
Sonekin Co. Ltd. employs fewer than 20 people at its two locations while still preparing considerable volumes of recyclable ferrous and nonferrous metals for domestic and global markets.
Sonekin, based in Japan, handles a variety of grades and materials, according to Operations Manager Jundai Gon. The company’s ability to handle the needs of its scrap-generating customers combined with the importance of offering clean processed grades to melt shops means it is highly selective when it comes to equipment.
In the past two years, Jundai has found the durability, reliability, flexibility and ease of maintenance Sonekin requires in two processing machines provided by Bano Recycling of Padua, Italy.

A true multitasking shredder
When Jundai Gon first saw a Bano Premac Hydro 18-70 model shredder at work, he was impressed by its ability to effectively reduce scrap at a slow speed and with strong hydraulic power, which he says is very good for the lifetime of the blades.
As the name Premac implies, the Bano device has been created as a primary or preshredder to downsize larger incoming scrap. At Sonekin, the stream of materials ideal for its Premac shredder includes varieties of copper cable, including marine cables, plus aluminum profiles and aluminum conductor steel-reinforced (ACSR) cables.
Jundai cites the slow-speed, single-shaft hydraulic configuration of the Premac as the first factor in the machine’s favor.
“With its slow movement, [the] Premac is able to handle a variety type of materials; this aspect of the machine attracted us,” he says.
Subsequent conversations with Leonardo Bano of Bano Recycling helped produce a system that was optimal for Sonekin’s needs as a smaller company with a limited workforce handling a variety of scrap.
While size reduction may be the Premac’s main task, Bano’s recommendations led to the installation of a magnet and a pivoting conveyor that help release material when the Premac shreds ACSR cable.
“ACSR is composed of both aluminum and steel, so in addition to shredding we need to separate each from the other by magnet,” Jundai says. He notes that with the simple but effective system devised by Bano Recycling, “we move the pivoting conveyor, depending on the material.”
Wire and cable streams that require further separation can be directed to Sonekin’s second Bano Recycling machine: a Horizontal Turbo wire processing unit designed to release copper from plastic, increasing its recovery rate so it is ready for shipment to markets anywhere in the world.
Sonekin’s copper customers have confirmed its Bano system was producing 99.8 percent pure copper chops, but a recent experiment with another recycling firm helped verify that.
“Not long ago, a local scrap dealer bought our plastic that was produced by our Bano Horizontal Turbo plant,” Jundai says. “They tried to get very fine copper from the plastic via a water separation method, but the company told me the copper percentage resulting from the procedure was just 0.2 percent.”

Reliability and a personal touch
Sonekin’s purchase and use of equipment made half a world away entails some long-distance conversations, and Bano Recycling has emphasized the importance of the relationships it has with its customers.
In the case of Sonekin, Leonardo Bano is in the sales department but came to Japan for the installation.
“He is always helpful and friendly,” Jundai says. “He is like a member of our company.
“He teaches me not only about our machines but also new technology they are going to build,” Jundai says. “This makes me feel very passionate and excited. He always thinks of our plant as his and cares about our machines.”
The support received extends beyond Leonardo, with Jundai adding, “Bano’s electricians and programmer always have helped me when we have an issue. Although we have distance, they check our plant remotely and they find a solution.”
But the problems are few and far between because of the heavy-duty nature of Bano Recycling’s equipment.
“Regarding their Horizontal Turbo, which is like a refiner, we have not changed its blades after some 700 working hours,” Jundai says. “This has saved us time.”
Of the Premac, he adds, “We run that machine six days per week and seven hours per day. I rate it highly for reliability.”
With a world of options from which to choose, Jundai Gon and Sonekin are satisfied they achieved the best possible outcome by selecting Bano Recycling to fulfill their processing needs.
