If there is one piece of processing equipment central to a recycling operation, it has to be the baler. Without its ability to compact material into dense, easily stacked packages, recyclers simply could not move their material cost effectively. It is also a piece of equipment that crosses over nearly all secondary commodity markets, including paper, cardboard, plastic, and ferrous and nonferrous metals.
There are basically four types of balers: horizontal, vertical, single ram and two ram. Briefly, in a horizontal baler the ram motion is parallel to the floor. In a vertical baler the ram motion is perpendicular to the floor. A single-ram or extrusion baler uses the compression device to also push the bale along the extrusion chamber and eventually out; and a two-ram baler uses one ram to compress the material, and another one to eject the bale.
In general, the basic operation of a ram compressing material into a bale has not changed; however, balers continue to evolve in areas that effect operating efficiency, such as energy management, anti-jamming devices, and other areas that improve the speed, density and sizing of bales.
SCRAP METAL COMPACTORS |
Transporting bulky white goods and other metals is made easier with a baler that can efficiently compact the material directly onto a self-dumping trailer. Harris Waste Management Group, Peachtree City, Ga., has a device on the market called the TransPac which is designed to do this. In addition, earlier this year SSI Shredding Systems, Wilsonville, Ore., introduced its Scrap Metal Compactor. These stationary balers are designed so that a trailer can be positioned at the bale discharge point. When a bale is ready, the ram pushes the bale directly onto the trailer bed. The SSI system, for example, can make a 25-cubic-yard bale that is about 17 feet long and weighs about 20,000 to 22,000 pounds. Two of these bales will normally fit on a standard trailer. The bale is loose and will flake off so that the material can be effectively processed in a heavy-duty shredder. |
TWEAKING ENERGY SAVINGS
Like an automotive engineer trying to squeeze out another mile per gallon from the next generation car model, baler engineers are targeting drive systems, hydraulics and material usage to achieve the best efficiencies possible in their designs.
"The biggest advancement in balers will continue to be efficient energy management," says Joseph Szany, waste division sales manager for Lindemann Recycling Equipment, Charlotte, N.C. "A more energy-efficient baler can bale two and sometimes three times the amount of material using the same amount of kilowatt energy."
One way to increase efficiency is to limit excessive torquing on the motor that drives the ramming device. "If a system is taxing the motor beyond its rated capacity, it is not using energy wisely; so our mission has been to bring that excessive torquing down," says Szany.
Erik van Dijk, vice president of Van Dyk Baler, Stamford, Conn., agrees that energy efficiency is important. "There are many areas in which balers have been upgraded recently, including not only better motor designs, but also more efficient flow of oil and hydraulic fluid. This has been achieved mainly by advances in pumps."
Others, such as Bryan Fisher, owner of Excel Manufacturing Inc., St. Charles, Minn., compare baler advancements to car engines. "The basic principle in a car engine is the same, but the inherent design makes one produce 200 horsepower while the other one can only yield 100 horsepower."
The rule of thumb that Richard Harris, vice president of American Baler Co., Bellevue, Ohio, uses to calculate the cost of baler operation is $110 per year per unit of horsepower for a baler. "Normally, that is what it costs to operate a baler," he says. "Now, if you can knock off $10 or $20 dollars from that ratio, the savings begin to add up quickly."
But Fisher says that you can only go so far in tweaking motor performance. "There are efficiencies that can be achieved through mechanical design, but you are always going to need a certain level of horsepower to make a bale and achieve the densities that are needed."
Another area that involves energy efficiency is the actual use of electricity. Some balers are now being fitted with energy savers that sense when material is not being loaded into the hopper. During those times, the baler goes into an energy saving mode – much like a screen saver on a computer. Technically, all systems are still on, but the baler is drawing the minimum electricity necessary to remain operating. Or, in another configuration, motors would be sequenced so as to limit the use of electricity, thereby being turned on only when more power is needed.
"By sequencing the motors on the baler, which can sometimes include up to four motors, and using special circuits, the spikes in electrical current that usually are associated with AC motors can be eliminated or reduced," says Harris.
