supply from reduced industrial activity in the United States, limited global supply growth, increased demand from U.S. steel mills, growing offshore steel output and demand for scrap in developing countries.
Estimates from Deutsche Bank find that China consumes roughly one-third of the crude steel consumed worldwide last year. This is a doubling from 2000, when China consumed about 16 percent of the entire world’s steel. Adding the rest of Asia to the figure brings the figure to more than 50 percent.
Meanwhile, North American crude steel consumption, as a percentage of global steel consumption, continues to decline. Steel consumption by North America makes up 13 percent of the global market compared to 21 percent in 2000.
A recent report by MEPS International Ltd., a U.K.-based steel market information provider, estimates that world crude steel production this year should increase by approximately 5.6 percent. While still a robust number, MEPS International sees the figure as declining from the previous year’s production growth of 7.6 percent. The group cites a weaker global economic climate as well as an anticipated reduction in the rate of steel production expansion in China for the slower growth.
The MEPS report finds that crude steel output in non-EU Western Europe is expected to expand by almost 10 percent this year. The main driver behind the growth is strong demand and rising capacity for steel manufacturing in Turkey. MEPS says this growth will continue, with high levels of investment continuing through the next four years. "Much of the growth in output is still related to the construction sector," the MEPS report states.
LINKING UPReflecting the expectation that higher ferrous scrap prices could be the norm, there have been several large acquisitions. While the scrap industry has been consolidating throughout the past several years, two fairly recent deals may point to concerns on the part of steel mills that higher prices and an uncertain supply stream could present challenges: Nucor’s acquisition of David J. Joseph and Steel Dynamics’ acquisition of OmniSource.
Many steel analysts say these two steel producers are operating nimbly. Their business moves have helped to bring greater attention to the trend toward mergers and acquisitions, especially vertical integration, as steel mills acquire scrap metal recyclers to gain better access to raw materials.
High-profile vertical acquisitions of scrap facilities by steel producers, however, are not limited to U.S. companies. Late last year Novolipetsk Steel acquired more than half of the Russian firm Maxi-Group. Aleksey Lapshin, NLMK’s president, noted that the move would lead to NLMK’s 100 percent self-sufficiency in steel scrap, which is an important competitive advantage, given projected higher scrap prices in Russia.
However, as EAF operators, these mills are far more dependent on ferrous scrap as a key raw material, as opposed to more traditional basic oxygen furnace mills.
While many observers postulate that the steel companies can acquire ferrous scrap at a far cheaper price as a result of this merger activity, scrap prices continue to escalate. Instead, these mills appear to have a better guarantee that they will be able to source enough scrap material, regardless of price.
Although ferrous markets are benefiting significantly from the global market, the domestic steel industry in the U.S. also shows promise. The Canaccord Adams report notes that several newer facilities are slated to come online in the United States, including projects by SeverCorr, ThyssenKrupp and MMK. According to the consulting firm, these three mills will require an additional 9 million tons of ferrous scrap per year.
While consolidation will likely continue in the metals recycling industry, there are relatively few scrap companies of enough size and scale to make a significant impact on raw material supplies.
As a result, steel companies may look to go deeper down the vertical chain to acquire smaller operations. The Canaccord Adams report notes that with access to raw materials becoming increasingly important for steelmakers, there will be a greater trend toward vertical integration, with a number of smaller deals helping to fill out companies’ regional portfolios.
On a global scale, demand for ferrous scrap is expected to continue to grow, as shortage situations develop in many of the steelmaking countries and U.S. supplies become more challenging.
With such a bullish outlook for the industry, the biggest concern for ferrous scrap processors is being able to get enough material to meet their supply requirements. Going forward, the field could become even more competitive.
The author is senior and Internet editor of Recycling Today and can be contacted at dsandoval@gie.net.
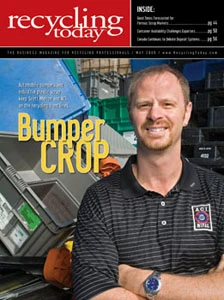
Explore the May 2008 Issue
Check out more from this issue and find your next story to read.
Latest from Recycling Today
- Nucor receives West Virginia funding assist
- Ferrous market ends 2024 in familiar rut
- Aqua Metals secures $1.5M loan, reports operational strides
- AF&PA urges veto of NY bill
- Aluminum Association includes recycling among 2025 policy priorities
- AISI applauds waterways spending bill
- Lux Research questions hydrogen’s transportation role
- Sonoco selling thermoformed, flexible packaging business to Toppan for $1.8B