
For some material recovery facilities (MRFs) in the United States, recovering glass for recycling adds to their bottom lines. These glass recyclers cite the profitability that is associated with large volumes of incoming material and multiple, steady end markets in their regions as an advantage of processing the material.
Some MRF operators recognize the need to approach glass in the same way they approach other incoming materials. As with paper, old corrugated containers (OCC), plastics and metals, these recyclers view glass as another product they are producing rather than as a byproduct.
They also agree that processing mixed broken glass is technically challenging, capital intensive and volume driven. Recyclers are aware of the material’s low value, how harsh it is on equipment and the lack of end markets for cullet in some regions. (Read the sidebar “Creating a Coalition” to learn how some misperceptions related to glass are being managed and about work related to creating specifications for recovered glass.)
Cal Tigchelaar, president of MRF operator Resource Management Cos. (RMC), Chicago Ridge, Illinois, says glass should be looked at not in isolation but rather as a large component of the overall single-stream mix. He considers RMC’s production of high-quality cullet as a core part of the company’s business that serves as a “profit center.”
RMC also operates a glass beneficiation plant at its Chicago Ridge location.
Tigchelaar will serve as one of two speakers, along with Kate Davenport of Eureka Recycling, Minneapolis, at the 2016 Paper & Plastics Recycling Conference session “Making the Most of Glass,” Oct. 19, from 2:45-3:45 p.m. in Chicago at the Marriott Downtown Chicago Magnificent Mile.
Clean up contamination
While glass generally has nominal value, Tigchelaar says, it is infinitely recyclable and saves a significant amount of energy when used as a secondary feedstock. It should not be viewed as a waste residue to be disposed of as cheaply as possible, he adds.
“Recyclers need to look at their mixed glass not as a waste byproduct of their MRF operation but as one of a core group of materials that needs to be approached as a product,” Tigchelaar says.

The best place to clean up mixed broken glass is at the MRF, he says, not at the glass processing facility. MRF operations that produce mixed broken glass that is relatively clean can expect to receive a better economic return, in general, than MRFs that use only sizing screens to separate glass from other materials.
“It makes little sense to transport large amounts of waste residue along with the more valuable broken glass to a processor and then have the processor incorporate the negative value of the waste and its removal into the economics that he provides back to the MRF,” Tigchelaar explains.
If contamination is removed from glass “on the fly” as the material flows through the MRF, Tigchelaar says the process can be fairly simple. However, if contaminated recovered mixed glass is piled up outside of a MRF where it is exposed to the weather, the challenge becomes greater, he says.
“The most significant aspect of our approach to processing glass has been our ability to develop customized equipment, which can stand up to the harsh nature of the feedstock that is available to us, and the ongoing improvement of the quality of material—sorted and crushed—that our system is producing,” says Tigchelaar.
Test out techniques
To accomplish this, he points to the importance of good equipment and to efficient MRF system designs.
For RMC, the process hasn’t been straightforward. Tigchelaar says, “We have gone through a long, costly and sometimes painful process to determine what works and what does not work in terms of glass processing techniques.”
The U.S. lacks cullet processing capacity, and more needs to be developed, Tigchelaar says.

While some MRFs have invested in basic glass cleaning equipment, the equipment used to perform this task varies. Furthermore, most MRFs today use sizing screens to separate broken glass from other single-stream materials and make no effort beyond this to remove additional contamination, he comments. Removing shredded paper, steel bottle caps, plastic lids and other small pieces of contamination “is not rocket science,” Tigchelaar says.
“Depending on the configuration of a particular single-stream system, it is usually possible to install a simple blowing or vacuum system to remove the biggest part of the contamination,” he suggests.
In addition, as glass continues to break down as it makes its way through a MRF, multiple screening steps should be incorporated throughout the process.
At the MRF level, Tigchelaar says modestly priced systems are available to clean up glass.
Efficiently equipped
If adding equipment to an already-packed MRF isn’t practical, Tigchelaar recommends installing glass recycling equipment in a separate, well-insulated building. This helps with issues related to noise, storage and space.
