
In 1966, Hilliard, Ohio-based Advanced Drainage Systems Inc. (ADS) was founded as thermoplastic corrugated pipe was first being introduced in the United States. From its first thermoplastic corrugated pipe product to its newest stormwater filter, the company has been a “groundbreaker” in the development and manufacturing of advanced drainage products and water management solutions.
ADS was one of the first companies in the U.S. to promote the use of corrugated polypropylene pipe for storm, sanitary sewer and various other product applications. From that point on, ADS has been considered the industry leader in the stormwater management arena.
According to the publicly traded company’s most recent annual report, ADS and its Infiltrator Water Technologies subsidiary purchased more than 550 million pounds of recycled plastics in ADS’ 2020 fiscal year, with its recycling subsidiary, Green Line Polymers, supplying 81 percent of the recycled high-density polyethylene (HDPE) the company used. ADS and Infiltrator Water Technologies, Old Saybrook, Connecticut, consumed 29 percent of the pigmented HDPE bottles recycled in the U.S. during that time.
Daniel Figola, director of sustainability at ADS, says HDPE is the company’s material of choice because “it’s lightweight, but it has strength and durability.”
Responding to a need
With decades of experience working with recycled materials, ADS wanted a way to ensure the recycled plastic entering its facilities was of consistent quality. To address this need, ADS established Green Line Polymers in 2012 to “source, purchase and process” plastic material into a form that ADS could use.
ADS operates eight recycling facilities in California, Georgia, Iowa, New York, Ohio, Pennsylvania and Texas. This does not include Champion Polymer Recycling, Winchester, Kentucky, a division of Infiltrator specializing in the procurement and processing of the recycled materials that are used to make Infiltrator products.
ADS’ recycling process focuses on producing quality recycled material that can go into the pipes made by the company. Incoming material is debaled, and ferrous and nonferrous metals are removed.
“Non-HDPE containers are removed by hand,” Figola says. “There are some automated methods that are out in the market, but to get the quality and the accuracy that we need, hand sorting is still the best way.
“We have a sort line where those materials are sorted, then the materials are flaked in granulators,” he adds.
The flake is washed, dried and then blended. “We take different batches of recycled plastic and different grades and blend them together to get the final product performance level that we’re looking for,” Figola says. “Then we pelletize—basically we take the flake, melt it down, filter it again and process it into pellets that go into our machines that will produce pipe.”
ADS buys plastic from a variety of sources—waste collection companies, manufacturing companies, local recycling entities and organizations and energy companies. “We purchase from a wide variety of sources, and it’s really everything from postindustrial and postconsumer plastic down to detergent bottles that you would use in your home,” Figola says.
The finished pipe and other products that ADS and Infiltrator produce are sold primarily into agricultural, private development, commercial development, public roadway, municipality, public highways and septic markets.
Investing in growth
Since ADS established Green Line Polymers in 2012, the company has invested more than $35 million to improve that subsidiary’s processes and equipment. “We began with high-performance materials, such as barrels and drums, and have been able to increase that kind of range of materials we obtain to pallets, shipping containers and many other types of materials,” Figola says. “[W]e’ve grown to where we were recently ranked by Plastics News as the second-largest plastic recycler in the U.S.”
He adds, “ADS continues to invest in and employ the latest technology with collaborative on-site partners and in its own product development.
“One of the most innovative things is our mobile grinding and washing systems. Those could be deployed directly at job sites across the U.S. to reclaim large quantities of plastic waste in remote locations.” – Daniel Figola, director of sustainability, ADS
“One of the most innovative things is our mobile grinding and washing systems,” Figola says. “Those could be deployed directly at job sites across the U.S. to reclaim large quantities of plastic waste in remote locations.”
Overall, ADS has been focused on its methods of “cleaning, sorting [and] processing” to ensure the quality of the material coming in, he adds.
Focusing on sustainability
ADS says its sustainability efforts aim to reduce pollution, maximize green space and protect natural resources. Many ADS products contain 60 percent or more recycled resins. The company says it is committed to reducing waste through its recycling program and can process HDPE scrap into new products.
