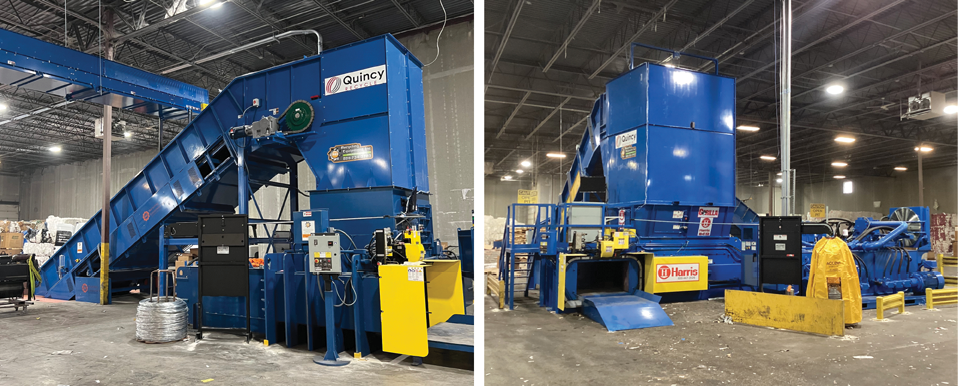
With more than 4,000 tons of material coming in per month and the potential for tonnage increases in the future, Quincy Recycle’s West Bend, Wisconsin facility needed not only to replace its long-tenured two-ram baler, but add a second one to help process a variety of commodities.
The recycling facility provides industrial waste solutions for manufacturers in Wisconsin, Minnesota and Illinois and primarily processes paper, plastic and food byproducts for manufacturers and others generating large volumes of those materials. According to General Manager Marshall Harting, 75-80 percent of the material coming in is fiber, such as old corrugated containers (OCC), sorted office paper and deinking grades.
With the growing need for versatility in baling, Quincy Recycle worked with a trusted equipment dealer in Newton, North Carolina-based Recycling Equipment Inc. (REI) to select a pair of two-ram balers that would operate efficiently while limiting downtime. Ultimately, the company chose a Harris Gorilla and an American Baler W721, both manufactured under the umbrella of Recycling & Waste Equipment (RWE).
Harting says the balers were purchased at the same time and installed in staggered fashion to limit downtime. The American W721 was installed in September 2023 followed by the Harris Gorilla in November of that year. They’ve proven their worth ever since, fitting seamlessly into the facility’s existing footprint while allowing for easy preventive maintenance.
“Our primary needs are fiber, OCC and office paper,” Harting says. “We do bale a variety of plastics and metal drums. We felt that based on the efficiency of the machines, along with the horsepower, they gave us plenty of strength while still meeting the speed demands of baling fiber on a daily basis. They give us both the power that we’re looking for and the efficiency in the commodities that we process. They really work well for our material mix in West Bend.”
After installing the balers, members of REI’s team worked with Quincy Recycle on-site to train staff, working through settings that would allow the facility to adjust bale sizes and easily switch programming based on the commodity. With the addition of a second baler, the facility can process OCC in one machine and run deinking grades, for example, in the other simultaneously, enabling the plant to process one-and-a-half times more material per shift than previously.
The Gorilla is used as the facility’s primary baler, helping the facility process 15-20 tons per hour.
“The two-ram model is fantastic,” Harting says. “A great thing about the two-ram is it just allows you to really work through a lot of different commodities. There’s probably nothing you’ll run into that you wouldn’t be able to use this baler for. And this particular model, the Gorilla, fit our specific needs as far as getting a second baler. In terms of ease of use, quality we’ve seen and how easy it is to maintain the equipment, it really creates efficiency for our maintenance team. We have very limited downtime with anything that occurs and it allows us to have confidence on a daily basis that we’re going to be able to process the materials we’re bringing in in a timely manner.
“The great thing about these pieces of equipment, too, is when we made those selections, we looked at where we are now and where we plan to be [in terms of tons]. This machine will meet our needs for years to come, even with adding more tons on a monthly basis.”
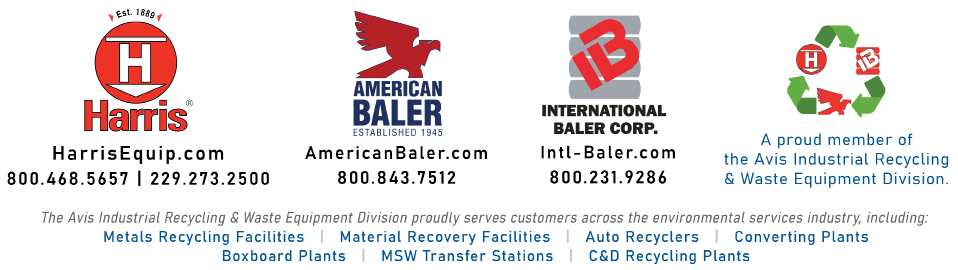

Explore the March 2025 Issue
Check out more from this issue and find your next story to read.