
While the negative ramifications of China’s decision to ban imports of plastic scrap have been reported in the mainstream media, that narrative has shaken the foundation of the public’s confidence in the U.S. recycling system.
The fact remains that, despite some notable challenges, the plastics and recycling industries have responded to this latest shift by working to increase recycling capacity and supply chain efficiency in North America. More specifically, China’s National Sword policy in part has led to a wealth of new developments in the United States.
What challenges did the import ban create?
Before China enacted its National Sword policy, high-value plastic scrap, such as polyethylene terephthalate (PET) and high-density polyethylene (HDPE), was sold to China, as were materials of lesser quality and value for which U.S. demand was limited. That’s why these materials were shipped to China; it was more profitable for material recovery facilities (MRFs) and brokers in the U.S. to send these materials halfway around the world than it was to further process them here.
With China’s National Sword policy in place, those MRFs and plastics recyclers have had to find new partners and build new recycling value chains to preserve the value of these scrap materials without involving China.
While building processing capacity and partnerships takes time, and demand for mixed recyclables in the wake of National Sword has been depressed, systemic changes in the recycling process have started to bubble to the surface.
What opportunities did the import ban create?
In my five years at the Plastics Industry Association (PLASTICS), I have assisted many prime resin suppliers, processors and brand owners as they have worked to better understand the recycling value chain and build strategies around how they fit into and can advance the system. They have supported many of our efforts to advance recycling but often struggled to find their most impactful place in the recycling value chain.
Before China enacted its National Sword policy, high-value plastics scrap, such as polyethylene terephthalate (PET) and high-density polyethylene (HDPE), was sold to China, as were materials of lesser quality and value for which U.S. demand was limited.
Today, and in part because of the urgency created by China’s National Sword policy, these players are making important leaps into that plastics value chain, directly investing in new recycling capacity and technologies that are intended to not only stabilize the recycling industry but also to advance it to another level.
In 2018, we saw numerous announcements about investments designed to support the growth of plastics recycling from nontraditional sources, such as Americas Styrenics LLC (AmSty), BP and Indorama Ventures PLC, as well as from consumer products companies that include PepsiCo and Procter & Gamble (P&G):
- AmSty, The Woodlands, Texas, announced a joint venture with Agilyx, Tigard, Oregon, for chemically recycling polystyrene (PS).
- BP, headquartered in London, announced it will purchase the diesel fuel and naphtha blend stocks produced by the RES Polyflow facility in Chagrin Falls, Ohio, for distribution in the regional petroleum market. RES Polyflow’s plant converts plastic scrap into 16 million gallons of ultra-low-sulfur diesel fuel and naphtha blend stocks per year using pyrolysis. Pyrolysis occurs with the right balance of heat and pressure and in the absence of oxygen, so no burning of the plastic occurs; it simply breaks it down into base materials.
- Indorama Ventures, Bangkok, entered into a joint venture with Loop Industries, Terrebonne, Quebec, to become a world leader in the circular economy for 100 percent sustainable and recycled PET resin and polyester fiber. Loop Industries developed a process to break down PET into its base ingredients, which will go back into the commercial supply of PET sold by Indorama.
- PepsiCo, Purchase, New York, signed a multiyear plastics supply agreement with Loop Industries. The company will incorporate Loop PET, which is made from 100 percent recycled plastic, into its product packaging to help meet its aggressive postconsumer resin (PCR) targets.
- P&G, headquartered in Cincinnati, has invested in PureCycle Technologies, a company that is commercializing a solvent extraction technology developed by P&G that will yield near-virgin-like polypropylene (PP). This PP resin is colorless and free of additives, making it a viable feedstock to meet a broad range of P&G’s packaging needs.
- LyondellBasell, headquartered in Rotterdam, Netherlands, partnered with Paris-based Suez and Quality Circular Polymers (QCP), also based in the Netherlands, to produce recycled PE and PP. Suez will use its technology solutions to improve the identification, separation and preparation of materials to be used as feedstock at QCP. LyondellBasell will add QCP’s recycled products to its existing PE and PP portfolio to help meet increasing customer demand for recycled content and to be in line with the European Union’s Plastics Strategy.
- The Sarnia, Ontario, ReVital Polymers startup, Pyrowave, Oakville, Ontario, partnered with the global plastics producer Ineos Styrolution, Frankfurt, Germany, to create a closed-loop recycling solution for PS packaging.
Collectively, these investments are growing the portfolio of technologies to manage plastic scrap, expanding the type of plastics we can process and end market possibilities.
