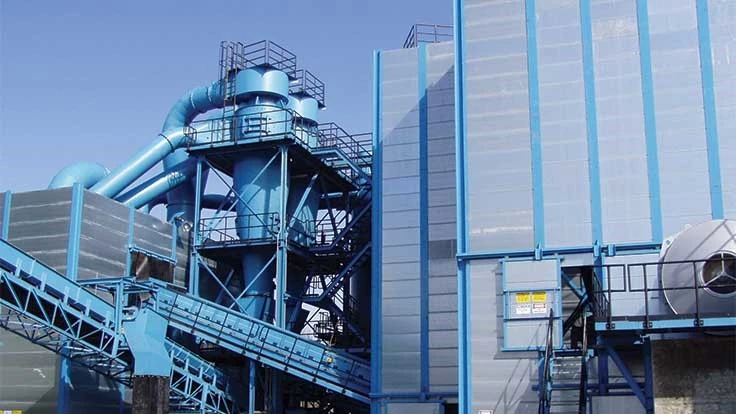
Wendt

Concern about auto shredder emissions is not a new issue, but it is a growing one. Shredding automobiles creates very fine particles of dirt and dust that can become airborne. European countries have long-established guidelines. In the U.S., government scrutiny of auto shredder emissions varies from state to state and city to city. To date, most of the scrutiny has been in California and several large metropolitan areas around the U.S.
For example, General Iron Industries, a metal shredding and recycling facility based in Chicago, has been cited for violations of the Clean Air Act, including air emissions from its auto shredder that the U.S. Environmental Protection Agency says have exceeded allowable limits. In August, the company announced that it installed and is operating a $2 million regenerative thermal oxidizer (RTO) that enables General Iron to comply with a state requirement to reduce uncontrolled volatile organic compound (VOC) emissions. Since the installation was completed in July, General Iron and the EPA have reached an agreed Administrative Consent Order resolving the alleged violations the EPA issued last year.
The trend toward greater scrutiny of auto shredder particulates is likely to gather steam in the coming years, according to auto shredder suppliers. However, emission control systems can help to control particulates, and more shredder operators are showing an interest in the technology.
“We are finding that as time goes on, it is migrating from California and we are seeing increased scrutiny from regulators all over the U.S. and Canada,” Ethan Willard, business development manager, shredders, for Buffalo, New York-based Wendt Corp. says of auto shredder emissions. “As far as most of our North America customers are concerned, it’s relatively new over the past two to three years.”
Keith Carroll, business development manager, metal recycling Americas, at Helsinki-based Metso, says his company has received several inquiries from West Coast shredders, as well as from operators in large Midwestern and Eastern cities, regarding dust-extraction-type emission control systems. He says he believes demand will continue to grow.
Fewer than 30 auto shredders of the nearly 300 auto shredders installed in North America use emission controls, Carroll estimates; however, he adds, about 90 percent of shredders in Europe have some type of extracted-dust control.
“It will be driven by environmental factors,” Carroll says of regulation in the U.S. “Plus, there will be reaction to what is occurring in Europe.”
He adds, “In Europe they have been getting further down the stream, looking at VOC emissions and other finer particulates that aren’t typically in the conversation in North America.”

