BC Disposal could be called a good corporate citizen of its home state of Massachusetts. In response to the state’s promulgated desire to reach an 88 percent recycling goal, the long-time hauler opened its first recycling center in 2002, a high-tech, sophisticated mixed C&D recycling center at its headquarters in New Bedford.
|
"In 2000, Massachusetts came out with a solid waste master plan developed in part to stop importing and exporting waste," according to Michael A. Camara, vice president and general manager of the family-owned ABC. "Included in that plan were waste bans from landfills, including one for C&D in 2003. Before that ban went into effect, we wanted to be ahead of the curve and take control of the situation before it started."
What Camara means is that despite the fact that ABC has been in the hauling business since 1967, the company had no landfill or recycling facility. The company, which handles residential, commercial and industrial waste as well as C&D, would have been at the pricing mercy of both landfills and recycling centers. "And if we were at the mercy of everybody we dump at, then we could not control our costs," says Camara. "With this C&D recycling operation we can control it somewhat, and if managed properly, we can keep the prices down for our customers." It’s a matter of customer service, he adds.
RENEWED EFFORT
Even though the facility, opened under the name of New Bedford Waste Services, is ABC’s first recycling plant, Camara says it is an extension of the company’s long-time recycling efforts.
For example, Camara remembers finding some boxes in the trash as a youth while working with his late father, Arnold B. Camara, on one of the company’s first trucks. They saved them and later sold the boxes to another company that used them to ship out their final product. "He was getting paid to take it out and paid when he sold it later," says Camara, who is also president of New Bedford Waste Services. "That’s what recycling is all about."
End markets are what make recycling happen. Currently, New Bedford Waste Services recycles 95 percent of its C&D by pulling out metals, aggregates, old corrugated containers (OCC) and wood. It also makes a small amount of an ADC (alternative daily landfill cover) product to help reach that high recycling rate. "Our goal is to make as little ADC as possible," says Camara. "As we are able to find more markets for the other materials, we will make less ADC. We make more money on the other products."
Both ferrous and nonferrous metals are no problem to pass on profitably. Additionally, the company has long had outlets for secondary aggregate because of its roll-off business. OCC is not a problem, as a processor of that material is 100 yards down the road from the recycling plant.
Yet like so many New England C&D recyclers, recycled wood remains a challenging market, even though the company is able to send its processed wood to energy facilities. The Massachusetts Department of Environmental Protection (DEP) does not even consider use of C&D wood for biomass to be recycling, preferring to call it diversion. Yet hog fuel is one of the few outlets available.
Some of that is because of state requirements. DEP does not allow the use of C&D wood into mulch, animal bedding and wood fiber products. However, Camara is hopeful the state will change this situation in the future. "We want to work with the state in any way possible to use clean wood product."
With most C&D recyclers throughout the country finding their state environmental agencies to be a thorn in their sides, why is he so optimistic about the DEP? Simply because the agency has been willing to listen to the recyclers’ viewpoint, Camara says.
"As a recycling entrepreneur, you can’t do it alone. No one in this industry can. You need to have a DEP or a state that is willing to work with you to reach the goals that you set and they set," says the second-generation hauler. "I spent a lot of time on various committees they had set up to figure out ways to properly implement the C&D ban. It provided us an opportunity to talk with them about the issues we face as processors; issues they needed to learn. We were able to educate them on changes that need to be made in order for recycling to be successful. I applaud them for taking the effort to do that."
UP AND RUNNING
It took a lot of time, money and effort to get the New Bedford Waste Services plant up and running. The entire operation is on only five acres of land in an industrial area of the city. Virtually all of that is paved, and half of it is under roof.
A storm water control system is online for handling water within the parking lot, and water from the building covering the recycling plant goes to the wastewater treatment plant, but only after passing through an oil separation system.
The entire $7.5 million operation is different from many C&D recycling centers because part of it is a municipal solid waste (MSW) transfer station.
Camara assures that there is no problem keeping the C&D and MSW separate. "One of the nice things about running a plant like this is that a lot of the MSW we bring in is dry commercial waste. After we dump that on the floor, we are able to identify recyclables in it. We take those recyclables, push them into the recycling area and recycle them," he says. "So we are minimizing the waste that leaves this facility, both on the C&D and the MSW side." Currently the site can only accept 500 tons per day, but New Bedford expects regulatory clearance to go to 1,500 soon.
The recycling plant building is a big one—"We put the biggest one we could on this site," says Camara. "If we had a large piece of land where we could put this facility in the middle of it and not affect any of our neighbors, we could have put it outside. But we don’t, and this is a better environment for our employees. It also keeps the material dry and easier to handle and process through the grinding equipment."
