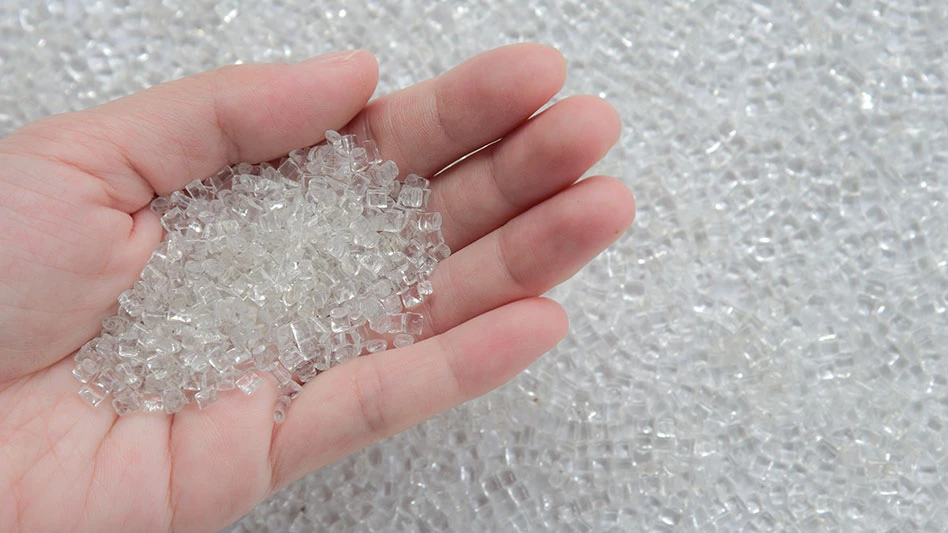
Recycle Man | stock.adobe.com
As we look to curb extraction of nonrenewable resources, the concept of circularity has become the predominant paradigm for the packaging industry and many other sectors. The general concept of circularity has been around for decades, first introduced by William McDonough in his 2002 book Cradle to Cradle: Remaking the Way We Make Things and recently popularized by the Ellen MacArthur Foundation (EMF).
The EMF defines the circular economy as “a system where materials never become waste and nature is regenerated. In a circular economy, products and materials are kept in circulation through processes like maintenance, reuse, refurbishment, remanufacture, recycling and composting.”
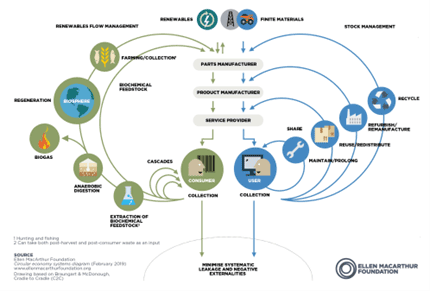
with subsequent materials used to build a new product.
It is important to recognize that a wide range of technologies and systems will be required to achieve this. As EMF rightly depicts, it will take embracing circles of varying sizes to ensure materials stay in use and never become waste. Only then can we reduce our reliance on nonrenewable and finite resources.
When we think about circularity, all loops will require innovation and new technologies to achieve the circular economy vision. The larger the loop, the further the product is broken down, with the subsequent materials then used to build a new product. Some of the technologies that will be required to achieve circularity, such as composting for organics and compostable packaging, will be truly transformative—breaking organic matter back into nutrient-rich soils that will be used to grow new feedstock for harvesting. That is perhaps the largest possible loop that materials can make in a circular economy and is widely accepted as an environmentally sound system.
When we think about closing the loop for plastics, however, it seems people often think of and get stuck on the idea of very small loops that are solely focused on taking a product back into the same product, such as bottle-to-bottle recycling. Today, this is achieved through mechanical recycling. Although mechanical recycling is extremely effective, it doesn’t come without its limitations. So, it begs the question how long can these little loops be maintained? Are these little loops the best from an environmental impact perspective? For example, a recycling process that takes a polyethylene terephthalate (PET) bottle to a thermoform or fiber application could have a lower environmental footprint than taking that PET back to a bottle. Using that PET in the fiber market could, in some cases, be considered a durable good, which means a longer service life than a bottle, further driving down the environmental impacts of that particular use cycle.
If we stay on the example of the PET water bottle becoming a fiber for a moment, perhaps that fiber-based product will make an even larger loop the next time through the cycle by being molecularly recycled back into a prime-like quality feedstock that would be suitable for any number of high-end uses, including food-contact uses, such as a bottle with virgin-like properties.
So, as we start thinking about the loop for plastics, we need to start challenging ourselves to consider the many loops that a material could take to truly succeed in achieving circularity. That also means embracing new innovations, including molecular (also known as chemical) recycling technologies, that will help keep creating and closing loops once the other, smaller loops are exhausted.
We also might need to think of some of these loops for truly transformative technologies as even being divergent. If we consider the largest possible loop in the circular economy model, which is composting, we are really looking at the circularity pathways used in the natural world. Nature takes materials through very big circles when we look at sustainable ecosystems. For example, a tree does not simply become another tree. Yes, a small subset of the tree’s cells become differentiated into seeds to propagate the growth of new trees, but the bulk of tree’s matter over its life cycle becomes food for other organisms that then break that matter down into nutrients. These nutrients become available to support other species of the ecosystem, including potentially supporting the growth of new trees. In this example, nature looks less like a circle and more like a fountain, with a diverse breakdown of products becoming part of a balanced and multifaceted system.
As we think about other transformative recycling systems for plastics, such as molecular recycling technologies, we need to consider the many different pathways a material could take. This includes considering the diverse range of products we can obtain from plastics that get looped back into manufacturing. The big loops, and potentially divergent loops, should be recognized as part of the multiple pathways a material could take on a circular journey.
Ben Scott is the director of research and innovation at Greenmanta Technologies, a molecular recycler based in Brantford, Ontario. Greenmantra has transformed millions of pounds of plastic materials into high-value polymers that extend the service life of key infrastructure materials, such as asphalt roads and roofing, yielding important greenhouse gas savings.
Latest from Recycling Today
- WM completes $40M automation project at Philadelphia MRF
- Speira commissions new furnace in Germany
- ABB report portrays paper sector circularity, emissions reduction
- RMDAS and Davis Index numbers portray stalled ferrous market
- Attero adds NGO veteran to its board
- AMCS launches the AMCS Platform Winter 2024
- Cirba Solutions celebrates construction milestone at Ohio plant
- Study outlines plan to transition US plastic packaging, textiles to circular systems by 2040