For many recyclers, baling secondary commodities such as old corrugated containers (OCC) and aluminum used beverage containers (UBCs) is second nature. They are familiar with the materials and know their balers can handle them.
But what happens when recycling companies want to expand their operations to include baling new materials, such as computer monitors or car door panels? Will the recycler’s existing baler be able to efficiently process the new materials in question?
This is when a recycling company’s relationship with its equipment supplier comes into play.
FOLLOWING A NEW PATH
Within the last 10 years, many baling equipment providers say they have seen an increase in demand for balers that are capable of processing a variety of materials beyond recovered paper and UBCs, including tires, computer monitor casings, shrink wrap and plastic automobile components. Equipment providers attribute this increase to the various opportunities these materials offer, including new end markets.
Baling can help recyclers realize freight savings when shipping these new recovered materials.
"Baling significantly cuts down on shipping costs," says Scott Melton, president, ACI Plastics, Flint, Mich. ACI has been producing recycled-content plastic resins from automobile bumpers and industrial scrap since the company’s inception in 1986. (For a profile of ACI Plastics, see "Bumper Crop" in the May 2008 issue of Recycling Today.)
Melton says he has witnessed the freight savings that result from shipping baled material vs. loose scrap firsthand after placing a vertical baler in his company’s new warehouse in Middletown, Ohio. "Instead of putting 6,000 pounds of material on a truck, we can put 40,000 pounds of baled material on a truck," he says.
Melton adds that ACI primarily uses the vertical baler at this location for punch and trim scrap.
Unfortunately, baling new materials, such as computer monitor housings and plastic auto scrap, also can bring new challenges to an established operation.
"The problem many recyclers have with these emerging materials is they have no baling history," says Ken Korney, director of regional sales, IPS Balers, Baxley, Ga. "Recyclers have no way of knowing how their balers will handle the material, nor do they know what kind of bale weights they are going to get out of them."
He adds, "If recyclers want to be successful, then they must get the manufacturer involved and have them perform a test run to see what type of baler works best for these materials."
TESTING THE LIMITS
To help recyclers get started, Aaron Krueger, director of sales, Excel Manufacturing, St. Charles, Minn., suggests considering the volume of material to be baled daily along with the variety of materials to be baled and how often the operation will switch materials when baling. "And, in the event that none of our customers are baling the new materials, we will make a test bale of the material in an existing similar model baler," Krueger says.
IPS Balers recently performed a test run for a customer who wanted to bale computer chassis, plastic casings and printers. Korney says IPS baled the material successfully using another customer’s closed-door horizontal baler with a hinged side. "The hinged-side design works because it provides the operator with a wider feed opening," Korney says.
The extra space a hinged-side design offers can be especially beneficial for operations that are baling large materials, such as whole Gaylord containers. "The problem with Gaylords is that they typically have to be broken down or cut up before being baled, which can be very time consuming and costly," Korney says. "With a hinged-side baler, recyclers are able to drop in a whole Gaylord."
But some materials, such as vehicle bumpers, might be too tough for a hinged-side baler to handle effectively. Instead, Korney says two-ram balers are often used to bale automobile bumpers, which can range in length from 5 to 6 feet.
The company’s two-ram baler can also be used to bale used tires. "About two months ago we did a test run on 3,000 pounds of tires for a customer on our two-ram, and it worked really well," Korney says. If the two-ram baler wasn’t up for the job, Korney says tires would have been popping out of the baler and the tying system wouldn’t have been able to tie off the bale.
The baler’s tying system also can play an important role when it comes to a company’s ability to bale new materials efficiently. "For instance, balers that tie horizontally around the bale as opposed to tying vertically are prone to having the bottoms of the bales fall out when handling materials such as rigid plastics," Krueger says.
He recommends a closed-door, manual-tie baler with specially designed slots in the top of the bale, ram and floor as well as wire guides to guide the wires vertically around the bale.
Roger Williams, vice president of sales, American Baler Co., Bellevue, Ohio, adds that single-ram balers are typically used for fiber products and not for rigid plastics because the density upgrade they offer to rigid plastics is limited. As well, single-ram balers typically tie off a bale with five wires, as opposed to two-ram balers, which can use additional ties.
KNOWING YOUR LIMITS
Even though balers are generally extremely versatile pieces of equipment, manufacturers and recyclers alike warn that they do have their limitations.
Melton has found that materials that are too brittle or too small, such as plugs and caps that protect parts in transit, are almost impossible bale. "Our only options are to ship the materials and pay the extra freight or to try to grind them," he says of the difficult-to-bale materials. Melton has decided to go with the second option, grinding the material to improve density when shipping.
"I am currently looking into purchasing three or four small 15- to 30-horsepower grinders," he says. "I want three or four grinders so we can run one type of material on each instead of cleaning them out between each grind."
Williams says American Baler was once asked by a customer to bale hot tubs made out of acrylonitrile butadiene styrene (ABS), which proved difficult to do efficiently. "The problem with ABS is that it is hard and brittle, so you would have a lot of pieces falling out of the bale," Williams says.
For products made of ABS, he recommends shredding the items to reduce their size in order to ship the material more cost effectively.
And as recyclers continue to explore baling new materials, Williams also recommends that they work with their equipment providers to find the best baling solution.
The author is assistant editor of Recycling Today and can be contacted at kmorris@gie.net.
Get curated news on YOUR industry.
Enter your email to receive our newsletters.
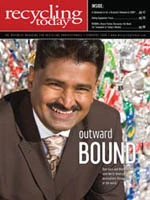
Explore the February 2009 Issue
Check out more from this issue and find your next story to read.
Latest from Recycling Today
- Returpack reports increased DRS activity in Sweden
- Trade groups align against European export restrictions
- Construction, auto sectors show mixed signals
- Politics in Turkey threaten recycled steel outlet
- Toppoint Holdings expands chassis fleet
- Lego creates miniature tire recycling market
- Lux Research webinar examines chemical recycling timetables
- Plastics producer tracks pulse of wire recycling market