
©nikkytok | stock.adobe.com

Scrap yards and demolition contractors rely on mobile shears to aid in preparing scrap. These devices have helped to reduce the use of cutting torches as operators downsize and dismantle objects that are too large to be introduced into processing machinery otherwise, resulting in safety, productivity and labor-saving benefits.
But, as with all machinery, preventive maintenance is key to ensuring maximum productivity and safety.
In the following interview, Loren LaGesse, technical trainer with Genesis Attachments, Superior, Wisconsin, offers his advice for keeping mobile hydraulic shears performing their best.
Recycling Today (RT): What is the typical lifespan of a mobile shear?
Loren LaGesse (LL): The typical lifespan of a mobile shear can vary greatly depending on the application, environmental conditions, aptitude of the operator and care given to maintain [the equipment]. It isn’t uncommon to see mobile shears still in operation well past 20,000 hours and [that] remain in relatively good, serviceable condition. We’ve also seen shears that have been neglected and would be lucky to see 8,000 hours if operation and maintenance practices don’t change.
The expectation of the “acceptable lifespan” also can vary quite a bit. A mobile shear that runs 40-plus hours a week in a scrap yard might have a high expectation for multiple years of reliable service at near-peak performance, while a shear that was purchased for use on a single remote demolition project may not.
RT: What typically is the most overlooked aspect of maintaining shears?
LL: The most commonly overlooked aspect almost always is centered around the main hydraulic cylinder.
A mobile shear operates as a system, with blade maintenance, grease practices, hydraulic care and jaw buildup all playing an equally important role. Mobile shear service challenges often can be compounded because care is addressed reactively rather than proactively. Internal condition of the shear cylinder is no exception and is rarely at the forefront of shear maintenance conversations.
The heart of the shear is the cylinder, and it cycles back and forth, end to end, all day long. [Because of this], the internal piston seals and packing will eventually wear out. If it is not repacked often enough, the cylinder can come apart internally and do significant damage before there are obvious signs of failure. If [the shear] is not shut down in time, the debris created inside the cylinder can wreak havoc on the cylinder, its components or even the carrier powering the shear. Cylinder replacement alone can be quite expensive—needing to decontaminate the carrier will only make matters worse.
The second item on my list is cutting blade maintenance.
Cutting blades are expensive and are consumable components, so they are sometimes used beyond their intended service limit. It isn’t uncommon to see cutting blades being maintained only after shear performance starts to suffer.
Focusing on proactive care regarding blade fitment, blade edge condition, maintaining proper blade gaps or blade fastener torque procedures can seem tedious and counterproductive at first but will pay dividends later on the blade’s third and fourth edges. Proper blade care will also become evident in the shear’s total life cycle. Maintaining optimal cutting performance, maximizing efficiency, minimizing unexpected downtime and limiting stresses in the shear’s structural and hydraulic components are all benefits of proper blade care that improve longevity of the shear.
RT: What is the most common issue you see when servicing shears? How much of that could be avoided with preventive maintenance and, if so, what types?
LL: One of the most common issues we find when working on used, aged [or] high-hour shears is poor blade seat and blade pocket condition. Sometimes, it is simply the result of years of neglect, but too often it is an issue that has been exacerbated by blade maintenance personnel.
Blade seat and pocket surfaces are crucial for proper blade support and retention along with fasteners and proper torque procedures. They should be clean, flat and free of deformations or debris.
Using a grinder to hog away at material in the blade pockets should not be the first move. I always recommend using the least-intrusive method possible, meaning wiping the surface down with a rag and solvent or cleaning surfaces with a rotary tool equipped with a Scotch-Brite pad or Wheel Wizard brush, then using a wire brush or wire wheel. Use a good file to clean edges or remove burrs or small deformations. A grinder may be required to remove rolled parent jaw material, but unless you know exactly what you’re doing, use of a grinder would be a last resort.
Grinders can have a long-term effect on the “near-perfect” machined surfaces of pockets and blade seats. Cutting blades need to be properly supported, so if a grinder is used at every blade rotation interval, eventually the surfaces will be artificially eroded to where they will no longer provide the required support, resulting in breakage and poor blade retention.

RT: What types of material should operators avoid processing with a shear?
LL: Other than a few specialty application mobile shears, shears are specifically designed for use on mild steel, such as common pipe, plate or structural steel. They are not intended to be used on hardened or high-carbon materials. Stainless steel may fall into both categories, depending on the grade and alloy, but the rule of thumb is this: If it snaps, pops, cracks or flies when being cut, it doesn’t belong in the jaw of a shear.
Materials we occasionally see in shear processing but are not approved applications are items like axles, hardened gears, springs, railroad track or steel mill reject material that was discarded because of incorrect metallurgy or heat-treating that resulted in the product being too hard.
