
Recyclers of plastic film face special challenges. In layman’s terms, film is “flimsy.” More specifically, it has low bulk density—meaning a given volume of it weighs less than the same volume of other materials. That means recyclers need different feeding, cutting and transport strategies for this material. Fortunately, companies offer technologies to make recycling film possible.
CUSTOMIZED SOLUTIONS
One industry expert says that all film scrap has become valuable in today’s manufacturing environment. Technology now exists to handle scrap that previously may have seemed uneconomical.
For instance, complex coextruded structures that, in the past, would have gone to landfill can be cost-effectively densified for use in the waste-to-energy market, says Sandy Guthrie, president of ADG Solutions, Fairfield, Connecticut. “Postconsumer and other film that typically was thought to be too dirty for reuse now can be washed and extruded at an economically viable price. We now integrate all these technologies and engineer a system that meets almost any requirements.”
Citing a lack of special in-house recycling expertise among film processors, Guthrie says ADG Solutions is now offering complete reclaim systems, using multiple technologies to meet specific operational requirements. “During the economic crisis, many companies downsized or eliminated their in-house engineering staff,” he says. “Today, younger engineers don’t have the experience or knowledge to put together a reclaim system, and the veterans are often fully committed to more complex projects. That’s where we come in.”
ADG Solutions now can customize a complete system, including size reduction, densification, pelletizing and melt-filtration equipment, along with the conveyors and feeders to integrate the whole system. Where other suppliers might not want the headaches and liability potential involved in designing, installing and guaranteeing a turnkey system, “we’re happy to take it on,” he says of ADG Solutions.

Guthrie says his company recently broadened its melt-processing offerings to include densification and extrusion/pelletizing.
Ram-stuffer extruders have super-sized feed throats to maximize infeed of low-bulk-density film and fluff for consistently high outputs of filtered and pelletized extruded plastic. The extruders also can accept regrind as well as chunks or pellets. In operation, a pneumatic ram is used to stuff material into a specially designed grooved feed area, where a deep-channel barrier reclaim screw conveys the materials forward. The ram stuffer ensures there is very little effect on the feed or plastication rate of the extruder regardless of the scrap bulk density.
On the other hand, if the film scrap is wet, dirty or contains a mix of polymers, paper or other contaminants, a densifier can be the simplest and most cost-effective way to produce a high-density particulate that can be re-extruded or size reduced quickly. The densifier operates continuously and automatically. After preliminary shredding, scrap material goes into a holding bin with two metering screws that feed material to an inclined vibrating table that guides the scrap into the open feed throat of the densifier. There, short, counter-rotating twin screws compact the material. Pressure and shear forces raise its temperature to between 380 degrees and 390 degrees Fahrenheit and force it through a die to produce extrudate that can be further reduced in size for reprocessing. The densifier’s rugged design and construction allow it to tolerate tramp metal or aggregates up to 4 millimeters in diameter. It also handles up to 20 percent moisture with minimal effect on rate.
A SINGLE STEP
Next Generation Recyclingmaschinen GmbH (NGR), Feldkirchen, Austria, has been building plastics recycling machines for more than 20 years. It does business in the United States as Next Generation Recycling Machines Inc., Norcross, Georgia.
As film recycling evolves, the company has found innovative ways to apply its technology.
“During the economic crisis, many companies downsized or eliminated their in-house engineering staff. Today, younger engineers don’t have the experience or knowledge to put together a reclaim system, and the veterans are often fully committed to more complex projects. That’s where we come in.” – Sandy Guthrie, ADG Solutions
With its patented chopper-feeder-extruder combination, the E:Gran series can chop plastic film and film edge trim directly into the extruder feed section. The conically shaped conveying area of the screw compresses the material as it enters the extruder as part of NGR’s One-Step technology.
NGR sold the first of this machine to the North American market in 2003.
One more recent installation involved a blown film producer purchasing six E:Gran machines so that it could do in-line recycling. NGR officials say this is a trend.
“If they run five different materials on six lines, they have an in-line process where scrap never touches the floor,” says NGR CEO Wolfgang Steinwender. “Because companies are running many different films at the same time, these decentralized in-line reclaim systems quickly pay off.”
The machine was built for energy efficiency. In the extruder, the material is brought to a uniform melt temperature and subsequently pelletized. The feed section (where the material is chopped), conveying area and the extruder all lie along a single shaft. The resulting design requires only one energy-efficient drive. All components are positioned closely together to prevent the material from oxidizing and to make optimal use of the heat from the chopping process, NGR says.