At 47,000 square feet, the building not only covers the recycling process, but all the stockpiles, as well as the tipping area for both C&D and MSW. The drivers can even de-tarp and tarp their loads under roof.
It’s no accident the plant is set up that way. It is part of the customer service New Bedford Waste Services offers.
Most customers will conclude it is better to tip under the roof on a concrete floor than at a muddy, windy top of a landfill, Camara says, adding that at the landfill they will usually have a long wait in line to tip.
Not so at the recycling plant. Five scales—two incoming, three outbound— are in place. "Even though it is a small site, it is amazing how many trucks we can move in and out of here," says Camara. The drivers all have a magnetic card that they swipe through a reader when they approach the scale. They get a printout from the printer at each scale. Hence, the driver does not have to leave the truck to get a slip signed, saving a lot of time. And with five scales, there rarely is any waiting, Camara says.
The many outbound scales also means the company will not rush and inadvertently send outany light or overweight trucks.
Material is coming into the plant from as far as 50 miles away, with only 35 percent of the material coming from ABC’s 50 trucks. The majority is from other haulers, a testament to the competitive tipping fee and the convenience of the facility, because a landfill is 15 minutes away and a waste-to-energy plant only 20 minutes.
For C&D processing, after being tipped on the concrete floor the material is inspected for hazardous materials, which are removed, according to Jeff Leech, New Bedford Waste Service’s operations manager. As much metal as possible is grabbed as well, he says.
Then a Caterpillar wheeled excavator feeds an Annihilator pre-grinder supplied by Continental Biomass Industries (CBI). Says Camara, "We decided to pre-grind because we did not want to put a dozer in the building for safety reasons, health reasons, and because we did not want to tear up our concrete floor." Two pickers on the line leading to the pre-grinder are looking for any surprises, such as paints, propane bottles and the like.
|
The material is then passed on to a 6-inch taper screen from Action Equipment. This vibratory screen separates the 6-to-9-inch products from the rest of the flow. "It goes into two separate lines from there," says Leech, "overs and fines. The fines side goes through a second shaker screen to separate out the 2-inch-minus."
Two big magnets are also positioned over the lines to catch any metals before the two lines go through the picking stations.
There are eight picking stations on each line, four on each side. Clean wood, trash, aggregates and metals are pulled.
After the picking lines the material is on a reversible transfer belt. Ordinarily it goes into a Flo-Cait float tank "unless we are running wood for fuel, then it goes into the high-speed grinder," says Leech. The grinder, like the picking lines and belts, is supplied by CBI.
In Leech’s office is a bank of television screens that are connected to most of the 17 cameras around the recycling plant. One key monitor, though, is not in Leech’s office but instead at the station of the pre-grinder operator.
Leech considers this monitor a life saver. "If a big piece of metal gets by those first two pickers and into the system, then the operator can see it and reverse the machine," says Leech. "Then you just open the anvil door, drop it out on the line, and call up to the picking station to be on the lookout for the big steel."
Personnel at the plant are a combination of permanent and temporary employees. Camara likes the opportunity to audition employees that using a temp agency allows, even though there is a fee to hire them later.
Camara says he literally traveled around the world, looking at other recycling operations to figure out what works. But he is the first to admit that despite the sophistication of the plant and all the hard work that went into developing and running it, the operation is far from perfect. "We are tweaking it all the time," he says. "We are not the experts. I don’t care who you are, there is always something you can learn. We are willing to learn something new every day."
That’s because he knows the importance of this recycling facility to the entire company’s future. "Sometimes you wonder, it was such a big investment, big challenge, a lot of sleepless nights. But we looked at the needs of our hauling company in the future. With this facility we can ensure our customers good service."
The author is associate publisher of C&D Recycler and executive director of the Construction Materials Recycling Association. He can be reached at turley@cdrecycling.org.
Get curated news on YOUR industry.
Enter your email to receive our newsletters.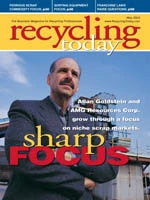
Explore the May 2003 Issue
Check out more from this issue and find your next story to read.
Latest from Recycling Today
- ReMA opposes European efforts seeking export restrictions for recyclables
- Fresh Perspective: Raj Bagaria
- Saica announces plans for second US site
- Update: Novelis produces first aluminum coil made fully from recycled end-of-life automotive scrap
- Aimplas doubles online course offerings
- Radius to be acquired by Toyota subsidiary
- Algoma EAF to start in April
- Erema sees strong demand for high-volume PET systems