
Demand for many metals is increasing worldwide because of the housing and transportation needs of an ever-growing global population.
Adding to this burden is the drive toward renewable energy and decarbonization, with about 90 percent of the world having established net-zero carbon targets, including increased use of electric vehicles (EVs), which run on lithium-ion batteries and, therefore, require higher quantities of metals like cobalt, nickel, aluminum and copper. This makes reliable supply of these metals crucial for the ongoing transition to cleaner transport and energy generation.
Unfortunately, this spike in demand comes as mining operations around the world face growing challenges. Energy prices are high, supplies of high-grade ore are scarce and miners frequently are working with extremely low metal concentrations. For example, a metal loading of just 0.5 percent is now the norm within copper mining operations.
This schism between supply and demand is only expected to widen, with a predicted copper shortfall of 15 million tons by 2034 based on current mine output, according to a report that cites global mining, mineral processing and metals production firm Rio Tinto.
In addition to these challenges, the industry is emerging from a period of relatively low demand and commodity prices. This means in recent years there has been an underinvestment in mining capacity, putting limitations on the speed at which the industry can increase its output to meet near-future copper demand. These issues must be resolved quickly if the industry is going to thrive and satisfy demand well into the future.

Waste not, want not
One answer to this problem is to increase scrap metal recycling.
Effective scrap metal sorting depends on fast and accurate elemental analysis using robust sampling and analytical technology to enhance process efficiencies and increase plant throughput. For instance, nonferrous and stainless steel samples must be analyzed individually and sorted into the right bin before they can be processed or sold, requiring rapid analytical technologies to avoid bottlenecks. It also is critical to accurately determine alloy grade and chemical composition of any material and check it for contaminants and hazardous elements to prevent unwanted materials from entering the stream when selling to foundries or steel mills.
These factors also affect the economic viability of scrap recycling as higher-grade alloys with fewer tramp elements are worth substantially more than those containing a higher amount of impurities.
Several nondestructive techniques can be used for this analysis, one of which is X-ray fluorescence (XRF). This method offers several benefits when sorting, particularly in terms of accuracy when analyzing different types of materials including wires, turnings, powders and mesh, among others. Hand-held XRF analyzers allow recyclers to rapidly and accurately determine the composition and grade of incoming nonferrous and stainless steel scrap, making it possible to verify high-value elements in many types of metal alloys, from trace levels to commercially pure metals.
The technology also increasingly is being used in lithium-ion battery recycling to provide the fast and accurate elemental analysis facilities need when sorting incoming material and quantifying impurities in recovered metal. For instance, by measuring elements such as cobalt, nickel, manganese, phosphorous, iron, copper and aluminum, hand-held XRF analyzers help recycling facilities estimate the economic value of cathode foils and black mass, allowing operators to optimize their extraction processes for more efficient metal recovery. Hand-held XRF devices, therefore, support recyclers in meeting growing demand for metals in the EV industry, as well as covering the predicted shortfall of several key battery components.
The convenient, on-site testing capability afforded by hand-held XRF analyzers removes the need to send metal samples off-site for analysis or rely on traditional verification methods—namely spark or chemical tests—that require grinding and the storage and handling of hazardous materials.
These devices also are designed to be incredibly rugged and to withstand constant exposure to dirt, dust, adverse weather conditions and inevitable high usage at processing plants. These robust hand-held analyzers can play a large part in enhancing productivity at recycling centers, providing detailed and reliable results to cut down on analysis time and bring as much metal back into the economy as possible.
Hand-held XRF analyzers are a popular and proven technology in the world of scrap recycling and are considered to be one of the best-known methods for sorting scrap quickly and accurately.
How they work
Hand-held XRF analyzers produce X-rays directed at the surface of a sample. The X-ray energy removes electrons in the sample’s atoms, causing each element in the sample to produce a unique set of characteristic fluorescent X-rays. The detector then collects this X-ray “fingerprint” and converts it to electronic pulses, which are amplified and processed to produce a detailed compositional analysis and grade identification in seconds.
Hand-held XRF analyzers are a popular and proven technology in the world of scrap recycling and are considered to be one of the best-known methods for sorting scrap quickly and accurately. In particular, they can be very useful for distinguishing between different alloy grades that are nearly identical in composition, such as 303, 304, 321 and 347 stainless steels.
A potential downside of hand-held XRF analyzers is that they currently are unable to identify lighter elements—those below magnesium in the periodic table—as the energy of the emitted radiation is too low to be detected.
Incorporating a graphene window into hand-held XRF analyzers within the last few years has shortened the measurement time of light elements, such as magnesium, aluminum and silicon, by three- to fourfold. For example, hand-held XRF analyzers can detect magnesium content of 0.5 percent and lower within a few seconds, enabling recyclers to more efficiently and accurately sort aluminum.

A look at LIBS
A complementary nondestructive technology for quickly analyzing lighter scrap metals is laser-induced breakdown spectroscopy (LIBS).
Hand-held LIBS analyzers use a highly focused laser to ablate the surface of a material, forming a plasma of electronically excited atoms and ions on the surface. As the atoms decay back into their ground states, they emit characteristic wavelengths of light that act as an identifier for each element in the sample. The emitted light is transferred through fiber optics and enters the spectrometer, where it interacts with a diffraction grating, splitting the light into component wavelengths before it passes on to the detector. The resulting spectral data are again processed by the central processing unit, generating a detailed composition analysis for interpretation by the user.
LIBS technology has different advantages than XRF analysis, so it is worthwhile for operators to consider adding this technique to their recycling processes to complement existing XRF analysis. For instance, LIBS is an optical method that measures light in the visible and UV spectrums and can analyze a broader range of elements than a portable XRF analyzer, including lighter elements. This is particularly useful when it comes to measuring carbon, which has a direct impact on the welding properties, hardness and toughness of the end-product alloy.
LIBS analyzers also can make it easier to identify low-alloy and carbon steels (those containing only 300 parts per million carbon), and L and H grades of 304 and 316 stainless steel—some of the most common forms of this material. However, the technology is not as effective as XRF when it comes to sorting heavy metals like high-temperature alloys or copper alloys. Operators should keep these factors in mind when deciding whether to employ LIBS or XRF technologies, or a combination of both, for their specific applications.

