
Making money from auto shredder residue (ASR) requires more than simply bringing cars in the front gate. A huge factor, as Earl Weber Jr., owner of Garden Street Iron and Metal in Cincinnati, knows, is recovering all the metals possible. That means the big stuff and the fines. Gathering fines not only adds to the amount of aluminum, copper, stainless and other metals recovered, it also reduces expenses on the back end.
Keeping an eye on details is one reason the family-owned operation is celebrating its 55th year in business this year. “Our goal is to recover more metal out of the fluff,” Weber says. He figures Garden Street’s installation of an Eriez FineSort allows the company to do just that.
“Our goal is to pull more minus-5-millimeter material out of the fluff,” Weber says. “We are getting an extra 3 percent, conservatively.”
He says he is less fixed on the exact percentage than he is on knowing that Garden Street’s processing line is more efficient and effective. “I don’t have as much of a trash bill for shredder residue,” Weber says.
Think small
“Fines are something that can’t be overlooked anymore,” agrees Ryan Njavro, general manager for ferrous and nonferrous products at U.S. Shredder and Castings Group, headquartered in Miramar Beach, Florida. “The value is huge, and the system is too easy to operate now not to use.”
A
Today, small to midsize shredder operators represent 90 percent of the market, according to Bill Close, applications engineer at Wendt Corp., Buffalo, New York. He says all those shredder operators should be making fines and
The remaining 10 percent of the market—those with large shredders or multiple shredders located closely together—have the volume to consider making additional investments that put them in the position to make high-quality refinery products. “These same fines processors will be in the business of buying the concentrates from the other 90 percent of the market,” Close says.
Fines often are referred to as “
“Fines ASR will typically constitute anywhere from 40 to 60 percent (by weight) of the ASR,” says Mike Shattuck, market manager of recycling for Eriez, Erie Pennsylvania. ASR
“In today’s market,
He notes that the figure will vary from operation to operation, depending on the shredder feedstock and the equipment installed at the residue plant. Regardless of where on the spectrum a recycler falls, Haegelsteen says his company’s system will leave no more than 0.2 percent of nonferrous metals in the MFP (
In a typical auto shredding system, roughly 2 percent to 3 percent of the fines stream is nonferrous, with an additional 5 to 7.5 percent being ferrous, according to Haegelsteen.
Concentrated effort
A certain volume of fines must be generated before a recycler can consider investing in fines recovery equipment. Njavro says he would like to see around 1,000 tons per month going to the landfill. “In some cases, lately people are seeing their 5/8-inch and under [fines] making up 50 percent of the total weight generated in ASR,” he says.
Close says 1.5 percent of the typical total ASR stream easily can be concentrated with screening and ECS technologies that are well-applied. An additional 0.75 percent can be concentrated using sensor-based and other technologies. Shredder operations of all sizes can benefit from screening and ECS technologies, while midsize and large shredder operations can benefit from the addition of sensor-based technologies.
“All recyclers should make concentrates,” Close says, adding that some should go even further.
In automobile shredding operations, typically nonferrous materials less than 1 inch in size are considered fines. Materials smaller than 1/4-inch are considered by most as
As much as 10 percent nonferrous can be recovered from the ASR between the
“Magnetic dirt will affect the recovery and grade of the
In fact, one of the main reasons nonferrous metals are lost in ASR fines is because of the entrapment of that valuable fraction in the magnetic dirt. Haegelsteen says that can represent 30 percent to 40 percent of the fines.
“The higher the moisture content of the fines, the more entrapment and the higher the loss of valuable metals in the magnetic dirt fraction,” he says.
_fmt.png)
Making it work
When Garden Street purchased its FineSort, the company’s goal was to recover 1-inch-minus ASR. However, the line failed to capture some of the finer nonferrous metals. So, Weber purchased another ESC to follow the FineSort. The strategy was to set the FineSort up to produce a dirty
Weber says he is recovering an additional 400 pounds of
When Weber sold the
“We get a mix of aluminum,
Garden Street’s
The misses from the FineSort, which contain that fine bare copper wire, and the misses from the second ECS with the intentional losses of the 1/4-inch-minus aluminum are presented to an ultra-high-frequency ECS to recover the
This process is netting more than 300 pounds of
Recovery targets
In addition to ASR, among the other applications that generate recoverable metallic fines are electronics recycling, ash from municipal solid waste incineration and wire chopping, Haegelsteen says.
Wherever the operation, certain areas almost always will profit from a once-over on the fines system. Be aware, however, that such special situations require a bit of rethinking in terms of handling the product, sources say.
“Every processor, regardless of capacity, should at least have basic recovery on the fines ASR,” Shattuck states. “ROI (return on investment) is typically short with the high volumes of nonferrous metal available in the minus-1-inch ASR stream,” he says.
A small shredder producing 50 tons per hour typically will produce 10 tons to 12 tons of ASR per hour. This equates to 5 or 6 tons per hour of fines that can contain better than 20 percent nonferrous metals.
Fine
Sizing materials
Most processors earn a small premium for
“I’d do it again for sure,” Weber says of his fines recovery project.
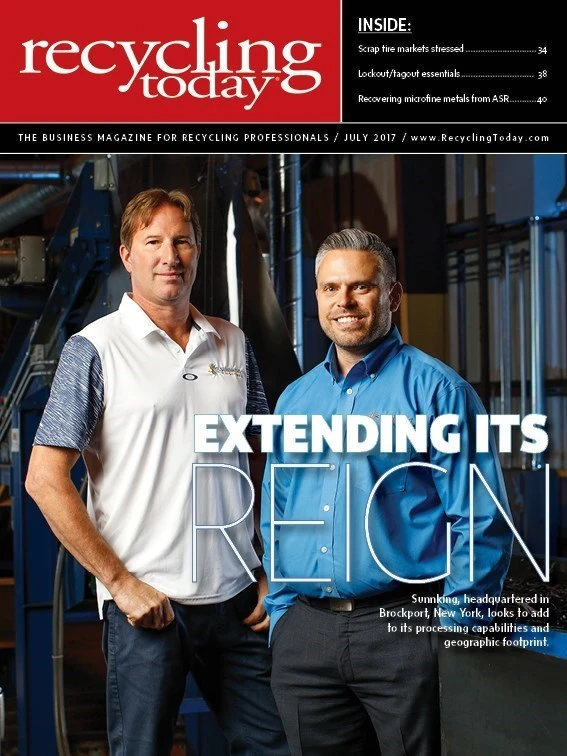
Explore the July 2017 Issue
Check out more from this issue and find your next story to read.
Latest from Recycling Today
- LumiCup offers single-use plastic alternative
- European project yields recycled-content ABS
- ICM to host colocated events in Shanghai
- Astera runs into NIMBY concerns in Colorado
- ReMA opposes European efforts seeking export restrictions for recyclables
- Fresh Perspective: Raj Bagaria
- Saica announces plans for second US site
- Update: Novelis produces first aluminum coil made fully from recycled end-of-life automotive scrap