
Totally autonomous sorting, a process most material recovery facility (MRF) operators have long considered unattainable, might be on the horizon.
Can a completely autonomous processing system be next?
In the fourth quarter of this year, a Canadian MRF operator is set to start up the first autonomous sorting line installed by Bulk Handling Systems (BHS), Eugene, Oregon. The system uses artificial intelligence (AI) to refine itself as plastics and other materials make multiple passes through optical sorters. It took more than eight years to develop the components and build the system.
“Our focus is to absolutely eliminate all of the people in the system with the exception of maintenance personnel,” says BHS Chief Technical Officer Thomas Brooks, who is based at the BHS technical center in Nashville, Tennessee.
“We absolutely believe this is the next big change we are going to see in recycling, just like what we saw when we introduced optical sorting and just like what we saw when we introduced robotics,” he adds.
Operator sets priorities
The system takes out much of the human decision-making in terms of prioritizing what type of material to sort and also can remove five different commodities.
“The operator has the ability to select on all five of those and how much of each he wants to remove from the stream,” Brooks says. “How aggressive do you want to be? What are you trying to achieve? You have also got some flexibility around market conditions.”
Brooks says the system also can determine which commodities to process first and how many times to send material through the system to extract each one.
“You end up with material going out to prescribed bunkers, and a person has not touched it either physically or technically,” he says, adding that maximum throughput of the system is about 6.5 tons per hour but easily can be set for higher throughputs.
BHS is not permitted to name the MRF operator or location except to say it is in Canada.
This first autonomous sorting system uses temporary storage bunkers and conveyors configured in a loop to carry mixed materials several times through an AI-powered optical sorter and robot station. The computer can reprogram itself with each pass to pull out a different commodity until all the polypropylene, natural high-density polyethylene (HDPE), colored HDPE, polyethylene terephthalate and aluminum cans have been sorted but also can prioritize a single commodity.
Brooks says the circular layout and sophisticated control system mean a single optical sorter and robot can do the work of several units. In a traditional sorting line, which requires a bigger footprint, five optical sorters and five robots would be needed to sort out five commodities.
BHS-powered system
Technology that drives the autonomous sorting system comes from several business units within the BHS group. Optical sorters, first introduced about eight years ago, are built by Nashville-based National Recovery Technologies, or NRT, air separators and conveyors come from Amsterdam-based Nihot and robotic sorters and vision systems are BHS Max-AI autonomous quality control (AQC) technology.
A Max-AI AQC-2 system uses a pair of delta robot arms to conduct a presort. “It is pulling out the general stuff you would see going into a container line, such as large residue, textiles, the random tennis shoes and teddy bears,” Brooks says. “There is also a magnet before going into the dedicated loop that pulls out ferrous material.”
He says the process allows the system to focus on specific commodities, noting, “The more noncommodities we can pull out, the greater the capacity and improvement in run times and everything else because of the larger cuts you can make with every pass.”

The vision system starts analyzing the stream during the initial presort, and the data help the control system decide the best way to sort the material.
After the presort, the material goes into a storage bunker. Once the bunker is full, the control system releases it to be conveyed to an optical sorter equipped with an AI-powered vision system and near-infrared detection system. The sorter then ejects the material it is programmed to detect, and the ejected material goes through another AQC-2 dual-arm system to be placed in the bunker designed for that item.
Everything not ejected by the optical sorter is conveyed back to the first storage bunker, and the process is repeated when the bunker is full. After several passes, it is expected that everything the control system is programmed to detect will have been ejected from the waste stream at the levels set by the operator.
The line requires one to two hours per day of downtime for maintenance, which includes cleaning the optical sorter lenses, checking light levels and checking for obstructions and general cleanliness.
Optimism for the future
Brooks says he is confident the new sorting system will operate as planned. “We’ve come a long way since we first introduced AI back in 2016 so that the systems we put in place now are performing at a relatively high level right out of the gate," he says. “We have learned so much over that time around the database creation, how we train, what we know about materials and how the AI and neural networks respond to different training techniques.”
Brooks says the installation has generated a good deal of interest from BHS customers, many of which struggle to hire and keep workers on sorting lines.
“Within the next couple of months, I am expecting to see another probably two or three of these contracts being signed, and then we will be looking for those to be closed out [installed] by the end of 2023,” he says.
Brooks adds, “We are very anxious to get this first system going. We expect to learn a lot at this first location.”
This new, patented sorting line technology is a big steppingstone, he says, and BHS is looking ahead to expanding it to a completely autonomous plastics processing system—an entire plant run by one or two maintenance people—a goal he says he has been working toward since 2016.
