
In most industries, standardization helps to maintain efficiency, quality and compliance, and in the automotive recycling industry, standardization is a collaborative process.
The Manassas, Virginia-based Automotive Recyclers Association (ARA) has teamed up with Georgetown, Texas-based United Recyclers Group LLC (URG) and Team PRP, Louisville, Kentucky, to develop operating standards for auto recyclers under a single, unified certification program.
Earlier this year, the ARA and URG officially merged the ARA’s Gold Seal standard and URG’s 9000 certification program, focused on quality assurance.
On the heels of the announcement and in collaboration with Team PRP, a group of independently owned auto recyclers, ARA and URG published a uniform set of parts preparation and shipping standards for the automotive recycling industry, serving as a foundational document for the developing Gold Seal Quality Assurance Certification program and ushering in a new era of industry accordance.
Staying gold
The merged Gold Seal Quality Assurance Certification program aims to create a unified framework to ensure customer service and part quality and reliability.
Shannon Nordstrom, chair of ARA’s Certification Committee and current ARA second vice president, says collaboration between ARA and URG had been on his radar for years.
“I thought it was important, in my leadership position, we explore the idea of one industry certification,” he says.
As both groups worked independently over the years to gain traction and secure stakeholders for their respective certification programs, Nordstrom says it made sense for them to come together to see what they had in common.
ARA’s Gold Seal Program was established in 1997 to ensure customer service and part quality at ARA-Certified Auto Recyclers (CAR). The program has provided professional automotive recyclers with a set of standards for general business practices and environmental and safety issues and aims to maintain quality assurance protocols and measure how recycled original equipment (ROE) parts are delivered to customers.
Prior to becoming ARA-certified, Nordstrom’s company, Garretson, South Dakota-based Nordstrom’s Automotive Inc., mainly operated as an auto repair business, selling previously wrecked, repaired vehicles. After reviewing ARA’s certification programs, he identified a guide to elevate his family’s business.

“[The certification program] creates the road map for a business to get the marks on the things that are important to run a professional automotive dismantling and recycling business,” Nordstrom says. “With any business you need a set of guidelines. … If you’re going to grow, it has to be understandable, measurable and repeatable.”
Today, Nordstrom’s Automotive is a professional automotive parts business, selling ROE, remanufactured, original equipment manufacturer (OEM) surplus and aftermarket parts, having grown from five to 80 employees since 1988.
URG’s 9000 certification references the International Organization for Standardization (ISO) 9001 standard, which focuses on customer satisfaction through quality assurance protocols, as well as ARA’s CAR certification.
“We’re not competing against each other or thinking that there’s some sort of a rivalry between the two because, at the end of the day, we both do many different things. Why don’t we see what we can come together on?” he says.
The Gold Seal Quality Assurance Certification program is in the works, awaiting final legal decisions from the groups, though Nordstrom says terms have been agreed upon.
The guiding committee will be formed with equal representation from both organizations, and the two groups have been working with an independent contractor to build out the program using shared resources.
“By the vision we have now, ARA will be the base of the certification,” Nordstrom says. “People will join ARA if they want to be involved … and ARA will provide the management of the certification program. But you’ll have to be involved in URG also.
“We’ll share the burden of expense and process between the two organizations so that ARA can remain the international standards body as it is, and URG can continue to work on bringing to the table quality assurance and what partners [in the professional collision repair industry and automotive repair industry] are looking for.”
Building trust
The Parts Preparation & Shipping Guidelines began as a benchmark for the Gold Seal Quality Assurance Certification program under development.
Based on PRP-Northeast-developed standards, the guidelines are a living document outlining best practices for preparing, shipping and delivering used auto parts. They will be updated as needed.
Team PRP Executive Director Jarret Hann says when it comes to selling recycled parts, standardization is necessary.
“Recycled parts removed from used vehicles will naturally have a different look than a new part,” Hann explains. “The Northeast Team PRP partners developed the guide for cleaning, inspection, shipping and packaging of parts bought and sold among one another. The guide served several purposes: a training tool, a manner for holding other partners accountable and a tool that helped build trust.”
ARA Executive Director Sandy Blalock echoes this sentiment around building trust within the industry.
“If we all agree to a certain type of standard on the parts and the shipping and everything else, then when our product arrives at our customer’s door, it’s something that they’re excited about,” she says. “They know they’re working with a qualified professional that prepared and got these parts ready for use, either on their customers’ vehicles or on their own personal vehicles.”
ARA has guidance documents in place for other certification areas, including high-voltage vehicles and recalls.
Blalock says the parts preparation and shipping document came together in about six months after ARA’s Certification Committee identified a need within the Gold Seal program to support parts preparation.
Blalock attributes the relatively short time frame for developing this document to the work PRP-Northeast has done over the last decade to develop its standards.

“We looked at what ARA had, what PRP had, what everybody had, and we put that all together,” she says.
Hann says the standards were developed to promote uniform products to end consumers.
“If one partner isn’t investing the time to prepare and package a part they are selling to another member, they are essentially passing on that work and cost to the buyer—it’s a vicious circle.”
The Parts Preparation & Shipping Guidelines also aims to eliminate confusion between providers and consumers about the parts being shipped.
