Rapid inventory turn-around in scrap yards and the controlled demolition trend in that industry are among the factors boosting the sale of mobile shears and other attachments that do more than simply move scrap material.
Without question, the scrap boom is causing grapples and lifting magnets to work overtime just as much as any other equipment in a scrap yard. And stationary processing equipment—from the alligator shear to the super-sized shredder—is humming along nicely in most regions.
But a growing number of orders have also been placed for mobile shears and multi-functional variations of this hydraulic attachment that are used by demolition contractors and the scrap processors who handle demolition scrap.
INSIDE JOB. Demolition contractors use compact excavators and skid steers outfitted with a variety of attachments to perform "infrastructure" demolition, or the removal of plumbing and heating and electrical systems within a building.
"In controlled demolition the contractor will normally remove any material with salvage value, such as wires, conduits, pipes and electrical equipment, using small shears and grapples on skid-steer loaders or mini- or standard-size excavators," Poul Rosengaard, senior application engineer for Caterpillar Work Tools, Peoria, Ill., says.
TIRES KEY TO MOBILITY |
Tires used in a recycling yard have a life expectancy similar to the flag-bearer in old-time battle formations, and they face almost as many hazards. But the life span of the tires can be extended. The general environment, cleanliness of the operating area and the operator’s skill all affect tire life. "Turning has a lot to do with it," says Robert Gilkenson, Atlanta, Ga.-based sales manager for Airboss Tires. Airboss is among several companies, including solid tire pioneer SETCO of Idabel, Okla., offering solid tires for use in harsh environments. Gilkenson says abrasion resistance, chipping resistance and resistance to heat buildup determine tire life. A semi-solid tire on a skid-steer loader will last an average 1,500 to 2,000 operating hours, he says. "The more expensive product will be more highly engineered," he adds. Gilkenson says one of the key features to look for in a tire is cut resistance. "Cut resistance is the main thing in a scrap yard. You want something that is not going to chunk or rip." Jerry Van Vlack, president of Airboss Tire Group, says that solid tires are typically the best bet for a recycler. "We advocate a semi-solid segmented tire or solid tire," Van Vlack says. Segmented tires offer cushioning for operator and machine. If a segment is damaged, it can be replaced. Be aware of tire diameter when replacing tires. "In all-wheel drives, the same axle must have the same size tire, and it’s better to have the same size on all four," he says. "Otherwise you put a tremendous strain on the drive line and hydraulics." Finally, Van Vlack recommends selecting a tire with little or no tread pattern. This is especially true of machines operated on concrete or asphalt pads. "If there is a lot of mud, you will need some tread for traction, but get as little as possible." Treadless tires have fewer places for litter to get between lugs. —Curt Harler |
"Due to the compact size, low weight and speed of skid-steer loaders, these machines are becoming much more popular in demolition applications," Rosengaard continues. "Also, with the ever-increasing versatility and great selection of work tools available for the skid-steer loader, they are widely used in selective demolition jobs, like refurbishment of residential and office buildings. The use of skid-steer loader machines and the appropriate work tools are often needed when working within the city limits."
In addition to demolishing structures, demolition contractors face a variety of recycling-related tasks, including the primary sizing and separation of material. This necessitates a number of tools, though just how many depends on the size and nature of the job and the time constraints a contractor faces, Cat's Rosengaard says.
Kevin Loumas at West Springfield, Mass.-based Atlas Copco, says the use of these carriers, equipped with either hydraulic hammers, grapples, shears or pulverizers, has increased greatly during the last eight years.
"They have a variety of attachments, plus they are light and they can work in confined areas, especially the compact excavators," Tom Witt, director of sales for Breaker Technology Inc., Thornbury, Ont., says.
While he says compact excavators are nice because they can sit in one spot and reach around to demolish the surrounding areas, a skid steer equipped with a bucket is ideal for picking up material and loading it out.
The two carriers, equipped with various attachments and used in combination, could provide contractors with an expedient solution for interior and infrastructure demolition tasks.
YARD WORK. At the scrap yard, recyclers eager to process incoming demo scrap efficiently to fill waiting orders have turned to mobile equipment with attachments to help increase production.
Cleveland Scrap, a metals recycling firm named after its home city in Ohio, has used such techniques exclusively in 2004 to handle its stream of ferrous scrap, which consists mostly of demolition scrap.
According to the company’s Allen Youngman, several hydraulic handlers equipped with various attachments are preparing the scrap for quick processing turnaround without the use of any stationary processing equipment.
Shears are also common on demolition jobs that include steel-intensive structures.
"If there is a lot of steel, the perfect solution is a steel cutting shear with 360-degree rotation. It is almost vital to have that rotation so you can work at every angle," Kevin Bakke, chairman of Genesis Equipment & Manufacturing, Superior, Wis., says. "A rotating shear sized to the job is priceless."
Scrap recyclers and demolition contractors using such attachments can be aided by innovative change-out systems that facilitate attachment changes. Bakke says more and more contractors are making use of quick couplers.
Operators of carriers equipped with hydraulic quick-couplers don’t even have to leave the cab to change attachments. "He just flips a switch, unlocks one attachment and goes for the other," Bakke says. "That can be as quick as a one-minute change-out."
Mechanical couplers require that the excavator operator leave the cab to remove a few pins from the current attachment and insert them in the new attachment, but the job can still be performed in five to 10 minutes.
The authors are editor and associate editor of Recycling Today. They can be reached at btaylor@gie.net and dtoto@gie.net.
Get curated news on YOUR industry.
Enter your email to receive our newsletters.
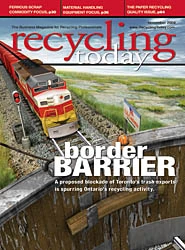
Explore the November 2004 Issue
Check out more from this issue and find your next story to read.
Latest from Recycling Today
- ReMA opposes European efforts seeking export restrictions for recyclables
- Fresh Perspective: Raj Bagaria
- Saica announces plans for second US site
- Update: Novelis produces first aluminum coil made fully from recycled end-of-life automotive scrap
- Aimplas doubles online course offerings
- Radius to be acquired by Toyota subsidiary
- Algoma EAF to start in April
- Erema sees strong demand for high-volume PET systems