If producing a clean, contaminant-free product from an aluminum recycling facility was an Olympic event, the Alcoa UBC Quality Award surely would represent the gold medal. A total of seven quality awards were presented in the most recent annual judging.
As with any other champions, the question is what the winners did and how they prepared themselves to be able to produce an outstanding product when compared to that shipped by the company’s other 1,500 suppliers. Like Olympic champions, their entries were clean, compact and free of foreign substances.
Among the winners of the Aluminum Company of America’s (Alcoa) UBC Quality Award for outstanding quality were Resource Management Companies, Plainfield, Ill.; and Tomra of North America, Stratford, Conn.; and Valley Recycling, Chandler, Ariz. The first two were nominated by Alcoa for the UBC Quality Award. Valley ships through Anheuser-Busch, who nominated them.
Also receiving UBC Quality Awards were: Tomson’s Scrap Metal, Pittsburgh, Pa; A. Tenenbaum, Little Rock, Ark; Fulton Recycling and Supply, Dallas, Texas; and United Metal Recyclers, Kernersville, N.C.
The award is presented in recognition of a firm’s consistent ability to provide contaminant-free aluminum can shipments. Alcoa, Pittsburgh, is one of the nation’s largest consumers of used beverage containers (UBCs).
"Improved quality starts with UBCs," says Bryan Steverson, chief process metallurgist with Alcoa in Knoxville, Tenn. "It is not just a cost issue. We don’t want to buy moisture, dirt or glass. But it also is a safety issue at times. The higher the quality of a shipment, the less chance there is of safety issues."
Quality certainly affects the final product. "We sell can sheet. The more contaminants in a load, the more difficult it is to meet the chemical requirements and our customers’ quality demands," he adds.
CURBSIDE PROGRAM
Both Valley Recycling and Resource Management certainly earn points for the degree of difficulty of their UBC operations. For one thing, these MRFs (materials recovery facilities) process curbside collected recyclable material, a situation which gives them little control over the quality of material that comes through the gates.
Although things may come into Valley Recycling’s MRF in a topsy-turvy fashion, when they go out the other end everything is in ship-shape. In fact, the company is so focused on keeping things clean and free of foreign materials that bundles waiting for shipment are kept under roof on a concrete floor. But there is a lot done beforehand to assure clean material hits the baler. Stella Tomlinson, vice president of operations, says the MRF processes 4,400 tons per month. "For as much material as we run, we do not have a lot of space," she notes. The key to producing a clean end product is Valley’s innovative sort system.
"We are the only recycler in the Phoenix area who uses three separate screening systems to clean materials," she says. Product comes from collection programs in the cities of Chandler, Mesa and Gilbert. They also serve some commercial customers and do operate a buy-back facility.
The screens, which include a trommel screen to remove rocks and large foreign particles, sort from larger to smaller before sending material through a typical container line with magnets and eddy current. While she attributes most of the quality to the line itself, there are other factors, as well. "We have material that is hand-picked on the line before baling," Tomlinson says. Workers remove pie plates, foil and plastic bags before the bales are created.
They use an HRB-8 baler which provides a densified, export-size bale. When the haulers pull out and final whistle blows in the quality game, Valley came through a winner.
RESOURCE MANAGEMENT
Resource Management provides the curbside collection of recyclable containers and paper for the City of Naperville, Ill. RMC is a regional processor of commingled recyclable materials dealing primarily with three streams. The first is commingled residential containers (glass containers, HDPE, PET, UBC, steel cans). The second is commingled residential fiber (newspaper, OCC, mixed paper, magazines). The third stream deals with commingled commercial fiber (OCC, office paper, mixed paper). Since 1991, the Plainfield facility has received, sorted and shipped over 400 tons per day of residential commingled containers.
Aluminum cans, along with glass bottles and jars, plastic bottles, and steel cans are collected in a single sort. Paper—including newsprint, magazines, and other mixed paper—is collected in a separate single sort of commingled fiber.
