On one hand, providing either plant-based or mobile secure shredding can guarantee a steady flow of material to their recycling yards. However, the downside for some recyclers is that the shredded material is often far less valuable than non-shredded material because of quality and contamination issues. Therefore, shredded bales will command less money from mill operations that consume recovered paper.
While many paper mills are already struggling with contamination problems arising from single-stream collection programs, many also now have to contend with bales of recovered fiber that may contain a far greater amount of non-fibrous materials.
SECURITY CENTERED
Tim Parrish, president of Trinity Recycling Services, an Indianapolis shredding company, says his company spends a fair amount of time trying to educate clients about keeping microfilm, paper clips and other materials that may pose problems for paper mills out of collection bins.
While continuous education is effective, shredding companies’ common mantra is that providing secure shredding services is their first priority. Therefore, these companies may end up with a lower quality shredded pack. However, secure shredding companies with plant-based operations have some leeway to remove undesirable materials prior to shredding, providing a fairly clean shredded pack to their consumers.
Trinity Recycling Services takes additional steps to boost the quality of its material. It will "back charge" its document destruction customers if they place contaminants into secure containers. This gives Trinity’s customers a greater incentive to place only designated materials into the secure containers. Using the back charge allows Trinity’s customers to see the cost differential between a load of material that can be baled and shipped to a mill and one that will be either rejected or sharply downgraded.
Reed Bates, an area manager for Weyerhaeuser Recycling, says that while the company asks its customers to keep paper separate from other materials, "We have to balance the demands for confidential destruction."
Ultimately, the onus on many paper mills becomes greater, as they may be required to add more cleaning and screening equipment to keep unwanted materials from entering the pulping or recycling stages.
Another area creating concern on the part of paper mills is the shrinking of shred sizes. A plant manager for a Pennsylvania-based shredding firm says that with the smaller shreds, a paper mill may feel the document destruction company is trying to hide contaminants. As shredded paper sizes near the "pulverized" stage, some mills are balking at taking in this material out of fear of creating problems in the recycling process.
The Pennsylvania-based shredder notes that with the exception of keeping old newspaper out of the stream, his plant-based shredding company shreds everything together. "Mills understand what is in the office waste," he says.
As for the quality of the material, he says, "We don’t have any problem selling our material to mills." He adds, "When prices are on the way up, they will blend it with non-shredded material."
Tom Wagner, with Allegheny Paper Shredders, a Delmont, Pa.-based company that provides equipment for the shredding industry, says he hears very little feedback from clients and customers who are concerned about the value of the shredded material. In addition to selling equipment to document shredding firms, Allegheny also operates a secure shredding company called Allegheny Records Destruction Service in New Alexandria, Pa.
For traditional document destruction firms their first priority is providing a service; any money that they make on the back end is secondary to the service they provide on the front end of the operation. This means that mills will have to start putting in equipment that will allow them to handle a wider range of material that travels along with shredded fiber. However, the costs of installing such equipment can be significant, as can the outthrows and rejections.
AT THE MILL
Additionally, many mills are feeling pressure from their consumers to provide paper with greater recycled-content levels. For high-end printing and writing paper producers this is a more daunting challenge. While these paper mills traditionally used the highest grades of recovered fiber, as more companies opt to have a greater amount of their paper shredded, less unshredded material is available.
Weyerhaeuser’s Bates says that the pressure to boost recycled-content paper is forcing retailers, and ultimately paper mills, to continue using more of this recovered fiber.
While many shredding companies say that providing secure shredding operations is first and foremost, consumers of shredded fiber are finding that the quality of the material is degrading.
For paper mills, this is unsettling news, as single-stream collection is already seen as one source of increased contamination. Now many mills that had been large buyers of white office paper are seeing greater volumes of incoming mixed, shredded material.
David Knight, the head of fiber procurement for SCA Tissue North America, Neenah, Wis., says that perhaps 50 percent of the recovered fiber being delivered to SCA’s mills is shredded.
One advantage that SCA has is the flexibility to move between producing white tissue paper and brown, industrial paper, depending on the quality of the recovered material it receives. While recognizing that shredding companies, especially mobile shredding companies, are limited in their ability to sort out paper that does not meet the quality needed to produce higher quality grades of paper, if SCA receives a load that has a higher level of kraft and non-freesheet paper, it will be used to make the industrial paper product. Additionally, the price SCA pays for shipments that are deemed closer to mixed paper and a shipment that is considered an office pack grade are significantly different.