While the effects of China’s National Sword policy have been challenging for some communities and have highlighted some of the current system’s deficiencies, they also have created momentum for transition.
Chinese plastics recyclers, which have been significantly affected by the National Sword policy, also have announced investments in processing capacity outside of China. With diminishing ability to secure consistent scrap supply from overseas, Chinese recyclers are looking to bring their processing capabilities to the U.S.
Balancing supply with demand
The story doesn’t stop with investments in recycling capacity and capability. Brand owners are pulling their weight, too, working to balance the supply equation with demand commitments. Some brand owners have set very bold PCR targets for packaging and products in recent years. These commitments provide assurance to recyclers that the materials they process will have homes if they meet the right specifications, building their confidence to make new capacity investments:
- Target, Minneapolis, has pledged to create three new end markets for PCR by 2020.
- P&G has pledged to use 8.4 million pounds of PCR to produce up to 50-percent-recycled-content bottles.
- Unilever PLC, London, has pledged to increase recycled content by 25 percent by 2025.
- PepsiCo set a goal of achieving 50 percent recycled PET (rPET) in bottles by 2030.
The sum of the announcements
Individually, the investment announcements suggest that, despite what has been widely reported, recycling remains alive and well. However, collectively, they signal a very important trend. The plastics supply chain is getting into the recycling game in an unprecedented way. This response likely is because of the urgency created by China’s National Sword policy. But other factors probably are at play also. The industry might finally be confident in the impact it can have when it strategically enters the recycling value chain. Or, it could be in response to growing demand from nongovernment organizations and consumers that industry becomes part of the solution. In reality, it’s probably a combination of all of the above.
While the effects of China’s National Sword policy have been challenging for some communities and have highlighted some of the current system’s deficiencies, they also have created momentum for transition. All key indicators suggest we are trending toward meaningful, systemwide solutions that are being funded by the plastics industry and brand owners. This is a critical piece of the story that consumers need to understand to restore faith in the recycling system and in the industry that is bringing these solutions into reality. There is no sign that investments will slow down this year, so it will be an exciting trend to continue to monitor.
To hear directly from the key players that are making these investments, be sure to catch the session Making the Vertical Jump, which is sponsored by Recycling Today magazine, at the 2019 Re|focus Sustainability & Recycling Summit May 22 beginning at 9 a.m. For more details, visit www.refocussummit.org/schedule/all.
Get curated news on YOUR industry.
Enter your email to receive our newsletters.
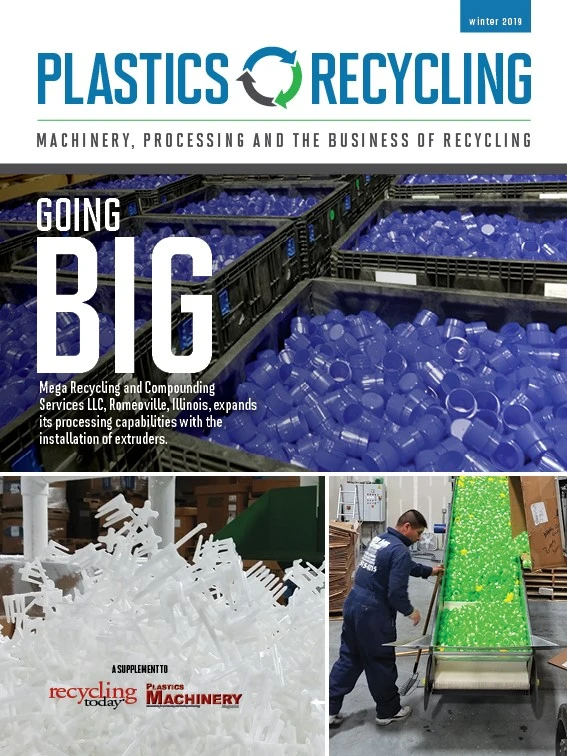
Explore the February 2019 Plastics Recycling Issue
Check out more from this issue and find your next story to read.
Latest from Recycling Today
- Toppoint Holdings expands chassis fleet
- Lego creates miniature tire recycling market
- Lux Research webinar examines chemical recycling timetables
- Plastics producer tracks pulse of wire recycling market
- Republic Services, Blue Polymers open Indianapolis recycling complex
- Altilium produces EV battery cells using recycled materials
- Brightmark enters subsidiaries of Indiana recycling facility into Chapter 11
- Freepoint Eco-Systems receives $50M loan for plastics recycling facility