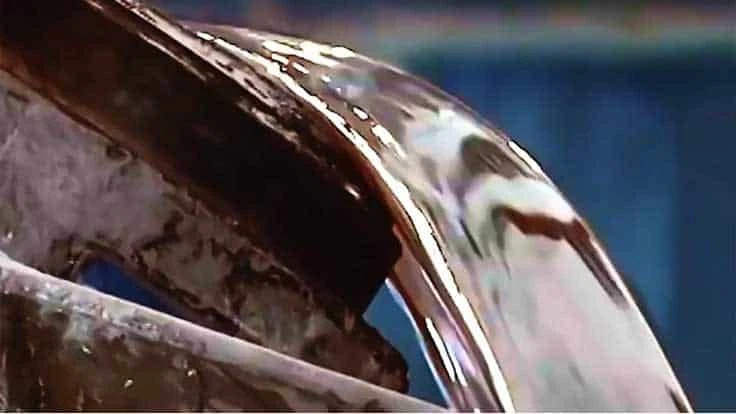
Photo courtesy of Alcoa.
Pittsburgh-based aluminum producer Alcoa Corp. says its new, patented Astraea metal purification process has been developed to convert shredded aluminum scrap into high-purity aluminum. “The process could create an entirely new value chain to economically produce aluminum of a quality that far exceeds the purity of the commercial-grade aluminum produced in a smelter,” the company says.
Alcoa says the Astraea process can “purify any postconsumer aluminum scrap into a purity level of P0101, surpassing the purity of P1020 aluminum that is produced at any commercial smelter.” The company says there is “a vast supply of aluminum scrap that can only be used for limited applications due its combination of impurities,” and cites the shredded zorba grade as an example.
The P1020 designation represents aluminum that is 0.1 percent silicon and 0.2 percent iron, says Alcoa. With few exceptions, most smelters have the technical capability to produce up to P0404, depending on how they deploy technology. The market has two, currently available solutions, that can translate P0610 or P1020 into higher grades, adds the company.
However, Alcoa says its Astraea process “would build a robust solution that could take any postconsumer aluminum scrap, regardless of alloy combination, and beneficiate it up to P0101. This super-pure metal could then be blended with less-pure scrap to produce a metal that meets purity thresholds, vastly improving the supply of postconsumer scrap that can be used as a raw material. The purity would be high enough for most rolling mill and extrusion applications, including applications in aerospace.”
Regarding zorba, Alcoa says because “the industry is unable to remove trace metals from this scrap, much of this metal is used to make engine blocks for gas-powered cars, which can tolerate less-pure scrap as a raw material. However, that market is slowly diminishing due to the growth of electric vehicles, which require higher purity aluminum for engines and other componentry.”
The company continues, “Today, there are no commercially available processes to [upgrade zorba] to the suitable purity for most rolling or extrusion applications. Alcoa’s Astraea process is the first and only technology that can purify this low-value scrap.”
The U.S.-based company says zorba produced in the U.S. “often is shipped to Asia in vast quantities. The U.S. alone produces approximately 4 million tons of zorba annually, approximately 1.3 million tons of which is shipped to Asia.”
Alcoa cites a carbon emissions reduction tie-in for adopting the Astraea process. “According to the International Aluminium Institute (IAI), the industry needs to increase postconsumer scrap recycling by 55 percent over 2018 levels by 2030 to achieve industry decarbonization goals for the 1.5-degree scenario outlined in the Paris Agreement. Alcoa’s patented technology could help achieve those scrap recycling targets.”
Astraea was one of three concepts introduced by Alcoa in a November Investor Day technology roadmap presentation. That presentation can be downloaded from this web page.
“Our technology roadmap represents an array of next-generation solutions that could significantly reduce emissions across the upstream value chain and concurrently generate significant stockholder value,” says Alcoa President and CEO Roy Harvey.
“Alcoa developed the aluminum industry more than 135 years ago, and that legacy of innovation motivates us to help create a better future for tomorrow – one where we are leveraging our products, processes, and people to realize our vision to reinvent the aluminum industry for a sustainable future,” adds Harvey.
Latest from Recycling Today
- Aqua Metals secures $1.5M loan, reports operational strides
- AF&PA urges veto of NY bill
- Aluminum Association includes recycling among 2025 policy priorities
- AISI applauds waterways spending bill
- Lux Research questions hydrogen’s transportation role
- Sonoco selling thermoformed, flexible packaging business to Toppan for $1.8B
- ReMA offers Superfund informational reports
- Hyster-Yale commits to US production