Like the expansive farms that surround it, Marine Terminals of Arkansas Inc., headquartered in Armorel, Ark., depends on the Mississippi River for its livelihood.
The same currents that bring water and rich soil to these riverside communities also grant passage to the massive barges loaded with ferrous scrap that Marine Terminals unloads on a daily basis.
The company has built a niche as a leading handler of barged iron and steel scrap shipped on numerous U.S. waterways.
EXTRA-LARGE DOCKERS. Marine Terminals has docks in Berkeley, S.C.; Hertford, N.C.; Decatur, Ala.; and two in Arkansas, all of which are situated close to scrap-dependent electric arc furnace steel mills.
Rick Ellis, general manager of Marine Terminals, estimates that the Yamato operation (named for the adjacent Nucor Corp. Yamato I-beam plant) in Armorel unloads between 2.3 million and 2.4 million tons of ferrous scrap yearly.
The Hickman, Ark., facility, located up the river from the Yamato dock, unloads approximately 1.3 million to 1.4 million tons of scrap per year for another Nucor facility.
When the Yamato operation opened in 1989, however, scrap iron didn’t flow off the barges nearly as quickly. It took 48 hours to unload a barge with a cable crane. The addition of a second crane reduced the time to 24 hours. But as Nucor Yamato’s demand for scrap increased, Ellis had to find ways to shift his unloading operation into a higher gear.
The answer Ellis found involved a Komatsu PC650 hydraulic material handler purchased from the Power Equipment dealership in Memphis, Tenn. As Marine Terminals began experimenting with hydraulic material handlers in the early 1990s, production steadily advanced.
The original reduction in unloading times of a hydraulic material handler vs. a cable crane can be attributed to easier controls, more powerful and precise hydraulics and the ability to manipulate more objects, thanks in part to its attachment fleet.
Today, with the help of its suppliers and a careful selection of equipment based on production demands, Marine Terminals unloads each barge in two to three hours and empties an average of five barges per 12-hour shift.
"We went out and purchased a Komatsu 650 and we could unload a barge in six to seven hours," says Ellis. "At the time, we had Mack highway trucks that we were loading into—but the mills were getting bigger, which meant we needed to get bigger. We moved to the PC1000, and that put us in the four-to-five-hour range for unloading each barge."
This evolution continued throughout the 1990s and into this decade. The hauling process from barge to mill evolved from using highway Mac trucks to off-road, 30-ton Caterpillar and 35- and 40-ton Volvo articulated dump trucks. Eventually, the company began using 61-ton, Komatsu HD465-5 rigid frame hauler trucks.
The material handlers kept getting larger, too. When the PC1000 couldn’t keep up, the company upgraded to a PC1100. In 2002, Ellis found a product combination that he says has been perfect for his production demands.
"We upgraded to the PC1250LC-7MH with the HD465-5 trucks, and it’s been a great marriage. We’re down from 48 hours per barge in 1989 to two to three hours per barge today."
MATCH MAKING. The PC1250LC-7MH matched with the HD465-5 haul truck is currently averaging 600 tons per hour for Marine Terminals. Ellis says his crews can load as much as 50 cubic yards of ferrous scrap into the trucks in six to eight passes.
Young Corp., a Seattle-based company with more than 100 years of experience in manufacturing attachments and specialty boom configurations, worked with Komatsu to develop two- and three-piece fronts for its material handlers in an attempt to achieve the most effective combination of reach, lift capacity and speed. Marine Terminals chose a 55-foot, two-piece configuration with an 8-yard orange peel grapple as the primary attachment.
"This design works well for us and it allows us to get the most out of the machine," Ellis says. "It allows us to reach both the outside and inside trucks (in a side-by-side loading pattern) and to the other side of the barge. It fits the radius we need to work at."
SUPPORT SYSTEM. Ellis credits his relationship with Power Equipment in Memphis and aggressive maintenance programs with the longevity of his equipment.
"Our uptime is great with this equipment," he claims. "We’ve got over 11,000 hours on the PC1250LC-7MH, and it has been pretty well trouble-free. We do our regular maintenance as well as the QUEST maintenance program. It’s our focus on good maintenance that really helps our uptime and productivity," Ellis says.
He backs his statement up with the following statistics: The HD465 haul trucks have their engines overhauled every 18,000 hours, a rate almost unheard of in intensive hauling situations. He has a PC650 running in the scrap yard with more than 80,000 hours on it. The PC1100 unloading at the Hickman facility has 13,900 hours. And most of these machines show no sign of slowing down, a fact that helps Ellis have faith that machines like the PC1250LC-7MH—already with more than 11,000 hours on it—will keep performing for him for years to come.
"We’ve been upgrading every three to four years," says Ellis. "But we’re at the point now where we need to make it stretch out. It shouldn’t be a problem with this machine."
This story was submitted on behalf of Komatsu America International Co., Vernon Hills, Ill.
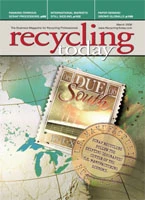
Explore the March 2006 Issue
Check out more from this issue and find your next story to read.
Latest from Recycling Today
- US ferrous market exhibits upward pricing pressure: Davis Index
- Glass Packaging Institute applauds regulation change
- Engcon adds to Tiltorotator line
- Paper recycling is focus of two January webinars
- Disruption likely for material flows in mid-January
- Blue Whale Materials to expand Oklahoma lithium-ion battery recycling plant
- CARI names new president and CEO
- Interzero revamps leadership structure