You’ve finally closed the door on 2009 and you’re glad to exchange last year’s low prices and even lower demand for the opportunities of 2010. A quick look at your latest financials, though, reveals an unwelcome expense line creeping into the spotlight and it’s labeled “equipment maintenance.” Your decision to delay buying that new baler last year was necessary to preserve capital, but now you’re paying the piper in maintenance and labor costs.
The frustration of spending good money after bad dredges up thoughts of Popeye the Sailor’s famous phrase, “That’s all I can stand; I can’t stands no more!” With that you decide it’s time to shop for a new baler, one that works the way it’s supposed to…every day. A baler with a warranty. A baler that’s shiny on the outside with oil on the inside, not the other way around.
Your situation may differ from the scenario above, but if you do find yourself shopping for a new baler, then I hope this article helps you select the right machine for your operation.
Alright then, let’s dig in and compare all the models and sizes and features and options from all the manufacturers and…organizing a bowl of spaghetti would be easier, besides, that topic would better fit the scope of a textbook. Instead, I’m going to concentrate on some important items that often get overlooked or discounted during the baler buying process.
USE AVAILABLE RESOURCES
Too often buyers distance themselves and don’t benefit from the knowledge and resources sales representatives and manufacturers offer simply because they don’t want to be “sold.” Worse yet, they may rely on only one of those sources to provide guidance and endorsement for all the rest.
For the technical folks who have spent years in the industry and don’t really want more advice on balers, please consider the following: Any manufacturer worthy of consideration has surely built and installed many more balers than you’ve owned and likely has learned from each installation. I would guess that most manufacturers approach their business like we at Excel Manufacturing do, constantly focusing on making our balers better. This continual progression results in new systems and features as well as improvements to existing models. Inviting manufacturers’ representatives to help with the evaluation process can help you make the best decision and often delivers solutions for problems you didn’t even recognize or didn’t think a baler could solve.
Imagine where personal computers would be today if everyone shopping for office equipment in 1984 told IBM, “I don’t have time for a meeting, all I want is a quote,” and then compared this number with a Smith-Corona typewriter quote and made their decision.
BEYOND SPEED
Auto-Tying One On |
Open-end auto-tie balers can start, bale and tie bales automatically. They offer a continual extrusion bale, which can result in high productivity, say their manufacturers. Mike Connell, sales manager for Balemaster, Crown Point, Ind., says auto-tie balers offer efficiency, first and foremost. “Most auto-tiers can complete the bale tie operation in less than 30 seconds, while a person will need approximately five to 10 minutes.” While auto-tie balers can excel at baling fiber grades of all types, plastics traditionally have been more challenging. However, some manufacturers have added features to improve auto-tie balers’ performance when processing plastics. Mark Neitzey, Southwest regional sales manager for Van Dyk Baler Corp., based in Stamford, Conn., says the company’s Bollegraaf balers can be equipped with three features to improve their performance on plastics: a hydraulic automatic perforator, a double wire feature and a channel pressure release switch. “Those three things working together allow us to make a very nice, dense plastic bale.” Consistent feeding is an important factor in achieving the best performance with an auto-tie baler, Neitzey says, adding that automatic feeding devices/storage containers can be effective. Conveyor belt speed also is a factor. “You can stagger the speed of multiple conveyors to help thin material out,” he says. Preventive maintenance can ensure a baler operates at peak performance. With auto-tie balers, operators will want to pay special attention to the tying mechanism, inspecting it daily. “A daily routine should include thorough cleaning of the tying device,” Connell says. – DeAnne Toto
|
Recyclers are often forced to make frequent material changes these days because of constraints on storage space. This puts significant demands on a baler that are no less important than speed. The correct baler must provide for quick material changes with no cross contamination of bales, and its wire tying system must be adaptable to provide ample holding power for highly resilient materials, like PET plastic, yet minimize wire costs when baling lower-rebound materials, like paper, corrugated and aluminum cans.
While a variety of baler styles, such as vertical, horizontal and two-ram, are available, I’m going to focus on the styles I know best: two-ram and manual-tie full-eject horizontal balers.
