s aluminum producers and recyclers battle with sagging prices for their nonferrous metal, aluminum itself is waging wars on several fronts. In automobile manufacturing, the seesaw battle continues between aluminum and steel for major part assemblies, while plastic manufacturers continue to advance their material in new auto applications. In another area, aluminum cans are trying to squelch a takeover by plastic bottles as the favorite packaging medium for beverages. And in the construction market, architects are looking to include aluminum in a variety of new building designs. Combined, these three markets – cars, cans and construction – account for two-thirds of the aluminum consumption.
These three markets will continue to dominate aluminum consumption in the next millennium, with the biggest gains expected in the automotive sector. Other markets include electrical, consumer durables, machinery and equipment.
MORE ROOM FOR VROOM
With the impact of the recent General Motors strike, and slumping Asian economies putting the brakes on vehicle sales, both ferrous and nonferrous materials alike are feeling the pinch. Consider that vehicle sales in the Asian-Pacific region declined 7% in 1997, and are predicted to fall another 30% this year, according to The Economist. It may be three to four years before the Asian auto markets recover, and who knows what changes the recently ended GM strike will bring, as that company fights to be profitable after several disappointing quarters.
While these relatively short-term scenarios run their course, the longer-term outlook is that aluminum continues to make significant inroads as an automotive material. And producers are counting on further gains in the years ahead. The transportation sector consumed nearly 6.6 billion pounds of aluminum in 1997, according to statistics compiled by The Aluminum Association, Washington. That figure represents just more than 29 percent of the aluminum market.
And the association says that the automotive market will continue to be the biggest market for aluminum in the years ahead. In a statement released by the association, "aluminum will soon be seen as a basic structural material for autos," putting it on the same playing field with steel. To make its point, the association points out that in 1990 there were no aluminum structured cars on the market. Last year, however, there were seven, among them were the Audi A8, the Plymouth Prowler and the GM EV-1 electric vehicle.
Recent parts that have switched to aluminum have been rear crossmembers on the 1998 Dodge Intrepid and Chrysler Concorde. In 1999, Chrysler will also install aluminum rear crossmembers on its LHS and 300M models.
Mercedes-Benz’ new A-class compact car has an "intelligent lightweight design which makes specific use of the advantages of various lightweight materials," according to a company press release. Much of that lightweight material is aluminum, including the 11-piece front structure that was designed by Alcoa, Pittsburgh, and is robotically assembled at Alcoa’s plant in Soest, Germany.
The new Corvette is fitted with an aluminum windshield surround, and there are many more examples. In fact, aluminum driveshafts are increasing in popularity, as more rear-wheel-drive vehicles such as pickup trucks and sport utility vehicles are being fitted with them.
Car makers like aluminum because of its light-weight, non-corrosive characteristics and ability to absorb impacts from collisions.
Auto recyclers and dismantlers have been bracing for this new influx of aluminum for some time, as they have installed new sorting equipment and are keeping a watchful eye on identifying which parts are aluminum so they can be removed prior to the shredding process. This is important, as wrought aluminum and cast aluminum are of different grades, and sorting them is desirable.
Lloyd O’Carroll, an investment analyst with Scott and Stringfellow, Richmond, Va., says that aluminum in cars will definitely accelerate. "Aluminum is going into systems and assemblies that never before were considered candidates for the metal. New casting techniques are allowing the breakthrough, and new engine programs are now requiring aluminum."
As for the GM strike, O’Carroll says that by year end the volume in the market will be back to normal and no one will have known that there was a strike in the first place. He acknowledges GM’s lag in productivity efficiencies that may hurt the company down the road.
Nick Adams, a statistics analyst for The Aluminum Association, says that the auto industry remains the number one market for aluminum and that market will continue to lead the other markets. "Aluminum usage in autos jumped 13% from 1996 to 1997," he says.
In another sector of the transportation market, the airline industry is also helping to drive aluminum consumption, and will continue to do so as demand for new planes remains strong. This demand for new aircraft is increasing as more people take to the skies for their travel needs. Low fuel costs, low inflation and a competitive industry have kept airline ticket prices affordable for a majority of travelers in the U.S. and abroad. Thus, major airplane manufacturers such as Boeing have backlogs of orders for new plane deliveries. In addition, aging fleets need to be replaced, adding to the demand.
Alcoa, for example, says it had a 14% rise in aluminum shipments to aerospace and defense customers in 1997.
CANNING WILL HOLD
Aluminum beverage cans, a popular packaging medium in the United States, have virtually eliminated the tin beverage can altogether. That dominance, however, was not happenstance as many of the large aluminum producers in the U.S. made it a priority to develop new canning techniques that would rely on aluminum. The strategy worked. But while the carbonation of a beverage could help the thin-walled aluminum can keep its shape, such was not the case with other canned items. For years aluminum producers attempted to make inroads in the food canning business by trying to fill their cans with an inert gas during the canning process. But the scheme never panned out in high-speed canning operations, so aluminum was, and still is, captive only to the beverage market.
But while the aluminum can quickly rose to dominance, plastic bottles have significantly reduced the use of glass in the beverage market, and have gained market share from aluminum to the point where aluminum is virtually no-growth in the market today. Seeing the pending doom, and knowing all too well the fate of the tin can, the aluminum industry launched a new multi-million-dollar television ad campaign that is currently running. The ads tout the benefits of cans as containers and a mainstay of the recycling industry.
"The aluminum beverage can has an assured place in the market," says O’Carroll, who has spent 20 years in the aluminum industry. "Aluminum cans have several advantages over plastic. One, they are recycled back into new cans and because of their value, fetch a higher price to support recycling operations. Two, they ship better because they can be stacked. And, three, filling speeds are faster for cans than plastic bottles."
