T
he automobile shredder has one of the toughest jobs in recycling—and the hammermill’s wear parts reflect just how much abuse the machine takes in doing its job.No matter how hard the alloy, shredder wear parts are quickly worn down, especially the hammers. Additionally, the metal panel wall gets beat up fast, as do the rotor and the grates at the bottom of the shredding chamber.
With hammers supplying the greatest burden in an auto shredder, wear parts represent a large chunk of a shredding plant’s operating costs. Estimating strictly on parts purchased and delivered and not accounting for variables like electricity and waste disposal charges, wear parts can account for 60 percent to 70 percent of a shredding plant’s costs, says Kevin Toft, general manager at Riverside Engineering Inc., San Antonio. And while auto shredder operators can’t get around wear part replacement, they can take steps to decrease their costs and to prolong the lives of their parts.
SLOWING WEAR. While there haven’t been many recent technological or operating breakthroughs when it comes to reducing wear on hammermills, some old tricks of the trade are becoming more widely accepted and practiced by operators trying to squeeze a little extra life out of their shredder wear parts, says Jim Schwartz of Texas Shredder Inc., San Antonio.
"The ideas, in principle, are very old," Schwartz says. "Something that’s been known for a long time by the sharpest shredders is happening more often—if you keep the shredder box full of scrap, wear parts last longer."
Keeping the box full takes some of the pressure off the hammers as scrap shreds in part against itself, saving some wear and tear on the cast parts, he says.
"Full-box shredding results in higher wear part life and denser scrap," Schwartz says.
Toft agrees. "Keeping the shredder full at all times is the best way to get the full performance from the shredder and the wear parts in the shredder," he says. "When the shredder is kept full of material, the motor is constantly loaded, the risk of unshreddables is reduced and the throughput of the shredder is increased," Toft says.
As automated feed systems have become more common, keeping the chamber full has become easier to do, says John Martinek of Levand Steel & Supply, Irondale, Ala. "It’s hard to keep it full using a manual system," he says. "Computer programs help maintain a full mill the whole time—and production goes up."
Increasing "scrap-on-scrap" shredding is a time-tested way to prolong shredder wear part life, says Randy Brace, also of Riverside Engineering.
In addition to keeping the shredder full, Brace also suggests mixing heavier scrap with lighter scrap to generate better production rates and the lowest wear rates.
Brace also says reducing the amount of dirt that is processed with the scrap can help reduce wear on parts. In addition, Brace recommends not shredding scrap to a higher density than needed. "Wear part consumption in the shredder goes up exponentially with an increase in density," he says.
Harris Adds Shredder Project Engineer |
Harris Waste Management Group Inc., Peachtree City, Ga., has added John Bauer as a project engineer in its Shredder Division. Bauer has 10 years of industry experience, having formerly been employed by Riverside Engineering and Newell Industries Inc. He will be based out of San Antonio, Texas, and will specialize in design and layout drawings for shredder plants and downstream systems. "John not only has engineering experience, but he has a lot of experience in installation and start-up of shredding equipment," says Doug Sebastian, executive vice president with Harris. "He will be a great help on our existing projects and future projects." In addition to automobile shredders Harris Waste Management Group manufactures two-ram balers, horizontal balers and vertical balers that process everything from solid waste, cardboard, paper and plastics to non-ferrous metals. Harris also makes ferrous metal balers, shears and shear/baler/loggers. Harris’s ferrous metal equipment can process a large range of metals including autos and scrap metal. |
Some say bigger parts are better, Schwartz says. Many argue if a hammer has more material, it will wear away more slowly and need to be replaced less frequently, he says.
"There’s a school of thought that says narrow hammers cut better," Swartz says. "But wider [hammers] tend to last longer—many hammers come up to 6 inches wide."
Schwartz also says many manufacturers choose to use bridge grates as opposed to multi-support grates on the bottom of the shredder, saying that they’re built to last longer.
While on first consideration, it may sound like multi-support grates would be better on wear, they are generally thinner than bridge grates and actually tend to wear away more quickly, Schwartz says.
"Just about all manufacturers are retrofitting old machines with bridge or trust grates," he says. "They tend to last longer and not break as often."
Toft says there have been a number of revisions to casting chemistry made in the last decade designed to prolong wear part life for shredders. He says the ease of maintenance is now playing a larger part in wear part design than in the past.