In addition to the material from Naperville, the facility procures and processes recyclable material from a five-state region. They are currently operating three processing facilities. The facility located in Plainfield covers 53,000 square feet. This facility processes more commingled containers per day—300-400 tons per day—than any other facility in the United States. The remaining two facilities are in Chicago Ridge, Ill. (150,00 square feet) and Earth City, Mo. (70,000 square feet). Combined, these three facilities processed approximately 225,000 tons of material in 1997.
RMC owns and operates a fleet of tractor-trailer units that service that five-state region which encompasses Illinois, Indiana, Wisconsin, Missouri and Michigan. According to Kristina A. Kaar, corporate project manager for RMC, the raw materials come from contractual relationships with collection companies and municipalities, a company operated curbside collection contract with Naperville, Ill. (34,000 residential units) and direct delivery from industrial generators.
Resource Management has been a supplier of UBCs to Alcoa since 1991. In fact, the company—which has three locations—has been the largest supplier of UBCs to Alcoa from a single location for several years. The Plainfield, Ill. site must be doing something right, not only in its ability to keep the customer satisfied, but also in increasing its purchases of UBCs.
Quality control is important in the recycling process. UBCs arrive at the processing facilities mixed with glass fragments, paper scraps, snow and other moisture, as will as with other similarly sized containers (such as single-serving PET, etc.).
Most of the equipment used at the Plainfield facility is fairly standard, off-the-shelf sorting equipment with the usual run of magnets to remove steel and eddy currents for the aluminum cans. However, RMC President Calvin Tigchelaar has always been big on adapting and tweaking equipment to make it work a bit more effectively. Although most of the changes are proprietary to RMC in terms of design and operation, one thing he likes to be sure of is the quality of the product which comes off the end of the line.
The process for residential commingled containers is complete and up-to-date, Kaar says. The commingled containers are received directly via route trucks from local collection programs or via transfer trailers from more distant locations.
The loads are dumped on a 12,000 square-foot tipping floor and are fed into a two-line sorting system. Ferrous metals are separated utilizing Dings electro-magnets. Aluminum beverage cans are separated using an Eriez eddy current separator. Materials like whole glass containers and plastic containers are manually sorted. The glass fragments are isolated and screened in preparation for optical sorting utilizing proprietary Resource Management technology.
Sorted materials are stored in 75-cubic yard bunkers under the sorting platform and are sequentially discharged past a quality control station to HBRT balers for baling. Glass containers are conveyed into outdoor bunkers and are blended with other separated glass material generated by the optical sorting system.
Fiber (both residential and commercial) is handled as a separate process using large, high-capacity sorting systems and balers at all three plants. The company currently processes and ships approximately 140,000 tons of sorted fiber per year. Aluminum cans generate approximately 50% of the gross revenue derived from the commingled container stream.
The cleaner the cans, the happier are the UBC buyers from such RMC customers as Alcoa and Alcan. Kaar notes that buyers wish to purchase only contaminant-free aluminum cans and have stringent quality expectations. "Buyers are not interested in paying UBC prices for broken glass and chips of plastic," she notes.
In addition to obvious issues, problems such as potential equipment damage during the production phase and inability to meet customer specifications in the final sheet are all potential results of the consumption of contaminated UBCs.
There are seven essential processing elements needed to generate high-quality UBCs form a residential commingled container stream, Kaar says. First, she says, RMC relies on high-strength electromagnetic separation upstream of the eddy-current process. Two levels of secondary magnetic separation ( one upstream, one downstream) are used. Agitation and tumbling action are essential for moisture reduction and drying of the UBCs. Size classification, upstream of the eddy-current separator, is used to optimize the eddy-current process.
Other important elements include screening of UBCs prior to manual quality control to remove remaining non-UBC fragments, a manual (visual) inspection prior to baling, and visual inspection after baling and if required reprocessing.
