The concept of economies of scale has not been lost on recyclers, many of whom continue to focus on large-volume processing. Corporate consolidation among solid waste and recycling companies has been one impetus toward larger volume plants, but even small- or medium-sized regional operators have been carefully calculating their operations costs.
The result for baler manufacturers has been a larger market for their largest machines.
CONSOLIDATING
"We certainly see a trend toward more centralized and larger facilities to consolidate and reduce operating costs," says Richard Harris, manager of sales for the Macpresse line of balers sold in North America by Sierra International Machinery, Bakersfield, Calif.
"The reason we are seeing increased sales [of large-volume balers] is because companies are trying to reduce their hours of operation and control their costs per ton," he remarks.
When baler sales representatives make the pitch for their high-volume machines, they point to several cost considerations. "These machines can offer higher volumes and heavier, denser bales," Harris notes. "This saves on energy costs, wire costs and freight costs."
Harris says that a new powerful machine making denser bales, depending on the machine it is replacing, can take the same amount of material that once went into 27 bales and fit it into just 18 bales. This can either help a recycler handle fewer bales while reaching a maximum over-the-road shipping weight, or to fit more tonnage onto a rail car. "The company can also store more tons in a smaller space in the warehouse," he adds.
Makers of large balers also tout the energy savings. "Our HHB is very power-efficient," says Jim Jagou of the new high-volume machine from Harris Waste Management Group Inc., Peachtree City, Ga. "Your two biggest costs in baling are for electric power and wire. The HHB has a very low cost per ton for power and also produces a very dense bale, so the cost per ton for wire is also very low."
Erik Eenkema van Dijk makes the same claim for the larger Bollegraaf extrusion balers sold in North America by Van Dyk Baler Corp., Stamford, Conn. "We have energy comparison charts we make after installations, where recyclers can see how their energy costs have gone down," he notes.
LOGGING ON |
Logging On Paper recyclers aren’t the only ones re-thinking the ways they use balers. Scrap metal recyclers are creating a renewed market for baler/loggers as a way to prepare collected scrap for shipment to shredder plants. “Logs are now more acceptable to operators of the large shredders,” John Sacco of Sierra International Machinery, Bakersfield, Calif., told attendees of the Institute of Scrap Recycling Industries Inc. (ISRI) Steel Scrap 101 event. Sacco said that baler loggers that can process from 25 to 250 tons per day of ferrous scrap are being used in areas that are somewhat distant from the nearest shredder yard as a means of preparing obsolete scrap for shipment to a shredder. “It can increase the trailer weight,” he said, as opposed to shipping loose scrap. He also remarked that there are several reasons why some recyclers would rather create logs that are shipped to shredder plants rather than prepare a grade for direct shipment to a steel mill. “Logging can produce from 30 percent to 50 percent more shredder production, so the shredder operators like the material. From the shipper’s viewpoint, they will probably be paid more quickly by a shredder operator, and there is less chance of a load being rejected by a shredder operator compared to a mill,” Sacco commented. Preparing material for further processing at shredder plants also provides a home for material that may previously been packaged as number two heavy melt—a grade that many recyclers find is facing a dwindling demand scenario. |
In some scenarios, larger balers can also help recycling plants eliminate an entire working shift. "The second shift always costs more money—for labor, power, having a supervisor. If you can cut out a whole shift, there are some real cost savings there," says van Dijk.
AFTER THE SORT
Material recovery facilities (MRFs) that handle a variety of recyclable commodities are among the customers buying new, larger machines. Waste Management Inc., Houston, is one example of a company that has undertaken a national plan to consolidate its processing capacity in major metropolitan regions, setting up large single-stream processing plants.
"Municipalities and haulers are bringing everything into single-stream plants," notes Ken Korney, director of worldwide sales for International Baler Corp., Jacksonville, Fla. "We are seeing larger plants with more capacity. The philosophy is, the more you can ship, the chances are your plants are going to run more profitably."
At MRFs, a variety of commodities are being segregated simultaneously, providing a consistent flow of material, but an inconsistent mixture of grades with different baling requirements.
"At most of these facilities, you have people sorting grades and putting materials into bunkers to be baled, as well as material being mechanically sorted for eventual baling," says Sierra’s Harris.
With the aid of a forklift and driver, a variety of different grades can be baled in a single shift, including old newspapers (ONP), old corrugated containers (OCC), used beverage cans (UBCs), steel cans, PET and HDPE plastic bottles and sometimes mixed paper and other mixed plastics.
Larger-volume balers on the market can handle the volume, baler manufacturers say. "The more constant the feed, the more productive the machine is," says Jagou, who is vice president of sales with Harris Waste Management Group. "These kinds of machines generally wait for material."
But buyers of the machines will ordinarily want to make sure they can justify it. "The initial cost is relatively high, so you’ll have to have a certain amount of volume to justify [purchasing] the machine," says Jagou.
VOLUME IN AND OUT
The high-volume baler style that seems to be gaining a lot of attention is the extrusion baler, sometimes also referred to as a channel baler or a horizontal open-end baler.
These balers offer fast, automated production as well as an option for bales with an almost infinite variable third dimension.
"These machines have incredible capacity," says Erik Eenkema van Dijk. He says one of Bollegraaf’s largest models can produce up to 85 tons per hour of some baled commodities.
The variable third dimension—"extrusion balers let you make the bale as long or short as you want," says van Dijk—may be of interest to some recyclers, but almost all of them like the automatic and energy saving aspects of the machines.
Baler designs have also been modified to allow material to be fed into the chamber faster.
One key innovation on this end of the process is the hinge-side baler designed by IPS Balers Inc., Baxley, Ga. According to Sidney Wildes of IPS, the hinge-side models minimize shearing activity while maximizing the cubic feet of material in the feed chamber.
This sequence of operation provides maximum production while using fewer cylinder strokes, according to Wildes. The increased feed hopper size also eliminates frequent bridging of material, which can cause unnecessary cycles without material in the bale chamber, affecting a recycler’s throughput and efficiency.
Such innovations help baler makers point to productivity improvements when they bring new models to the attention of customers.
"We’re selling efficiency and profits, not a piece of equipment," Sierra’s Harris says of the positive attributes of high-volume balers that are presented to prospective buyers.
The author is editor of Recycling Today and can be contacted via e-mail at btaylor@RecyclingToday.com.
Get curated news on YOUR industry.
Enter your email to receive our newsletters.
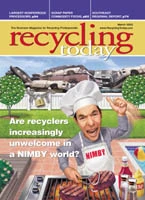
Explore the March 2003 Issue
Check out more from this issue and find your next story to read.
Latest from Recycling Today
- Toppoint Holdings expands chassis fleet
- Lego creates miniature tire recycling market
- Lux Research webinar examines chemical recycling timetables
- Plastics producer tracks pulse of wire recycling market
- Republic Services, Blue Polymers open Indianapolis recycling complex
- Altilium produces EV battery cells using recycled materials
- Brightmark enters subsidiaries of Indiana recycling facility into Chapter 11
- Freepoint Eco-Systems receives $50M loan for plastics recycling facility