
Before COVID-19 and accompanying restrictions caused an economic downturn in the first half of 2020, the auto shredding market already was considered to be overbuilt by many plant operators in that line of business.
With industry conditions that might have included overcapacity even before inbound scrap volumes dropped by double-digit percentages, however, few in the scrap metal industry have been questioning the prominent place of shredders in their sector.
“It’s the most efficient piece of processing equipment that this industry has ever seen by far, and they’re being made bigger and better and tougher than they’ve ever been,” Ben Abrams, CEO and president of Pennsylvania-based Consolidated Scrap Resources (CSR), said of auto shredders at Recycling Today’s 2020 State of the Scrap Recycling Industry Roundtable in May.
The participants of the roundtable had plenty to say about the state of shredding in 2020. While much of it was positive, such as the comment by Abrams, a note of concern was raised about the U.S. Environmental Protection Agency’s (EPA’s) efforts to scrutinize and minimize shredding plant emissions.
Not out for the count
The number of shredding plants in the United States grew in the second half of the 2010s, according to Recycling Today’s research for our 2020 list. (Click here for the list.) While some companies with multiple shredder locations idled one or more plants, and a few smaller companies also exited the business, other companies added smaller or mobile shredders.
Many operators also learned how to run their shredders efficiently for fewer weekly operating hours, and several companies have invested in rebuilt or entirely new plants. Such investments seem to back up Abrams’ contention that shredders remain an efficient way to size-reduce and then sort obsolete scrap, including auto bodies and appliances.
Downstream sorting technology continues to be the focus of many investments, as equipment and technology providers work in cooperation with scrap processors to devise new ways to recover greater quantities and improve the quality of metals exiting their yards.
In Ohio, auto shredding plant operator Milliron Recycling has a nonferrous recovery system that includes eddy current separators and sensor sorting technology, plus a dry media plant equipped with X-ray and optical sorting technology supplied by Germany-based Steinert and Wendt Corp., Buffalo, New York. The firm and its owner Grant Milliron also have focused on maximizing the value of the wire portion of the plant’s shredder infeed and output. In 2013, the company commissioned the installation of an insulated copper wire recovery plant that features equipment from SGM Magnetics of Italy.
In 2018, Milliron invested in additional wire chopping equipment to upgrade that wire. The new system incorporates two shredders, with the stainless steel being removed after the first one, which was supplied by American Pulverizer of St. Louis, Milliron says. The recycler says his goal is to seek the highest grade of copper possible. “We might even end up with a No. 1 copper chop,” he told Recycling Today in late 2018.
On Long Island, New York, Kevin Gershowitz and Gershow Recycling are undertaking a shredder downstream investment project in 2020, he told Recycling Today during the roundtable in May.
“We are in the middle of building/erecting a new screening plant and an eddy current plant,” Gershowitz said. “It’s going to be fairly massive. Our intention is to be able to process at the rate of close to 100 tons per hour of ASR (auto shredder residue).
He added, “We’re moving along quite well, and we hope to be ramping up the conveyors and motors sometime in late August or early September. We are full steam ahead on the project. We actually believe that investing in times like this is the strategic time to invest.”
However, Gershowitz also told roundtable participants that at the same time his company is investing to improve profitability, it also could be required to spend money to try to meet U.S. EPA emissions targets tied to the shredder.

Clean it up
In comments published as part of Recycling Today’s State of the Scrap Recycling Industry supplement, Gershowitz said, “The big kick now with [the] EPA on a nationwide basis is volatile organic compounds (VOCs), which are emitted at shredders.”
The EPA defines VOCs as “any compound of carbon, excluding carbon monoxide, carbon dioxide, carbonic acid, metallic carbides or carbonates and ammonium carbonate, [that] participates in atmospheric photochemical reactions.”
Gershowitz said the EPA has targeted auto shredders in part because of “residual oil left in the engine” of shredded auto engines or other motors. “The shredder doesn’t get hot enough” to burn off this oil, he added, “but it gets hot enough to create fumes, and the fumes get hot enough to become VOCs that go into the atmosphere.”
