
When Dan Becker first started to work for Becker Iron & Metal, his family’s business in the St. Louis area, about 19 years ago, he says safety had been somewhat of an afterthought.
“Safety … wasn’t part of the culture,” Becker says of the company in 2001. He adds that “guys weren’t wearing hard hats” because many of the company’s employees had the mentality that they were just for construction workers.
Becker says he wasn’t comfortable with Becker Iron & Metal’s stance (or lack thereof) on safety in the early 2000s, so the management team at that time allowed him to take ownership of the safety program. Gradually, he says, he introduced new safety procedures to the business, such as making sure employees all used personal protective equipment (PPE).
In 2011, Becker Iron & Metal’s business was growing, and the company moved from its 6.5-acre site in St. Louis to a nearby 16-acre greenfield site in Venice, Illinois. With the move, Becker says he saw a clear opportunity to take the company’s safety culture to the next level.
To improve Becker Iron & Metal’s safety culture at the new yard, Becker says he did something that made some employees uncomfortable: He signed up for a free on-site consultation program offered by the Occupational Safety and Health Administration (OSHA). Through the program, a consultation group from OSHA would inspect the Venice yard and inform Becker of any OSHA violations. The company would then be given a deadline by which to address the violations.
“That made a lot of people uncomfortable,” Becker says. “They thought I was nuts inviting OSHA. I had to convince them that this was going to be a nonpunitive approach of getting to the next level and why not be safe right out of the gate and not have to worry about OSHA coming to us later. To me it was the best time to bring in OSHA because then if I needed to do anything, I’m already in construction.”
Welcoming OSHA
With OSHA’s on-site consultation program, employers can find out about potential hazards at their worksites, improve their safety and health programs and qualify for a one-year exemption from routine OSHA inspections. According to OSHA, the service is delivered by state governments using well-trained professionals. The program is primarily targeted at small businesses and is separate from OSHA’s inspection efforts.
Also, when companies participate in the program, no OSHA citations or penalties are issued, according to OSHA, but companies must correct serious job safety and health hazards.
Through the program, OSHA identified some minor issues that could have resulted in fines for Becker Iron & Metal’s site in Venice. Becker says some of those issues included frayed cords, chains missing at docks, a ladder that needed to be replaced and labels missing on an electrical box. He adds that it was easy to rectify these issues in the time frame OSHA gave.
Lisa Dunn, QEH&S (quality, environmental, health and safety) director at Becker Iron & Metal, says the consultation program has made the company much more aware of OSHA safety violations.
“It was unbelievable to go from [minimal safety] to being recognized by the state of Illinois as a safety winner.” – Dan Becker, owner, Becker Iron & Metal
“A lot of times you don’t know what you don’t know,” she says. “Being a part of this program can help you correct things without fear of citations.”
Through the program, Dunn says companies can invite OSHA consultants in two times per year to perform a walkthrough of the facility to ensure compliance with OSHA standards. Seeing OSHA periodically helps Becker Iron & Metal stay on top of any new standards, she adds. Because of the program, the company also has been able to develop a better self-audit checklist it uses internally at least once a month.
“Just because you correct it once doesn’t mean it won’t resurface or happen again,” Becker adds.
Looking SHARP
About two-to-three years after initially connecting with OSHA for the on-site consultation program, Becker says the agency commended his company for its safety culture and encouraged Becker Iron & Metal to work toward earning OSHA’s Safety and Health Achievement Recognition Program (SHARP) status.
To earn SHARP status, companies must request a comprehensive visit from the state’s On-Site Consultation office, which involves a complete hazard identification survey. Companies must involve all employees in the consultation process and correct all hazards identified by the consultant. SHARP applicants must implement and maintain safety and health programs that at a minimum address OSHA’s Safety and Health Program Management Guidelines and Issuance of Voluntary Guidelines. Companies that apply for SHARP status must maintain their rates for days away, restricted or transferred (DART) and total recordable cases (TRCs) below the national averages for their respective industries. Finally, companies must agree to notify their states’ On-Site Consultation offices prior to making any changes to working conditions or before introducing new hazards into the workplace.
When a company achieves SHARP status, it is exempted from OSHA-programmed inspections for up to two years, with a subsequent renewal for up to three years.
Throughout much of 2013, Dunn says she spent months making sure Becker Iron & Metal was ready to apply for SHARP status. “While it wasn’t a one-woman show, I was cooperating with all employees to make sure that we were where we needed to be and that we stayed there,” she says.
The company formed an in-house safety council as part of its SHARP application process. Dunn says Becker Iron & Metal had one employee from each department involved in the group.
By 2014, Becker says the company officially received SHARP status from OSHA. He adds that Becker Iron & Metal was the first scrap company in the state of Illinois to achieve this designation. The company even received recognition for this when it earned the Illinois Governor’s Safety and Health Award in 2018.
“It was unbelievable to go from [minimal safety] to being recognized by the state of Illinois as a safety winner,” Becker adds.
Since 2014, Becker Iron & Metal has continued to renew its SHARP status. The company’s most recent application for renewal was in December 2019, which was just before press time.
Sponsored Content
Labor that Works
With 25 years of experience, Leadpoint delivers cost-effective workforce solutions tailored to your needs. We handle the recruiting, hiring, training, and onboarding to deliver stable, productive, and safety-focused teams. Our commitment to safety and quality ensures peace of mind with a reliable workforce that helps you achieve your goals.
