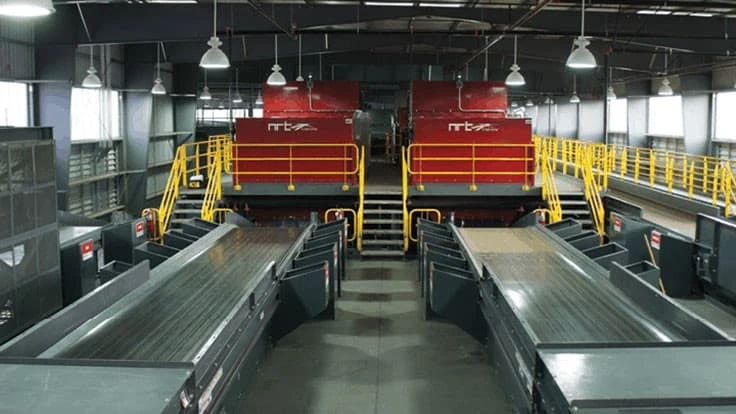
Photo courtesy of Athens Services

As older material recovery facilities (MRFs) are upgraded and new MRFs built, they are incorporating tools that enable operators to capture data in real-time that can help operators improve uptime and throughput.
About six years ago, Athens Services built and opened a mixed-waste MRF in Sun Valley, California. The MRF features a system from Bulk Handling Systems (BHS), Eugene, Oregon, that includes a supervisory control and data acquisition (SCADA) system that is designed to enable MRFs to improve efficiencies by tracking data. Today, the 80,000-square-foot MRF has about 150 employees and processes about 15,000 tons of commercial and residential single-stream mixed waste per month. The MRF is permitted to receive 1,500 tons of waste per day.
Athens Services, headquartered in City of Industry, California, operates a total of three MRFs: a 25-year-old MRF in City of Industry; a MRF it acquired from Crown Recycling near Sun Valley that processes municipal solid waste (MSW) and construction and demolition (C&D) debris; and the Sun Valley MRF that it built six years ago.
Riel Johnson, director of resource recovery at Athens Services, says his team was very excited in 2014 that the BHS system featured SCADA, a system of software and hardware that would provide the MRF with data to optimize operations.
“It took us some time to get a handle on what SCADA meant and what it provided, but as we learned about it, we started asking for more information,” he says.
SCADA is a feature many systems integrators offer. The SCADA system from BHS provides a customized supervisor dashboard, production reports, downtime tracking and cause analysis, staffing charts and integrated data collection.
Prior to installing the system, Johnson says Athens Services relied on manual reports at its MRFs to analyze operations. A foreman would manually report how long a line or screen was down, for example. However, that method wasn’t always reliable—sometimes foremen would forget to write certain things down. But with SCADA and automated systems, human error is less of an issue.
“With a fully automated SCADA system, the data is in real-time,” he says. “You can’t manipulate it. It’s created a non- biased report for us, which in general has made us a much better operator.”
In the last six years since adding the SCADA technology at the Sun Valley MRF, Athens Services has collected and analyzed data from that system as well as from several in-house apps the company has developed.
Putting SCADA to work
Brian Hunter, operations manager at Athens Services’ Sun Valley MRF, says the SCADA system consistently gathers data throughout the day.
“At any moment, we can go [into the system] if we want to know what’s going on,” he says.
Johnson adds that SCADA will send a report at the end of the day that highlights different data points that summarize operations at the MRF. Then, on a weekly basis, team members sit down to discuss the findings in those reports.
Hunter says the program provides a variety of important data points, including the system’s speed, material types sorted, capture rates, average hertz rate and screen angles. The company can use the data to make adjustments to screen angles and system speed in real-time based on material observations.
“We’re able to extract that data to know what we can do differently the next day,” Hunter says.
Some data SCADA provides help with productivity, such as determining how presorting affects downstream operations. “As presort folks wrestle through the material, it can slow the waste stream down,” Johnson says. “The significance of that is maybe we’re loading the system too high, or maybe there are some other things that are happening up front.”
The program also provides a good indication on how much uptime or downtime the MRF is experiencing.
“[I]t allows us to know how much we were up, whether we were up 95 percent of the time, 80 percent of the time, 100 percent of the time,” Hunter says. “Then it also tells us downtime. It also tells us in minutes and shows us exactly when it happened so we can figure out what caused the downtime.”
For instance, a report might say the MRF achieved a production time of four hours and 37 minutes out of a possible four hour and 45 minute shift, highlighting the few minutes of downtime. SCADA reports will identify how much downtime was because of operational issues and how much downtime was because of process issues.
