Attachments are the key to successful demolition and recycling operations. Using the right tool for a particular job can increase an operation’s efficiency and profitability.
"The key to profitable demolition or recycling jobs, to maximizing profit, is using the right tools," Mark Ramun says. Ramun works out of Youngstown, Ohio, and represents Auckland, New Zealand-based A-Ward Attachments. "If they have the right equipment, they can do the job faster and more profitably."

"It’s the attachments that do all the work," Kevin Bakke, chairman of Genesis Equipment, Superior, Wis., says. "Not having the right attachment ruins your end product.
"It’s all about speed, in my opinion," he continues. "Quickly taking mixed material and adding value to it. Having the right tools is critical."
Scott Guimond, president of National Attachments, Gorham, Maine, also credits optimal efficiency to using the right work tool for a particular job. "Efficiency is money," he says.
By equipping their operators with the right arsenal of attachments, demolition contractors and C&D recyclers can ensure higher production rates, less wear on size-reduction equipment and improved profitability.
THE BIG GUNS
Bakke says demolition contractors increasingly are turning to high-reach material handlers equipped with a variety of attachments to handle demolition projects. He refers to it as the "Swiss army knife" approach.
Guimond (whose company markets Dutch-made EuroRam products) says, "The Europeans are a generation ahead of us in regard to using attachments, simply because they’ve had to be," citing the space restrictions found in Europe’s older cities.
He adds that demolition contractors and recyclers in the U.S. are beginning to favor the European approach, realizing that efficiency is a must in order to successfully compete in the marketplace.
While most demolition jobs require a variety of work tools, hydraulically powered, multi-tasking attachments, such as multi-processors or universal processors, are popular with demolition contractors. When mounted on high-reach excavators, these tools can provide the contractor with power, versatility and affordability.
"It is a tool that can precisely nibble or crush concrete and precisely shear steel," Guimond says of the multi-processor. "It’s the backbone of the industry."
John Knott, hydraulic products specialist with Atlas Copco Construction Tools, West Springfield, Mass., calls such tools "soft" demolition tools. "We have seen more requests for crushers and pulverizers because of recycling; soft demolition also has an advantage because it lessens vibration force."
"Multi-processors are tools that offer a chassis that has the versatility of accepting different jaws or jaw sets," says Guimond. "One jaw may be for cutting steel. Another jaw set would be for crushing concrete and cutting rebar. With that one tool, you have the ability to cut smaller gauge steel or process concrete. You have one tool that performs a couple of specific functions, as opposed to buying two different tools," Guimond says.
Bakke also notes the growing popularity of multi-processors in high-reach demolition applications.
"One of the reasons Genesis is popular with demolition contractors is that we make an attachment that can crush concrete and cut steel," Bakke says, referring to the company’s DemoPro. According to Genesis literature, the DemoPro’s jaw and blade configuration allows it to process concrete and rebar and structural steel without having to change the jaw or blade.
Uwe Kausch, attachment product manager for Stanley/LaBounty, Two Harbors, Minn., agrees that in high-reach applications, universal processors provide advantages in light of their wide jaw openings and hydraulic rotation. The independent movement of the jaws enables the operator to process material even if it is not ideally positioned in the jaws, he says.
Tramac Corp. of Parsippany, N.J., also produces a multi-tasking attachment known as the DA Demolition Processor. "Tramac’s DA Demolition Processors are shorter and lighter in weight," Michele Carline, Tramac marketing manager, says. "Smaller carriers can mount the DA Demolition Processor as a third member mount resulting in a better balanced machine. The trend in building demolition from the top down makes the weight of the attachment an important consideration."
Ramun, however, notes that demolition jobs are getting smaller in scale, with larger industrial demolition jobs growing fewer and far between. Therefore, the strength and rotation provided by the multi-processors are not as necessary. He finds that contractors’ interests are returning to mechanically powered tools, as they represent a smaller initial investment and do not require modification of the carrier.
"Our system allows the contractor to have very specialized equipment without a dedicated machine," Ramun says. In two to three minutes, a contractor can swap attachments on an excavator with the A-Ward system, he notes.
Ramun stresses that every tool has its place, however. While a universal processor may not always be the right tool for a particular job, a mechanical tool will not provide the rotation that some jobs require, he notes.
However versatile a single tool may be, demolition contractors often require a few more attachments to successfully complete a job.
