"When we were trying to find a location for our material recovery facility, we were told that there was not any property that would fit our needs available," recalls Mike Morris, Green Tech partner and project manager.
In 2005, with the search for the new site underway, Morris and several other company partners attended the National Brownfields Association Convention, and the information the team garnered from that event led them to start looking into brownfields as a possible home for the planned recycling facility.
Morris says the team took what it learned at the convention and immediately started looking for brownfield sites upon returning from the event. "The Studebaker Plant 8 had been empty for 23 years—locked down and overgrown," Morris says. The company purchased the former automotive manufacturing plant and began the work of transforming it from an overgrown eyesore into a C&D processing facility and recycling transfer station.
EYE ON THE MARKET
Green Tech’s South Bend, Ind., recycling facility and transfer station opened on Earth Day 2008—April 22. The operation accepts C&D materials for recycling, including metal, brick, concrete and asphalt, as well commingled residential recyclables and municipal solid waste (MSW).
Good Neighbors |
Green Tech Transfer and Recycling and its affiliate Mother Earth LLC embarked on a massive public relations blitz for the redevelopment work on the Studebaker facility, and the effort has more than paid off, according to Mike Morris, partner and project manager. The company’s experience with the first proposed site for its recycling and transfer facility was a PR nightmare, Morris says. "We met resistance the first time," Morris says. "When we went for this second piece of property, we got 100 percent approval from the neighborhood and city government. We went from worst-case scenario to complete success." From the project’s earliest stages, Morris says the company was active in communicating with the community. "We started talking to the neighborhood—we became part of the community instead of just preaching to the community," he says. The outreach program included educational programs with local schools, as well as a foreign exchange student program that offered students from around the world the chance to study brownfields. "We wanted people to realize we were part of the community, not just outsiders coming in, and that we are trying to take something and revitalize it and bring jobs," Morris says. Additional information about Green Tech is available online at the company’s Web site www.recycletoday.com. |
The facility encompasses a solid waste transfer station with a material recovery facility (MRF), a mixed C&D recycling facility and an outdoor pad where concrete and wood are crushed and ground, respectively.
Material is currently being sorted manually, with crews pulling out valuable commodities. The facility is in the midst of a sizable equipment upgrade and is installing an automated sort system by Hampstead, N.H.-based Green Machine Sales LLC, says Morris.
The system being installed at Green Tech is designed to be adaptable to allow it to process all of the material Green Tech accepts, including C&D, MSW and commercial waste, according to John Green, president of Green Machine. (See sidebar "Equipped for Growth," on p. 46) The system will be capable of processing between 25 and 40 tons per hour, Green says.
Wood is currently ground for the local mulch market, although Morris says the company is focusing on developing a fuel product. "My direction is to take our wood and turn it into biofuel," says Morris. "Animal bedding is seasonal, so is mulch for us here in Indiana, so we’re trying to be ahead of the curve for the biomass market, which is emerging here."
The 34-acre site served as the former home of the Studebaker 8 plant, which was founded in 1854 and manufactured automobiles until 1963. The site was then used as a storage facility for the next 30 years, but sat vacant from 1993 until 2005, when Green Tech identified it as a possible location for its proposed recycling and transfer facility.
SALVAGE JOB
Before deconstruction could start, a number of environmental remediation tasks had to be completed, including clean up of lead-contaminated soil and asbestos surveys and remediation of the paneling from the 665,000-square-foot building.
Award Winner |
South Bend, Ind.-based Green Tech Transfer and Recycling LLC and its affiliate company Mother Earth LLC earned valuable experience and industry knowledge by embarking on a brownfields redevelopment project, says Mike Morris, partner and project manager for Green Tech. The company also earned accolades from the state—winning a Governor’s Award for Environmental Excellence for its redevelopment of the Studebaker Plant 8 facility in its home town of South Bend. The award honored Green Tech and Mother Earth’s achievements in the Recycling and Reuse category. The Governor’s Awards for Environmental Excellence are open to all Indiana facilities, government agencies, individuals and other groups that implement exemplary environmental projects with measurable results. The awards recognize Indiana’s leaders who seek out and use innovative environmental practices. The award was presented during the Association of Indiana Solid Waste Management District’s 16th annual conference held in 2008. Green Tech Transfer & Recycling LLC and Mother Earth LLC have also applied for the 2009 EPA Brownfield Phoenix award. |
Recycling was a huge element in the project. The company found profitable reuses for much of the material from the demolished building. Revenue from recycled materials—some $1.4 million—paid for eight months of demolition activities, with less than 1 percent of the demolished materials going to a landfill.
