Balers are a vital tool for companies that process material for recycling because they produce a dense package that can be economically shipped to domestic mills via truck or rail.
In today’s global economy, most companies are looking into export shipments, which create a need for a baler that will provide the bale weights necessary to meet container weight limits. Thus, when looking at balers, these companies should specific focus on the bale size and how easily the bales can be loaded into containers to achieve maximum weight.
Balers used for paper, plastic and light metals basically come in three major configurations: vertical, horizontal and two-ram. Vertical balers are typically more labor-intensive and have to be loaded by hand and the baled tied manually. Horizontal balers can be purchased in either closed-door or open-end model types. Closed-door balers are semi-automatic balers that can start and bale automatically, but the bale has to be tied manually. Open-end balers are automatic balers that can start, bale and tie bales automatically. Finally, two-ram balers typically require an operator, but the unit bales and ties automatically.
QUESTIONS, QUESTIONS. When a potential buyer looks into purchasing a baler, he or she must consider several questions. First, a recycler should consider how many different types of material are going to require baling? Second, of these materials what is the percentage mix by material type? Third, into which market is the product going to be shipped (domestic or export)? Fourth, what is the recycling company’s budget for the baler purchase?
The total tons per month of material to be baled can go a long way in determining the type of baler the recycling company should be looking for. Balers come in a variety of sizes that are driven by different horsepowers, contain various sizes of main cylinders and feature multiple hopper sizes.
In order to make sure recyclers select the correct baler, they should look at the specifications of the balers and consider the cycle time, the total hydraulic force on the press head and the feed hopper size. These factors can help recyclers determine which baler will allow their operations to load material at the rate required to produce the total tons per month desired. Examining the machine specifications can also help recyclers determine which baler has a hopper size that will best accommodate the material to be processed.
In a facility that will bale several hundred tons per month of multiple materials, either the open-end horizontal or two-ram baler can work in these cases.
Typically, if the materials to be baled will all be fiber grades, the open-end baler can be ideal because they offer a continual extrusion bale type, which is often the most productive type of baler. If the mix of material will include plastic containers or nonferrous products, then the two-ram could be used because its operation allows the material to be pressed against a wall and ejected through a tier that can place multiple ties on the bale.
Tightening One's Belting |
Before material hits the baler, it can be transported with varying degrees of efficiency by one or more conveyors. Regarding conveyor belting, the longer and stronger it is, the more it can spell "ROI," for return on investment, according to one supplier. Don Corsaro, V.P. of sales and marketing of Ohio’s May Conveyor, says each recycling application is unique and recyclers must approach it this way. "We study the application and then recommend the belting best suited for each application," he comments. "For example, with paper and cardboard and light metals, your approach may be a rubber combination belt," says Corsaro. "A rubber belt over heavy cross channels with a steel side chain is recommended for this application," he comments. "These are also good for outdoor environments that can quickly rust and bind hinge steel belts and cease operation." Corsaro also says that rubber or "combo" belts are appropriate for applications that may contain liquids, such as beverages, which can collect and pool in one area and damage standard steel hinge links. "If you have co-mix material that may contain metal parts and paper, where the majority of the material is metal, then a hinge steel belt may be the more suitable choice for your application," he comments. "The all-metal construction with various strengthening options can be customized for your particular needs." Other aspects to be considered, says Corsaro, include: conveyor length, incline lift, material size, material type (wet, dry or oily) and material roll back vulnerability. "These factors bring into focus belt drag friction factors, effective chain lubrication and possible cleat configurations that may be required," he notes. Such factors contribute to the overall belt pull that may reach a critical friction point from weight drag, says Corsaro. "Again, by reviewing your unique application a recommendation can be made, which may include the introduction of a friction reduction bearing to reduce the overall belt pull." Corsaro says recyclers should be aware that friction reduction bearings require proper lubrication. One method can include "drilling horizontal shaft holes inward on each side of the through-pins, then adding lubrication fittings at each end," he comments. "This is costly and, arguably, some feel that by drilling in the through-pins their integrity has been compromised. In this case we would suggest a simple automatic side chain lubricating system.This solution saves maintenance departments’ costly time and man power expenses, not to mention the upfront cost on the belting." Being aware of such manufacturing techniques can provide conveyor owners with a stronger and better wearing hinge assembly, resulting in longer belt life with less maintenance, says Corsaro. --Brian Taylor |
Both types of balers are very popular and can be used in all levels of required throughput because various horsepowers and main-bore cylinder sizes are available, making these baler styles capable of processing smaller or larger amounts of material.
