Choosing the right baler is a difficult task. Hopper size, peak tons per hour, energy savings, wire tying and safety issues are all thoroughly discussed prior to making the final baler model decision.
But the job is not complete. After a company has selected the best baler for its application, there is more that needs to be considered. American Baler has developed a list of the top seven things buyers need to do once they have ordered their balers.
1. Foundation
You will need to consult with a civil engineering company with a concrete specialist to ensure that the foundation will structurally support the weight of the baler and other system components. Just ask the baler manufacturer for the weight and dimensional drawings. You will need to supply these to the engineering firm.
2. Electrical
You will need an electrical contracting firm that is certified to handle this type of application. One of the most important pieces of information that the contractor will require will be the FLA or full load amps.
FLA requirements include not only the baler but all components that will comprise your baling operation, including conveyors, air systems and fluffers. Each of these units draws amperage and needs to be calculated into the requirements. The FLA information is required so that the electrician can specify the right electrical components required for the hook-up between the main power source and the main control cabinet (MCC) located on the baler.
If the equipment is going to be used in an outdoor application or in an area that will be exposed to moisture, NEMA 4 electrical components must be specified. Of course this will have been part of the discussion you would have had with your baler dealer or OEM to make sure that the equipment that you have selected meets your defined requirement.
3. Transportation and Off-loading
The big day has arrived. Balers are transported by various means, but usually on flatbed trailers. They are then off-loaded by one of several methods, depending on the installation contractor’s recommendations. The company doing the installation will need to know the weight of the baler, the height and width of your dock and your existing equipment. Again, the equipment weight and dimensional drawings are critical and will be something that the installers will need. Make sure that the OEM supplies them to you. Using the wrong lifting equipment could result in damage of the equipment or even injury.
At American Baler, the factory or our dealers can make the freight arrangements with a trucking firm that has an establshed track record. This includes providing customer service, such as calling you or your installation contractor 24 hours prior to arriving at the site. Providing you or your contractor with advance notice means that the rigging company has time to get the right equipment in place to off-load your new investment.
Many of our dealers are certified to perform the off-loading. Those who are not certified have contacts within the industry to perform this stage of installation. It is critical to have a company that is certified to carry out this stage, as the baler warranty may be voided if it is not done correctly. Most dealers will be more than pleased to supply you references if you are unfamiliar with them.
4. Start-up and Training
You are ready to get to work. However, before you can bale your first bale, start-up and training is the next phase of the installation. Again, many dealers are certified for start-up and training your operators on the features of your new investment; maximizing the baler efficiency, maintenance and safety. At American Baler we also have field technicians on staff certified to provide this service, as well, as do some other manufacturers.
Getting trained is serious business, as properly trained operators are vital to an efficient baling operation. Don’t rely on the "follow Fred around" approach to baler operator training. At American Baler, we believe training is so important, we offer four Service Schools each year.
Service Schools include instruction and hands-on training on how to properly maintain, troubleshoot and operate a baler at maximum efficiency. Representatives from American Baler’s engineering, quality assurance and service departments will provide all instruction. All classes are designed to focus on each attendee’s individual level of experience relative to his or her baler model.
5. Hydraulic Fluids
Your new baler will not be shipped with hydraulic fluid in the tank. Your pre-start-up manual will provide the correct number of gallons of hydraulic fluid to add and a list of suggested fluid manufacturers.
The hydraulic fluid needs to be located at the installation site upon the equipment’s arrival so that the installation contractor or dealer’s installer can add the fluid into the tank prior to start-up. (For some models it is suggested that the hydraulic fluid be added with an inline filter with no more than 10 microns of filtration. Check your operator’s manual for your baler manufacturer’s recommendations concerning hydraulic fluid. )
6. Baling Wire
Make sure that when it comes time to test the machine you have the correct baling wire. Not using the correct wire can cause serious injury to the operator. Talk to your dealer or the equipment manufacturer about the proper wire size and type.
7. Baling Material for Testing
When all of the installation procedures have been completed, you will be able to test the equipment to ensure that it is operating as it should. Getting it right at this time will get you to the production numbers more quickly and with fewer headaches. Make sure that you have enough testing material available to properly test the equipment. Since not all equipment can process the same amount of material, it is recommended that you talk to your dealer or the equipment manufacturer so that you have enough material on hand to do a proper test.
Congratulations, you now have your baler ready to go to work. Together, you, your dealer and the manufacturer should have identified all the applications to make sure that you got the equipment that you needed.