However, it doesn’t necessarily make sense for most MRFs to go to the extent that RMC has at its Chicago Ridge facility. Here RMC operates a 30,000-square-foot glass beneficiation plant where glass particles from 3/8 inch to 1 ¾ inches in diameter are optically sorted by color and then sold to bottle makers. Cullet particles smaller than 3/8 inch in diameter, as well as the green fraction, are used as feedstock for its crushed cullet operation and sold to fiberglass production facilities. The company receives mixed broken glass from its Chicago Ridge MRF, conveying the material directly from the MRF into the adjacent glass processing facility, as well as from other RMC facilities and third parties.
RMC has refrained from purchasing entire systems for its beneficiation facility and instead buys “off the shelf” vertical shaft impact crushers and sizing screens to produce its mixed bottle cullet.
The company also uses customized equipment—conveyors, hoppers, super structure, cyclone vacuums and storage—designed, manufactured and installed by CMD Conveyor Inc., a Chicago Ridge-based manufacturer of recycling equipment that RMC has worked with for more than 25 years, Tigchelaar says. In addition, CMD manufactures the cleaning equipment RMC uses to remove contamination from mixed broken glass prior to crushing. Austria-based Binder and Co. makes the optical sorting equipment RMC uses.
As equipment manufacturers continue to develop and improve glass cleanup systems for MRFs, and as the relative value of “clean” versus “dirty” mixed glass continues to diverge, Tigchelaar says he anticipates that recycling plant operators who have invested in glass recycling will be better off in the end.
“The trend should favor increased availability of better feedstock for glass processors such as ourselves,” he says.
For MRF operators who cannot justify the capital cost of operating glass processing equipment in light of volume constraints, Tigchelaar says partnering to pool volume is a possible approach, allowing regional processors the opportunity to achieve the economies of scale necessary to drive a successful bottom line.
Going forward, Tigchelaar says he sees glass recycling as sustainable. “You will see more MRF operators invest in glass processing equipment and process mixed broken glass as an additional core part of what they do on a daily basis.”
Get curated news on YOUR industry.
Enter your email to receive our newsletters.
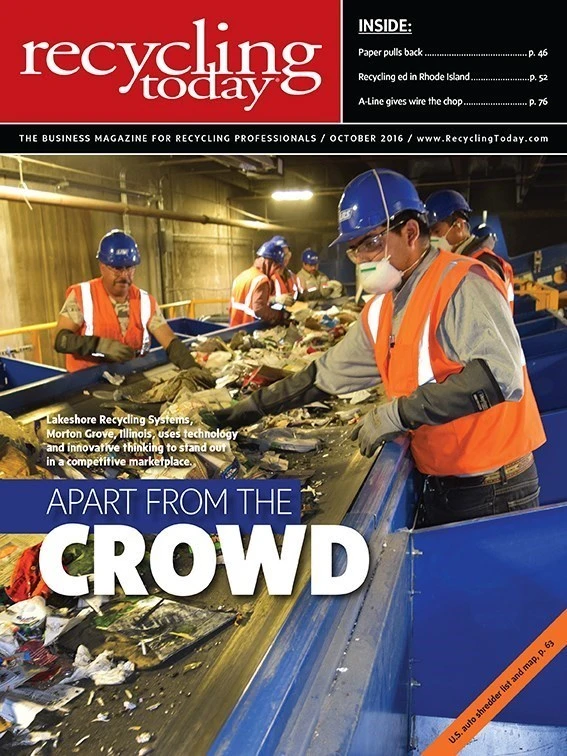
Explore the October 2016 Issue
Check out more from this issue and find your next story to read.
Latest from Recycling Today
- Hitachi forms new executive team for the Americas
- Southwire joins Vinyl Sustainability Council
- Panasonic, Sumitimo cooperate on battery materials recycling in Japan
- Open End Auto Tie Balers in stock, ready to ship
- Reconomy names new chief financial officer
- ICIS says rPET incentives remain weak
- New Jersey officials award $16.2M in annual recycling, waste reduction grants
- Linder Industrial Machinery announces leadership changes