Efficiency ratings of motors in the U.S. may soon be regulated as the government looks to establish a standard efficiency rating system instead of leaving it up to the individual manufacturer, he adds. Already, Canada has adopted such legislation.
Finally, newer, stronger steels are being used to increase the life of baler parts. One area where this is evident is in the lining of baling chambers. Companies are using steel that is both harder and slicker so that the ram can move more effortlessly and the liner lasts longer.
"The newer materials are hard all the way through, and not just at the top," explains Szany. "We are now using a steel with the trade name Hardox 500 that has a Brinell hardness of 500. The material we used before had a hardness factor of only 300."
Liners are normally less than an inch thick and some are laid in alternating strip heights. The alternating heights help prevent material from jamming the ram and also guide the ram in the chamber, because the ram, too, is lined with alternating height strips, but the strip heights are opposite the chamber walls so that the ram engages the grooves.
The strips themselves are an innovation because it allows the ram to remain in place during a liner change out.
Some balers, however do not have liners, and van Dijk explains why. "In our baler there is no shearing, and because of that the ram moves on wheels, and not on a liner; therefore, you do not need a liner and there is less wear and tear."
ANTI-JAMMING DEVICES
When a baler jams, productivity sinks. Preventing baler jams has a lot to deal with operator education, but today many balers are designed to operate hands-free or in some type of automatic or semi-automatic mode. So preventing a baler jam has much to do with the overall design of the equipment. Most manufacturers have addressed the concern of baling jams in one way or another.
There are basically two types of jams that can happen. The first one occurs in the baling chamber. "This happens when too much material is compressed and the ram cannot eject the bale," says Buck Hughes, president of Hughes Consulting Service, Lady Lake, Fla., who has been involved in the recycling industry for more than 20 years. "What manufacturers did is add a release mechanism that would retract one of the walls of the chamber enough so the bale could move forward."
Some companies employ a release mechanism that bows the middle of the extrusion sides outward so the bale can move forward. American Baler, on the other hand, has recently developed an "H" style extrusion chamber that compresses the bale from the sides and the top, but when a stall condition is about to happen, the mechanism releases both sides and the top enabling the bale to proceed through.
"The benefit of this is that denser, more even bales can be made," says Harris. "The chamber is able to hold onto the material longer, and is able to bale very slippery grades of material."
The other type of jam, according to Hughes, occurs in the charge hopper. "Sometimes material can get caught between the ram plate and the stationary shear knife," he says. "There are two innovations that solve this problem. One is making the shear knife saw toothed or in stages, so the material hits parts of the blade at different times, effectively cutting the material. The other method involves a ‘tramper’ or ‘stamper’ that pushes the material down enough so that the ram can push through the chamber."
Although these devices are not new, they have received renewed attention lately because they are now being added to two-ram balers, whereas they were previously only common on one-ram systems.
Many companies are now adding these push-down devices simply because it increases the efficiency of baling. "A lot of the energy is expended to bale when material needs to be sheared off at the shear beam," says van Dijk. "But if you can push that material down, you save money in electrical costs."
The push-down device in some balers can also be programmed so that when it receives a signal that the baler is jamming, the ram retracts and the stamper comes down and pushes the material below the shear beam. Onboard computers are doing a better job of automatically sensing when a jamming situation is occurring, so they may instantaneously retract and recycle the ram without the operator knowing it. Stampers are also important for safety reasons, say manufacturers, because they keep people out of the baler.
The stamper can serve as a clamp to hold the bale into position and help square it off, and it can also be used to create target bales of 38, 40 and 42 inches in height.
Material intake is also key to preventing jams in the first place, according to Fisher. "We control the rate of material into the machine," he says. "If you can do that adequately, you don’t need any type of lid or stamper. The key is not to let the baler ever get into a jamming situation. We have electronic triggers in our baler that sense the distance and level of the incoming material. So when the correct level and load is achieved then the ram cycles."
