
Editor’s Note: Studies referenced in this article are based on a Metso EtaRip preshredder and a 98-inch Metso Texas Shredder. Actual results will vary based on equipment and operating conditions.
Designed to meet the grueling conditions inflicted by processing bales, logs, end-of-life vehicles (ELVs) and heavy grades of scrap, automobile shredders are the backbone of many scrap yards. However, these machines are not impervious to their rigorous workloads and the potentially debilitating effects of unshreddable materials or other hidden dangers in their feedstocks.
Faced with the ongoing challenges of potential shredder damage and operating risks, shredder owners around the world have integrated preshredders into their operations. The allure of preshredders has increased as operations managers and scrap yard owners recognize the enhanced value this machinery provides through operational efficiencies, reduced downtime, quality throughput and lower cost per ton processed.
Preshredder principles
Installed upstream of the primary shredder, preshredders can help to reduce and defuse material before it is fed into the shredder. In addition to reducing the risks of unshreddables and explosions, preshredders can homogenize incoming material, allowing the shredder operator to better control the feed rate for the primary shredder. This can lead to a more uniform flow of material that increases production capacity and reduces the cost per ton of material processed.
Preshredders can differ from one another in terms of power, chamber size, ease-of-operation through the human-machine interface (HMI), and efficiencies based on the code that controls the operational characteristics. The Metso EtaRip, for example, is a low-speed, high-torque preshredder that tears apart bundles, logs, bales or ELVs before this material is fed to the primary shredder.
A set of parameters in the operation code creates hands-free operation, controlling the rpm, oil pressure and rotational direction to produce efficient operation while also protecting the machine from inappropriate materials. Additionally, the operator of the crane that is feeding the preshredder can use a remote control to override the preshredder’s operation at any time.
Operational perks at the primary shredder
A preshredder can improve wear life on the primary shredder’s castings, protect against unshreddable or explosive materials and reduce peak power loads to the shredder.
By processing a homogeneously sized product, yards also might be able to achieve higher average throughput from their auto shredders. In our testing of auto shredder throughput before and after the installation of an EtaRip preshredder, the average tons per hour processed increased by more than 17 percent.
Depending on a yard’s downstream processing capacity and market conditions, some yards might benefit by yielding the same tonnage of output but with fewer operating hours. This can reduce operator burnout, labor costs and energy costs without sacrificing throughput. In addition, it can allow for routine scheduled maintenance to keep the shredder operating in peak condition.
By stabilizing the operating load of the auto shredder with preprocessed material, it can operate in a more efficient energy range, reducing or eliminating “peak loads” as charged by utility companies. This is an especially important feature for shredder yards that are charged for electricity on a power demand basis.
Also, the homogenous infeed to the primary shredder helps to create a full-box shredding scenario that runs on constant rpm with higher output. The reduced drop in rpm arising from high drive motor loads also can result in less stress to the shredder’s driveline, resulting in less maintenance and longer life.
Lower cost per ton is an important goal for all shredder operations. Preshredders can support lower costs in various categories.
More even loading of the primary shredder can result in fewer surges, more consistent full-box shredding, less process time inside the primary shredder and a steadier discharge stream. In a power-consumption analysis, Metso recorded nearly a 14 percent kilowatt-per-ton energy savings by preprocessing infeed material using the preshredder.
Additionally, because the preshredder releases entrapped dirt and soil, this abrasive material does not enter the primary shredder’s chamber. That filtering process, coupled with the preshredding of high-density bales and the rejection of unshreddables, improves the life and value of shredder consumables by reducing premature damage to hammers, rotors, grates and liners. In testing, we found a 20 percent reduction in hammer consumption when material was preprocessed with a preshredder. Similarly, less high-impact shock results in longer life for the complete power driveline.

Safety and environmental considerations
In addition to the operational benefits of preshredders, they can help to reduce or eliminate the risk of explosions and fires inside the primary shredder from undetected gas bottles, fuel tanks or other hazardous elements in ELVs, logs or bales.
