
For quite some time, the aluminum industry’s recycling narrative has long focused on the used beverage container (UBC). (Turn to page S48 to read more about UBCs in the feature “Quantity and Quality.”) While there is much to spotlight regarding UBCs—as one example, a well-touted statistic from the Aluminum Association is that an aluminum beverage container can be recycled and back on the shelf in 60 days—the Arlington, Virginia-based trade association representing U.S. aluminum producers, recyclers and industry suppliers is attempting to broaden aluminum’s story.
Beyond UBCs, many other markets have contributed to the growth in aluminum recycling in the U.S. in recent years. Most notably, the automotive, construction/building and electronics sectors have supplied aluminum for recycling.
Matt Meenan of the Aluminum Association says, “There’s this untold story in the aluminum industry, from our automotive market to the electronics market and building market, where aluminum recycling has really taken off in the last three decades in the U.S.”
He continues, “There are economic reasons for that but also a stewardship story there.”
In 1980, 30 percent of U.S. aluminum production consisted of secondary aluminum; today, that figure has reached 70 percent, Meenan says.

“That reversal—that we used to be at 30 percent recycled, and now it’s 70 percent—in just a 35-year period is a remarkable change,” Meenan says. “Consumers like to know that the product they have has recycled content.”
CONTENT COUNTS
Increasing recycled content has been an objective of Atlanta-based Novelis, the world’s largest producer of rolled aluminum sheet. Since 2011, the aluminum rolling and recycling company has increased its recycled content from 33 percent to 49 percent as of the end of its 2015 fiscal year, says Nick Mize, director of global recycling, Novelis.
That progress, he says, is directly attributed to the company’s recent investments and expansions to process more aluminum scrap.
Mize explains, “While UBCs will remain the primary source of postconsumer material we purchase, we are working to buy and process more of other types of postconsumer aluminum as well—for example, aluminum from automotive, architectural and electronic products.
“In order to recycle this wider variety of scrap types,” Mize continues, “we recently opened the world’s most technologically advanced aluminum recycling center in Nachterstedt, Germany.”
The aluminum production plant, costing approximately $258 million, will consume up to 400,000 metric tons of aluminum scrap per year. The recycling plant will convert the aluminum scrap into ingots that will be consumed by Novelis’ European manufacturing operations.
Aluminum ingots produced at the Nachterstedt facility will be hot-rolled at Novelis’ facilities in Norf, Germany, and Sierre, Switzerland, and supplied to company operations across Europe for further processing. Finished aluminum sheet will be delivered to customers primarily in the automotive and beverage can markets.
According to Novelis, the facility features technology for aluminum scrap sorting, decoating, melting and casting. The company also reports the facility will allow the aluminum rolling and recycling company to process a wide range of scrap types, helping to create a more efficient closed-loop recycling system and increasing Europe’s domestic scrap consumption.
“This new facility is able to process more types of scrap than ever before possible,” Mize says.
In January 2015 the company completed a $48 million investment in its automotive recycling facility in Oswego, New York, Mize says.
He says the New York facility expands upon the company’s recent growth in Oswego to meet the increased demand for aluminum automotive sheet in North America. “Designed specifically to meet the needs of North American automakers, the recycling center will enable Novelis to process as much as 10,000 metric tons of recycled scrap per month,” Mize says.
BUSINESS BENEFITS
Manufacturers’ focus on recycling is correlated with the idea that companies want to be “a good steward of the environment,” Meenan says.
“Novelis supports efforts to make postconsumer aluminum recycling easy and convenient since such recycling is essential to our efforts to ‘close the loop’ on the aluminum life cycle.” – Nick Mize, Novelis
“Industries recognize there’s a lot of value in aluminum, and they don’t want it to end up in landfill,” he says. “Those big industrial sectors do a great job of getting that metal back.”
Joel M. Fogel, nonferrous metals director for Middletown, Ohio-based Cohen, agrees. He says the buzz of “being green” is increasing aluminum recycling rates.
“More people are understanding the overall benefits of recycling as it relates to our environment,” Fogel says.
Mize says, for Novelis, recycling remains a “key pillar” of the company’s business strategy, which explains its recent investments in recycling capacity. In addition, he says, recycling is an “important competitive differentiator for” the company.
Mize continues, “We continue to believe in the strategy of recycled material from a sustainability perspective and as a business benefit by diversifying our supply.
“Novelis supports efforts to make postconsumer aluminum recycling easy and convenient since such recycling is essential to our efforts to ‘close the loop’ on the aluminum life cycle,” he adds.
The company has a “growing share” of postconsumer aluminum scrap coming from closed-loop recycling agreements it has with its automotive customers, such as Ford and Jaguar Land Rover Jaguar, Mize says.
