Nearly five years ago, I authored an article for Recycling Today titled "Preventive Medicine" about auditing electronics recyclers. (The feature is available from the Recycling Today Web site at www.RecyclingToday.com.) The article provided a tutorial on how to properly audit an electronics recycler. My inspiration came from years of hosting generator audits at electronics recycling facilities around the United States.
The good news was that the electronics recyclers always passed the audits. The bad news was that the electronics recyclers always passed the audits.
Why? Most of the audits were traditional environmental, health and safety audits and did not include critical elements for qualifying an electronics recycler. Key factors that would reveal whether hazardous scrap materials were being exported to developing countries were completely overlooked.
Fast forward nearly five years. Although the U.S. still has no federal standards for electronics recycling, generators have made significant strides in their efforts to effectively qualify their electronics recyclers to assure proper management throughout the end-of-life cycle.
What is driving this progress and where do we need to go from here?
EXIT NEPSIIn early 2004 The National Electronics Product Stewardship Initiative (NEPSI) became the poster child for failed efforts to establish a national electronics recycling system when the U.S. Environmental Protection Agency cut off funding for the project and major OEMs could not agree on a financing mechanism to pay for the recycling. However, tremendous work was accomplished in identifying what responsible electronics recycling should entail and what would have been required of recyclers wishing to process material collected under the NEPSI program.
Even though the process "failed," the large number of stakeholders and other NEPSI participants, armed with information, took the guidelines they developed to their own organizations and incorporated them into RFPs (request for proposals) for electronics recycling services. Moreover, they began looking for compliance with those standards when conducting audits.
ENTER EPEATIf NEPSI became the symbol of failure, EPEAT (Electronic Product Environmental Assessment Tool) has the potential to become the symbol of success in a federal environmental initiative involving electronic product stewardship.
EPEAT, modeled after the U.S. EPA Energy Star program, identifies electronic products with superior environmental performance from the
Visit the following Web sites for additional information on auditing electronics recyclers and their downstream vendors: • Responsible Recycling (R2) Practices for Electronics Recyclers – accessible via stakeholder Hesstech LLC’s Web site at www.hesstech.com/usepa.htm • CHWMEG Inc. – www.chwmeg.org • Electronic Product Stewardship Canada (EPSC) Recycling Vendor Qualification Program – www.epsc.ca/rvqp.htm • Institute of Scrap Recycling Industries Inc. (ISRI) Best Management Practices – accessible at www.isri.org (select "Specs & Markets" > "Electronics" > "Resources" > "ISRI Electronics Recycling Operations Practices" • International Association of Electronics Recyclers, IAER Certification Standard – www.iaer.org/certificationstandard.doc
manufacturing stage through the product’s useful life onto its disposition.
Auditing Resources
One product attribute an OEM can claim to reach the highest EPEAT status (Gold) is to have a legitimate recycling program in place for the product. But, to get credit for this attribute, the OEM must conduct annual audits of all first-, second- and third-tier recyclers. Ah, downstream due diligence!
But, in practice, is this really downstream due diligence?
MaSeR is often a second-tier recycler that is subject to audits by generators looking to evaluate an electronics recycler’s entire downstream to qualify that responsible recycling is taking place. Armed with audit criteria, such as what has been laid down by NEPSI and EPEAT, these auditors are asking more of the right questions more frequently, but not all of the questions.
Here is what’s missing. Recently, MaSeR was audited by a consultant representing a major OEM. It was one of the most rigorous EH&S and recycling audits we’ve had. After the audit, the consultant joined us for lunch, and I complimented him on his thoroughness. Then I asked him if he wanted me to tell him a critical element that he missed.
"Certainly." He asked, "What do you think I missed?"
I queried, "You know how you asked for a list of all our downstream markets, and I gave that to you, and we went over all of them?"
"Yes," he replied.
"Well, you never asked me for proof," I responded.
Without reviewing actual shipping documents and accounting records showing that we were shipping to those markets, he had no way of knowing if we were actually doing what we said.
WARNING TO AUDITORSIn my 2003 article, I warned generators not to be swayed into thinking everything with a recycler was OK just because they got a "certificate" of recycling, which anyone can produce on a printer. Without due diligence, the certificate means nothing.
Now, as generators and auditors are more frequently conducting due diligence, some not-so-honest electronics recyclers have come up with other ways of creating smoke and mirrors to prevent from revealing how they are really managing material.