A preshredder can lower a yard’s risk by minimizing explosions and fire propagation and the associated losses with incidents of this magnitude. This helps to create a safer working environment for the shredder operator and other scrap yard employees.
Moreover, preshredders can decrease the noise pollution commonly associated with unshreddables and explosions in the primary shredder. This not only provides for better community relations but also for a safer and more pleasant working environment. The open chamber and the slow rpm on the start rotors on these units provide an improved scenario to mitigate explosions and deal with fires in an offline configuration, lowering the risk of damages across the entire shredding line. Additionally, some preshredders can be equipped with dry fire suppression systems.
In addition to the environmental and safety benefits of a preshredder, suppliers continue to develop dust control, air treatment, volatile organic compounds (VOC) and sound control solutions for auto shredder operators.

Where a preshredder makes sense
Market conditions in the metals recycling industry are ever-changing. Between steel price fluctuations, competition and the ongoing effort to become more efficient, the need to reduce a shredding operation’s cost-per-ton processed is growing. This competition can also extend to the acquisition of shredder feed stock. But, for many, that also can increase the risk as unknown materials are fed into the shredder.
A preshredder can be an ideal solution for scrap yards that want to increase throughput, reduce wear parts costs, shredder downtime and operational risks while also increasing operational efficiencies and diversifying their feedstock options with a larger market reach.
In addition, preshredders can be helpful to scrap yard operations that have existing shredders that are too small to handle high-density bales or for operations that have aging shredders that are prone to break down more frequently.
Reducing explosions and downtime at the primary shredder are common reasons shredder operations consider preshredders. But, with increasing demand and stronger competition, the improved efficiencies and lower cost-per-ton processed are key factors driving the integration of preshredders.
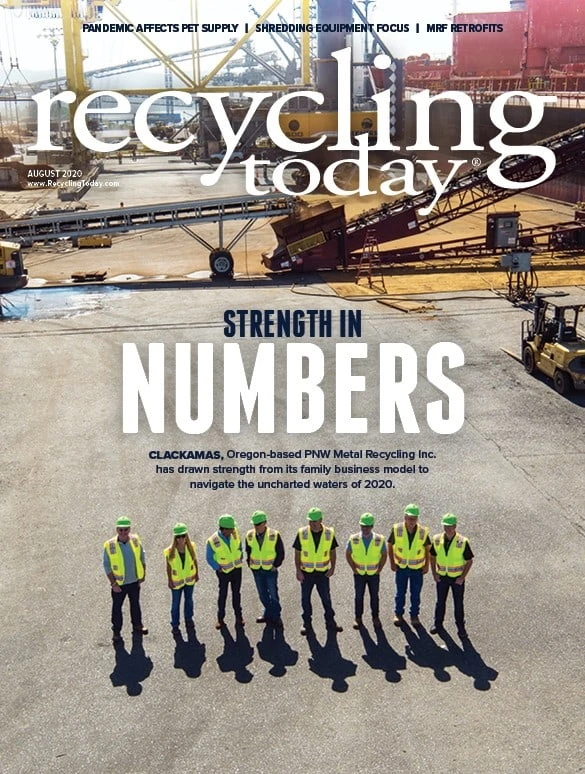
Explore the August 2020 Issue
Check out more from this issue and find your next story to read.
Latest from Recycling Today
- Massive Chinese steelmaking rebound recorded in March
- LME looks into sustainable metal pricing
- OnePlanet Solar Recycling closes $7M seed financing round
- AMCS launches AMCS Platform Spring 2025 update
- Cyclic Materials to build rare earth recycling facility in Mesa, Arizona
- Ecobat’s Seculene product earns recognition for flame-retardant properties
- IWS’ newest MRF is part of its broader strategy to modernize waste management infrastructure
- PCA reports profitable Q1