Working to the advantage of many paper mills is the overall growth of the shredding industry. As competition intensifies, profit margins among shredding companies are shrinking. This is crystallizing the need to maximize their profits on the back end. With this in mind, Knight says that more shredding companies, including mobile and plant-based, are calling and asking how they can improve the shredded packs they are sending to SCA’s plants.
While Knight says the two parties have a better understanding of the other’s position, issues will continue to be problematic. While SCA has the opportunity to shift the loads to different production cycles, pulverized material is unacceptable.
TALKING SPECIFICS
While educating shredding companies as to what is acceptable, Knight doesn’t feel that adding a new grade to the PSI (Paper Stock Industries chapter of the Institute of Scrap Recycling Industries Inc.) standards would do much good for the shredding side of the business. For one, Knight says there are just too many variations in shredded material to come up with any particular standard that would work for different mills.
Secondly, for many with mobile shredding operations, there really isn’t any way to verify the quality differences in material prior to shredding, leaving these operations uncertain as to whether they could meet some specifications.
Bates says Weyerhaeuser does the best it can to provide a balance between a cleaner pack and customers’ security needs. "The operators who run the shredding equipment have to balance the demand for confidential destruction with a better shred," he says.
Ultimately, Bates says it is inevitable that mills will have to put in new equipment at the front end of their systems to get cleaner raw material for the pulper.
The challenge, as Knight points out, is that as mills invest in more cleaning equipment to handle the current amount of non-pulpable material, the trend toward shredding continues to grow, resulting in even more shredded material.
While SCA as a mill can take a wider range of shredded and unshredded paper, other mills may have much tighter tolerances and could see their available supply of raw material shrink noticeably.
Bates says one of the best ways to keep the supply of material from degrading further is to highlight the price opportunities that exist between the different quality packs being shredded.
For its part, PSI does not yet have a grade definition for shredded material, but a host of mills are looking at implementing their own standards. Georgia-Pacific’s buying arm Harmon Associates, based in Jericho, N.Y., is reportedly considering the introduction of a shredded paper grade, though it is not yet official.
While many paper mills are grudgingly accepting more shredded paper at their mills, Roy Geigel, with Fox River Paper, a long-time recovered-fiber consuming mill in Wisconsin, sees it as a great opportunity.
Geigel acknowledges that some tricky issues must be resolved, but he says Fox River is able to take in practically all the shredded paper that is shipped to the mill, with the exception of shredded material from the healthcare industry. Geigel says oftentimes his company is able to purchase fairly high quality shredded material at a lesser value.
He says that when dealing with his supplier base, as long as the shipped material meets the mill’s specifications, he will accept it.
While Fox River is willing to accept a wider range of shredded material, Geigel cautions about problems associated with shredding material from the medical industry. "The singular problem," he stresses, "is that with medical files you get more pill bottles that have adhesive labels." This causes the biggest problem and will likely result in rejections by the mill.
However, as opposed to many mills that are focusing on the decline in their raw material quality, Geigel looks on the bright side. "While at first you can look at it as a negative, it is one hell of an opportunity. We will take the necessary steps to handle the material," he says.
Geigel adds that the amount of shredded paper Fox River takes in has grown from about 20 percent to more than 80 percent of its raw material.
"We don’t have specifications for size," he adds. Instead, if a supplier is interested in shipping the material, Fox River takes in a test load to test its quality. If there isn’t a problem, it will use it.
"It isn’t a problem, but a perceived problem," Geigel adds. "Our approach is simple," he notes. "Here is what I use. If the material makes it, then we will use it."
The author is Internet and senior editor of SDB magazine and can be reached at dsandoval@gie.net.
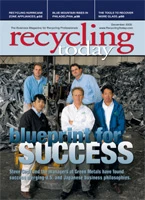
Explore the December 2005 Issue
Check out more from this issue and find your next story to read.
Latest from Recycling Today
- ReMA opposes European efforts seeking export restrictions for recyclables
- Fresh Perspective: Raj Bagaria
- Saica announces plans for second US site
- Update: Novelis produces first aluminum coil made fully from recycled end-of-life automotive scrap
- Aimplas doubles online course offerings
- Radius to be acquired by Toyota subsidiary
- Algoma EAF to start in April
- Erema sees strong demand for high-volume PET systems