When government officials, scientists, environmental activists and business leaders converged on Copenhagen in December of 2009, many of the business leaders were there to represent the sustainability aspects of their industry sectors.
The Bureau of International Recycling (BIR) maintained a presence to represent recyclers, and the International Aluminium Institute (IAI), London, prepared its case that the light metal can remain a viable choice in a low-carbon economy.
Much of the IAI’s case for aluminum can be found in a six-page brochure the group prepared for Copenhagen called “Aluminium for Future Generations.”
Growth Anticipated in India |
Although many of the world’s leading aluminum companies have capacity sitting idle as 2010 begins, at least one major company appears poised to invest to increase its production capacity. According to Bloomberg LP, India’s National Aluminium Co. plans to more than double its production capacity in the next several years. The company’s own output of aluminum could grow from 460,000 metric tons to 1.25 million metric tons, Sharma indicated in the interview. According to the Bloomberg article, the company already added 115,000 tons of capacity in December of 2009 and plans to bring another 180,000 tons of capacity to the market via expansion at its Angul plant in the eastern India state of Orissa. The Bloomberg article also attributes Sharma as saying that the company anticipates that aluminum will increase in value as well as in demand during the decade to come. |
The brochure is based on a position paper by the same name first released in 2003 (and updated in 2009), that identifies 14 voluntary objectives through which the IAI says it can improve the “social, economic and environmental performance across all the key phases of aluminum’s life cycle.”
Three of the 14 objectives have a direct application to recycling, while several others involving such things as energy use and emissions cutbacks can entail recycling as part of meeting the objective.
Should the IAI put resources behind its sustainability and recycling goals, that could bode well for the scrap industry. The multi-national organization is comprised of 27 member companies that it says produce some 80 percent of the world’s aluminum.
The extent to which IAI member companies such as Alcoa, Dubai Aluminium Co. Ltd. (Dubal), Glencore International AG, Hindalco, Hydro, Nippon Light Metal Co. Ltd., Rio Tinto Alcan and Sumitomo direct their resources can have a considerable bearing on how investment capital is directed toward the recycling of aluminum.
AN ADDED OBJECTIVE
When “Aluminium for Future Generations” was initially released in 2003, it contained only 13 objectives. The one that has been subsequently added and that is labeled as Voluntary Objective 10 in the 2009 edition focuses on aluminum used beverage container (UBC) recycling.
“The global aluminum industry will work to encourage a global aluminum UBC recycling target of 75 percent by 2015,” reads the IAI’s additional industry objective.
According to the figures being used by the IAI, the UBC recycling rate for 2007 was 69 percent, which would seem to put the 75 percent objective well within range.
However, the aluminum UBC is already “the most recycled beverage container in the world” by the IAI’s own admission, so the additional percentage points may be hard to illicit. As well, the IAI comments, “The collection rate of UBCs depends greatly upon individual national incentives, including deposit systems, voluntary prepaid recycling charges or advertising and the efficiency of the collection schemes.”
The new objective on UBCs joins Voluntary Objective 9, which pertains to the IAI’s commitment to the recycling of all types of aluminum scrap.
CHARTS AND STATISTICS
“The IAI has developed a mass flow model to identify future recycling flows,” reads the objective. “The industry will report regularly on its global recycling performance.”
Calling its industry “a pioneer in racking the global flows of its products through the full value chain,” the IAI says it has developed a mass flow model that tracks material from mining, through use to recycling and re-use.
A resulting flow chart starts with bauxite and then alumina production. The chart shows that in 2008 approximately two-thirds of the light metal’s production consisted of primary aluminum, while scrap-based re-melted aluminum provided one-third of all the metal needed.
The paper tracks and notes scrap volumes produced throughout various stages of the industry, with the tonnages leading back to the re-melt capacity stage of the chart.
Finally, the paper notes the finished product sectors that consumed aluminum in 2008, with the building, transportation and engineering/cable sectors being the three largest by far in ranges from 28 to 32 percent. While packaging applications are visible, they consumed only 1 percent by weight of the total aluminum produced.