"I would say the standard arsenal of attachments would be a bucket/thumb combination on an excavator, an extreme-service demolition grapple for an excavator, a hydraulic breaker, an appropriately-sized hydraulic shear and either a mechanical or hydraulic concrete pulverizer," Guimond says. With this combination of attachments, a demolition contractor would be ready to face virtually any demolition project. "He could take an existing facility and remove it like it was never there and have everything prepped for recycling," he says.
Kausch says demolition contractors require a bucket, hydraulic breaker, concrete pulverizer, universal processor, mobile shear and grapple. This combination of attachments will enable a demolition contractor to handle nearly any task that confronts him, from shearing structural steel to pulverizing concrete to basic material handling tasks. Kausch adds that if the demolition contractor encounters wood in a building, the grapple is capable of pulling out the wood and downsizing it in addition to the tool’s standard applications.
THE CUSTOMIZED WEAPONRY
Material Handling. Carline says Tramac’s MP Grapple will demolish concrete as well as being able to sort and load.
"In many cases, a grapple might be the only tool needed," Ramun says of demolition jobs, though he cautions that some grapples might not be heavy enough to tackle concrete in a demolition situation.
Guimond says, "The grapple is the backbone or fundamental tool of material handling." Grapples range from a simple contractor’s grapple for light-duty or general-purpose applications, he says, to those designed for more intense and demanding applications. "If you have a more intense application, we offer a box-tine grapple that has an intricate interior to each tine utilizing bridging and gusseting for strength."
The dexterity of a grapple, which is often compared to a human hand, offers demolition contractors and recyclers precise control and high efficiency in material handling applications, whether sorting through piles of mixed C&D debris or loading large pieces of concrete into a crusher.
Bakke says, for example, that a grapple can be used to feed larger chunks of concrete into a crusher, while a bucket and front-end loader may be used to feed chunks less than 2-feet in diameter.
While buckets used to log considerable time in C&D recycling operations, the entrance of quick-coupling attachments is changing that.
"With pin-grabbing quick-couplers becoming more popular, other attachments are logging more time. Now, it’s quick to take off the bucket and put on a hydraulic impact hammer," Al Springer, national sales manager for Allied Construction Products LLC, Cleveland, says.
Larry Carlisle of Anvil Attachments, Houston, says buckets are more appropriate for uniform, free-flowing materials, such as mulch, while grapples are better suited to materials of varying shapes and sizes because of their dexterity.
Terry McKague, an Ontario-based regional manager for Breaker Technology Inc. (BTI), Solon, Ohio, says he sees a 50/50 split among C&D recycling yards that use excavators equipped with grapples and wheel loaders equipped with buckets for basic material handling responsibilities, such as loading a concrete crusher, or moving mixed C&D material.
While grapples and buckets are somewhat interchangeable, innovations such as quick couplers enable recyclers and demolition contractors to have the best of both worlds.
Guimond says that quick couplers enable demolition contractors and recyclers to shift between grapples and buckets, depending on the task at hand. "They have the best of both worlds available to them by pressing a button inside the cab of the machine they are using as a base carrier."
With grapples, Guimond says, "You can be very precise with your movements. You can manipulate large volumes of concrete very quickly. You can dispense them into the crusher with precision. You can be fast and precise."
Kausch suggests that the grapple is best suited for loading mixed C&D debris because of its capacity and ability to separate the various materials. Grapples are also suitable for loading wood into a tub grinder because of their ability to pick and place, he says, adding that specialized grapples with narrower tines can be used for moving mulch. In light of size variability and the presence of fines, he suggests that a bucket is the better tool for loading a concrete crusher.
Buckets can also be used to pry paved surfaces away from the surrounding area, Ramun says. McKague also finds that buckets are a popular tool for this task, because the teeth slide under the surface and help to pry it away from its surroundings.
Guimond says that specially designed buckets, known as "slab-grabs," are ideal for removing paved surfaces.
Bill Papineau, engineering manager of NPK Construction Equipment, Solon, Ohio, suggests that once the pavement has been detached, a grapple is a good tool to use to remove it. "Assuming you can get the jaws on both sides [of the pavement] to grasp it, you’d be able to articulate it so it’s not in danger of falling," he says.
Rather than lifting a paved surface, some contractors might decide to break it in place. This is where a breaker or hammer might come into play.