Among the smokescreens du jour are fabricated bills of lading (BOL) and accounting records. Many of these forms can be purchased at any office supply store and printed to say anything. So, a recycler, for example, could produce a BOL and/or bill of sale saying all its scrap is going to MaSeR and, instead, load up export containers and ship its material overseas.
Fortunately, qualifying the downstream vendors is very easy. All it takes are a few phone calls to the vendors identified on the BOLs to verify that they actually do receive material from that recycler. And, don’t forget to qualify the volume of material the recycler claims to be shipping to a particular vendor.
Although more generators now understand the importance of an on-site audit, some believe that if a recycler has been audited at all, then it is somehow sanctioned or "approved."
An influx of computers, printers, copying machines and other obsolete items has prompted MaSeR Corp., Barrie, Ontario, Canada, to expand its recycling facility. The company’s Lauren Roman says MaSeR reached its processing capacity in the fall of 2007 and began holding back new suppliers. She attributes the deluge of electronic scrap from North American recyclers to "customers [who] are increasingly demanding total domestic recovery." Keith Blinn, the company’s vice president of operations says, "Between January and August of this year, we went from receiving about 400 tons to 800 tons per month. We needed to hit the brakes a bit at that point to ramp up our system throughput to ensure we could continue to service the market." As volume increased in late 2007, MaSeR secured a 70,000-square-foot facility adjacent to its original plant. Also, since August MaSeR has added shifts and is installing new processing equipment to further address its in-bound volume. A portion of the company’s new investment will allow it to segregate plastic earlier in its process, ideally creating more marketable plastic scrap. – Brian Taylor
A good example of this is facilities that have been audited by an organization called CHWMEG Inc. CHWMEG is a trade association that conducts independent reviews of commercial "waste" facilities to help members manage the many facility audits that are required yearly. Each year, members select the facilities they need to audit, and independent environmental firms perform the audits. The results are then made available to members who must determine whether an operation meets its corporate standards.
Electronics Recycler Adds Capacity
CHWMEG and other independent auditors do not "approve" processors; they provide generators with information so they can approve or reject a facility.
IN THE FUTUREFor nearly the past two years, the U.S. EPA has been convening meetings of a group of stakeholders to establish nationally recognized voluntary standards for recycling electronics. These responsible recycling ("R2") practices will be used in accredited certification programs that assess electronics recyclers’ environmental, health and safety and security practices.
Certification to these standards will provide generators with a simple means of verifying that an electronics recycling company is forthright and responsible about how it manages used and end-of-life electronic equipment. At the same time, responsible electronics recyclers will finally have a means of highlighting their values and performance to customers.
Although final consensus has not yet been reached on all issues, the stakeholders agree that the document must be field-tested prior to finalizing. This was expected to begin in the fourth quarter of 2007.
In the meantime, generators of electronic scrap can assure their recycling program meets their own standards by:
• Visiting the primary processing facility and, when possible, secondary and tertiary facilities;
• Conducting business, environmental, health, safety and security audits;
• Mapping downstream processors and verifying processes and compliance;
• Getting proof by reviewing bills of lading and accounting records as evidence that materials are going where the recycler says they are going and calling the downstream vendors to verify the relationships and volumes; and
• Re-auditing annually.
By following these simple steps, companies can be assured that their electronics are being recycled in an environmentally and socially responsible way.
The author is executive vice president of MaSeR Corp., Barrie, Ontario, Canada, and can be reached at LRoman@masercorp.com.
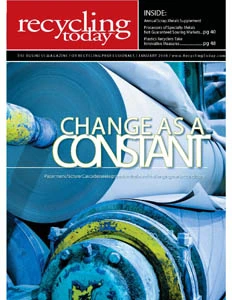
Explore the January 2008 Issue
Check out more from this issue and find your next story to read.
Latest from Recycling Today
- Nucor receives West Virginia funding assist
- Ferrous market ends 2024 in familiar rut
- Aqua Metals secures $1.5M loan, reports operational strides
- AF&PA urges veto of NY bill
- Aluminum Association includes recycling among 2025 policy priorities
- AISI applauds waterways spending bill
- Lux Research questions hydrogen’s transportation role
- Sonoco selling thermoformed, flexible packaging business to Toppan for $1.8B