Concrete and bricks were crushed and used as foundation base under the construction of the new building and roadways. Green Tech also donated this material for the parking lot at the Southside Little League baseball field. More than 7,500 tons of base aggregate was produced.
Cement blocks from the plant were used to build the break room and supervisor’s office in the new building. In addition, a semi-load of bricks was shipped to a local brick company, and the remainder was sold for reuse.
Approximately 2,000 tons of iron and steel were shipped to steel mills in Gary, Ind., and 5,000 cubic yards of wood from the roof was ground up into mulch.
In addition to the revenue generated by the recovered recyclables and a $4 million investment for clean-up, deconstruction and redevelopment from Mother Earth LLC, the project received grant money from the Indiana Brownfields Program and EPA Brownfields Assessment grant fund to help finance the project.
The company opted not to pursue the U.S. Green Building Council’s (USGBC)
Leadership in Energy and Environmental Design (LEED) green building certification, but did incorporate a number of green building features in addition to the extensive C&D recycling activities the project employed, Morris says. The company installed skylights to make better use of natural lighting and to save on energy costs. Rainwater runoff is captured and used for washing and process water.
The company also used recycled materials in the construction of the facility. Recycled steel from the demolition was used for new construction of the tipping floor of the transfer station, in the push walls and door protectors, support posts and steel bollards to protect the inside of the paper baling facility.
THE NEXT CHALLENGE
The Studebaker Plant 8 project was Green Tech and Mother Earth, LLC’s first foray into brownfield redevelopment. The team has been so impressed with the results that the company has committed to developing more brownfield properties and has added brownfields redevelopment to its roster of services. "[This project] has shown us that there are great opportunities in the brownfield redevelopment area, but you have to have the support staff and patience to make it work," Morris says.
Green Tech reaped a number of benefits by choosing a brownfield site for its
Equipped for Growth |
Green Tech Transfer and Recycling LLC is in the midst of an upgrade that will increase the automation of its South Bend, Ind.-facility. Green Tech is installing an automated sort system by Green Machine Sales LLC of Hampstead, N.H., which it hopes to have operational by spring 2009. The system is designed to be adaptable and able to process all of the materials Green Tech accepts, including mixed C&D debris, municipal solid waste (MSW) and commercial waste, according to Green Machine Sales President John Green. Green says the average throughput of the system being provided to Green Tech is between 25 and 40 tons per hour. Material starts its journey on an extra heavy duty apron steel belt infeed conveyor, which conveys it up to an elevated sorting platform, Green describes. Material is then dropped within a dust enclosure and deposited on a sort belt conveyor. The first sorting station is designed with a narrow deck to allow bulky OCC (old corrugated containers) to be thrown over the railing. Then traditional drop chutes are provided within the same bunker for the removal of smaller-sized OCC. Three more bunkers, which allow for the positioning of two roll-off containers each, are under the mezzanine deck to accommodate additional grades of recyclable materials, including multiple grades of plastics, wood and ferrous and nonferrous metals. Recovery rates for selected demolition debris have been recorded as high as 70 percent, according to Green. |
The company has joined the National Brownfields Association and has become more active in that organization. Green Tech is eager to share its story and to encourage brownfield development. "It allows the industry to give something back to the neighborhood," Morris says. C&DR
The author is managing editor of C&DR and can be contacted at jgubeno@gie.net.
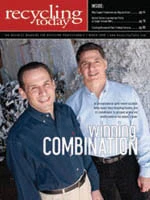
Explore the March 2009 Issue
Check out more from this issue and find your next story to read.
Latest from Recycling Today
- Combined DRS, EPR legislation introduced in Rhode Island
- Eureka Recycling starts up newly upgraded MRF
- Reconomy Close the Gap campaign highlights need for circularity
- Nickel carbonate added to Aqua Metals’ portfolio
- EuRIC, FEAD say End-Of-Life Vehicle Regulation presents opportunity for recyclers
- Recyclers likely to feel effects of US-China trade war
- BCMRC 2025 session preview: Navigating battery recycling legislation and regulations
- Yanmar Compact Equipment North America appoints new president