In business, there’s a cheap way to do things, there’s an easy way to do things, and there’s the right way to do things. Demanufacturing electronics isn’t the cheapest, nor is it the easiest way to process materials, but I believe it’s the only way to truly recycle all components of obsolete electronics.
When a computer is shredded, as much as 30 percent of the end product cannot be reclaimed. When lead, glass, mercury, plastic, steel, aluminum, copper and brass are commingled, all of the materials are at risk for contamination.
Many companies use shredding because it allows them to process a larger volume of materials. Shredders process a mixed range of equipment to recover different types of materials, primarily metals. Many shredders produce a shredded ferrous metal product and a mixed nonferrous metal product. This process can create a hazardous waste stream by commingling the nonhazardous recyclable materials with hazardous components (i.e. lead, mercury, cadmium and bromides). Shredders also produce a byproduct waste stream consisting of dirt, glass, rubber and plastics, referred to as “fluff,” which unfortunately, typically gets landfilled.
BENEFITS OF DISASSEMBLY
On the flipside, when a computer is demanufactured, materials are separated to ensure they can all be properly recycled. The plastics get grouped with the plastics, the aluminum with the aluminum, glass with glass and so on. The demanufacturing process we have developed at Intercon Solutions is designed to ensure zero commingling of materials and zero contamination. This gives us the ability to ensure that no materials are exported or landfilled. Demanufacturing electronics for re-use as raw materials is 100 percent pure recycling at its finest. Demanufacturing allows for domestic recycling of these components and removes potential cross-contamination issues.
Using demanufacturing, Intercon is able to extract raw materials that most domestic refiners can accept, meaning these items are processed domestically to high environmental standards.
And it’s not just the environment that benefits from demanufacturing, because, while the process is more expensive than shredding, the economic payoffs for the community can be substantial. At Intercon Solutions, we hire employees to process electronics, creating jobs and stimulating the economy. Unemployment rates have skyrocketed to more than 10 percent by some estimates, but hiring laborers to demanufacture electronics can stimulate economic growth. At Intercon’s main warehouse in Illinois, many newly hired members of our labor force come from nearby communities and were previously unemployed.
Additionally, Intercon contributes to economic growth right here in the U.S. by selling material to domestic refiners, stimulating domestic manufacturing. It is impossible to manufacture products without the raw materials and metals that are needed.
Additionally, by demanufacturing electronics to recover the metals they contain, we do not need to mine for new raw materials. Not only is this the best option for the environment but it also can be a safer way to extract raw materials, as the mining accidents of the last year can attest to.
Using manual labor, our company has created many jobs, which in turn helps stimulate the local economy. In addition to the health of the economy, the health of laborers is a primary concern at Intercon Solutions.
EMPLOYEE SAFETY
Safety is key, and the employees at Intercon Solutions perform their task of physically breaking down electronic equipment to raw materials using air hammers, screwdrivers and air drills according to Intercon’s OHSAS 18001 program. This program utilizes OSHA (Occupational Safety and Health Administration) standards and incorporates a multitude of safety precautions.
We believe that demanufacturing is the safest way to recycle electronics, especially for those charged with doing the manual labor involved in recycling.
Our company has gone to great lengths to show our clients our commitment to environmental and worker safety. Our certifications include ISO 14001, an environmental management system; ISO 9001, a quality management system; and OHSAS 18001, an international standard that indentifies necessary requirements relating to health and safety management systems. Earlier this year, we also became AAA Certified from the National Association for Information Destruction (NAID), meaning our demanufacturing facility passed the security audit requirements to be certified for information and data destruction. Our R2/RIOS (Responsible Recycling/Recycling Industry Operating Standard) certification sets out commonly accepted practices for the electronics recycling industry. R2/RIOS is a management system standard specifically designed for the scrap recycling industry as a system framework for recycling plants to use to achieve measurable continual improvement in their quality, environmental, health and safety performance. We have also initiated the e-Stewards certification program and expect the certification process to be completed soon.
Because employees at shredding facilities can be exposed to airborne debris containing lead and other hazardous substances, they are required to be monitored and tested for lead exposure and to wear respirators as well as other personal protective equipment (PPE). The respirator cartridges and PPE must then be disposed of as hazardous waste.
We have tested for levels of debris in our facility and are safely within OSHA limits. It’s not just the well being of our employees we’re protecting; rising health care costs often cost taxpayers.
COST ANALYSIS
It’s true that the process of demanufacturing costs more than shredding, much like a Cadillac costs more than a Yugo. But smart business people know that smart investments do pay off in the long run. The automated process of shredding requires a major capital investment associated with a wide range of equipment consisting of the shredder, conveyors and sorting and air collection systems. This costly equipment can result in a lengthy return on investment. Additionally, because of the lengthy installation process, by the time the machinery is ready to use, there may be newer, more efficient models available. Maintenance shutdowns also can add to the escalating operation costs of such systems.
When considering e-scrap, it is important to know that 100 percent of the materials used to manufacture electronic equipment can be recycled and kept out of shredding operations and—most importantly—landfills. At Intercon the electronics recycling process consists of demanufacturing and concentrates exclusively on the recovery of raw materials for use in domestic manufacturing. The process greatly helps in the reduction of mining of raw materials. Demanufacturing methods can be environmentally safe with no unnecessary threats to worker safety, and they allow our company to achieve our goal of zero waste.
Intercon Solutions recycles millions of pounds of material annually and, by sending that material to certified domestic manufacturers as raw materials, we are able to recycle 100 percent of the electronics we touch.
Brian Brundage is the CEO of Intercon Solutions, www.InterconSolutions.com, an electronics recycling company based in Chicago Heights, Ill.
Editor’s Note: The views expressed in this feature are not necessarily those of Recycling Today magazine.
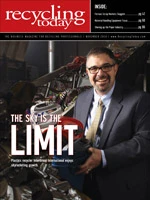
Explore the November 2010 Issue
Check out more from this issue and find your next story to read.
Latest from Recycling Today
- ReMA board to consider changes to residential dual-, single-stream MRF specifications
- Trump’s ‘liberation day’ results in retaliatory tariffs
- Commentary: Waste, CPG industries must lean into data to make sustainable packaging a reality
- DPI acquires Concept Plastics Co.
- Stadler develops second Republic Services Polymer Center
- Japanese scrap can feed its EAF sector, study finds
- IRG cancels plans for Pennsylvania PRF
- WIH Resource Group celebrates 20th anniversary