
Safety is a good reason to add a breakaway coupling to an automobile shredder. It was the main aspect that prompted City Scrap & Salvage, Akron, Ohio, to incorporate a breakaway coupling to its shredder’s universal joint shaft.
Without a breakaway coupling, a driveline failure could be deadly if a shredder operator happens to be present. When the u-joint shears apart, it often does so violently and explosively. If workers fail to recognize the early warning signs—such as a change in operational noise, vibrating equipment or a sudden line stoppage—they could face serious consequences.
The need for breakaway couplings comes from a simple fact: Material going into a shredder is never consistent, and sometimes objects cannot be broken down by the system’s hammers. When that happens, the hammers jam and the driveline fails—often catastrophically—which can create an economic toll on an operation. Even worse, driveline failures can sometimes put workers in harm’s way if components in the driveline burst into pieces.
Unshreddables—such as cement chunks, propane tanks, high-density metal and wire bundles—are typical problem items that can be hidden inside junked vehicles sold for scrap. A shredder will tear through an engine block with no problem, but refrigerator doors and mini safes hidden inside a trunk (often used to add weight by sellers) can stop an entire system within moments.
Whatever the item is that the shredder encounters, the aftermath matters most to metals recyclers—a total and sometimes disastrous shutdown that could cause injuries to workers.
Disaster avoided
Neil Smith, ferrous operations yard supervisor at City Scrap & Salvage, recalls one near-miss incident he encountered while working as a shredder operator. He says it all began when an unshreddable object got inside the shredder system.
“It hit and banged around in there until we were able to get it out of the bang-out box,” he says. “After that, we noticed a vibration, so we stopped operation.”
Immediately after the incident, Smith says he left the tower to check on any issues that might have occurred in the engine room. Approaching the door to the engine room, he saw a worker standing there, peering inside the engine room from the doorway.
“Inside, the jack shafts were still spinning because the rotors were still spinning,” Smith says. “One of the jack shafts had bumped and was spinning free from the rest of the shaft. It was bouncing around and sparking.”
As the 1,000-pound piece of equipment continued to rotate out of control, Smith says he glanced at what else was going on. “It was wobbling around in there, just barely able to stay in place with guarding and belts that hadn’t already been ripped apart.”
Smith adds that the worker by the doorway just stood there in amazement, unsure of what was going on. Smith, however, says he knew exactly what was happening. “I told him to run. We both got out of the way fast.”
Within minutes, Smith says he could hear that the spinning had stopped. After going back to the engine room, he says he saw that the jack shaft had managed to stay together—barely. The danger was over, but the lesson remained on Smith’s mind.
“Had that shaft broke free, the worker or myself could have been severely injured or even killed,” Smith adds. “This is not machinery you want flying around.”
Although Smith and his co-worker avoided getting hurt that day, the incident still counted as a driveline failure. It would cost City Scrap & Salvage. If the incident had resulted in an injury or death, the financial impact on the company would have been even steeper as a result of medical expenses and potential lawsuits.
Risky incidents such as this encouraged Smith to install a breakaway coupling at City Scrap & Salvage. Others in the industry also recognize the safety breakaway couplings add to shredders. The Institute of Scrap Recycling Industries (ISRI), Washington, notes the importance of breakaway couplings in new recommendations for shredder safety listed in the Safety Point section of one of its “EHS Update” e-newsletters. ISRI adds that breakaway couplings can protect some equipment during a major jam.
An economical option
Breakaway couplings offer many advantages. Jim Fraser, product sales manager, Americas, Voith Turbo Inc., with U.S. headquarters in York, Pennsylvania, says breakaway couplings are economical, as well.
“From an economic standpoint, and also from a safety standpoint, couplings are a great investment for shredder operators,” Fraser says. “You prevent driveline damages and shredder downtime while improving safety.”
Driveline failures can be very costly for recyclers. Downtime for repairs costs thousands of dollars per hour because of lost production. Operators also must replace the components that failed—and that sometimes includes an expensive motor replacement, too.
The universal joint shaft, however, is the most vulnerable (and valuable) piece of the driveline when an unshreddable hits a system. This is because when the torque generated in the engine has no place to go, it twists the u-joint to the breaking point. This disastrous release of torque satisfies the laws of physics, but it also wrecks a recycler’s budget because replacement costs are so high.