"This is easily seen in front wall castings and bottom grate castings," he says. "These pieces are now originally designed to be easier to replace in the mill for less downtime due to maintenance. There have also been changes to spider cap design for increased life and better fit."
KEEPING TRACK. While some principles of wear parts maintenance—like full-box shredding—apply pretty evenly to any shredding operations, others are a little more case-specific, Brace says.
"The recipe for maximizing the money spent on wear parts is a little different for every yard," he says.
For instance, Brace says that a high-production yard will typically choose to replace hammers with fewer production tons on them because a hammer’s productivity drops as it wears out. In tailoring a replacement program, shredding plant operators should be aware of their yards’ wear parts consumption rates and the effect of waiting too long to replace a casting, Brace says.
"For example, some yards replace many liners at one time, reducing overall downtime, while other yards will change liners as they have to be changed," he says. Operators need to examine their individual production rates to figure out which method of replacement will save them more money.
Planning is essential for maximizing the life of wear parts and keeping wear costs down, Schwartz agrees.
He advises keeping accurate records of exactly what is replaced and when. A strict replacement schedule will save on unexpected and costly downtime if a part needs to be replaced before an operator is ready for it, Schwartz says.
Keeping on schedule is particularly important in today’s unpredictable scrap market, Brace says. "The industry is pushing the demand side of the equation past the availability of supply, thus creating a shortage of castings for the processors who wait until the last minute to order parts," he says.
AHEAD OF THE GAME. When the time arises to replace worn shredder parts, operators should take care to make sure they’re shopping smart and getting the most for their money.
Up until a couple of years ago, price dominated the wear parts market, says Schwartz. But the volatility of the scrap industry has changed things, he says. "Prices are a moving target," he says. "Foundries don’t know what scrap is going to cost."
Toft agrees. "Pricing will always be very important, but in today’s market, delivery has become almost as critical."
The smartest shredder operators find a company they can trust and build a relationship with, says Schwartz. "Mutual trust needs to be built up," he says. "You have to have a rapport."
Finding a castor you can trust is a part of effective wear parts maintenance that can’t be underestimated, Martinek says. "Every castor is different—our chemistries are different, our heat treatments are different. You really need to know your supplier."
Martinek recommends testing the wear part waters before making a major purchase. He says when dealing with a new castor, smart operators will try out a small sample before buying a truckload.
Getting references on wear part suppliers is also a good idea, Martinek says.
Schwartz advises going with a company with a strong reputation for good inventory assistance. "You have to think ahead, know your consumption and make sure [the supplier] always has things in the pipeline," he says.
In addition to keeping a good inventory of readily available replacement parts, a smart operator will also keep himself up to date on the latest designs, says Martinek.
"We’re always reinventing the wheel," he says of wear parts manufacturers. "Good foundries are always looking for ways to improve."
Martinek says operators should take advantage of trade shows and seminars to learn about new technology and to meet castors and manufacturers.
Because wear parts are designed to be expendable, experts agree that following a replacement schedule is the best way to control costs.
"Controlling costs is more important than trying to drive the costs down," says Toft. "To control costs, operators must carefully monitor their inventory levels of replacement parts along with watching the infeed material of their shredders. Avoiding costly downtime due to lack of replacement parts or damage caused by unshreddables is a good way to control wear parts costs."
Unplanned downtime usually proves more costly than scheduled wear parts maintenance, Toft says.
Manufacturers say effective planning can keep auto shredders running smoothly.
"Nowadays, availability is far more important than anything else," says Schwartz. "Shredders more than ever have to think ahead."
The author is assistant editor of Recycling Today and can be reached at jgubeno@gie.net.
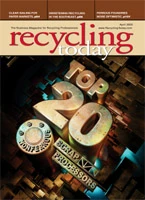
Explore the April 2005 Issue
Check out more from this issue and find your next story to read.
Latest from Recycling Today
- Fitch Ratings sees reasons for steel optimism in 2025
- P+PB adds new board members
- BlueScope, BHP & Rio Tinto select site for electric smelting furnace pilot plant
- Magnomer joins Canada Plastics Pact
- Out of touch with reality
- Electra names new CFO
- WM of Pennsylvania awarded RNG vehicle funding
- Nucor receives West Virginia funding assist