Mobile shear operators cannot be afraid to sort out the hard stuff. In some cases, the stuff to be sorted out can look exactly like the material that is perfectly OK to process—it may even have come into a scrap yard in the same truckload or from the same demolition project.
Broken blades, bent or broken structural components, premature fatigue and structural cracking are all common results of improper applications. The hydraulic system of the shear as well as of the excavator take abuse from cutting material that is too hard, and the sudden unloading of the hydraulic system as it instantly busts through the material can do damage to the internal seals, cartridges, valves and coolers of both the shear and the carrier. We call this phenomenon a “decompression spike,” and it can be severe.
Each scenario is unique, but processing hard materials can result in a warranty denial should the shear fail.
RT: What are some signs a shear could be malfunctioning?
LL: Low power, poor cutting performance, slow operation, contaminated hydraulic filters or even excessive heat are all signs of a malfunctioning mobile shear. Some are more obvious than others, but operators need to be able to think on their feet. Not all malfunctions will be shear-related, but they may manifest as something related to shear operation or performance.
Prior to troubleshooting, carrier function and output always need to be verified first. Shear performance will not be up to par if the carrier output pressure is down from normal, or perhaps an operator was messing with the carrier tool settings in the onboard computer. It isn’t uncommon to see a simple hydraulic hose replacement turn into a troubleshooting issue because someone closed a ball valve.
RT: How can operators ensure maximum efficiency with their shears?
LL: Ensuring maximum efficiency is a combination of multiple factors. First, the shear needs to be plumbed from the carrier properly. There is a right and a wrong way to set up a shear/excavator package when trying to realize the full potential of the combination.
Next, the shear needs to be properly maintained and all systems need to be operating at the intended specifications, including hydraulic pressure and flow, grease practices, rotation speed, blade gaps and blade radius wear and fastener torque values. Address small issues before they become uptime-killing problems.
The last part of the equation is training an operator to become proficient, not just when it comes to pulling levers, but [also] about caring for the carrier, greasing at proper intervals, making sure setup is done correctly, taking care of their work area, taking the time to look things over—those types of things.
When the operator takes pride in their work, the production will follow.
The goal is not to put as much processed material on the ground in any one-hour span but more of an average across a week, month or even a year. Don’t let today’s production numbers negatively impact tomorrow’s.
RT: Do you have tips for making owners’ manuals and the information they contain more accessible for operators or for relaying the information without having to read through a dense, technical manual?
LL: When it comes to familiarity with Genesis shears or work tools, I always recommend operators, maintenance technicians, managers and welders get to know the safety and operator’s (S&O) manual. The S&O manual is full of useful information and isn’t written in extremely technical terms, making it easy to read and understand. Without proper context, the information may seem a bit dry, but the concepts are certainly applicable at a daily level and will absolutely help to promote proper care practices. Even if it isn’t read cover to cover, it is beneficial to understand what subjects are addressed so it can be referenced when questions arise.
Genesis Attachments publishes our S&O manual as well as our parts manuals online, so if you have access to the internet, you will always have access to our literature. We actively encourage our customers to review this material, so we have never required logins, user portal or authorization to access it on our website. Our Marketing Communications Manager Amy Burmeister, along with our engineering group, does an excellent job making the material easy to find as well as making it easy to understand.
Regarding encouragement for employees to read through the information, this can pose a challenge and I think it mostly falls on the shoulders of the individual, unless it is required training reading. We make it available to everyone but, admittedly, not every person will seek it out.
RT: What are some easy first steps operators can implement to take control of their preventive maintenance?
LL: A great first step for any operator is to read through the safety and operator’s (S&O) manual. This will help them get a grasp on the different aspects of mobile shear care. Shear care can be significantly different than most other mechanical devices, so it needs to be understood before it can be implemented.
The next steps involve spending time around other operators, learning good habits while trying to improve on their bad ones. It’s easy to fall into a maintenance rut that can be difficult to dig out of later. “It’s good enough” is not a great philosophy when it comes to proactive shear care.
I don’t encourage chasing perfection, but a balance of care and time being well-spent can be an imperfect science.
RT: What’s the best way to assess when to repair and when to replace?
LL: Knowing when to replace a mobile shear component versus repairing is normally a simple cost-value equation. Without component replacement, you typically can weigh a few hundred or a few thousand dollars versus how long it would likely take to repair, then [factor] in labor and acceptable downtime for each option.
When it comes to complete mobile shear replacement, the cost figures increase exponentially, making the equation much more complex. ... I would compare it similarly to how you determine when it’s time to get a new vehicle. Is having a low-mileage pickup truck a big concern or is simply being reliable [a reason] to keep your old one? Is your current truck doing the job well, or is it too small or too big to be efficient in your daily routine? How far do you drive every day and is it your only vehicle? Even if you’re due or overdue for a new vehicle, does your budget allow it? The equation can be as complex or simple as you want to make it, but … needs to be figured out on a per-case basis.
