The powerful hydraulic cylinders that do the compressing get a lot of the attention when recyclers shop for balers, but they should also make sure the wire tying system they buy is the right one for them, manufacturers say.
The design of the system, operator training, the type of wire used and the material being baled are all factors in the wire-tying equation.
Wire and tying is a considerable cost of operations, most manufacturers agree, so it should not be overlooked.
COST CONTROL
The purchase and use of baling wire is an unavoidable ongoing operating cost for recyclers who bale material. Jim Jagou, vice president of sales with Harris Waste Management Group Inc., Peachtree City, Ga., cites baling wire as one of the two largest operating costs of baling, along with electric power.
But it is not necessarily a fixed cost, as there are variables that can affect the baling wire budget for recyclers. Different gauges and types of wire, as well as different types of tying systems, can affect wire expenses. Additionally, the experience of a baler operator who knows how to use just the right amount of wire can also keep expenses in line.
The two most common categories of wire on the market are black annealed and galvanized wire. Galvanized wire, as its name implies, is coated to offer corrosion resistance. Black annealed wire, however, often costs slightly more (perhaps just one cent per pound more) than galvanized.
The wires come in different thicknesses or gauges, with thinner 14- and 12-gauge wire commonly used when baling paper. "With OCC (old corrugated containers) you can use 14-gauge or 12-gauge wire, but with PET plastic we recommend going to a thicker 9-gauge wire, especially if the bales are going to be out in the sun," says Ken Korney, director of worldwide sales for International Baler Co., Jacksonville, Fla.
Korney notes that on one recent sales call, he observed PET bales tied with 12-gauge wire sitting out—and the strain was showing. "You could see some of the twists untying—in some cases the back two of the five twists," he remarks. "The more memory a material has, the heavier gauge wire you need to utilize."
Richard Harris, sales director for the Macpresse line of balers sold in North America by Sierra International Machinery Inc., Bakersfield, Calif., notes that telephone directories are another material that can require additional wire. While bales of most paper grades can be held together with five straps of wire, "I’ve seen telephone directories [baled] with 15 or 20 wires," he notes.
While recyclers want to make sure they use enough of a suitably strong wire to get the job done, they also don’t want to use more wire than is needed, which adds unnecessary operating costs.
Two-ram balers often come with systems that permit an operator to choose from a wide range of strap counts, introducing a variable that offers flexibility in the process, but, in the hands of an inexperienced operator, can eat into wire costs. "I’ve seen as many as 23 wires on a bale," Harris says of his visits to recycling plants. "When that amount of wire is holding in a bale of plastic, the cost of the wire may exceed the value of the product that is baled," he remarks.
The upside to these systems, Harris notes, is that whatever is being baled, enough wire can be applied to secure it safely for the long-term.
AUTOMATIC
The makers of extrusion or open-end horizontal balers tout the automation of the machines, and this extends to the tying system.
Recyclers are paying extra upfront for additional automation, but ideally they save on labor costs and wire costs if the wire tying systems are configured to use wire efficiently.
Makers of extrusion balers promote the ability of the machines to offer a consistent (and thus cost-manageable) use of wire, although the amount of wire used on a bale can vary along with the variable bale length.
A reliable automatic tying system is so crucial that Erik Eenkema van Dijk of Van Dyk Baler Corp., Stamford, Conn., calls it "the most critical part of the machine. If the motor is the critical part of a car, the tying system is similar for a baler, because it is the most complex part."
Most two-ram balers are configured with an automated tying system made by manufacturers such as U.S. Wire Tie/L&P Wire Tie Systems, Carthage, Mo., or Gerrard Packaging Systems, Portland, Ore.
L&P Wire Tie Systems says its Model 330 system, long marketed under the U.S. Wire Tie brand, "is found on more two-ram balers in North America than any other model," and has been installed with more than 1,200 balers worldwide.
According to promotional material on the company’s Web site, the system is "adaptable to all two-ram balers" and is ideal for baling "paper, corrugated, non-ferrous metals, plastics or virtually any recyclable material."