The aluminum company shares the drive seen in other aluminum recyclers as the Aluminum Association says the industry has increased the amount of aluminum collected and recycled domestically over the past several decades. In 2014, the industry collected 11.7 billion pounds of aluminum for recycling, according to the trade association.
“To produce a pound of recycled aluminum is about 92 percent less energy intensive than to make new aluminum,” Meenan says. “So while there are economic reasons [for recycling aluminum], there are also good stewardship reasons.” Novelis is not the only company investing in expanding its recycling capacity.
In September 2014, Bermco Aluminum, a secondary aluminum producer based in Birmingham, Alabama, completed a $5 million investment at its melt shop. At the time, the company said it realized it had to increase its capacity to compete in the growing secondary aluminum sector. To accomplish this, Bermco opened a 220,000-pound furnace in early 2014 and a second furnace that began operating in the late summer of 2014.
The investment drew the attention of Japan-based Toyota Tsusho America, which announced its acquisition of Bermco in August 2015.
Steve Weinstein, president of Bermco, said at the time of the announcement, “This is the beginning of an exciting new chapter for Bermco. It is a unique opportunity to join one of the world’s top performing automotive-related businesses.”
In September 2015, Total Merchant Ltd., a company controlled by Chung Sheng Huang, the chairman of the board and managing director of China-based secondary aluminum producer Ye Chiu Group, purchased scrap processing firm Metalico Inc., Cranford, New Jersey, for $102 million, likely in an attempt to secure more aluminum scrap for its production operations.
PRICING PREMIUMS
Despite the growth in secondary aluminum capacity that has been seen in recent years through investments from various producers, pricing for the nonferrous metal has not fared well.
Cohen’s Fogel says aluminum pricing is at a six-year low. “The reduction of the Midwest Premium as well as the low LME [London Metal Exchange] has pricing down,” Fogel says.

Sean Duffy, president and chief operating office of material recovery facility (MRF) operator ReCommunity, Charlotte, North Carolina, points to three factors that “really drove the free fall in aluminum pricing that we are now experiencing.”
As an effect of a strong U.S. dollar and China’s overproduction of material flooding the U.S. market, aluminum inventory is “very high,” Duffy says.
In addition, he says, within the last year the market saw a rebalancing of stockpiled inventory in the Midwest market that drove inventories even higher.
Duffy says, “As a MRF operator, we are facing pressure on both the inbound and outbound side of our business.
“Most and sometimes all of our revenue is supported by the sale of commodities,” Duffy says, continuing, “Lower revenues from commodity pricing and higher costs to process are straining the industry and individual MRF operators.”
For Cohen, one of the largest ferrous and nonferrous metal recycling companies in North America, relying on just one material is not an option, especially considering the fluctuation in commodity prices.
Fogel says, “We handle both ferrous [and] nonferrous and e-scrap while continuing to grow other revenue streams, so we are not dependent on one commodity or product class.”
Get curated news on YOUR industry.
Enter your email to receive our newsletters.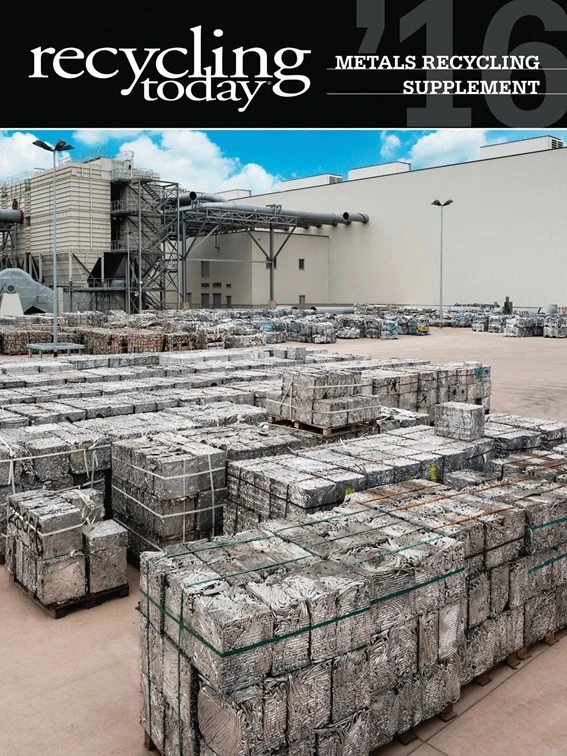
Explore the Jan 2016 Metals Recycling Supplement Issue
Check out more from this issue and find your next story to read.
Latest from Recycling Today
- Astera runs into NIMBY concerns in Colorado
- ReMA opposes European efforts seeking export restrictions for recyclables
- Fresh Perspective: Raj Bagaria
- Saica announces plans for second US site
- Update: Novelis produces first aluminum coil made fully from recycled end-of-life automotive scrap
- Aimplas doubles online course offerings
- Radius to be acquired by Toyota subsidiary
- Algoma EAF to start in April