By tracking downtime this way, Athens Services determined it would be more efficient to feed the system with a material handler than with a loader.
“A material handler increases our uptime,” Johnson says. “By tracking this uptime and downtime, and then doing some root-cause analysis, we’ve been able to make improvements all the way to the tipping floor and how we feed the system.”
Hunter and Johnson add that data from SCADA enable the MRF to be proactive when it comes to preventive maintenance. For example, SCADA monitors the amperage of the equipment’s motors. Johnson says if SCADA alerts him that amperage is too high on a motor, it could indicate that something is wrapped around a shaft.
“We look at that as a precursor or warning that a part may need to be rebuilt or replaced, or there’s something going on in the bearing,” Johnson continues. “So, data is also helping us do maintenance and improve uptime in general.”
Building an app
Waste characterization studies provide good data on the material stream at a MRF. For a while, Athens Services did these studies by hand. But two years ago, Hunter says the company decided to develop a waste characterization app that could help improve accuracy in those studies.
“Our IT team, myself and a few others spent some time, combined what was happening via hand and tweaked it to be able to use it on an app,” Hunter says.
The MRF’s waste characterization app allows employees to input waste characterization data on tablets and smartphones. That information goes to a shared file using the company’s intranet. Hunter says information tracked on the app includes location of material collection, material type processed (such as recyclables, MSW, C&D and food waste), routing information, weights and photos. He adds that Athens Services has some employees on waste characterization teams that will input this information throughout the day. He says the app also allows employees to enter information about things like recovery goals and recovery rates.
An employee might enter bin weight, and the app tracks average weight for the bin over time. Or, an employee can enter information about residue to indicate what material is being missed in the sorting process, Hunter says.
“With the waste characterization app, whether it’s looking at one piece of data or data over a period of time, it just allows us to be able to find areas of improvement based on what we’re receiving,” he says. “It’s getting a representative sample from the residue, the process pile, whatever it might be. That representative sample is what we actually will characterize.”
Athens Services also developed a load-check app in 2019 to assess loads as they come to the MRF’s tipping floor. Hunter says before developing the app, MRF employees checked incoming loads by hand.
With the app, the MRF’s employees can assess loads for recyclability as they come in and feed information into the app. The data are then shared with the haulers who brought in the material.
Johnson says he hopes that sharing data with haulers will help them to clean up their routes and provide better education to customers if loads are consistently poor quality.
He adds that bale counts are another important data point. “This helps us with commodity sales and inventory,” Johnson says. “That’s data we gather at the end of the day from the baler operator and guys loading the containers that we utilize.”
Always improving
Hunter says the SCADA system and the apps provide Athens Services with a great deal of information, which can be overwhelming to analyze. However, he says, focusing on data points that affect throughput, recovery and uptime are typically most important. The Athens Services team has learned what data to analyze most through trial and error.
“You can’t be afraid of the data but, at the same time, you can’t be afraid to make a mistake,” Hunter says. “One thing I’ve learned working with Riel and the team is that the data maybe didn’t look good this week, but that doesn’t mean you ignore it. Let’s look at the data a different way and figure out how we can get better next week.”
Johnson offers that applying data at the MRF is like an art and a science.
“It’s nice to use data as an adjustment to the way you operate. But I don’t think an operator should ever rely strictly on data, nor do I think an operator should rely strictly on their gut,” he explains. “I think it’s a hybrid. You need to be able to rely on both.
“A lot of operators might be intimidated by data,” Johnson continues. “That’s absolutely acceptable and expected, but maybe just ease your way into it. Maybe pick a couple of data points or parameters that you want to analyze and just focus on those two. Then slowly broaden your scope. You just kind of develop a comfort. And then, it kind of almost becomes fun mining the data.”
Athens Services is a recycling and waste diversion company based in Southern California. Family-owned and operated since 1957, Athens was founded on the principle of providing exceptional service by hiring and developing great people while fostering a safe, healthy and sustainable environment. Today, the company teams with local communities, as well as private institutions and government agencies as a zero waste partner.

Explore the June 2021 Issue
Check out more from this issue and find your next story to read.
Latest from Recycling Today
- USTR announces phased measures designed to address China’s shipbuilding dominance
- APR, RecyClass release partnership progress report
- Clearpoint Recycling, Enviroo sign PET supply contract
- Invista expanding ISCC Plus certification program
- Redwood partnership targets recycling of medium-format batteries
- Enfinite forms Hazardous & Specialty Waste Management Council
- Combined DRS, EPR legislation introduced in Rhode Island
- Eureka Recycling starts up newly upgraded MRF