Future-proofing supply
A net-zero carbon future largely will rely on the use of a range of metals.
Improving the efficiency of scrap recovery and lithium-ion battery recycling processes is vital to ensure these versatile materials will be available in decades to come. Existing issues with supply have already driven technological innovations to enhance metal recovery rates recently.
Analytical tools will play a major role in bringing as much metal back into circulation as possible in the years ahead, helping the scrap recycling industry keep pace with demand and supporting a more sustainable future.
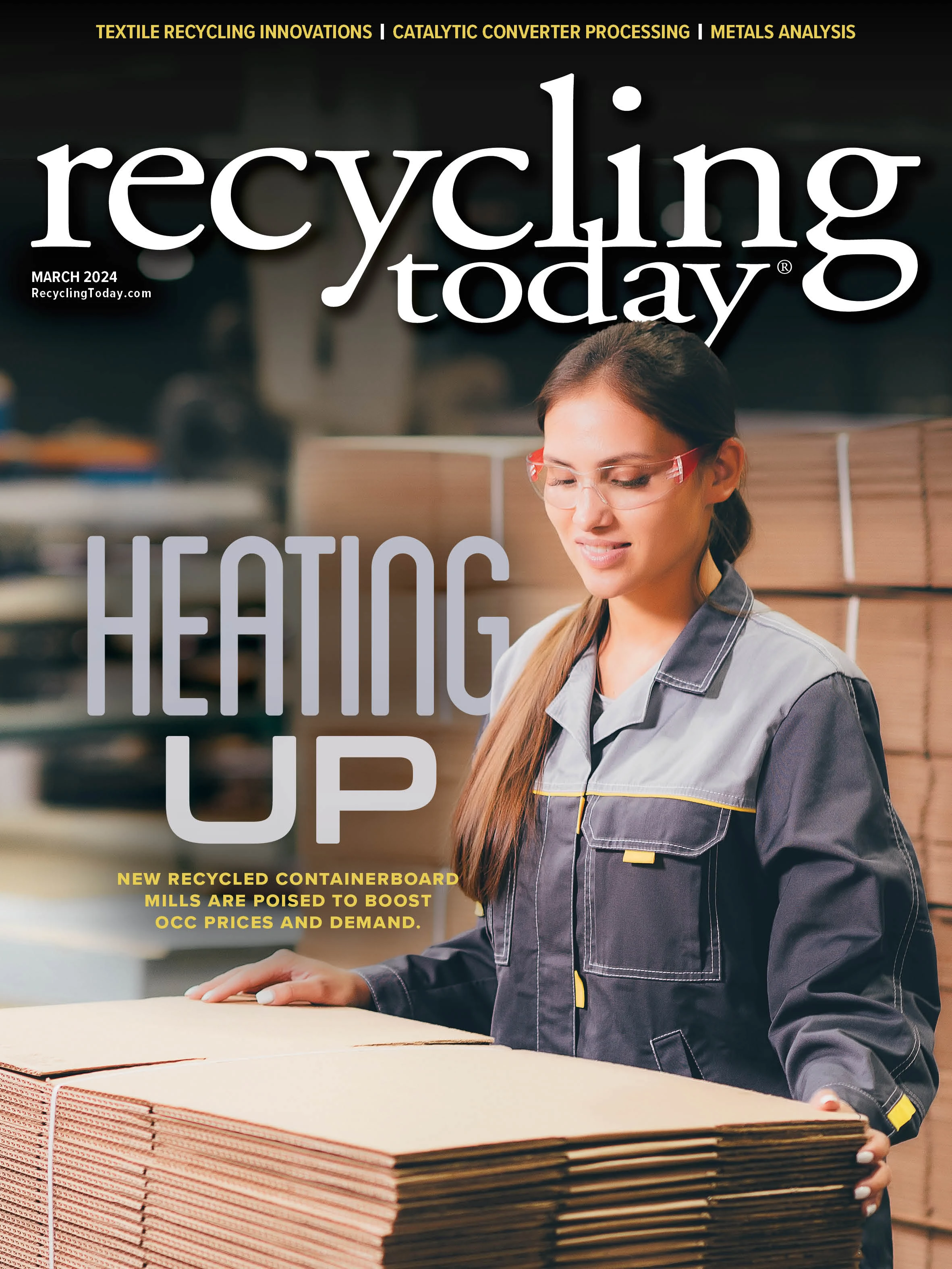
Explore the March 2024 Issue
Check out more from this issue and find your next story to read.
Latest from Recycling Today
- Athens Services terminates contract with San Marino, California
- Partners develop specialty response vehicles for LIB fires
- Sonoco cites OCC shortage for price hike in Europe
- British Steel mill’s future up in the air
- Tomra applies GAINnext AI technology to upgrade wrought aluminum scrap
- Redwood Materials partners with Isuzu Commercial Truck
- The push for more supply
- ReMA PSI Chapter adds 7 members