One critical difference between these balers is that the two-ram typically produces uniform-sized bales while open-end balers produce bale lengths that can vary depending on the material type and the feed charge.
Both of these baler types can be loaded with one or multiple conveyors and typically fit well at the end of a dual- or single-stream sorting system. Recyclers should give special care to the material type and size to be baled when specifying their balers.
OTHER CONSIDERATIONS. Once a recycler has decided upon a style of baler, many other considerations still deserve attention.
For instance, the feed size is the area at the throat of the baler where the press head is located. If the material will fit in this area, then the baler will accept it with no problem.
For multiple materials recyclers, it should be noted that some new balers are equipped with computers that will allow the operator to change materials to be baled on the fly, quickly changing to the baler set-up most suited for that particular material.
Maintenance and service are also critical considerations. Often, manufacturers offer a scheduled maintenance program, and, when possible, I would highly recommend that program for at least the first two years of service.
The filtration system and oil cleanliness are two of the most important factors in maintaining consistent operation of the hydraulic system at the heart of the baler. Recyclers should make sure to use original replacement parts and to follow the manufacturer’s guidelines to ensure proper replacement of the filters. This will reduce the need for costly replacement parts and for downtime during the baler’s life.
When shopping for a new baler, recyclers can often determine the soundness of the structural design by the baler’s weight. Balers with the same specifications can vary in total weight. Variables like horsepower and main cylinder size can cause this difference.
Heavy structures are preferable because there is a lot of force involved in baling material. Heavy beams should be used in the shear area and the main cylinder mount to eliminate the possibility of damage during the baling process. The liners should be replaceable and made of highly resistant material for longer life.
NEW VS. USED. In some cases, potential purchasers look at used balers as an option for their operations. Recyclers should consider several factors when looking into the used balers.
First, has the baler been refurbished by a reputable company and have the major areas, such as liners, been inspected or replaced to the original manufacturer’s specifications? Secondly, the baler should have updated electrical and hydraulic components when possible. Thirdly, a reputable company will offer a warranty on the major components. Additionally, recyclers should check the specifications from the original manufacturer to assure that the baler will perform the job expected. Care should be taken to make sure replacement parts are still available for the baler and that the filtration system has been properly maintained.
Used balers should also be offered with operators’ and parts manuals and the original manufacturer is still in existence to provide technical support and replacement parts.
Balers, whether new or used, can be purchased to provide a solution to a recycler’s baling requirements if care is taken to investigate the type of baler needed by determining the material and tons per month to be baled.
If export shipments are required, recyclers should look at balers that will produce a bale dense enough to provide the container weights the end user requires. Also, recyclers should make sure they have a relationship with the manufacturer to provide technical support and parts as well as a local service company that can provide emergency service if required. This will allow you to have a long, productive and profitable life with your new purchase.
The author is president of IPS Baler Inc., Baxley, Ga. He can be reached at sidwildes@aol.com.
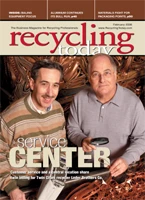
Explore the February 2006 Issue
Check out more from this issue and find your next story to read.
Latest from Recycling Today
- Astera runs into NIMBY concerns in Colorado
- ReMA opposes European efforts seeking export restrictions for recyclables
- Fresh Perspective: Raj Bagaria
- Saica announces plans for second US site
- Update: Novelis produces first aluminum coil made fully from recycled end-of-life automotive scrap
- Aimplas doubles online course offerings
- Radius to be acquired by Toyota subsidiary
- Algoma EAF to start in April