An ounce of prevention is worth a pound of cure. The shear [is] a system that works in unison, with all the pieces working as one, [and] poor practices in any area will eventually affect the others.
Mobile shears are commonly a core component in many businesses, especially scrap yards, and should be treated as if you don’t want to go back to the old methods—torches.
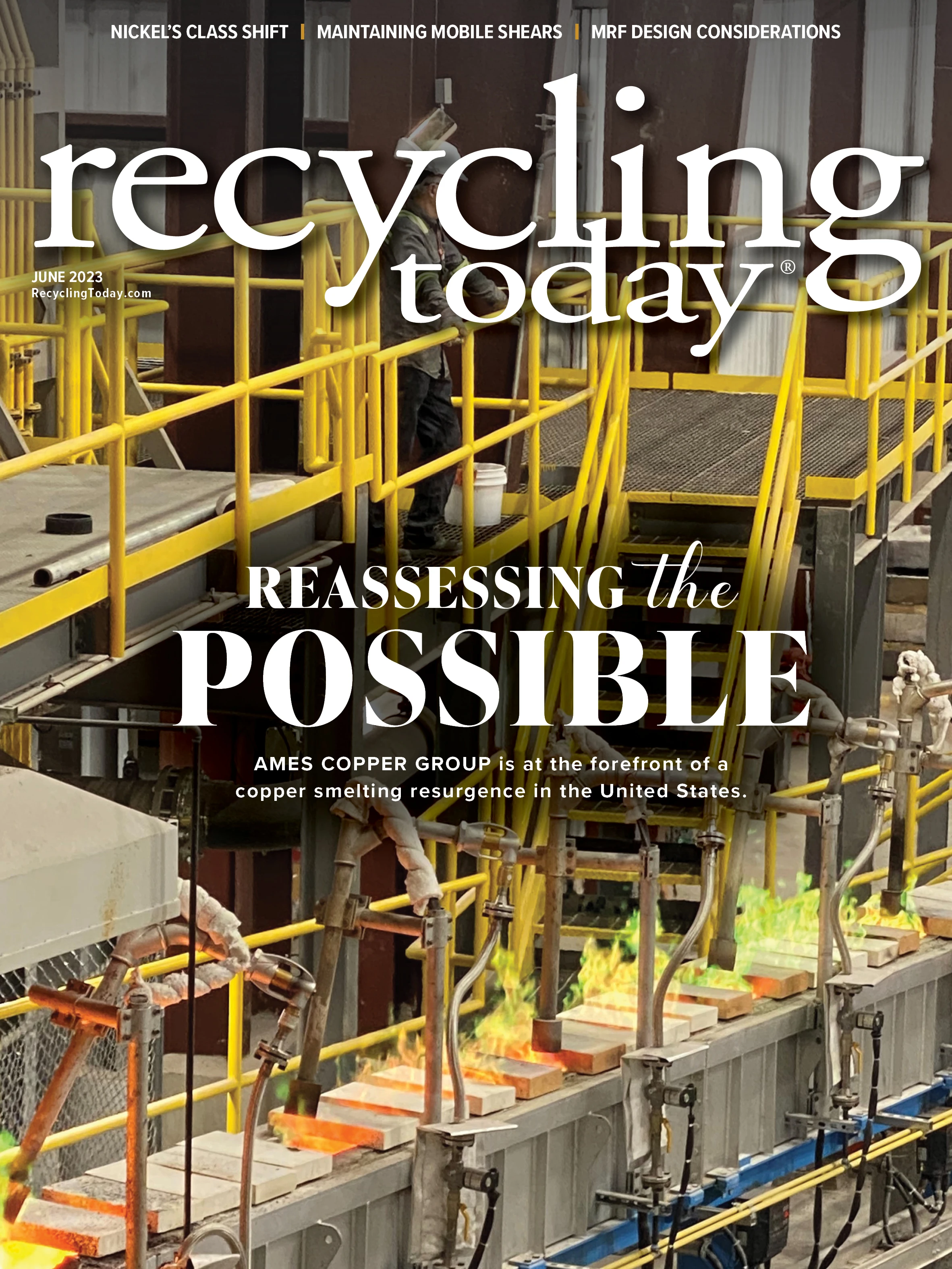
Explore the June 2023 Issue
Check out more from this issue and find your next story to read.
Latest from Recycling Today
- Athens Services terminates contract with San Marino, California
- Partners develop specialty response vehicles for LIB fires
- Sonoco cites OCC shortage for price hike in Europe
- British Steel mill’s future up in the air
- Tomra applies GAINnext AI technology to upgrade wrought aluminum scrap
- Redwood Materials partners with Isuzu Commercial Truck
- The push for more supply
- ReMA PSI Chapter adds 7 members