There are still more methods for preventing jams. Stephen Kingeter, vice president of sales and marketing for Harmony Enterprises, Harmony, Minn., says his company has a photo-eye system that automatically detects whether the baling chamber is full or empty, helping prevent jams and giving the proper signal to stroke or retract the cylinder.
DENSITY, SIZE, SPEED
With the preponderance of baling companies and types of balers, its understandable that there are differences in opinion as to what is the most important feature of a baler, and where to concentrate improvements. Some say speed is the most important; some say density; while others point to proper sizing.
"We are at the point now where speed in baling is becoming more important," says van Dijk. "If a processor can bale faster, he can move more material."
Bale densities today are more than adequate, says Szany. "We have found that if bale densities go up, the cost of the machine goes up exponentially – up to 30 times more just to double the bale density. What we are focusing on is reducing the overall cost of baling, and the best way to do that is to reduce electrical and wire costs."
But others, like American Baler’s Harris, still say density is important. "Mills want heavy, dense bales, and if you can provide denser bales there is an advantage," he says. "That means less wire usage, and fewer trips back and forth with the forklift."
Harris Waste Management Group, Peachtree City, Ga., just introduced a new two-ram model that focuses on density. The company says that the compression ram can penetrate into the compression chamber at 50 percent providing for denser bales. The baler control system also allows the operator to customize 20 different materials by changing seven baling parameters per material.
Another upgrade with the Harris baler is a short-stroke option. When the baler nears the end of the bale, the baler will automatically short stroke to finish the bale off at the proper length.
Proper sizing is also key, according to Fisher.
"It's ideal to have something like 40 bales at 40 feet high at 40,000 pounds," he says. "If you are making a bigger bale and the density is less, you lose something there because the bale doesn’t weigh enough and you are not truly maximizing your outbound load."
Van Dyk Baler sells a baler that can produce a 45-inch by 45-inch bale, and van Dijk says that’s important because "you can load fewer bales for shipping but keep the same volume, and, over time, that means fewer forklift trips."
Lindemann has also focused on bale sizing through the use of a new Versa Door. The door comes down through the baling chamber and allows a separation of one type of material from another. It also allows for the creation of an oversized bale. "If you have 50 or 100 pounds of material left over, it’s not enough for another bale, so the door allows you to add that extra material to the existing bale," says Szany. "With this feature, bales can be oversized by 25 percent, or about 9 inches larger than the target bale size."
Density and bale sizing are important because they directly effect the use of baling wire. Typically, a processor pays about $1.20 to wire a bale of OCC. If that bale weighs about 1 ton, and the processor is baling 3,000 tons a month, the cost for bale wire is $3,600 a month and $43,200 a year. Over a 10-year period, that amounts to $430,000, which can be about twice as much as the baler cost originally.
The baler also has to use the correct number of wire ties – the number varies depending on the type of material being baled. If excessive wire is being used, wire costs could skyrocket. Many companies are now managing wire through an automated tying feature that sets the correct number of wires and spacing so that the bale is tied off efficiently.
FUTURE TRENDS
The trend in the U.S. during the last few years has been toward the large single-ram balers, according to Hughes. "Material recovery facilities really like the single-ram ones because of the throughput and because they use less electricity than two-ram models," he says. "They also have a large throat to handle corrugated."
This is true, agrees Szany, but he notes that the two-ram style is gaining in popularity because of the recent upgrades. "It has been going back and forth, but now I think the two-rams are taking the lead," he says.
The future of balers may also involve bar coding and tagging bales. Although this would enable processors to know immediately what the material is, where it came from and the weight, there are some concerns about keeping the tag on the bale so that it can be properly read and the bale identified. "Right now we can store all the information in an onboard baler computer, but we have yet to find a way to transfer it effectively into or onto the bale," says van Dijk.
Another challenge to bar coding right now is being able to switch the coding when the material changes, according to Harris. "We are looking at this technology, but it really has to be demanded from the customer first," he says.