The machine also is being applied to recycling projects that involve multilayer film and printed film. To address the unique technological needs of printed film, NGR provides a venting system for its machines used in such applications.

NGR uses a water-ring vacuum system on the extruder to accommodate volatiles that evaporate when the ink on the printed film reaches a certain temperature, Steinwender says.
“If you extrude printed film, the ink will give off gases,” he says. “The gases will end up in the pellets.”
To address that problem, a venting system is required.
“This is, on the one hand, interesting for printed films and also for materials that have hygroscopic characteristics, such as polyamide,” Steinwender says. “The vacuum system removes the moisture from the material, which leads to homogenous pellets.”
SPECIAL CHALLENGES
Weima America, Fort Mill, South Carolina, says it engineers equipment for each specific application. Madison Burt, Weima’s vice president of sales, echoes the sentiments of ADG Systems’ Guthrie, saying, “There appears to be a trend toward processing more contaminated film due to its low commodity value.”
To meet some of these special challenges, Weima has developed a plastics shredder, the WLK15, specifically for reprocessing film. To handle even the toughest tasks, it boasts wear-resistant features and a shock-tolerant drive assembly, Burt says. Material is loaded into the hopper and pressed against the rotor by the hydraulic ram. The rotor shreds the material until it can fall through the desired screen size.
According to Burt, the WLK15’s rotor, known as an F-rotor—for film, fiber and filaments—makes the machine ideal for film recyclers. “The F-rotor is designed with a close gap between the rotor and bed knives, even when the rotor knife has passed through the cutting zone. This helps prevent wrapping and self-feeding.”
The WLK15 is highly customizable, and buyers can choose among an array of options, including different versions of the ram, hopper and hydraulics.
“There appears to be a trend toward processing more contaminated film due to its low commodity value.” – Madison Burt, Weima America
Additionally, a cooling package is available for 24-hour operations, and a heating package is available for cold weather startup.
While Weima has seen the most demand from manufacturers dealing with internal scrap, Burt says demand from other sources is growing. “More companies are sourcing film to produce new products with reclaimed LDPE (low-density polyethylene) film pellets as a main base,” he says.
Though low resin prices have dulled some manufacturers’ interest in recycling, Burt says demand for ways to reclaim low-quality film is growing. Weima continues its innovation efforts in anticipation of a recycling upswing.
“The draw to processing this kind of film is the abundance of it on the market at a low price,” Burt says.
Get curated news on YOUR industry.
Enter your email to receive our newsletters.
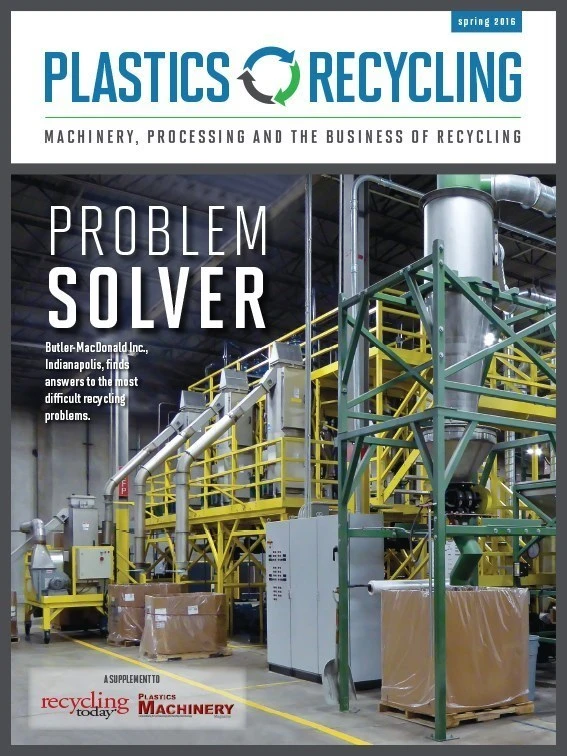
Explore the April 2016 Plastics Recycling Magazine Issue
Check out more from this issue and find your next story to read.
Latest from Recycling Today
- Astera runs into NIMBY concerns in Colorado
- ReMA opposes European efforts seeking export restrictions for recyclables
- Fresh Perspective: Raj Bagaria
- Saica announces plans for second US site
- Update: Novelis produces first aluminum coil made fully from recycled end-of-life automotive scrap
- Aimplas doubles online course offerings
- Radius to be acquired by Toyota subsidiary
- Algoma EAF to start in April