Following these seven steps will help ensure that your baler is ready to go to work as soon as the installation is completed. Working closely with the manufacturer and your dealer, this need not be a complex or unorganized event.
The authors are regional sales managers for American Baler Co., Bellevue, Ohio. They note that the information in this article is not intended to be all-inclusive. Readers should consult the manufacturer for important information pertaining to their equipment and should use this information with OSHA/ANSI regulations and local or state codes.
AN ALTERNATIVE TO WIRE
1) How long has Presona offered plastic baling wire?
We built our first baler with a plastic strapping unit in 2000. This first machine was launched at the Entsorga fair in Cologne the same year.
2) Why might this plastic wire be preferable for recyclers?
The main reason why we developed this feature was the increasing use of solid waste (municipal waste) for incineration purposes, the so called “Waste-to-Energy” plants.
When baling waste for incineration purposes the use of traditional strapping material, the steel wire, causes a lot of problems. The steel wire must be removed before the incineration process which costs both money and efforts. Very often bales are wrapped with plastic foil (for storage) which additionally complicates the removal of the steel wire as it is “hidden” under the foil layers.
The plastic string breaking properties are comparable to the steel wire. Another argument is the cost level. Strapping wire is the most expensive consumable in the baling operation - the cost for strapping material can be reduced by up to 50 % using plastic strings instead of steel wire. With the perspective where steel prices fluctuates strongly and in times when the supply/demand relation is unbalanced this can very well be a growing incentive for recyclers to choose the plastic strapping solution.
3) Why might it be better for consuming mills?
We can see a number of advantages with polypropylene strapping in this sector. The PP material has the same or better tensile strength compared to steel wire. The bales can be stored outdoors - very good UV stability. The weight of strapping media (which is considered as waste in this sector) is reduced - the weight of the PP strings for a typical mill size bale is less than 15 % of the weight of steel wires. The bale handling is safer - no protruding, sharp wire pigtails.
According to our experience, we believe that the entire process of handling the strapping media - from the de-baling to the screening/extraction of the strapping media in the pulping process is fully transferable from steel wire to polypropylene strings.
4) Which materials can be baled with this wire?
As regards the use of plastic strapping for different materials, Presona offers two different baling/strapping systems.
In plants where the material is pre-treated (sorted and shredded to a relative homogenous and dry material) and where the operation requires continous feeding with large material amounts we typically offer our channel balers. Our tying system straps the bale with 5 vertical polypropylene (PP) twine strands.
In plants where no pre-treatment is available or desired we offer a two-ram baler with a tying system that uses polyester (PET) straps. This system functions as a normal steel wire tie system where the bale is strapped while being ejected out of the bale chamber but instead of twisting the steel wire ends together, the PET strap ends are welded together to a strong joint. With this system it is possible to set the number of straps per bale. The material characteristics determine the number of straps required to keep the bale shape. For the “Waste-to-Energy” sector it is worth mentioning that the PET has a high calorific value = an added value instead of a problem as is the case with steel wire.
This means that we can offer plastic strapping for all materials that can be baled.
5) What percentage of market share do you think might someday be claimed by plastic baling wire?
This is a difficult forecast to make. However, considering
- the abovementioned (price and supply of steel vs. plastics),
- the fact that the steel wire in most baling processes is a more “foreign substance” than both PP and PET,
- the favourable handling (and transportation) costs due to the lower weight to mention a few arguments in favour of plastic strapping media, we are quite sure that the market share will grow. How fast and how much is to a large extent depending on the “level and pace of acceptance” from the receivers, not least the consuming mills. If and when fully accepted the plastic strapping can very well reach 50 % of the market share or more.
Get curated news on YOUR industry.
Enter your email to receive our newsletters.
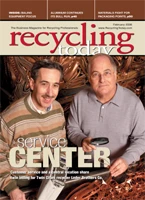
Explore the February 2006 Issue
Check out more from this issue and find your next story to read.
Latest from Recycling Today
- Astera runs into NIMBY concerns in Colorado
- ReMA opposes European efforts seeking export restrictions for recyclables
- Fresh Perspective: Raj Bagaria
- Saica announces plans for second US site
- Update: Novelis produces first aluminum coil made fully from recycled end-of-life automotive scrap
- Aimplas doubles online course offerings
- Radius to be acquired by Toyota subsidiary
- Algoma EAF to start in April