
During its 2024 fiscal year, Advanced Drainage Systems purchased 540 million pounds of recycled polypropylene and
high-density polyethylene.
Photos courtesy of Advanced Drainage Systems Inc.
Advanced Drainage Systems Inc. (ADS) places itself at the intersection of water stewardship and plastics recycling and has set ambitious goals for the latter.
The company, which manufactures water management solutions such as corrugated thermoplastic pipe, chambers and stormwater filters for the stormwater and septic wastewater industries, also is one of the largest plastic recyclers in North America, using more than 500 million pounds of recycled polypropylene (PP) and high-density polyethylene (HDPE) per year.
Headquartered in Hilliard, Ohio, ADS operates more than 100 facilities—including 50 for production of pipes and other water management products and nine for recycling—and employs about 5,000 people across its vast operations.
Approximately two-thirds of the postconsumer and postindustrial resin the publicly traded company uses in its products are processed in-house, and it aims to procure 1 billion pounds of recycled materials per year by 2032. To meet its goal, ADS has spent $36 million in the last year upgrading its recycling infrastructure and is in the process of ramping up its ability to research and develop ways to incorporate a more diverse array of recycled materials in the future.
By the end of this year, ADS officially will open its $65 million Engineering & Technology Center in Hilliard, a 110,000-square-foot facility where its team will focus on product development, testing operations and manufacturing engineering development, which includes recycled content.
“I think one of the things that makes ADS unique is the fact that we are preserving water and we’re doing it with recycled plastic, and that intersection, to me, is really fun to be a part of,” says Scott Fredrickson, a category manager of recycled materials and sustainability at ADS.
Engaged recyclers
ADS has used recycled-content plastics in its products for more than 30 years, and its 2024 fiscal year sustainability report highlights that commitment.
In fiscal year 2024, the company processed 540 million pounds of postconsumer and postindustrial plastics—about 50 percent of the 1.1 billion pounds of plastic it purchased during that period. In particular, ADS consumed approximately 33 percent of the recycled pigmented HDPE bottles recovered in the U.S., an increase from about 25 percent during the 2023 fiscal year.
Fredrickson says one major advantage ADS’ pipes have over other recycling applications is their long service life. He notes the company’s black pipe, which is made from mixed-color HDPE, and its gray pipe, made with PP and designed to compete with concrete, can last up to 100 years after installation.
“When we recycle a postconsumer bottle, for example, that bottle will not end up in a landfill for 100 years because it’s going into a product that’s going in the ground,” he says. “And it will be there for a long time.”
While the company currently uses a nearly 50-50 mix of recycled and virgin resins in its products that can vary slightly year to year, its goal is to use 1 billion pounds of recycled material per year by 2032, and it is taking substantial steps to get there.
In December 2021, ADS acquired privately owned Jet Polymer Recycling, based in Fort Payne, Alabama, further expanding a recycling footprint that spans North America. The Jet Polymer purchase included three plants in Alabama and Georgia with the capacity to recycle about 100 million pounds per year. Along with the former Champion Polymer Recycling, a Winchester, Kentucky-based company and division of ADS subsidiary Infiltrator Water Technologies, the two comprise ADS’ PP recycling arm.
Through the company’s vertically integrated in-house recycling operation, ADS Recycling, it reprocesses baled material into flake and pellets.
The company’s recent investments are focused on transitioning to bulk handling for pellets, simplifying blending processes and enhancing material quality.
“These enhancements enable our recycling facilities to shift from the conventional practice of shipping in cardboard gaylord boxes with plastic liners to bulk shipping, thereby curbing waste and reducing the risk of contamination,” ADS says in its report.
Additionally, the company is installing what it says are state-of-the-art vented extruders at its facility in Cordele, Georgia, that can eliminate encapsulated moisture in its recycled plastic pellets.
“This upgrade ensures the production of high-quality recycled pellets,” ADS reports, “facilitating their seamless integration as a drop-in replacement for virgin resin.”
Fredrickson, who spent a decade in the recycling industry before joining ADS three years ago, notes the company’s dedication to producing high-quality pellets.
