Brothers Craig and Scot Uhrig, now 38 and 36 years old respectively, admit that they weren’t certain how things would go when they started their own scrap metals company in 1991.
The duo started All Recycling as a one-acre nonferrous feeder yard in Englewood, Colo., on a parcel of land where Englewood borders the city of Denver.
In the subsequent 18 years, Craig and Scot have helped preside over a company that has grown steadily in terms of the volume and types of material it handles. The capital equipment deployed and the amount of property All Recycling now owns help it serve the growing ranks of customers from which it buys and to whom it sells ferrous and nonferrous scrap.
HELPFUL ADVICE
The Uhrig brothers started All Recycling not long after Scot graduated from high school and while his older brother, Craig, was only 20. They chose the metals recycling business because their father, Bill, had worked in the industry during the 1970s and 1980s.
ALL RECYCLING AT A GLANCE |
Principals: Brothers Scot and Craig Uhrig Location: A 25-acre facility with a shredding plant, nonferrous facility and rail loading area sits astride Englewood and Denver, Colo.; additional feeder yards and two transfer stations are in other parts of the Denver region No. of Employees: 150 Equipment: 6,000-horsepower Riverside Engineering M106 Megashredder; shredder downstream system with SGM eddy currents and sensor sorters, plus trommells and a Bivitec screen; two Harris two-ram balers; alligator shear; three Genesis mobile shears; 12 Terex Fuchs hydraulic scrap handlers; 10 Komatsu wheel loaders; 35 trucks; 100+ trailers; and 500+ containers Services Provided: Recycling of ferrous and nonferrous obsolete and industrial scrap; mobile car flattening services; solid waste transfer station management |
“He had retired from the business, but we used a lot of his knowledge and advice as we got started,” says Scot. “We definitely have to give a lot of credit to my father.”
Bill Uhrig still frequently visits the facility and is proud of what his sons have accomplished, say Craig and Scot.
All Recycling started as a small feeder yard that purchased nonferrous scrap. “We started on about an acre of ground and in a small building where we collected nonferrous scrap and then took it to larger processing facilities.”
The company diversified into ferrous scrap when, in 1994, a neighboring scrap company closed its doors and its former customers started asking All Recycling if it would accept ferrous scrap. Recalls Scot, “We started paying for loads and we put in a truck scale and started buying ferrous scrap as an ongoing part of our business.”
The decision to broaden the scope of the business led to greater scrap volumes and increased investments into the business, including purchasing additional land, says Scot. In the mid-1990s, All Recycling purchased its first roll-off truck and began pursuing industrially generated scrap.
Subsequently, All Recycling has expanded its footprint in terms of land and buildings, processing equipment and a customer base that draws from 12 western states and into Canada. The scrap products the company makes head to consuming destinations throughout North America and overseas through Pacific Ocean ports and via rail into Mexico.
MOVING UP THE CHAIN
“Initially we were not doing a lot of processing and were more of a feeder yard, but around 1998, there was consolidation in the Denver area that wasn’t too favorable for us,” says Scot. “So we started looking for other avenues to compete and we put in a small Eidal used auto shredder in 1999.”
The company’s first shredding plant had an output of just “20 tons per hour—and that was in a good hour,” quips Scot, but it was an important first step in converting All Recycling from a feeder yard into a scrap processing company.
All Recycling’s customer base and its scrap volumes continued to grow, while Craig and Scot scrambled to put the equipment in place to fulfill its new role as a regional scrap processing company.
“We ran that first shredder for a couple of years and bought more property,” recalls Scot, “and then installed a larger shredder—a Newell 80/104—in 2001. That plant was able to produce at about 40 to 45 tons per hour.”
Just two years later, in 2003, All Recycling installed a larger shredding plant. “We put in a brand new Texas Shredder 80/104 that was able to process 80 to 90 tons per hour,” says Scot. “We also added to our rail capabilities to be able to ship more outbound scrap by rail.”
All Recycling had been using a rail side spur since 2001, but now the company can stage and load a greater number of railcars and also accepts inbound scrap via rail and over its railcar scale.
In 2008 the company purchased yet another shredder—its fourth in 10 years. “We put in a 6,000-horsepower Riverside Engineering shredder that can produce about 250 tons per hour,” notes Craig.
The company’s former one-acre site has grown to 25 acres of land that takes up three-and-a-half city blocks and straddles the border of Englewood and Denver.
Additionally, the company operates several feeder yards in the region and two solid waste transfer stations.