Gershow Recycling has been selected by the EPA for emissions testing on its shredders, with Gershowitz saying as of May that “the writing is on the wall” that shredders in urban and suburban areas like his likely will be required to install a thermal oxidizer.
That technology cost General Iron Industries in Chicago $2 million for a system by Lake Zurich, Illinois-based Catalytic Products International (CPI).
The CPI system is scheduled to be moved to a new, indoor General Iron location several miles south of the current one at the end of the year under a plan enacted by the city and Ohio-based Reserve Management Group, which now owns General Iron. (The company’s current shredder on the north side of Chicago was ordered to shut down following a fire in mid-May. As of August, repairs had been made at the site and the company was awaiting inspection by the city’s Public Health and Buildings departments and the Chicago Fire Department to be cleared to resume shredding.)
CPI says its regenerative thermal oxidizer (RTO) destroys VOCs by heating shredder exhaust gases at extremely high temperatures. The hot RTO exhaust gases then pass through a quench/packed tower scrubber, evaporating a portion of the scrubber water and generating steam.
At the roundtable, Gershowitz said such technology “all sounds great in a controlled environment, [but] shredders are not controlled environments. They are controlled chaos.” He expressed concern that the loud “booms” created when sealed units or gas tanks with vapor combust in the oxidizer will increase noise complaints and shredder wear and tear.
“Beside that operational issue,” Gershowitz said, “the competitive issues is another one.” He said shredding plants in EPA nonattainment areas (cities and inner-ring suburbs) will now have a $2 million or more expense (plus related operating costs), while plants in outlying areas will not. “If I have an operating cost of $8 to $10 per ton higher for these new environmental controls and others do not, we’re going to see scrap cross some county and state lines to the lower cost operator [because] the implementation of controls is not uniform around the country.”
Despite the EPA scrutiny and potential added costs, the shredding plant continues to gain votes of confidence from scrap recyclers. “They’re being made efficiently, and I think you’re going to continue to see these machines be made and be the foremost piece of processing equipment going forward,” Abrams said at the roundtable.
While acknowledging the regulatory challenges, he added, “For the most part, there’s nothing to compete with shredders in terms of processing scrap at the rate that it needs to be processed and to the specs that it needs to be processed.”
Get curated news on YOUR industry.
Enter your email to receive our newsletters.
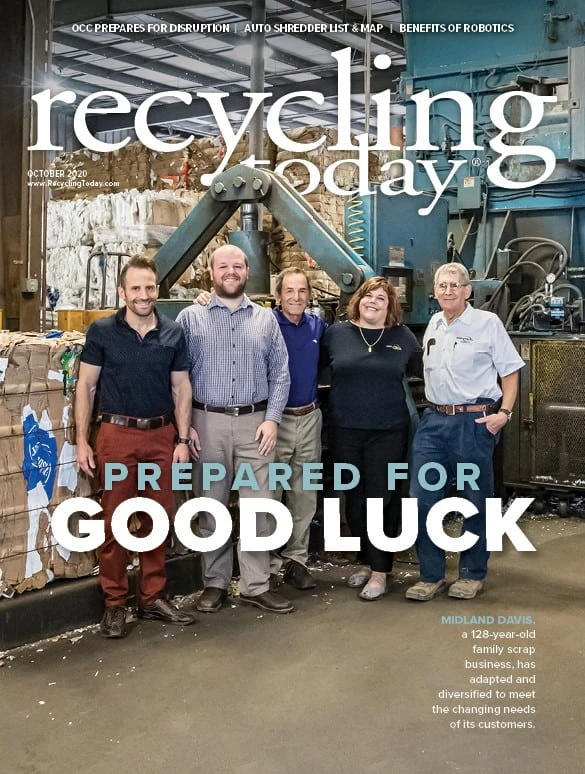
Explore the October 2020 Issue
Check out more from this issue and find your next story to read.
Latest from Recycling Today
- Ascend Elements appoints new president, CEO
- Culligan International to provide aluminum water bottles at Chicago running events
- Returpack reports increased DRS activity in Sweden
- Trade groups align against European export restrictions
- Construction, auto sectors show mixed signals
- Politics in Turkey threaten recycled steel outlet
- Toppoint Holdings expands chassis fleet
- Lego creates miniature tire recycling market