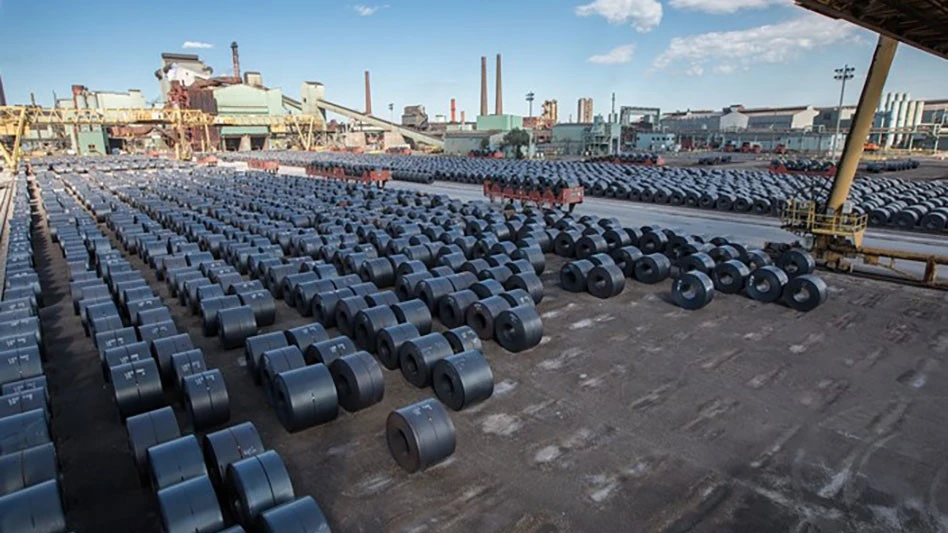
Photo courtesy of ArcelorMittal
ArcelorMittal, a Luxembourg-based steelmaker, invited representatives from the governments of Canada and Ontario as it broke ground on its CAD$1.8 billion ($1.31 billion) investment to transition to direct reduced iron- (DRI-) electric arc furnace (EAF) steelmaking at the ArcelorMittal Dofasco plant in Hamilton, Ontario. That plant has long used blast furnace-basic oxygen furnace (BOF) technology.
The project, which first was announced in July 2021, has received backing from the governments of Ontario and Canada, in part for its anticipated decarbonization outcomes.
In its descriptions of the project, ArcelorMittal has not mentioned consistently the use of scrap metal as feedstock. That differs from the BOF-to-EAF transition being undertaken elsewhere in Ontario by Algoma Steel Corp. That company not only has mentioned scrap consistently, but has forged an alliance with Ontario-based scrap yard operator Triple M Metals.
ArcelorMittal says a new 2.5 million-metric-ton capacity DRI furnace to be installed will initially operate on natural gas and will be constructed “hydrogen ready” so it can use hydrogen as an input if “a sufficient, cost-effective supply of green hydrogen becomes available.”
“By investing in ArcelorMittal Dofasco’s project to produce clean steel, we’re investing in the future of this plant and this industry," Canadian Prime Minister Justin Trudeau said at the October ceremony in Hamilton. "Together, we’re delivering real results: good, middle-class jobs, a strong economy and clean air for today and generations to come.”
ArcelorMittal Board Chair Lakshmi Mittal said, “Today is a historic moment for our company. This is the first full-scale decarbonization project we have broken ground on since announcing our commitment to achieve net zero by 2050 and reduce carbon emissions intensity by 25 percent by 2030. This day is possible thanks to the power of partnership and in particular the confidence and support the governments of Canada and Ontario have shown in us.”
Technology to be deployed in Hamilton includes an Energiron DRI plant jointly developed by Italy-based companies Tenova S.p.A. and Danieli & C. S.p.A. The system is being designed to produce 2.5 million metric tons of DRI per year to be used in Hamilton’s EAFs and is described by ArcelorMittal as “the largest single-module direct reduction plant in Canada.”
On-site work in Hamilton is scheduled to begin in January of next year, starting with the demolition of a decommissioned coke plant to make room for the new DRI plant. Demolition is anticipated to take up to nine months.
Engineering work also will be undertaken next year before foundation work begins in 2024. “Construction on the new assets will be complete in 2026, at which point a 12 to 18-month transition phase will begin with both steelmaking streams (BF-BOF and DRI-EAF) active,” ArcelorMittal says, adding, “The transition will be complete by 2028.”
In addition to the new DRI facility, the project also involves building an EAF “capable of producing 2.4 million metric tons of high-quality steel through ArcelorMittal Dofasco’s existing casting, rolling and finishing facilities,” the company says.
Modifications to ArcelorMittal Dofasco’s existing facility and continuous casters will be undertaken “to align productivity, quality and energy capabilities between all assets in the new footprint,” the company adds.
Referring to its “detailed roadmap to support its target of reducing the carbon intensity of the steel it produces,” the company points to EAF conversion or installation projects announced in Belgium, France and Spain.
Latest from Recycling Today
- Nippon Steel acknowledges delay in US Steel acquisition attempt
- BASF collaborates to study mechanical plastic recycling
- Commentary: navigating shipping regulations for end-of-life and damaged batteries
- Haber raises $44M to expand to North America
- Canada Plastics Pact releases 2023-24 Impact Report
- Reconomy brands receive platinum ratings from EcoVadis
- Sortera Technologies ‘owning and operating’ aluminum sorting solutions
- IDTechEx sees electric-powered construction equipment growth