Some recyclers prepare for driveline failures by stocking spare u-joints and consider it part of the cost of doing business.
“Even when they lose a motor, they put up with the downtime despite the costs,” Fraser says. “But using a breakaway coupling is the smart, economic way to protect an operation.”
Neither the cost of warehousing spare equipment or extended downtime is a necessary sacrifice now that breakaway couplings have become available for use in the metals recycling industry. These are long-proven (for more than 20 years) as standard equipment with some shredders and in hundreds of steel mills, as well as in crushers and other heavy-duty applications.
How they work
Breakaway couplings protect drivelines from unexpected overloads. For metals recyclers, they are the answer to problems caused by unshreddables.
The torque-limiting coupling protects against overloads and allows driveline equipment to function safely while operating at high levels. The breakaway coupling disengages the driveline before peak and dangerous torque is achieved. During a high-torque event resulting from an unshreddable, the coupling slips, shears the shear tube and instantly disconnects the driveline. The oil pressure inside the coupling drops, frictional surfaces separate, and the breakaway coupling rotates on bearings without transmitting torque through the driveline, saving it from damage.
Resetting the breakaway coupling after an incident is simple. A new shear tube is installed, oil is refilled, and the system is pressurized and resealed. City Scrap & Salvage can do this procedure in a matter of 10 minutes.
“From a safety standpoint, it’s a priority value,” says Steve Murphy, plant manager at City Scrap & Salvage. “To have something [like this] gives me comfort to know we are not going to put our associates at risk. We are not going to have a spindle snap and fly out when an unshreddable hits.”
_fmt.png)
Customizable couplings
Breakaway couplings usually need to be customized to each operation.
“One of the major questions we get is ‘Will it release too frequently?’” Fraser says. “Operators are concerned they’ll get hit with constant shutdowns.”
Fraser says a breakaway coupling runs reliably for the life of a shredder, protecting the shredder’s driveline and workers’ safety with the same accuracy as when it first started.
“We know going in what the torque is that can break a shaft,” Fraser says, adding that Voith’s SafeSet is customized to be able to determine the shaft’s torque threshold. The company then designs the product around that threshold.
The result is an investment that can pay for itself in one unshreddable instant—especially when it also serves as a safety device. For now, it’s up to the industry to demand breakaway couplings. Given the safety and production issues caused by driveline failure, these can be a worthy addition to all shredders.
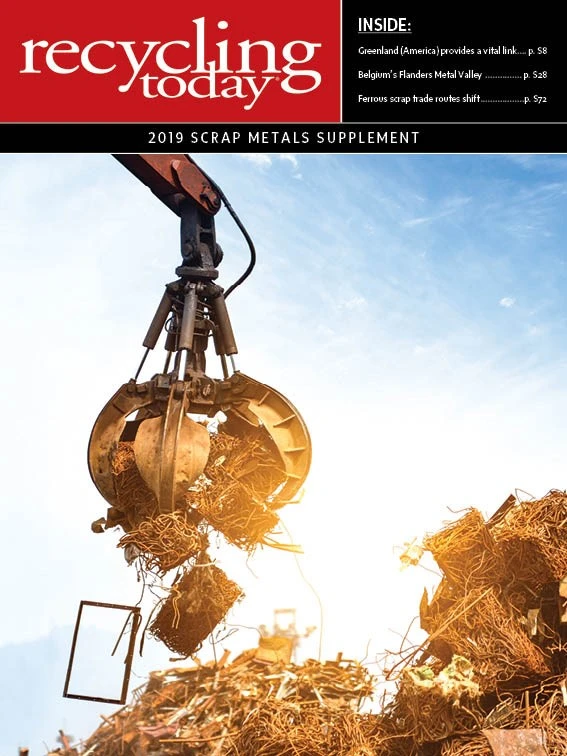
Explore the January 2019 Scrap Metals Supplement Issue
Check out more from this issue and find your next story to read.
Latest from Recycling Today
- AF&PA report shows decrease in packaging paper shipments
- GreenMantra names new CEO
- Agilyx says Styrenyx technology reduces carbon footprint in styrene production
- SABIC’s Trucircle PE used for greenhouse roofing
- Hydro to add wire rod casthouse in Norway
- Hindalco to invest in copper, aluminum business in India
- Recycled steel price crosses $500 per ton threshold
- Smithers report looks at PCR plastic’s near-term prospects