The market today is flooded with choices for the consumer—which can be confusing and make choosing a product to buy a difficult decision. When shopping for a spectrometer, the buyer must look at how the unit will be used in order to choose a machine that will fulfill the needs of the company. Once the uses of the machine are determined, an educated and informed choice can be made when purchasing a spectrometer.
Whether to buy a hand held or laboratory model is often the first decision the buyer must make. But, the buyer must choose a unit that best fits the needs and uses of the company. “Most of the people in our industry buying metal are very confused about what is out there,” says Randy Moffat, vice president of sales and marketing for Angstrom, Belleville, Mich. “There are a lot of things coming out that are supposedly great, but it could be because they use buzz words and are deemed by the customer to be better.”
THE BASICS
There are two basic types of spectrometers available—the optical emission (OE) and the X-ray fluorescence (XRF) spectrometer. OE spectrometers make an arc or spark to the sample and create light that is emitted back. This reflected light is directed onto a series of photomultiplier tubes that pick up an individual wavelength produced by the spark given off the sample. That individual wavelength is then analyzed and interpreted. A potential draw back of this method is that in order to analyze ten different elements, ten detectors are needed, making it a process that is not always the most efficient.
XRF spectrometers bombard the metal sample with X-rays and then analyze the rays given back. They are known for very accurate results and are good at identifying high level alloying elements, such as chromium and nickel, although they can have difficulties finding light elements such as carbon and silicon. Also, because the machines use X-rays, certain safety precautions must be taken to make sure they do not pose any danger.
AN ARRAY OF CHOICES
For some scrap operations, a portable unit is preferred, making it easy to quickly classify the materials by using a hand-held model to do a preliminary sort. The portability of these units makes them popular choices for many businesses.
Because of their compact size, hand-held spectrometers do not utilize vacuums in the analyzing process, which can tend to make the units provide slightly less accurate readings than other laboratory models available. The lower price tag on hand-held models can also make them a popular choice for operations that need materials separated but do not require a more detailed analysis.
“I think the general trend is going for smaller and smaller instruments,” says Paul Penny, president of Arun Technology Inc., Dearborn, Mich. “It’s a function of what do you need to do the job you are required to do. If all you need to do is segregate, then one of the small units will work quite well. If you need to segregate some other materials with lighter elements, you can’t do that with smaller units.”
When accuracy down to very small percentages is critical, laboratory models of spectrometers may be better suited for these applications. The laboratory, and less portable, models achieve a greater level of accuracy for identifying materials, but the user also sacrifices the portability, Moffat says.
“I’m finding that at least in recyclers, that the big yards that are dealing with high volume steel mills want to very accurately pin down what they have,” Moffat says. The laboratory models allow for this accuracy.
For facilities that sell materials to steel mini-mills, more accuracy in classification may be needed and a laboratory unit may be better suited for the business. Mini-mills often want very low levels of contaminants, making it essential that the processor identify materials very accurately.
On the horizon
Other options aside from the basic spectrometer that are coming into the industry include a spark emission spectrometer that uses a chip for a detector. The system, manufactured by BAIRD-Applied Research Laboratories, Franklin, Mass., has the ability to analyze an array of metals because of the charge injection device (CID). The CID is one detector instead of multiple detectors found in more conventional units. The one detector offers the user more flexibility because it provides the ability to analyze multiple materials, says Charley Belle, a sales engineer with BAIRD.
Modification of existing technology has created another choice for purchasers looking for analyzing equipment. A product in the making called a Bulk Scrap Analyzer (BSA) uses technology from the aggregate industry to analyze metals. Using neutron analysis, the unit analyzes scrap that runs on a conveying system through the machine. “The scrap runs through the machine on a conveyor, and as it passes through there are neutron sources and detectors across the top of the machines,” says Dan Pflaum, executive vice president of corporate development, Systems Alternatives Inc. (SAI), Maumee, Ohio. “As the material passes through, neutrons are emitted to the scrap and the scrap emits a gamma spectra and the detectors interpret those results.”
The company is currently working on methods to perfect separation methods downstream of the BSA so that materials analyzed as being undesirable can be diverted from the rest of the stream.
According to SAI president John Underwood, the BSA can analyze ferrous scrap at a rate of 200 tons per hour, depending on the grade. The device can detect the percentage of copper, chromium and other elements present in a stream of shredded scrap or in turnings or bushlings. In the future, it may have the potential to analyze a greater range of scrap grades when it is redesigned with a larger aperture, according to SAI.
