For recyclers of multiple materials, balers may be among their most versatile pieces of equipment. Whether employing a vertical/horizontal, auto-tie or two-ram baler, these machines are capable of handling a variety of materials, including old corrugated containers (OCC) and other paper grades as well as a variety of plastics.
In the following paragraphs, I will offer some general suggestions for operating a baler and also will provide several tips related to baling specific nonmetallic materials.
When selecting a baler, you first need to get a sense of a machine’s throughput, or how many tons per hour it is capable of processing. This factor is critical to selecting the right baler for your application. A small vertical baler may be appropriate if you’re processing 1 ton per hour, while a two-ram or auto-tie baler may be needed if you are processing 20 tons or more per hour. Knowing your output is vital to selecting the right style baler for your operation.
Beyong the Boxes |
In addition to various paper grades and plastics, balers can be used to process materials such as tires, textiles and solid waste. Tire recyclers can find baling helpful in reducing transportation costs because they reduce air space, allowing you to get more material into a truck. We have gotten 2,000 pounds of tires into a bale measuring 30 inches by 60 inches by 48 inches. When baling textiles or clothing, you have to be careful not to rip or tear the material because it is most often resold in developing countries. A vertical baler does an excellent job in making an approximate 1,000-pound bale of clothing. Finally, solid waste can be baled on a two-ram baler. Bales of solid waste can be bagged or wrapped and then taken to the landfill as bale fill. They are stacked two or three high, helping to extend the life of the facility compared with a traditional landfill operation. |
Finished bales normally measure 30 inches by 60 inches by 45 inches, no matter if you are using a two-ram baler, a vertical baler or an auto-tie baler. The goal is to get the densest bale possible so you can ship out at 40,000 pounds or more. Those bale dimensions will cube out a trailer very well.
In terms of pre-processing material before it enters the baler, I recommend a waterfall design conveyor system. In this setup, the first conveyor has a horizontal pit section where workers can dump material on the floor and push it onto the infeed section in the floor. The conveyor inclines upward and discharges onto a second conveyor from a height of approximately 6 or 7 feet. Let’s take a look at how this might work well with compacted loads.
The conveyor’s 6- or 7-foot drop will help break up any compacted material. The second conveyor, a variable speed model, then can be used to uniformly feed material into the baler. This waterfall design can work well for any material.
When operating a baler, it is also important to remember to perform regular scheduled maintenance. The problem is many companies don’t do that; they will just run the baler until something breaks and then they’ll fix it. Many baler manufacturers offer their customers a scheduled maintenance program. In the case of IPS’s preventive maintenance program, a service technician from our company will visit the customer’s facility quarterly or twice per year to do a checkup.
MATERIAL MATTERS
While the tips above provide some basic guidelines for efficiently running your baler, there are also several factors to consider when baling specific materials:
OCC
• You need to know the largest size of OCC your baler will be handling. It’s also important to know whether boxes entering your facility will be whole or broken down and whether they’ll be compactor loads. These factors will determine the charge box size. A lot of people refer to the charge box as the hopper, but the hopper could be any size at the opening. The charge box has to be large enough to accommodate incoming material.
• Breaking down boxes before baling takes more time. Ideally, for efficiency, you don’t want to break down boxes but instead want to feed them whole to the baler.
• If you get some heavy material such as slab waste coming out of a printing or folding carton operation, it may be thick, say 6 inches, and you have to be careful about feeding, as not to jam the baler when running that material through.
Rigid Plastics
• Before you run plastic bottles through your baler, it is highly recommended that you perforate (pre-shred) the material or remove the caps from PET (polyethylene terephthalate) bottles. If you are trying to make a bale with all the bottle caps on, you’re not squeezing out the air, so you’ll have a light bale. You want to put that material through a perforator or pop the caps off so when you make your compression stroke, you get a more densely packed bale.
Plastic Film
• Shrink wrap and similar films are fairly easy to bale. They will fall into the baler and the infeed density is light. It will take you a good number of strokes to make a bale of plastic film, but the material is easy to handle.
• One precaution to keep in mind is that you want a uniform feed to the baler.
High Grades
• The biggest concern with high-grades is shearing. You are going to be shearing across the total width of the baler. In some cases you need a larger cylinder to give you more force to do the cutting. The downside of the larger cylinder is that it puts more force on the machine and more wear on the baler’s floor. IPS has designed a hinge-side baler that compresses the material beneath the shear blade and only cuts about 10 inches, which reduces the wear on the floor and can save replacement costs.
• In some balers, you can execute a full stroke or full penetration of the main ram where it goes all the way forward to the door. Making each stroke or lamination, you have eliminated the air space between the high grades. You have a denser lamination which gives you a heavier bale when it is completed.
Shredded Paper
• Shredded paper, such as in a document destruction application, can be baled in a closed-door horizontal baler or an auto-tie baler, based on the required throughput.
• Keep in mind that the shredding operation produces dust, thus, the baler should be equipped with a dust collection option, to help minimize the escape of dust in the baling area.
The author is director of regional sales for IPS Balers of Baxley, Ga., and can be contacted at kkorney@aol.com.
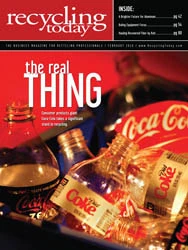
Explore the February 2010 Issue
Check out more from this issue and find your next story to read.
Latest from Recycling Today
- Aqua Metals secures $1.5M loan, reports operational strides
- AF&PA urges veto of NY bill
- Aluminum Association includes recycling among 2025 policy priorities
- AISI applauds waterways spending bill
- Lux Research questions hydrogen’s transportation role
- Sonoco selling thermoformed, flexible packaging business to Toppan for $1.8B
- ReMA offers Superfund informational reports
- Hyster-Yale commits to US production