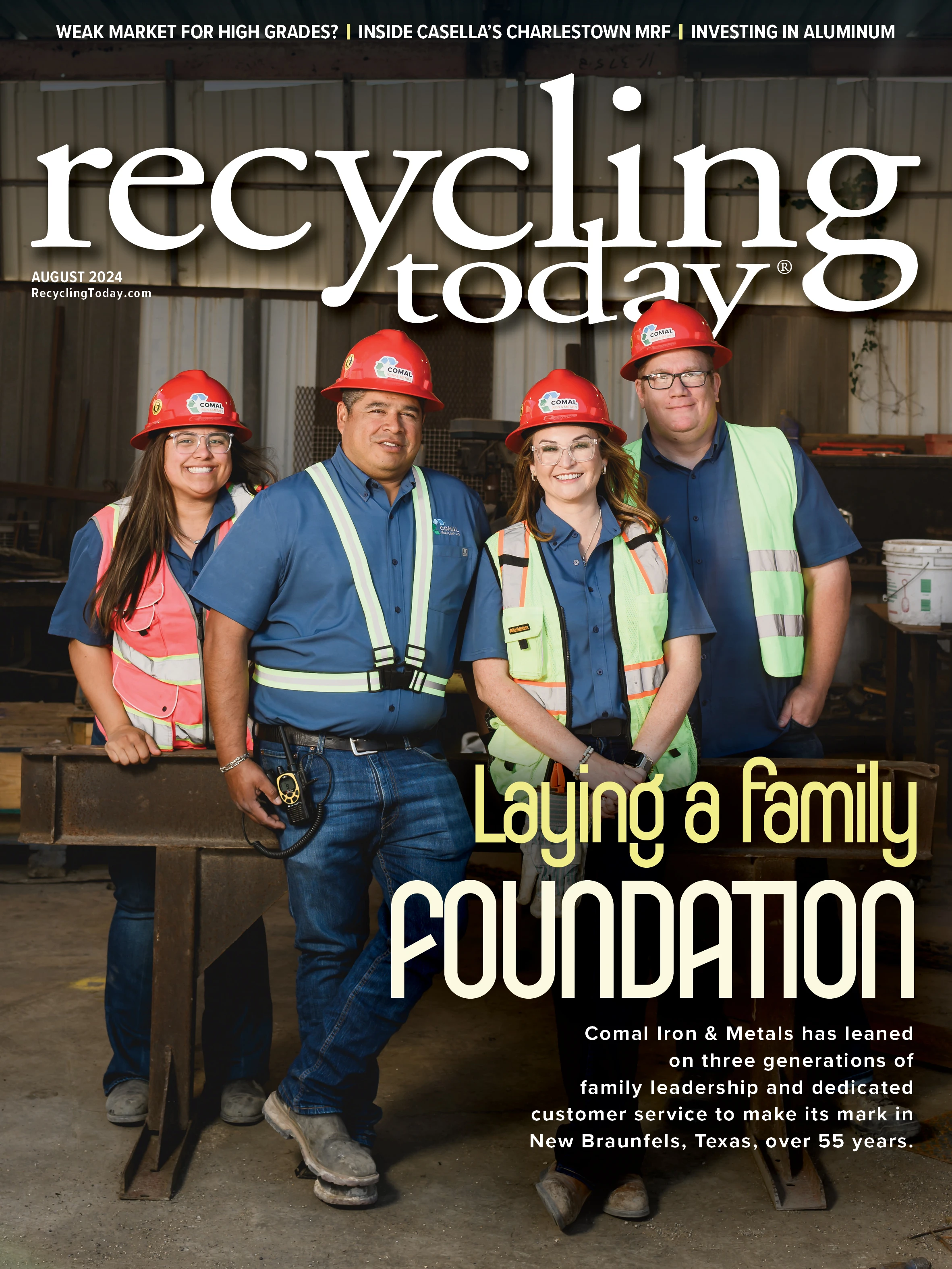
Explore the August 2024 Issue
Check out more from this issue and find your next story to read.