Currently, it seems, there is little demand for bar coding, despite the convenience it could offer. "I just do not see any real benefit from implementing bar coding for bales," says Steve Flanagan, Southwest regional manager for Rock-Tenn Recycling, Dallas. "There may be some benefit in inventory control, but we already operate pretty well in that area. The only other area would be tracking quality control. But we have been without bar coding for so long that I am not sure that the effort to implement it matches the benefits it would bring."
Fisher is also not confident that bar coding bales will happen, either. "We developed a system that ink-jetted data directly on the bale, but no one was really interested in it, and it was very expensive to implement."
Instead, down the road, Fisher has a vision for the next generation baler that will feature better sensors, hydraulics, valving and knife shapes and will be able to build a better bale.
Others see balers being able to provide the user more information about their operating parameters and being integrated into a larger processing scheme. Lindemann is presently in the midst of a large-scale project with Jefferson-Smurfit Recycling, St. Louis, to install a new control system that would encompass several balers and sequence more than 70 different motors. The system would track baler strokes, wire management, numerous baling categories and other parameters to make the operation as efficient as possible.
FLEXIBILITY
Today, recyclers need balers that are flexible and can change between materials, according to Hughes. They also need to bale at the lowest cost per ton possible. "My number-one advice to the processor is to make sure that you match your throughput with that of the baler," says Hughes.
"Everyone has a good system today," he continues, "and I don’t foresee the baler changing that much in the near future. What will change is the pre-preparing of material prior to baling and the use of sorting systems that will automatically feed balers. Large MRFs are very expensive to operate, and the one way to reduce costs is to remove the manual labor and automate."
"My best advice is to buy a properly configured baler," says Excel’s Fisher. "Always look for quality and consider cost, but match the baler to your needs. A lot of the older processors that have been in the recycling business for a long time – look at what they are using. They have large, two-ram balers because those balers are the most versatile, and they have balers with large feed openings so that they can bale a wide range of bulky material."
Recyclers should look for a baler that doesn’t have options, but comes with the items that are needed as standard, he says. "Bells and whistles and fancy options may seem nice in the showroom," says Fisher, "but the reality is that on the floor you need a machine that is easy to operate and easy to understand. You don’t want your operator having to push a lot of buttons. Plus, an option is just a fix for something that isn’t right in the first place."
Buy a baler that fits your needs, recommends Doug King of Quality Recycling, Horse Shoe, N.C. "I know that sounds obvious, but there are a lot of people out there who think they are knowledgeable about balers, but are not. You have to sit down and figure your costs over the long-term, what the payback will be, and how much electricity and wire cost you are going to have. Don’t overextend yourself and buy a baler that will end up eating up all of your profits."
Manufacturers also caution against limiting your options by buying a baling setup that is too specific. One metal processing company bought a baler for its nonferrous division and installed a permanent magnet. Although the baler has doubled the company’s shipping capacity of aluminum, it cannot be used to bale tin or light ferrous. "In hindsight, I wished we had bought a system that had an electromagnet instead of a permanent one," says the plant manager for the company. "With the electromagnet, you can shut off the magnetic field."
The life cycle of balers is definitely getting shorter, according to many manufacturers, who say that companies can no longer sit back on technology and designs that were popular 10 or 20 years ago. They point to an industry that is beginning another round of significant design upgrades, most of which will revolve around making the baling process more cost effective for the processor.
The author is managing editor of Recycling Today.
Get curated news on YOUR industry.
Enter your email to receive our newsletters.
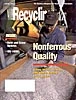
Explore the August 1996 Issue
Check out more from this issue and find your next story to read.
Latest from Recycling Today
- ReMA opposes European efforts seeking export restrictions for recyclables
- Fresh Perspective: Raj Bagaria
- Saica announces plans for second US site
- Update: Novelis produces first aluminum coil made fully from recycled end-of-life automotive scrap
- Aimplas doubles online course offerings
- Radius to be acquired by Toyota subsidiary
- Algoma EAF to start in April
- Erema sees strong demand for high-volume PET systems