The unit is currently being field tested to detect materials such as manganese and copper. “The steel industry has been buying scrap for decades on specifications from a physical standpoint,” Pflaum says. “In the old days descriptions gave some idea but when a wider spectrum of materials has been taken on, physical descriptions don’t mean much in terms of chemical composition.”
The benefit to this new product, Pflaum says, is that the materials can be sold to a specific chemical composition. “Steel mills and foundries can use the device for quality control when paying for materials that you need.”
An educated choice
Although there is a flood of new equipment on the market when it comes to spectrometry, some companies have chosen to wait until the particular piece of equipment that will meet all of their needs comes onto the market. Annaco Inc., Akron, Ohio, a scrap metal processor, has yet to find that perfect piece of equipment. Instead, when the company needs a piece of scrap analyzed, they send it to an outside facility.
Chad Donley, sales supervisor, says that the variety of materials that the facility handles make it hard to find one piece of equipment that can analyze all of them. Instead, the company has chosen to delay purchasing an analyzing unit because of the cost and because there is not a machine that meets their needs.
“If there is a piece we have a real question about we send it out,” he says. “We haven’t found anything yet that does all of the things that we want it to do. Anytime a new alloy comes out, then the (computer) program you have isn’t as effective. Why spend the money on equipment that you are not going to use that much?”
The broad range of materials Annaco handles for different markets makes it difficult to find one machine that can analyze all of the materials handled at Annaco, he says.
Where it’s headed
More concern for the quality of materials bought and sold has led the industry to be very conscious, both on the buying and selling end of the market. “It is a very fast moving field,” says Dr. Richard Burlingame, a Cleveland-based melting materials consultant, “because we must know very accurately what we are starting out to melt in order to give us the very sharply specified products we are after. Quality is always going up, with greater demands from the customer.”
As technology and accuracy have improved, the price for machines available has dropped at the same time, says Belle. A machine that may have cost $70,000 in 1965 could be in the $45,000 to $50,000 range today. The cost drop makes the units more affordable and more accessible to businesses that depend on accuracy and detail. “The industry demands to know what they are making, what they’re selling and what they’re buying,” Belle says.
Burlingame says the rate of change in the field of metals analyzing has been very rapid over the past 20 years and he expects it to continue at the current rate for some time. “ There is huge demand for all of the new ideas that can be brought along.”
Overall, spectrometers and other analyzing equipment are being used more and more by both processors and customers to ensure that the materials being sold are meeting customer specifications, and to make sure the customer is indeed receiving what they paid for. A higher focus on quality control overall has been seen in the industry. “Quality is always going up,” says Burlingame. “There is greater demand from the customer.”
Typically, when market prices are higher, more sorting will take place, but when the markets are low, some processors will complete the minimum number of processes needed to get the product out the door.
And as markets change in the scrap business, Penny says there is still room for growth in the field of metals analyzing equipment, but when that growth will be and what it will bring remains to be seen. RT
The author is the assistant editor of Recycling Today magazine
(Sidebar)
How It All Works
There are several other methods to analyze metals in addition to the popular spectrometry. Processors must evaluate their individual business needs and determine what kind of equipment and what kind of testing process will best suit their operations. Here are other methods by which composition of a metal can be determined.
Non-instrumental methods:
The spark test: The spark test is one of the simplest methods of metals analyzing, determining the composition of a sample by looking at the shape and color of sparks given off when the sample is ground against an abrasive wheel. Very useful for steels, this test must be conducted by a skilled operator who can interpret the results. The test does have limited uses with other alloys.
Chemical spot tests: A chemical spot test entails dropping a chemical or a series of chemicals onto the surface of an alloy. The color change that results from the reaction between the chemical and the sample can indicate the presence or absence of particular elements. This test does have limitations, although the costs involved with using the test are relatively low and it can produce good results under the right circumstances.
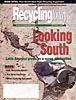
Explore the October 1999 Issue
Check out more from this issue and find your next story to read.
Latest from Recycling Today
- Indiana county awarded $65K recycling grant
- Mixed paper, OCC prices end year on downward trend
- Updated: CAA submits final draft program plan in Oregon
- Enviri names new president of Harsco Environmental business
- Survey outlines ‘monumental challenge’ of plastic packaging collection in UK
- Nippon Steel acknowledges delay in US Steel acquisition attempt
- BASF collaborates to study mechanical plastic recycling
- Commentary: navigating shipping regulations for end-of-life and damaged batteries