_fmt.png)
Polypropylene has historically been difficult to recover, but it’s one of the biggest revenue opportunities for material recovery facilities (MRFs) today. The market and pricing for recycled polypropylene is growing fast, driven by consumer demand, producer commitments and government policy. Yet most MRFs aren’t capitalizing on this opportunity or preparing for a future where more accurate material identification and sortation can drive revenue instead of tipping fees.
How2Recycle recently upgraded polypropylene to “widely recycled” in the U.S.—a milestone that reflects the tremendous impact of $6.7 million in grants awarded by The Recycling Partnership’s Polypropylene Recycling Coalition to improve polypropylene recovery and further develop end markets. AMP Robotics’ AI-guided robotics systems offer MRFs the precision and flexibility to incorporate polypropylene recovery into their operations, without interruption to existing lines.
Cedar Avenue Recycling and Transfer Station (CARTS), a Caglia Environmental company, is one of the MRFs that’s begun realizing the opportunity in polypropylene recovery. CARTS, started by the Caglia family in 2004, represents the latest generation of MRFs. It handles all of Fresno’s trash and half its recycling, plus a portion of recycling for Madera County. CARTS recycles more than 70 percent of trash, organics and recyclables it collects, repurposing it into raw material feedstock for new products and packaging.
Last year, the Caglia family decided it was time to modernize CARTS, and the initial improvements more than doubled its processing capacity. The success of the first wave of technology upgrades made Mike Ledieff, division manager for CARTS, eager to explore other ways to improve efficiency and keep the MRF on the cutting edge. That’s when he learned about and pursued the grant opportunity available through The Recycling Partnership, and CARTS was ultimately awarded funding.
Ledieff chose to partner with AMP Robotics after several facility visits and working with the team. The grant provided funding for one robotic system, but CARTS decided to purchase two additional units from AMP to increase recovery and landfill diversion after seeing what they could do. Along with the grant-funded robot sorting polypropylene, the MRF also has a tandem robot on its last-chance line picking high-density polyethylene (HDPE) natural, HDPE color, polyethylene terephthalate (PET) and film. CARTS installed another robot on the aluminum can line for quality control.
Robots can be superior to humans in quality controlling polypropylene to produce a cleaner, more valuable bale given how many form factors the material comes in. It’s a challenging task for a human and can be a full-time job, which is problematic given the tight labor market. AMP’s neural network recognizes 50 billion objects on an annual basis—a number that continues to exponentially increase as its install base of nearly 300 robots expands. AMP’s vision technology counts more than 4.5 million discrete polypropylene materials daily. Plus, the AI platform is constantly learning and improving its ability to recognize and sort different objects made of polypropylene, along with a wide variety of other recyclables.
AMP’s systems often deliver purity upwards of 98 percent. Plus, robots can target multiple material types simultaneously. Their flexibility and precision have been selling points for grant awardees and others targeting a plastic with a strengthening end market like polypropylene. Ledieff calls the polypropylene-focused robot “the best success story” and encourages other MRFs to learn more about the polypropylene market and funding opportunities.

1-888-402-1686
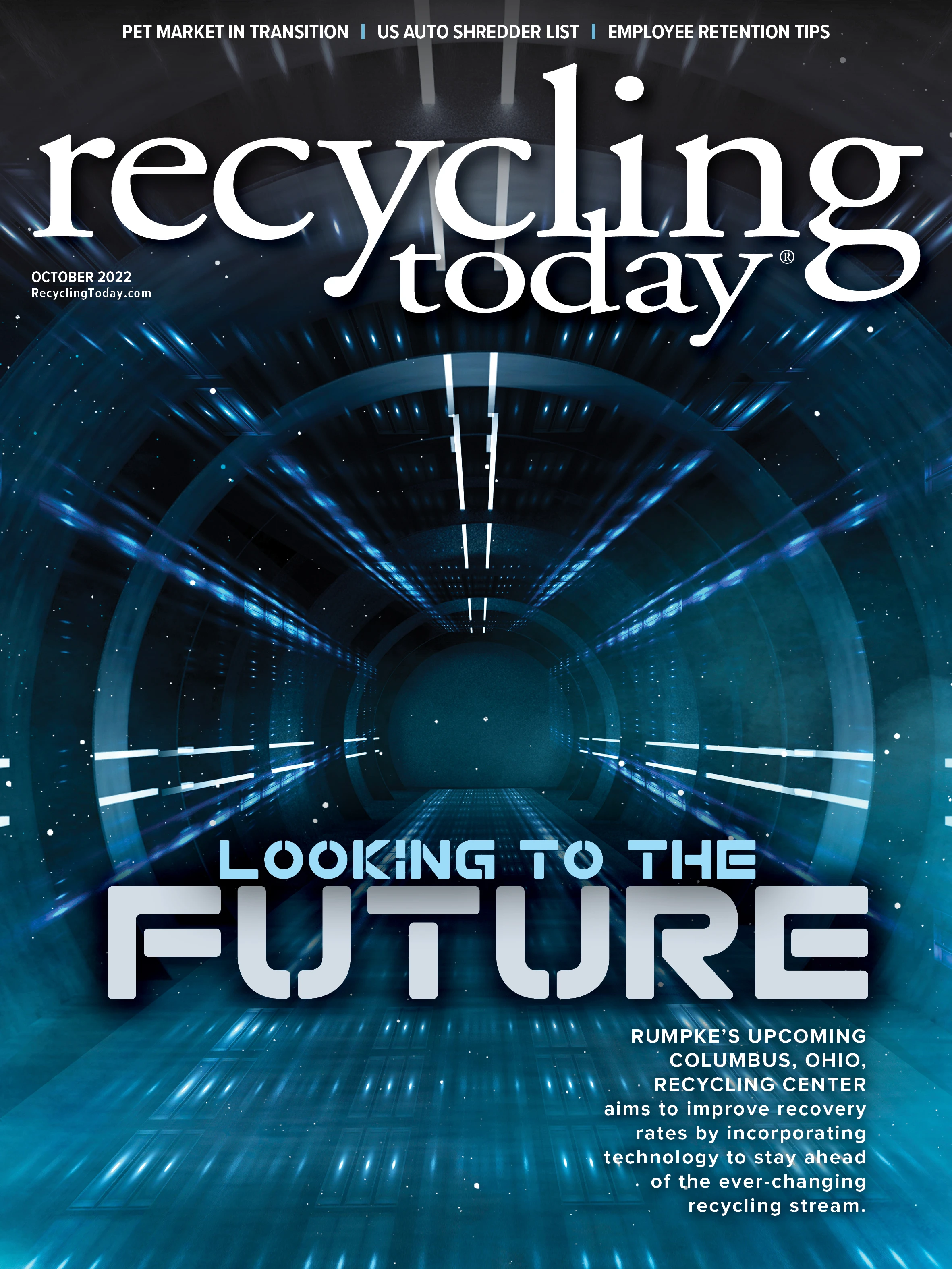
Explore the October 2022 Issue
Check out more from this issue and find your next story to read.
Latest from Recycling Today
- APR, RecyClass release partnership progress report
- Clearpoint Recycling, Enviroo sign PET supply contract
- Invista expanding ISCC Plus certification program
- Redwood partnership targets recycling of medium-format batteries
- Enfinite forms Hazardous & Specialty Waste Management Council
- Combined DRS, EPR legislation introduced in Rhode Island
- Eureka Recycling starts up newly upgraded MRF
- Reconomy Close the Gap campaign highlights need for circularity