Full-eject and two-ram balers expel each bale completely before beginning the next bale, helping to prevent cross contamination during commodity changes. Additionally, wire ties can be made manually or programmatically, providing flexibility. When baling aluminum cans, for example, wire savings are possible if some tie slots are skipped on a manual-tie baler, while two-ram balers allow you to adjust the tie count and spacing between ties. Conversely, with manual-tie balers, PET bales requiring more holding power can be single- or multi-strapped in all slots, and thicker wire also can be used, if desired. On a two-ram baler, the tie spacing can be reduced, increasing the total number of ties per bale. Two-rams also can double strap at any position required.
Material contamination is difficult to put a price on until you have a container or two of material rejected, but wire cost savings can be estimated. The sales reps you work with should detail this information as part of their ROI proposal.
When buying a baler, you not only need to consider its initial cost, but the overall cost of operation as well. However, many buyers make decisions based on the purchase price alone. We routinely discover ROI proposals that demonstrate savings that easily justify a more expensive baler and, in some cases, cover an entire lease payment from day one.
Downtime is a factor that contributes to a baler’s overall cost. When thinking of downtime, you might envision breakdowns and failures, but people can sometimes disregard downtime that is part of the baler’s normal operation, such as the time required to load baling wire. You will want to compare and qualify equipment under consideration by doing a review of the design, construction techniques, weight, etc. Remember to talk to references as well.
ROOM FOR GROWTH
If recycling is your core business, consider your company’s growth plans when determining your baler throughput requirements.
If recycling is not your core business and you’re baling boxes at a distribution center or paper at a printer, there is no advantage to buying a machine with more capacity than required.
Once you’ve determined your throughput requirements, narrow your search to qualifying balers. When comparing balers on published cycle times, consider that different manufactures calculate cycle time differently. Some report a “dry cycle” time, which is based on the time it takes under no load to move the platen from home, down the baling chamber and back, while others report the time it takes to complete a round trip with maximum penetration, while others report the time to the bale completion zone or anywhere in between. Be sure to make apples to apples comparisons. Visit a facility using the model of baler you’re considering to bale materials similar to those your operation will be handling.
PROPENSITY FOR DENSITY
Bale weight and density are important factors to consider when shopping for a baler. Commodities shipped by truck or container are of more concern than others. Baled OCC shipped in containers can result in excess freight or price penalties if the combination of bale weight and size doesn’t fill the container well.
Rely on the baler manufacturer’s rep to provide you a stacking and loading plan for each material that you handle.
Also consider if the bales are of a size that can be transported two at a time into the container with a forklift. When narrowing the field, a valuable comparison to make is the number of trips a forklift must make to load a container to capacity with the bales produced by a given baler.
SEEING IS BELIEVING
Ask sales reps to set up visits to facilities similar to yours and go see the balers at work. Customers are your best gauge of whether you’ll be happy with the baler you choose, so get multiple references.
Sales people instinctively pick good references, so take the wheel yourself and ask for three or four references with consecutive serial numbers from each manufacturer under consideration.
I hope you spend the time and effort to get the right equipment for your business.
The author is president of Excel Manufacturing, St. Charles, Minn. He can be reached via e-mail at twondrow@excelmfg.com.
Get curated news on YOUR industry.
Enter your email to receive our newsletters.
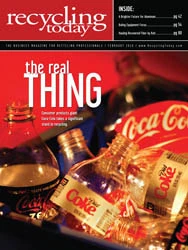
Explore the February 2010 Issue
Check out more from this issue and find your next story to read.
Latest from Recycling Today
- ReMA opposes European efforts seeking export restrictions for recyclables
- Fresh Perspective: Raj Bagaria
- Saica announces plans for second US site
- Update: Novelis produces first aluminum coil made fully from recycled end-of-life automotive scrap
- Aimplas doubles online course offerings
- Radius to be acquired by Toyota subsidiary
- Algoma EAF to start in April
- Erema sees strong demand for high-volume PET systems