Concrete Demolition and Size Reduction
"Hydraulic hammers can be used to break up concrete slabs into manageable pieces for crushers," Carline says. "Pulverizers and crushers are used to separate and clean rebar from concrete. By using a pulverizer, concrete can be processed to a smaller size and may not require additional processing in a crusher."
To break up slabs of concrete, Kausch recommends a hydraulic breaker, which is designed to work on a horizontal surface. However, he says, breaking up a vertical concrete structure, like a wall or bridge, requires a universal processor, which is also able to handle the rebar within the concrete.
"The hydraulic breaker is probably still the best means of breaking concrete slabs," Ryan Murphy of Indeco North America, Stratford, Ct., says. "Breaker (or hammer) technology has come a long way as well over the past 10 years or so. Fully hydraulically operated systems reduce the routine maintenance required to operate a breaker, and shock mounted breakers drastically reduce wear and tear on the machine carrying the breaker."
Papineau suggests that a hydraulic hammer is more appropriate for large concrete structures, while a concrete crusher is more appropriate for smaller jobs. A secondary concrete crusher can also be used to load concrete directly into the hopper of a crusher, Papineau says, because it offers control and precision in comparison to a bucket.
Universal Impact Technologies, Cumming, Ga., manufactures a line of impact breakers that is used in secondary processing to downsize concrete and remove rebar.
Frank Smith of Universal Impact says the majority of the company’s impact breakers are sold to demolition companies that want to further break down and densify concrete for transporting off site.
Equipment makers, including Atlas Copco, are now offering dust suppression systems with attachments that are commonly used with concrete. "Our latest hammers have a provision to hook a water line up so that operators can have a water jet spray for dust control," says the company’s John Knott.
Ramun recommends a cracker jaw for demolition contractors faced with the task of breaking large slabs of concrete. "A cracker jaw has a small surface area, which puts more cutting power on a smaller edge," he notes, adding that it also has a blade to separate concrete from rebar.
Ramun suggests that pulverizers, in adition to being a processing tool, can act as a grapple to set material aside.
Says Guimond, "If you are working with concrete, the best tool is a concrete pulverizer that is available in either a hydraulic or a mechanical version. In recycling, high-volume production is desirable. A mechanical concrete pulverizer is typically three times faster than a hydraulic pulverizer. In recycling, the mechanical concrete pulverizer rules." He continues, "When you need precise nibbling, that is when the hydraulic pulverizer is used. That is more in demolition than in recycling."
"With regard to concrete and aggregate material, generally the product of choice is the hydraulic pulverizer," McKague says. "It’s powerful enough to crush the concrete and separate the steel. It is not limited to the size of the concrete. Some mechanical pulverizers, when the concrete is too thick, can slow production down. A hydraulic pulverizer is not limited to the size of material it can process."
Regardless of the particular tasks facing demolition contractors or recyclers, the breadth of specialized attachments available from numerous manufacturers ensures that they will be able to find a tool specially tailored for their needs.
ARMING FOR EFFICIENCY
Work tools either enhance or detract from the efficiency of an operation, Guimond says, and that affects bottom-line profits.
"What people are realizing is that efficiency is a must if you are going to compete in the marketplace," he says.
"The larger contractors use a variety of attachments," Ramun says. However, he has noticed that smaller contractors or those new to the industry may try to use one attachment to tackle multiple tasks.
While buying a variety of work toos can add up, many contractors and recyclers may decide that the tools pay for themselves in the long run by increasing the efficiency of their operations and the quality of their end products.
The author is assistant editor of C&D Recycler and can be contacted via e-mail at dtoto@cdrecycler.com.
Get curated news on YOUR industry.
Enter your email to receive our newsletters.
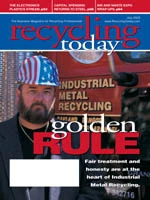
Explore the July 2003 Issue
Check out more from this issue and find your next story to read.
Latest from Recycling Today
- ReMA opposes European efforts seeking export restrictions for recyclables
- Fresh Perspective: Raj Bagaria
- Saica announces plans for second US site
- Update: Novelis produces first aluminum coil made fully from recycled end-of-life automotive scrap
- Aimplas doubles online course offerings
- Radius to be acquired by Toyota subsidiary
- Algoma EAF to start in April
- Erema sees strong demand for high-volume PET systems