Developing solutions
When Wendt began exploring the development of emission systems a couple of years ago, Willard says the company discovered that no technology was made specifically for shredders operating in the U.S. European auto shredders generally are smaller than their U.S. counterparts. They also don’t use the same feedstock. He says the U.S. market needed something more robust.
Wendt’s engineering team embarked on a project to address the issue. The company consulted with customers and with companies specializing in emission control systems for other industries. The result is a process that can be custom designed to meet the regulations auto shredder operators may encounter.
“It can be designed for anything from simply containing emissions from an auto shredder to particulate control to VOC control, and even far and above that,” Willard says. He adds that Wendt has relied on its expertise as a systems integrator in developing its technology, partnering with several companies.
Willard says he expects that the trend toward greater emission controls will continue. Wendt increasingly fields inquiries about these systems, either for adding to an existing shredder or including in proposals for new shredders, he says.
Metso, who manufactures the Texas Shredder and Lindemann brands of automotive scrap shredders, also offers dust-extraction emission control systems. It has partnered with R&R Beth, a dust removal and filtration specialist based in Bad Lobenstein, Germany. Metso has had an ongoing relationship with R&R Beth for several years, particularly in Europe. A global partnership, which includes North America, was finalized this year. Metso says the relationship with the company grew stronger in recent years in response to evolving regulations in Europe.
“We are their exclusive distributor globally, and our collaborative solution has been developed primarily through our team in Germany,” Carroll says. “Our primary system at this point is a dry-type system that uses duct work coming off of the top of the shredder box with various explosion-proof features. It’s fed through a primary cyclone, which pulls out any larger elements. That in turn is fed through secondary processes that eliminate most of the remaining particulates in the airflow,” he explains.
Emission control investment
Emission control is costly, but costs vary greatly because shredder sizes vary greatly. Also, solutions are not one-size-fits-all as regulations vary. One city might have a particulate regulation, while another might require nothing. Cost can be substantial, ranging from hundreds of thousands of dollars to millions of dollars, suppliers say.
Developing an emission control system for a particular shredder can be a long process, and it usually involves environmental consultants and local regulators. Willard says Wendt’s method is to work as a team with customers and consultants to develop a customized system. Attention must be paid to the regulations that may apply, and air permits may be required.
“It’s not the simplest process to go through,” Willard says. “Wendt has worked through this process a few times now and … we have been able to create a good process and develop a solid knowledge base to help educate our customers, the environmental consultants and local regulators to determine what’s needed and what’s not.”
The challenges in developing a system are many, sources say. Small explosions are an occasional occurrence in U.S. shredding plants when gas cans or propane tanks accidentally are fed into shredders.

“The thing about European shredders is that they are not as prone to explosions as U.S. shredders are, partly because of local regulations and feedstock control,” Willard says. “In the U.S. we have to design and plan for explosions on a shredder on a regular basis.”
System designers also have to consider the various climates where shredders are located. Control systems have to be able to operate in hot and cold weather.
Willard says Wendt’s systems can be modified as regulations dictate. “If two or three years down the road from now, one of our customers comes back and says the particulate control is doing a good job, but regulators are now requiring VOC controls, we can go in and add VOC control on the back end of the particulate control that’s already been in operation,” he says.
European and American emission control processes always have diverged, Carroll says. In Europe, it’s common to do dedusting via air extraction at the shredder, using either a wet or dry system that pulls the hot, dusty air out of the shredder box and runs it through a cleaning process. Carroll says Metso’s U.S. customers have leaned toward using water-injection systems in the shredder to control dust.
“In North America, we are still pretty far behind European standards,” he says. “In Europe, they have been getting further down the stream, looking at VOC emissions and other finer particulates that aren’t even in the conversation in North America. VOC reduction has been under investigation for many years, but there is no EU-wide consensus on what the standard should be.”
Metso advises auto shredder operators to stay involved in the regulatory process and understand the regulations that apply to their operating regions. Also, it is helpful to be proactive and have a good relationship with the regulatory agencies as they try to better understand auto shredder emission controls.

Explore the October 2019 Issue
Check out more from this issue and find your next story to read.
Latest from Recycling Today
- USTR announces phased measures designed to address China’s shipbuilding dominance
- APR, RecyClass release partnership progress report
- Clearpoint Recycling, Enviroo sign PET supply contract
- Invista expanding ISCC Plus certification program
- Redwood partnership targets recycling of medium-format batteries
- Enfinite forms Hazardous & Specialty Waste Management Council
- Combined DRS, EPR legislation introduced in Rhode Island
- Eureka Recycling starts up newly upgraded MRF