Sponsored Content
Labor that Works
With 25 years of experience, Leadpoint delivers cost-effective workforce solutions tailored to your needs. We handle the recruiting, hiring, training, and onboarding to deliver stable, productive, and safety-focused teams. Our commitment to safety and quality ensures peace of mind with a reliable workforce that helps you achieve your goals.
Sponsored Content
Labor that Works
With 25 years of experience, Leadpoint delivers cost-effective workforce solutions tailored to your needs. We handle the recruiting, hiring, training, and onboarding to deliver stable, productive, and safety-focused teams. Our commitment to safety and quality ensures peace of mind with a reliable workforce that helps you achieve your goals.
Sponsored Content
Labor that Works
With 25 years of experience, Leadpoint delivers cost-effective workforce solutions tailored to your needs. We handle the recruiting, hiring, training, and onboarding to deliver stable, productive, and safety-focused teams. Our commitment to safety and quality ensures peace of mind with a reliable workforce that helps you achieve your goals.
Sponsored Content
Labor that Works
With 25 years of experience, Leadpoint delivers cost-effective workforce solutions tailored to your needs. We handle the recruiting, hiring, training, and onboarding to deliver stable, productive, and safety-focused teams. Our commitment to safety and quality ensures peace of mind with a reliable workforce that helps you achieve your goals.
Sponsored Content
Labor that Works
With 25 years of experience, Leadpoint delivers cost-effective workforce solutions tailored to your needs. We handle the recruiting, hiring, training, and onboarding to deliver stable, productive, and safety-focused teams. Our commitment to safety and quality ensures peace of mind with a reliable workforce that helps you achieve your goals.
Sponsored Content
Labor that Works
With 25 years of experience, Leadpoint delivers cost-effective workforce solutions tailored to your needs. We handle the recruiting, hiring, training, and onboarding to deliver stable, productive, and safety-focused teams. Our commitment to safety and quality ensures peace of mind with a reliable workforce that helps you achieve your goals.
Makers of extrusion balers offer unique variations of automated tying systems, according to Sierra’s Richard Harris. Most of these systems tie five straps simultaneously, reducing the tying cycle time.
Erik Eenkema van Dijk, whose company markets extrusion balers made in the Netherlands by Bollegraaf, notes another advantage of this tying method. "If there is a problem with just one of the five tying mechanisms of an extrusion baler, it means you’re missing just one of the five straps. In a system used by two-ram balers, if there is a problem, the whole baler system is down," he remarks.
There has been some experimentation with cross-wrap systems, especially on European-made machines, but Sierra’s Richard Harris says cross-wrapped bales can provide extra work at consuming mills.
"When paper bales go to the mill, they are conveyed for cutting, often done by either a person with a pair of shears or by an automated saw that cuts the wires," says Harris. "The mills with the automated systems are geared to accept bales with wires going in the same direction. A cross-wrapped bale might not be compatible with their de-wiring system," he notes.
Making bales that are welcome at mills is the ultimate goal for shippers, adding yet one more consideration for recyclers who are shopping for a new baler and its accompanying wire tying system.
The author is editor of Recycling Today and can be contacted via e-mail at btaylor@recyclingtoday.com.
Get curated news on YOUR industry.
Enter your email to receive our newsletters.
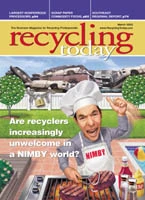
Explore the March 2003 Issue
Check out more from this issue and find your next story to read.
Latest from Recycling Today
- Altilium produces EV battery cells using recycled materials
- Brightmark enters subsidiaries of Indiana recycling facility into Chapter 11
- Freepoint Eco-Systems receives $50M loan for plastics recycling facility
- PET thermoform recycling the focus of new NAPCOR white paper
- Steel Dynamics cites favorable conditions in Q1
- Hydro starts up construction in Spain
- Green Cubes unveils forklift battery line
- Rebar association points to trade turmoil