Get curated news on YOUR industry.
Enter your email to receive our newsletters.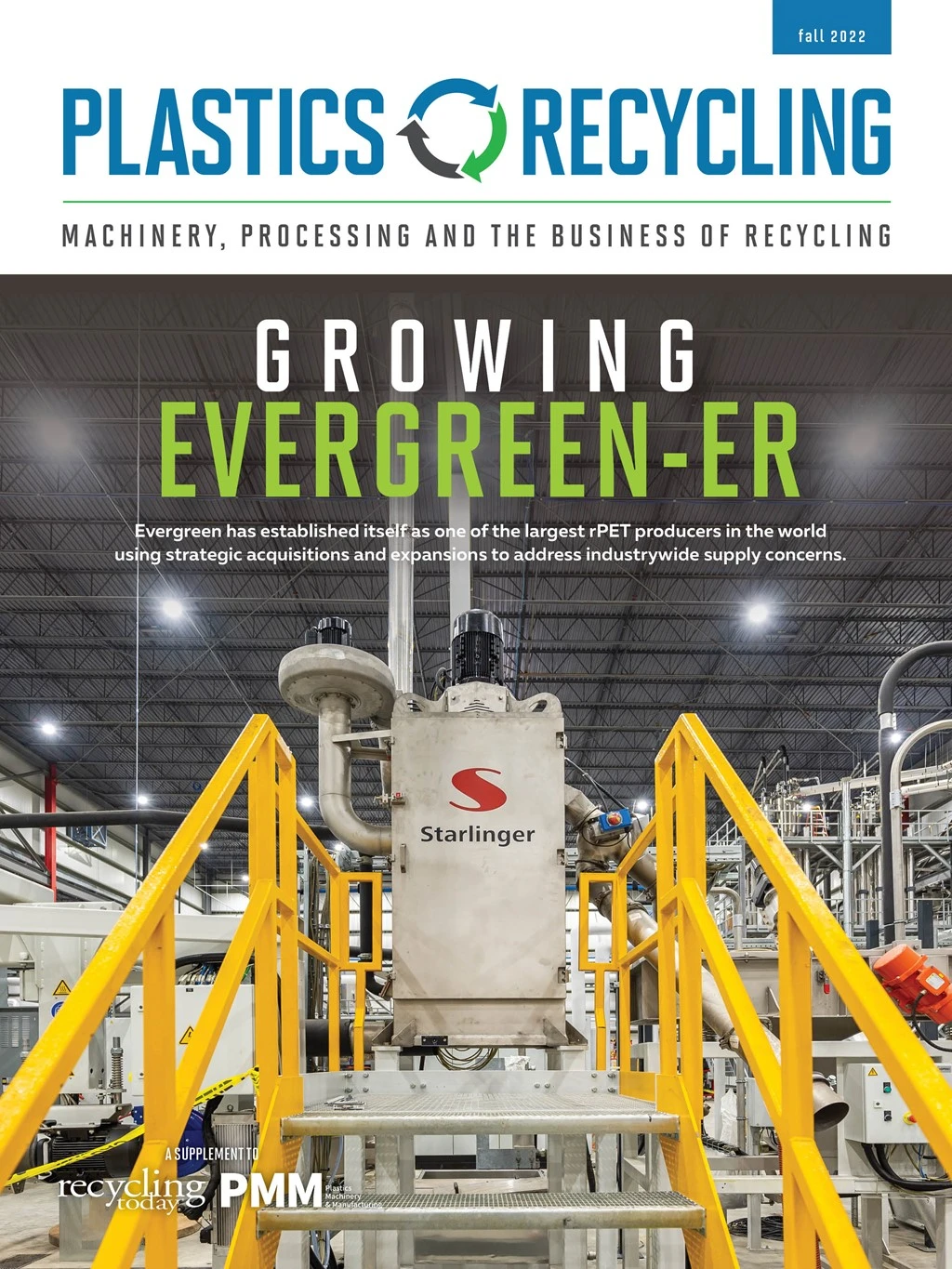
Explore the Fall 2022 Plastics Recycling Issue
Check out more from this issue and find your next story to read.
Latest from Recycling Today
- ReMA opposes European efforts seeking export restrictions for recyclables
- Fresh Perspective: Raj Bagaria
- Saica announces plans for second US site
- Update: Novelis produces first aluminum coil made fully from recycled end-of-life automotive scrap
- Aimplas doubles online course offerings
- Radius to be acquired by Toyota subsidiary
- Algoma EAF to start in April
- Erema sees strong demand for high-volume PET systems