Carpet padding, also known as carpet cushion, represents one of our nation’s most efficient closed-loop recycling efforts. The formal name for recycled carpet padding is bonded polyurethane foam, or re-bond carpet padding.
You can’t mistake it. It’s the multi-colored padding made up of chopped and shredded pieces—pieces of used carpet padding combined with postindustrial polyurethane foam scrap.
According to the Carpet Cushion Council, Riverside, Conn., recycled carpet padding now accounts for 80 percent of all carpet padding sold in the United States. Remarkably, more than 50 percent of all used and removed carpet padding in the United States is recycled and used to make new re-bond carpet padding, as reported by the National Association of Home Builders Research Center.
This level of recycling is approaching the phenomenal success of asphalt and concrete recycling, or certainly the aluminum can recycling rate in the United States. According to the Aluminum Association, Americans recycle between 53 percent and 54 percent of all aluminum beverage cans shipped.
COMBINED EFFORT. The national estimate of recycled, post-consumer carpet padding scrap amounts to 62,500 tons per year. That’s enough used carpet padding to create a 50-foot wide roll stretching from Los Angeles to New York City (or enough to cover almost 12,000 football fields)—a significant amount of material that could otherwise be landfilled.
Producing recycled carpet padding involves the efforts of a number of industries and businesses working together, including carpeting and padding installers, retailers, materials brokers, padding manufacturers and padding recycling companies. Approximately 200 carpet padding recycling companies are in the United States. These companies collect, bale and ship used carpet padding to more than 30 U.S. factories where it is converted into new re-bond carpet padding.
One of these padding recycling companies is run by Mike Trick, president of Cushion Recyclers, with locations in Louisville and Lexington, Ky., and Kennesaw, Ga. Trick also operates a wholesale flooring accessories company. "Much of the used carpet padding we receive is brought directly to one of our locations from carpet installers and contractors within a 20 to 25 mile radius," Trick explains. "Individuals weigh their scrap padding using a truck, pallet or conveyor scale and are paid between 5 and 10 cents per pound.
"We also receive used padding from collection bins located at retail carpeting and flooring accessories stores throughout our operating regions," Trick states. "While installers and contractors are not paid for the used padding they drop off, the bins do provide a convenient disposal site for them as they stop to pick up carpeting and flooring supplies."
"The stores also benefit from our bin system," Trick adds. "The collection bins not only offer their installer and contractor customers a convenient disposal site for used padding, they serve the same purpose for the store’s installation teams. We send our trucks out to replace full bins with empty bins, and in this instance, the store locations receive the 5 to 10 cents per pound paid for used padding. Plus, the stores save the time, transport costs and tipping fees they would typically incur in disposing the used padding at a landfill."
Once Cushion Recyclers receives the used carpet padding, it is bundled or baled and then transported to either a broker or directly to the closest carpet padding manufacturer. At the manufacturer, it undergoes a series of steps in a recycling process to create totally new re-bond carpet padding.
The recycled, or re-bond carpet padding, is formed by combining chopped and shredded pieces of used carpet padding with postindustrial polyurethane foam scrap in different sizes and usually different colors into one solid piece. The process starts with grinding, steaming and chemically washing the padding. The sterilized padding is mixed with postindustrial polyurethane foam scrap (with virgin foam in some instances) and molded into padding rolls of various fractional-inch thicknesses. Sources of post-industrial foam scrap include manufacturers of sofas, chairs, mattresses, automotive seat padding and door panels, textiles and clothing.
ROUND AND ROUND |
Foam scrap and used re-bond carpet padding can be put through its recycling process eight to 10 times before it loses its spring and padding characteristics. According to the Carpet Cushion Council, the recycled-content carpet padding has the same performance characteristics and benefits as virgin carpet padding, including sound control, temperature insulation, extended carpet life and improved air flow that helps vacuum cleaners to clean more efficiently. |
COMPRESSION REQUIRED. Trick says operational efficiency is critically important for carpet padding recyclers to maintain profit levels. "Bundling and baling in preparing the used padding to ship may be the most important step to maximize your operating efficiency and ROI," he says.
"We’re working with a lightweight, spongy, springy product. First of all, it’s unwieldy and difficult to handle. Secondly, we’re trying to fit as much material and as much weight as we possibly can in each semi trailer in order to maximize our shipping cost. To achieve that, we need to compress the padding as much as possible and then keep it that way, in dense, neat bales. That’s why our baler equipment is so important to our productivity.
"When it comes to baling, I’ve learned from trial and error," Trick says. "Our current operation started in 1999, but we were actually in the business in the early ‘90s and had to get out for a few years because it just wasn’t profitable. Our initial problems were that our operation was too labor-intensive and we couldn’t generate the necessary volume. I kept in touch over the next few years with our dealer Midwest Scrap Systems in Cincinnati and I learned about a fully automatic baler from American Baler Co. that had the potential to dramatically reduce our labor costs and increase our volume."
Trick continues, "Today we have a baler from American Baler in each of our locations: Louisville, Lexington and Kennesaw. We’re now able to bale in one hour what used to take—and what still takes other recyclers—eight hours to bale. We produce about 110 bales a day each weighing between 700 and 800 pounds. Today our baling efficiency creates sufficient volume to enable us to ship directly from each of our locations to the padding manufacturer without the need of using a waste broker. In fact, we serve as a broker for other padding recycling businesses."
He adds, "American Baler specially designed the software and gearing for our balers and then stayed on site during start-up until everything was operational. Each start-up was quick and efficient—and ever since, the balers have been extremely reliable."
Trick says he believes that with increased public awareness, and as used padding collection and recycling companies learn to improve their baling and production efficiency, it seems likely that strong increases can be made beyond the current national level of 50 percent of used padding being recycled. "We’re watching the trend of our company’s increasing volume and we’re almost ready to invest in another new baler."
Trick says additional work still needs to be done in the more complicated task of recycling the carpeting itself. But, as recycling efforts for carpeting and other consumable products improve and move toward the efficiencies of carpet padding recycling, the nation will be able to further conserve valuable material, natural resources and landfill reserves.
The author submitted the story on behalf of American Baler Co., Bellevue, Ohio, www.americanbaler.com.
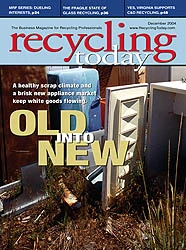
Explore the December 2004 Issue
Check out more from this issue and find your next story to read.
Latest from Recycling Today
- Fitch Ratings sees reasons for steel optimism in 2025
- P+PB adds new board members
- BlueScope, BHP & Rio Tinto select site for electric smelting furnace pilot plant
- Magnomer joins Canada Plastics Pact
- Out of touch with reality
- Electra names new CFO
- WM of Pennsylvania awarded RNG vehicle funding
- Nucor receives West Virginia funding assist