For example, when a dealership orders a door for a damaged vehicle, it will receive a shell. All other parts, such as hinges and handles, are excluded, and the repairer will attempt to salvage the original parts from the damaged vehicle and attach them to the door shell. However, if the customer needs more than the shell, a door assembly must be ordered instead.
“We wanted to define the actual parts,” Blalock says. “What comes on a door shell? What comes on an assembly? What do the standards look like when [certain parts] are included with that assembly?
“Part of this is to make sure we’re talking the same language as our customers. We and our customers are understanding what they’re going to get, and there are no surprises when those parts show up at their doorstep.”
The Parts Preparation & Shipping Guidelines are available on the URG, ARA and Team PRP websites.
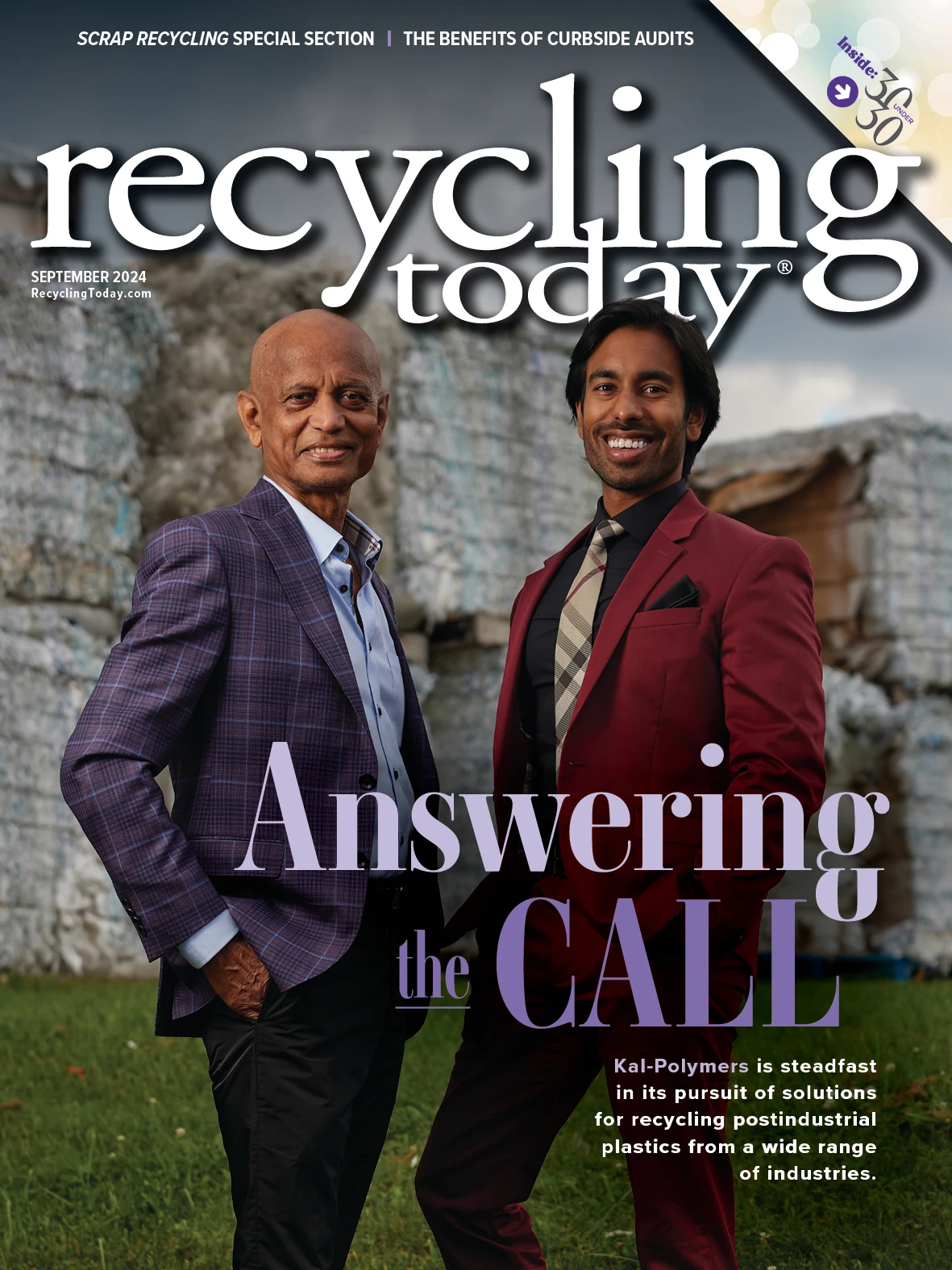
Explore the September 2024 Issue
Check out more from this issue and find your next story to read.
Latest from Recycling Today
- Athens Services terminates contract with San Marino, California
- Partners develop specialty response vehicles for LIB fires
- Sonoco cites OCC shortage for price hike in Europe
- British Steel mill’s future up in the air
- Tomra applies GAINnext AI technology to upgrade wrought aluminum scrap
- Redwood Materials partners with Isuzu Commercial Truck
- The push for more supply
- ReMA PSI Chapter adds 7 members