Many companies, seeking to chart a "greener" path and to improve their bottom lines, have gone beyond rudimentary recycling programs and are looking at the concept of greater landfill diversion.
One company that has been striving to improve its environmental efforts is the Energizer Personal Care Co. (EPC), a part of Energizer Co. Joe Huk senior corporate purchasing manager for The Energizer Personal Care Co., Playtex Division, in Dover, Del., was tasked by senior management with reviewing how the company managed and dealt with its waste stream. The Personal Care plants manufacture products for EPC’s feminine-care, infant-care, wet shaving, sun-care and wipes business segments.
Working with A Greener Solution LLC, Zion, Ill., Huk created a cross-functional team that reviewed the processes and waste streams of the manufacturing plants. Sites that fell under the initial research included plants in Dover; Sidney, Ohio; and Ormond Beach, Fla. The review process also expanded to include the company's Schick EPC facility in Milford, Conn.
Huk says the tools used to find ways to reduce the amount of material being landfilled included process mapping of how its disposal was presently handled followed by recommendations for improvements. The company established a charter and stretch goal for recycling in excess of 90 percent, far above its initial baseline of 25 percent.
"We needed assistance from subject-matter experts to achieve our goals," says Huk. "We wanted a step change improvement. To do that, we needed more expertise than we had in house. We wanted the program to be impactful. After a thorough search for the correct supply partner, and a few starts and stops, we established and continue to develop our relationship with A Greener Solution (AGS)."
Huk says the expertise, creativity and structure AGS brings to the table is significant. "Many larger companies were glad to manage our plastic regrind and old corrugated containers (OCC), but few would engage to the level of detail we were looking for to reach our goals. This is where AGS distinguishes itself," says Huk.
"They work closely with their customers and worked to manage the entire waste stream vs. cherry-picking larger commodities," Huk says of AGS. "In essence [AGS is] a one-stop solution, which is what I was after."
Partnering with AGS allowed the company to reach its stretch goals. The company's Dover plant is achieving a 90 percent diversion rate, with more than 11 million pounds of material being diverted from landfills from all EPC facilities in 2010. "The underlying benefit is that the program actually supports itself and can generate revenue," says Huk. "The largest cost impact is the avoidance of landfill fees. We actually eliminated all trash compacters from our Dover site and manage the non-recyclable waste with one FEL (front-end loader) container," Huk notes.
Even though it is achieving a 90 percent diversion rate at its Dover plant, the company, along with AGS, is looking at other opportunities to further reduce the volume of material being landfilled, including looking at waste-to-energy options.
In addition to the benefits of working with a partner like AGS, Huk credits employee acceptance of the program as key to its success. "We knew we needed to make a culture change for this to be effective and longstanding," he comments. "We spent a lot of time up front communicating with the plants and employees to ensure they understood what we were doing and the expected benefits to the company and the environment. It became an easy sell once we crystallized our message. The program is alive and well and continues to be a cornerstone of our corporate sustainability program."
- Dan Sandoval
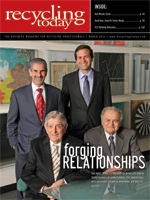
Explore the March 2011 Issue
Check out more from this issue and find your next story to read.
Latest from Recycling Today
- Nucor receives West Virginia funding assist
- Ferrous market ends 2024 in familiar rut
- Aqua Metals secures $1.5M loan, reports operational strides
- AF&PA urges veto of NY bill
- Aluminum Association includes recycling among 2025 policy priorities
- AISI applauds waterways spending bill
- Lux Research questions hydrogen’s transportation role
- Sonoco selling thermoformed, flexible packaging business to Toppan for $1.8B