“We are committed as a company to providing innovative solutions that protect water, which is a natural precious resource. We primarily deal with the stormwater side, but it is all part of the water cycle. It’s all water that we drink eventually, so we are focused on providing environmentally friendly and cost-effective materials for the management of water,” Figola says.
ADS continues to expand its recycling efforts with the goal of keeping millions of pounds of plastic out of landfills each year. “The protection of water and our recycling initiatives are two of the core pillars in our sustainability program,” he adds.
The company’s sustainability efforts also include reducing its energy and electrical consumption. Figola says, “ADS takes measures to improve its overall environmental footprint.”
ADS recently developed and implemented an environmental, social and governance program, which he says are the three factors used in measuring the sustainability and societal impact of a company. “Sustainability and our environmental stewardship are really driving who we are as an organization and providing a road map for where we go in the future,” Figola says.
Looking to the future
In 2018, changes to the American Association of State Highway and Transportation Officials (AASHTO) M 294 and the American Society for Testing and Materials (ASTM) International F 2306 standards allowed pipes for public storm drains and culverts to use recycled content.
Figola says, “When we first started doing our work with recycled materials, those standards prohibited the use of recycled materials” in pipes for public storm drains and culverts. “It was a big hurdle to convince end users to accept the product and help them to understand the material science and the quality of what we were doing.”
He adds, “The recent standard changes through ASTM and AASHTO have been extremely beneficial in helping increase the acceptance of that product and giving municipalities, engineers and specifiers a safety net, if you will, by saying here’s an actual standard that’s been created and [a] specified product that meets that standard. They can feel comfortable with the products they’re using.”
Figola predicts that recycled-content pipes will continue to grow in popularity. “In the last few years, plastic waste generated by single-use products has become a concern to the public, and processing recycled material into pipes is the perfect outlet,” he says. “We can utilize recycled material of any color and items with odor trapped in the plastic, so really it’s a great solution to some of the plastic waste problems because it’s a great spot for a wide variety of products to go.”
As the focus on sustainability and single-use plastics continues to grow, the acceptance and desire for materials that are made from recycled content also will grow, Figola says.
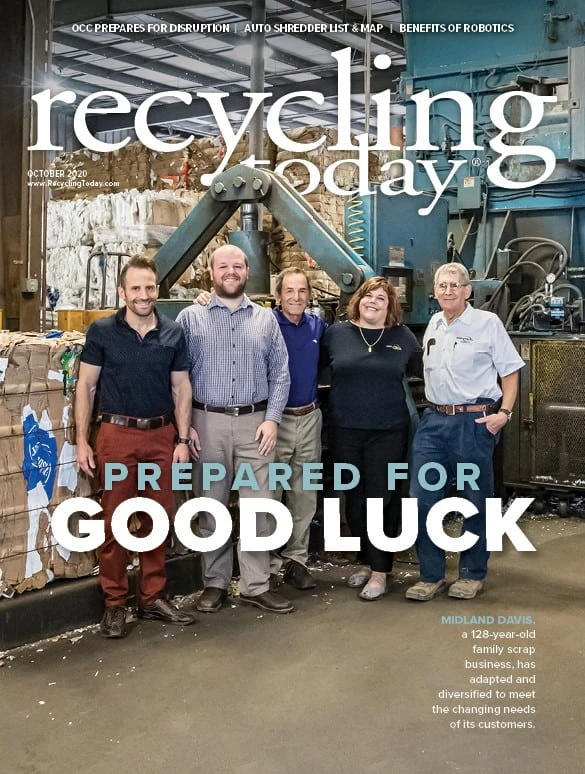
Explore the October 2020 Issue
Check out more from this issue and find your next story to read.
Latest from Recycling Today
- Astera runs into NIMBY concerns in Colorado
- ReMA opposes European efforts seeking export restrictions for recyclables
- Fresh Perspective: Raj Bagaria
- Saica announces plans for second US site
- Update: Novelis produces first aluminum coil made fully from recycled end-of-life automotive scrap
- Aimplas doubles online course offerings
- Radius to be acquired by Toyota subsidiary
- Algoma EAF to start in April