"Plastic has grabbed some share of the market away from cans, but only around the fringes," he says.
Overall, unit volume for cans was up about 2% last year. Soft drink canning was up about 3%, but beer canning was down, mainly due to the efforts to reduce alcohol consumption by the public.
Still, The Aluminum Association’s ads may not be enough to beat down the attack from plastic, so can producers are trying another approach. Now on the horizon are new can designs that offer promise to the lackluster aluminum canning industry that is currently looking at maybe a 1% growth rate per year during the next five years, according to analysts.
The new cans are being designed with embossed letters and designs that consumers can feel when they pick them up. Also, due to a new process, higher quality graphics can now be placed on aluminum cans, enhancing their marketability on the shelves.
Alcoa is the first company to introduce the new can design process, and Anheuser-Busch, St. Louis, is currently test marketing the cans in four U.S. markets.
Coca-Cola, Atlanta, is still reviewing a new can design that was introduced two years ago that adds the familiar wavy Coca-Cola bottle shape to the Coke can.
BUILDING A MARKET
Largely due to products in the residential, industrial, commercial, farm, and highway sectors, the 1994 building and construction market accounted for about 3 billion pounds of net shipments, or 15% of total shipments and the third largest market for aluminum.
While aluminum siding has virtually given way to vinyl siding for residential applications, the metal is still strong in window framing, covering applications and other uses in the commercial building sector.
Aluminum is also being considered for infrastructure applications, such as bridges and oil rigs. In many cases, the light weight, high-strength and durability of aluminum makes it attractive to construction contractors.
The benefits of aluminum in construction include less maintenance or painting than traditional materials. It can also be installed easily, thus saving time on the job. In addition, many concrete and steel-reinforced bridge decks face extensive rebuilding due to weather damage, and aluminum is currently being studied as an alternative material.
NEW APPLICATIONS
There is considerable ongoing research, both within the industry and at universities aimed at increasing the performance of existing aluminum products and developing new applications. The introduction of improved in-line process sensors, computer simulation models, and advanced process controls will enhance process efficiency, reduce energy consumption, minimize scrap generation and improve the recovery of metal from wastes, all of which will contribute to lower costs. In addition, "net shape" technologies (such as semi-solid forging, which is a more flexible material) will eliminate some of the fabrication steps, yielding further savings in energy and product cost.
Customers are demanding more sophisticated materials to meet demanding engineering specifications. One area is bridge construction, and aluminum is being tested in new designs as an alternative material that won’t rust, yet has enough strength to do the job.
Recently, The Aluminum Association’s Technical Advisory Committee identified several industry-wide performance targets that focus on increasing aluminum use in specific end-product markets. The committee also looked at ways to reduce the cost of aluminum through improved processing and production techniques so that the aluminum could be accepted more readily in key markets. These markets and products for which aluminum could play an expanded role include food cans, autos and light trucks, marine applications, transportation structures (such as lightweight bridges), desalinization equipment, housing, high-rises, scaffolding, lightweight construction tools, mass transit vehicles, aerospace, and military applications.
New design concepts, such as double-walled unconventional fuselages and innovative high performance ship, truck, and rail structures, need to be explored, the committee concluded.
As for geographical markets, Adams of The Aluminum Association says that most of the major aluminum companies like Alcoa and Reynolds are already, or looking to be, world providers. Aluminum is emerging in markets such as India and China, and in Russia there is high risks, but high rewards.
Reynolds Metals Co., Richmond, Va., for example, predicts continued growth in the industry of 2.5 to 4% annually for the next five years.
But even with steady growth there are pressures. Aluminum pricing has been "disappointing" according to Allen Born, chairman of Alumax. Therefore, Alcoa, which is merging with Alumax, Atlanta, has announced a $1.1 billion cost cutting goal by the year 2001 to stay competitive.
BARRIERS PERSIST
As with any material, barriers must be overcome to increase usage, and The Aluminum Association’s Technical Advisory Committee identified two main barriers: customers’ lack of knowledge of the metal’s performance, and structural characteristics. Another barrier involves the large amounts of energy needed to extract aluminum that affects its cost and use in end products. And while recycling rates for aluminum are high, the committee says that more has to be done to raise that rate even higher, including better alloy separation.
Technology barriers included formability and strength issues of sheet; the need for faster, cheaper joining methods and better coatings; requirements for enhanced lubricating systems; difficulties in joining dissimilar materials; the limited formability of aluminum compared to steel; and demonstrating long-life performance.
In addition to technology barriers, many customers are not very sophisticated in their knowledge of the characteristics and design properties of aluminum.
For example, some designers substitute aluminum for steel in products to take advantage of its lightweight properties but they don’t alter the product design to take advantage of other beneficial properties. This can lead to unrealistically conservative design codes that can contribute to aluminum’s cost disadvantage.
Finally, the committee says that several non-technical issues are limiting the use of aluminum by finished products producers. Barriers include a lack of educated engineers, workers and sufficient R&D funding. In addition, there is insufficient cooperation between aluminum producers and customers and among government, industry, and academia.
The author is a technical writer and Recycling Today contributing editor based in Parma, Ohio.
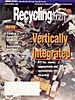
Explore the September 1998 Issue
Check out more from this issue and find your next story to read.
Latest from Recycling Today
- Aqua Metals secures $1.5M loan, reports operational strides
- AF&PA urges veto of NY bill
- Aluminum Association includes recycling among 2025 policy priorities
- AISI applauds waterways spending bill
- Lux Research questions hydrogen’s transportation role
- Sonoco selling thermoformed, flexible packaging business to Toppan for $1.8B
- ReMA offers Superfund informational reports
- Hyster-Yale commits to US production