“I was very familiar with who ADS was [before joining the company], and I knew them as incredibly picky,” he says. “At the time, I thought, ‘Come on, guys, you’re making black pipe.’ But because we’re making a thin-wall product, you actually need a really high-quality pellet. To be able to extrude that product without having blowouts and other problems [is important] and getting moisture in pellets is a real issue. Having extruders that can pull all that moisture out and make sure we’re creating a pellet that doesn’t look like Swiss cheese, that keeps our scrap rates low.”


ADS’ Engineering & Technology Center in Hilliard, Ohio, will consolidate its product development, testing operations and manufacturing engineering development once it opens late this year.

The Engineering & Technology Center is a $65 million investment that spans 110,000 square feet in Hilliard, Ohio.
Along with upgrading its recycling facilities, ADS is transitioning to reusable totes for internal storage of recycled flake and pellets within each ADS recycling facility to minimize potential contamination and reduce scrap generation.
Looking to the future
Once ADS begins operations at its Engineering & Technology Center, engineers, scientists and technicians will play a crucial role in the company’s 1-billion-pound goal for recycled material use.
In its announcement of the project in August 2022, ADS President and CEO Scott Barbour said his team would build sustainable solutions that use recycled plastics to improve quality of life in communities across North America.
“The ADS Engineering & Technology Center will be the most advanced stormwater engineering center in the world dedicated to product engineering, material science and manufacturing technologies,” Barbour said at the time. “This new facility will accelerate our development of products designed to capture, convey, store and treat our most precious resource: water.”

The new facility will consolidate all of ADS’ current product development, testing operations and manufacturing engineering development into one central location, and will include a product development laboratory focused on the full range of a product’s life cycle; a hydraulics lab that supports ADS’ water treatment business, including separation, traditional filtration and low-impact development filtration; an advanced technology lab for manufacturing and engineering prototyping; and materials science labs.
In the product development lab, ADS says its team will be able to prepare product samples for testing, fabricate prototype parts and test fixtures, analyze structural performance of prototypes and use three-dimensional printing to rapidly develop and vet concepts. The company’s materials science labs will include extensive performance-based materials testing capability, analytic tools to generate structural and chemical information on materials and extrusion capability for the development of next-generation product formulations.
“There are a lot of different goals [for the facility],” Fredrickson says. “One of the big ones is having everyone under one roof in one place with all the testing they need done right there. It will allow us to bring products to the market quicker.”
From a recycling standpoint, Fredrickson is hopeful and optimistic about the facility, saying it will allow ADS to expand outside of its traditional recycling streams in search of new resins. He uses flexibles and low-density polyethylene film as two hypothetical examples of material that could be tested at the site to see if it could be incorporated into pipe manufacturing.
“Having that site there really allows us, in procurement, to find opportunities to pass that [new material] off to material science and let them run with it and come up with an answer relatively quickly on if it’s something we want to expand into and start trying to collect and recycle that material,” he says.
Outside its own recycling initiatives, ADS has gotten involved with several recycling industry associations that include The Recycling Partnership (TRP) and the Association of Plastic Recyclers (APR), both based in Washington, to help push for higher nationwide collection rates. While the company relies on in-house production of its flake and pellets, it also sources about one-third of those products from other North American recyclers.
“If tomorrow I flipped a switch and we were able to utilize a billion pounds of recycled material, we wouldn’t know where to get it all, and there’s not enough recycling within the United States, even within North America, to feed that demand,” he says. “We view joining these industries as, ‘Hey, we’re prorecycling, we’re prorecycling expansion.’ Anything we can do to help and kind of put our money where our mouth is on helping expand access to recycling and to get more people recycling and to get the word out is worthwhile.”
Addressing challenges
In Fredrickson’s view, the biggest challenge the plastics recycling industry faces surrounds the amount of potential demand looming in the future and the lack of clarity on where supply will come from. Data published in recent years by organizations such as the APR, TRP and the U.S. Plastics Pact, among others, have shown U.S. recycling rates of around 27 percent for HDPE bottles, for example.
“[Companies] are all making investments into recycling and saying, ‘OK, we’re going to get into recycling, as well,’” Fredrickson says. “But there’s no talk about how we are going to truly expand recycling in the United States. … Everyone’s jumping in, but where’s all the material going to come from? We’ve got to figure out how to make recycling more effective here. Otherwise, you can have a lot of people that are going to put a lot of money into something that’s going to sit idle.”