Craig and Scot are quick to note that the growth this decade has only been possible because of the hard work of the company’s managers and other key people among All Recycling’s staff of 150 employees. “We have managers who we trust who run the other locations,” says Scot. “We have some really good managers and employees, and without them we couldn’t be where we are today.”
A SMALLER MINDSET
In tandem with running a more sophisticated and growing business, Craig and Scot say that staying in touch with their roots as feeder yard operators is an important part of their philosophy.
“We try to treat everyone equally, from the guy with the bag of cans to the driver with the semi load of scrap,” Scot says of his and Craig’s philosophy.
“Buying from small dealers, we understand them because we’ve been in their shoes before,” he continues. “We try to understand what their wants and needs are and put ourselves back in their shoes. They need to sell scrap every day or week, even when mills aren’t buying. We’ve been there before; we’ve been in their shoes and I think we relate to that dealer set of customers really well.”
Craig and Scot also have reached out to learn more about the recycling industry through membership and involvement with the Institute of Scrap Recycling Industries Inc. (ISRI) as well as with its supply chain through involvement with the Colorado Automotive Recyclers (CAR) and the Colorado Association for Recycling.
All Recycling was part of an alliance between auto dismantlers and shredder operators that helped put a mercury switch removal program in place in Colorado before the national ELVS (End of Life Vehicle Solutions Corp.) system was established.
OPTIONS AND OPPORTUNITIES
All Recycling’s story has largely been one of growth and forward momentum, but like virtually all companies in the industry, the market turmoil of late 2008 provided an interruption.
The 2008 downturn “came faster and was sharper, but we’ve been through this before,” says Scot. “That’s not to say it didn’t slow things down, and we’ve had to cut hours back for some employees. But we felt comfortable that there would be a rebound, so we went through with our capital equipment investment plans and didn’t shy away.”
The company’s recent investments include an expansion of its nonferrous production building and the installation of a downstream shredding system.
All Recycling’s nonferrous operations—the site of its original small scale where the company got its start—has now moved across the street to a new 5.5-acre parcel and 20,000 square feet of new indoor space that features a high-output Harris two-ram baler. The building is slated to grow by another 8,000 square feet, says Craig.
The shredder yard and the nonferrous plant are hubs of processing activity served by an array of Komatsu wheel loaders and Terex Fuchs material handlers. All Recycling’s fleet of trucks, trailers, containers and its RM Johnson E-Z Crusher mobile car flatteners all help bring scrap into the plants.
Says Scot of the Uhrig brothers’ two-decade journey from a small feeder yard to a major regional processing company: “It gets pretty hectic and it stays busy, but sometimes we do have time to reflect on where we’re at now versus then.”
He continues, “At the beginning, there really wasn’t a firm plan as to where the company would go. We’ve learned as we’ve gone, and we learned to enjoy the business and start growing it.”
Scot says he does not believe the growth is at an end. “We’re looking for new opportunities, possibly other materials and commodities to look into,” he continues. “We’re both young, so we want to expand and keep learning. We go out to our customers that we buy from to find out what kinds of needs they have. We also go to consumers to see what makes a better product for them. We’re constantly trying to understand the whole flow and the whole supply chain.”
The challenges and opportunities are likely to keep the Uhrig brothers engaged in the business for some time to come. Scot is the father of an 18-month-old daughter and his family has another child on the way. Currently, though, any next generation is a long way from managing the company.
For now, the present and near future have plenty to offer, says Scot. “There is always something going on—it just never slows down,” says Scot. “Managing a recycling company keeps you very, very active and it’s never the same thing day-to-day, every day. Personally, I just enjoy the business.”
The author is editor-in-chief of Recycling Today and can be contacted at btaylor@gie.net.
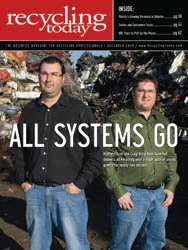
Explore the December 2009 Issue
Check out more from this issue and find your next story to read.
Latest from Recycling Today
- Greenwave Technology pares back losses in Q3
- Lindner shredders prepare Brazilian plastic for recycling
- China ups steel output, while other nations cut back
- ReElement, Posco partner to develop rare earth, magnet supply chain
- Comau to take part in EU’s Reinforce project
- Sustainable packaging: How do we get there?
- ReMA accepts Lifetime Achievement nominations
- ExxonMobil will add to chemical recycling capacity