Quality control checkpoints are established throughout the line. Every worker on the line has to be well versed in the material moving through and every effort is made to be sure the right items are pulled off at the right time. "We make sure our employees know what they are looking for," says RMC's Kaar.
In addition to Alcoa, materials are shipped to domestic aluminum mills, glass processors, steel mills, secondary plastics processors and paper mills. Some of the recyclable fiber and plastics make their way to countries around the Pacific Rim.
TOMRA FACILITY
Before Tomra ships UBCs out of its site, they have to clear more hurdles than an Olympic runner. There are 28 employees in the warehouse, and all of them are involved in a triple-check system that was instituted to assure that only the cleanest loads are shipped out. "Our loads are always a high or premium quality," says Tomra’s Plant Manager Britt T. Liotta. "This relates back to the warehouse, where we stress the cleanliness of the loads."
Tomra credits the quality of its aluminum partly to its employees and partly to the efficiency of its processing facility. Tomra Metro, which occupies a new 42,000 square foot facility, currently purchases over six million pounds of aluminum each year. Alcoa Recycling bought about 2.5 million pounds of that total in 1997.
"At some point, everyone works the aluminum," Liotta continues. "When we open the bags, we check for any material other than aluminum and pull that aside."
There is a second quality check done before the material is actually baled, where workers pull out any stray material that might have gotten by the first checkpoint. But that is not the finish line for quality control. "We even check the bales while stacking them for shipping," he says. "These three checks help to keep the aluminum as clean as possible."
Beyond the eddy currents and magnets, most of the work done at the MRF relies on the human eye and skill in sorting. But to win the Alcoa award, more objective, quantifiable standards are imposed.
OBJECTIVE CRITERIA
Criteria used in the evaluation process for the UBC Quality Awards include quantification of levels of moisture, heavy metal, dirt and ferrous metal concentrations in UBC shipments. The actual awards were presented at the company sites by Steverson and by Dennis B. Crooker, president of Alcoa Recycling Company.
Loads are graded on a scale of zero-to-four, with four points being the highest and zero a rejected load. The three areas checked are dirt, combustibles, and other metallics (iron, copper, etc.).
The categories are weighted and a score of zero to 100 in generated. Anything less than a score of 45 is put on a quality caution list.
One of several criteria is how high the MRFs’ scores were. "Our winners were at the top end of the scale," Steverson says. Top performers did well in five categories: overall average scores, overall moisture content, having no rejections, safety or quality issues, fallout information generated on several loads (checking for magnetics, heavy metals, and dirt).
Typically, any load over four percent moisture is deducted back to two percent. That is, if five percent moisture is found in a 40,000-pound load, a total of three percent of the load would be deducted.
On dirt, there is a 1.75 percent limit. Any load over that limit generates a warning letter. Three letters to one supplier in a 12-month period gets the company on the caution list. This means all shipments from that firm are watched more carefully than most.
There is a limit of two-tenths of one percent for magnetics and heavy metals. "We do not buy from companies which do not have magnetic separation," Steverson says. Violations trigger a letter, and three letters in a 12-month period get a company put on the caution list.
As with most things in this industry, the standards are constantly subject to change. As technology and techniques become more refined, there are adjustments in the levels of quality required.
Just as an Olympian trains to meet an improved level of competitor, so too do the gold medallists of recycling continue to train their personnel to set new standards of excellence in UBC recycling.
The author is an environmental writer and Recycling Today contributing editor based in Strongsville, Ohio.
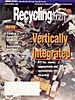
Explore the September 1998 Issue
Check out more from this issue and find your next story to read.
Latest from Recycling Today
- Aqua Metals secures $1.5M loan, reports operational strides
- AF&PA urges veto of NY bill
- Aluminum Association includes recycling among 2025 policy priorities
- AISI applauds waterways spending bill
- Lux Research questions hydrogen’s transportation role
- Sonoco selling thermoformed, flexible packaging business to Toppan for $1.8B
- ReMA offers Superfund informational reports
- Hyster-Yale commits to US production