Sponsored Content
Labor that Works
With 25 years of experience, Leadpoint delivers cost-effective workforce solutions tailored to your needs. We handle the recruiting, hiring, training, and onboarding to deliver stable, productive, and safety-focused teams. Our commitment to safety and quality ensures peace of mind with a reliable workforce that helps you achieve your goals.
Sponsored Content
Labor that Works
With 25 years of experience, Leadpoint delivers cost-effective workforce solutions tailored to your needs. We handle the recruiting, hiring, training, and onboarding to deliver stable, productive, and safety-focused teams. Our commitment to safety and quality ensures peace of mind with a reliable workforce that helps you achieve your goals.
Sponsored Content
Labor that Works
With 25 years of experience, Leadpoint delivers cost-effective workforce solutions tailored to your needs. We handle the recruiting, hiring, training, and onboarding to deliver stable, productive, and safety-focused teams. Our commitment to safety and quality ensures peace of mind with a reliable workforce that helps you achieve your goals.
Sponsored Content
Labor that Works
With 25 years of experience, Leadpoint delivers cost-effective workforce solutions tailored to your needs. We handle the recruiting, hiring, training, and onboarding to deliver stable, productive, and safety-focused teams. Our commitment to safety and quality ensures peace of mind with a reliable workforce that helps you achieve your goals.
Sponsored Content
Labor that Works
With 25 years of experience, Leadpoint delivers cost-effective workforce solutions tailored to your needs. We handle the recruiting, hiring, training, and onboarding to deliver stable, productive, and safety-focused teams. Our commitment to safety and quality ensures peace of mind with a reliable workforce that helps you achieve your goals.
Sponsored Content
Labor that Works
With 25 years of experience, Leadpoint delivers cost-effective workforce solutions tailored to your needs. We handle the recruiting, hiring, training, and onboarding to deliver stable, productive, and safety-focused teams. Our commitment to safety and quality ensures peace of mind with a reliable workforce that helps you achieve your goals.
Dunn says the process of recertifying with OSHA for SHARP status is stressful yet worth the extra work.
“You have a better safety culture in general—you can’t put a price tag on that,” she says. “There are also tangible savings with lower workers’ compensation rates.”
Maintaining a safety culture
Today, maintaining a safe workplace is regularly stressed at Becker Iron & Metal. Becker says he often reminds his employees in company meetings that their No. 1 job is to go home in the same condition they arrived to work in. Becker says he only resorts to punishing poor safety behaviors when rules are “flagrantly disregarded.”
He says, “If someone is not following the rules—like not wearing a hard hat or not wearing a seatbelt in a forklift—my goal is for someone to tell them that and not punish them but remind them. If it’s punitive, then you get people who hide it. But if I have someone say, ‘We almost had an accident,’ then I’m happy that somebody reported it to me. I would rather reward people for near misses than be punitive about people almost getting into accidents.”
Becker Iron & Metal often has safety meetings during company breakfasts or just before lunch. Becker adds that he always makes sure employees are on the clock during safety meetings because he wants to ensure they’re paid for that time. “Safety is a part of your workday,” he says.
Get curated news on YOUR industry.
Enter your email to receive our newsletters.
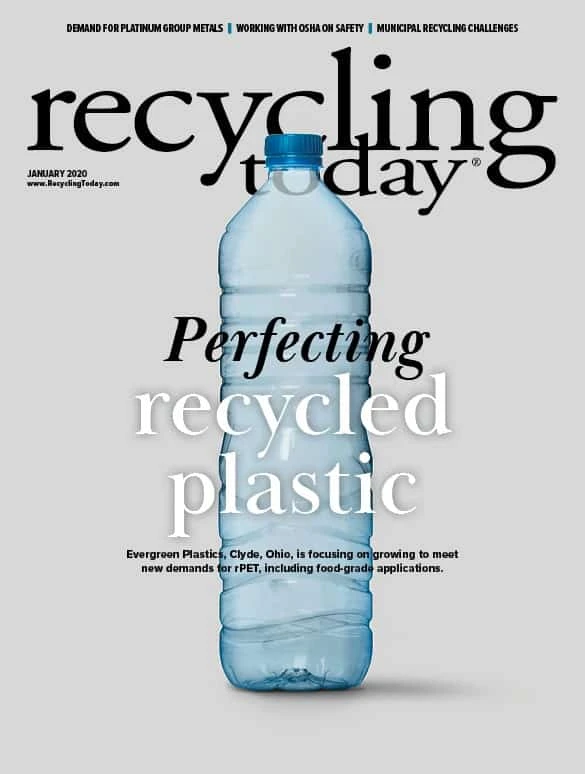
Explore the January 2020 Issue
Check out more from this issue and find your next story to read.
Latest from Recycling Today
- Green Cubes unveils forklift battery line
- Rebar association points to trade turmoil
- LumiCup offers single-use plastic alternative
- European project yields recycled-content ABS
- ICM to host colocated events in Shanghai
- Astera runs into NIMBY concerns in Colorado
- ReMA opposes European efforts seeking export restrictions for recyclables
- Fresh Perspective: Raj Bagaria