He points to the Engineering & Technology Center as one possible solution for ADS as it looks to increase its recycled material usage.
“I don’t know that I’ll always be able to rely on my bread-and-butter streams,” Fredrickson says. “Today, we have what got us to the first 550 million pounds. But what got us here today is not what gets us to a billion. We’re going to have to think outside the box. We’re going to start looking at utilizing different types of materials because, frankly, there’s no visibility to getting to an 80 percent recovery rate of HDPE out of residential streets, unfortunately.
“There’s really no one positioned better to lead that charge than ADS,” he continues.
“We have a lot of experience [in plastics recycling]. … We’re vertically integrated. We know we’ve got the outlet for the recycled materials, so it really puts us in a unique position to lead the way on what we could do with film or some of these other hard-to-recycle materials that are in abundance out there. The technology center is going to help answer a lot of those questions.”
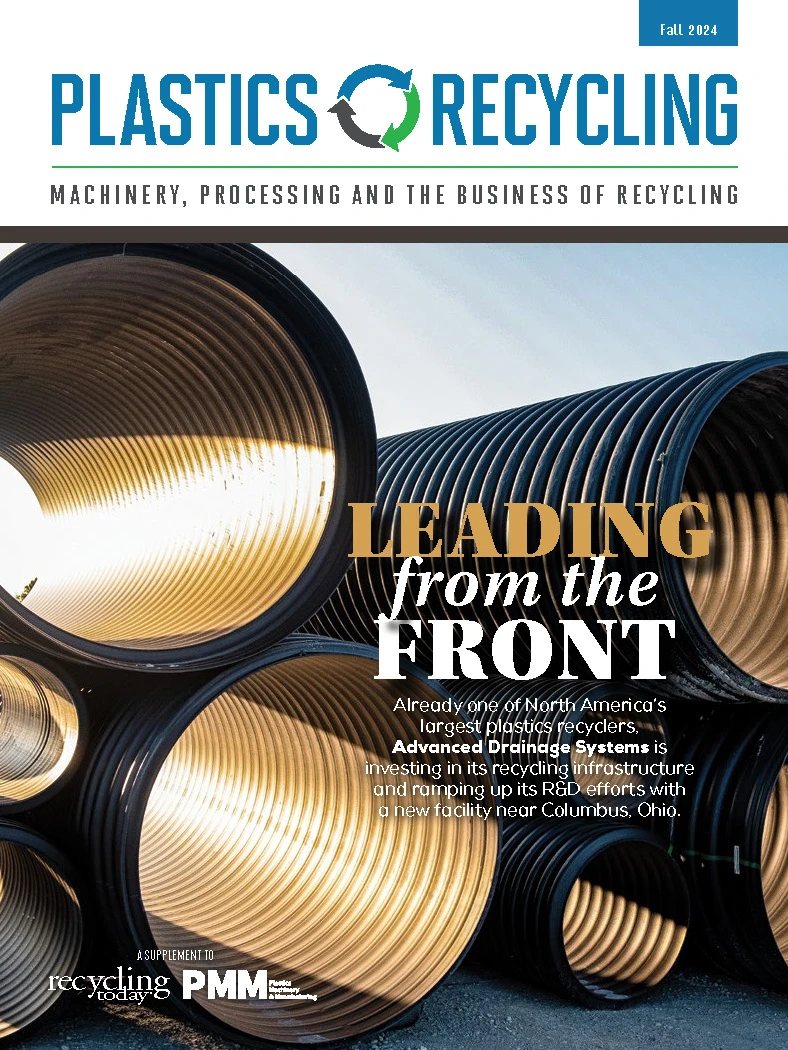
Explore the Fall 2024 Plastics Recycling Issue
Check out more from this issue and find your next story to read.
Latest from Recycling Today
- ICM to host co-located events in Shanghai
- Astera runs into NIMBY concerns in Colorado
- ReMA opposes European efforts seeking export restrictions for recyclables
- Fresh Perspective: Raj Bagaria
- Saica announces plans for second US site
- Update: Novelis produces first aluminum coil made fully from recycled end-of-life automotive scrap
- Aimplas doubles online course offerings
- Radius to be acquired by Toyota subsidiary