The IAI portrays the future of increasing the recycled-content portion of production in a bad news/good news scenario.
“Projected growth rates in the demand for aluminum products, combined with the long life times of most products, suggest that this ratio of recycled-to-primary-sourced metal is unlikely to change in the short-to-medium term,” reads the 2009 report.
On the other hand, “Three-quarters of all the aluminum every produced since the 1880s is still in productive use,” pointing to a deep reservoir of some 640 million metric tons of aluminum that will someday be scrap to be harvested.
Where is all this aluminum? “Of the aluminum currently stored in productive use, equally one-third is in buildings (windows, roofing, cladding, etc.); transport (automotive, public transport, etc.); and engineering and cable applications (overland cables, machinery).”
GREEN ANGLES
Sustainability as defined by most of those using the term extends beyond materials recycling. In its “Aluminium for Future Generations” sustainability report, the IAI also addresses carbon emissions, fluoride emissions, energy consumption, human health and safety, mine site land rehabilitation and recovering resources from spent pot-lining (SPL) generated at smelting facilities.
The latter objective presents opportunities for recyclers willing to handle the trace amounts of aluminum found in SPL or those in the recycled aggregates sector willing to work with the material.
The IAI report notes that a “main barrier to [using] SPL as a feedstock has been [that] individual smelters do not produce enough SPL to provide a continuous supply of feedstock” for consumers that may be able to use the material.
Recycling companies with experience in aggregating material and with the equipment to collect it at different locations could be among those to help hurdle this identified barrier.
Minding the Metal |
A session being planned for the 2010 Paper Recycling Conference is likely to be of interest to recyclers who handle metal containers along with their tons of scrap paper. “Minding the Metal” is a session scheduled for Sunday, June 13, from 4 to 5 p.m. at the conference, which takes place at the Marriott Downtown Chicago-Magnificent Mile June 13 to 15, 2010. The session is being designed to address both operating and trading considerations for recyclers who collect, sort and sell aluminum used beverage containers (UBCs) as well as tin-plated steel food cans and other metal containers commonly collected from homes, commercial locations and at special events. More information about the Paper Recycling Conference’s schedule, location and how to register can be found at www.PaperRecyclingConference.com. |
On the energy consumption front, every time the industry can tap into the 650 million metric tons of existing aluminum to make new products, it is saving considerable energy. As the IAI’s Web site notes, “The use of recycled metal in any aluminum product results in an energy saving of up to 95 percent over the use of primary metal.”
In an essay in the book “One More Time,” published by the Danish scrap recycling firm H.J. Hansen in 2009, chemical engineering professor Henrik Wenzel notes that to make 100 kilograms of aluminum without scrap requires 1 metric ton of mined ore and 230 kilograms of fuel. But to make 100 kilograms of aluminum from scrap requires merely 104 kilograms of scrap and 20 kilograms of fuel.
There seems little question that as events like the Copenhagen 2009 United Nations Framework Convention on Climate Change meeting occur in the future, the IAI will continue to examine the ways recycling can keep its industry viable in all legislative and meteorological climates.
The author is editor-in-chief of Recycling Today and can be contacted at btaylor@gie.net.
Get curated news on YOUR industry.
Enter your email to receive our newsletters.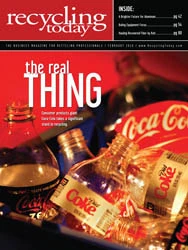
Explore the February 2010 Issue
Check out more from this issue and find your next story to read.
Latest from Recycling Today
- LumiCup offers single-use plastic alternative
- European project yields recycled-content ABS
- ICM to host colocated events in Shanghai
- Astera runs into NIMBY concerns in Colorado
- ReMA opposes European efforts seeking export restrictions for recyclables
- Fresh Perspective: Raj Bagaria
- Saica announces plans for second US site
- Update: Novelis produces first aluminum coil made fully from recycled end-of-life automotive scrap