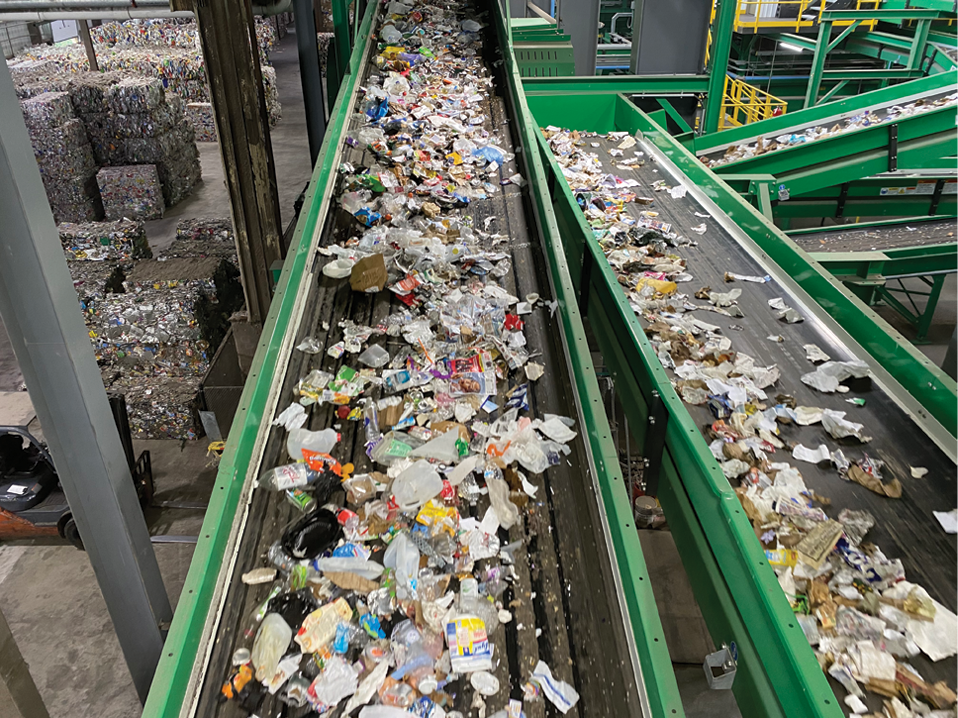
When Murphy Road Recycling announced plans to rebuild its material recovery facility (MRF) in Berlin, Connecticut, the All American MRF, in March 2021, it sought a processing system that would have the flexibility to adapt to ever-evolving consumer habits and recycling market conditions. With that in mind, Frank M. Antonacci, chief operating officer at Enfield, Connecticut-based Murphy Road Recycling, says the new MRF deliberately was designed to facilitate future upgrades.
“Things are changing every day, and it was nice to have that kind of forethought so we had areas where we could put all this new equipment,” he says.
“We always referred to the machine and operation as a living, breathing beast that would be always changing, along with the ever-changing material stream that we’re seeing. Once we got the initial equipment in—and it’s been working great—it allowed us to see more into the stream and what was available [to recover], and that allowed us to make some even more educated decisions on what additional equipment we wanted to add and what could make the people who are working there a little bit more efficient.”
In November of last year, Murphy Road Recycling took advantage of that preplanning and installed three additional optical sorters, modified two optical sorters and added 15 Greyparrot Analyzers, as well as an additional magnet on its glass line.
The installation of the new equipment was done over a weekend, and when the system started up the following Monday, Antonacci says the disruption was minimal.
Improved visibility and actionable data
To further improve visibility into the material streams the All American MRF processes, Murphy Road Recycling added artificial intelligence, or AI, units by London-based equipment manufacturer Greyparrot.
Supplied and installed by Norwalk, Connecticut-based Van Dyk Recycling Solutions, the systems integrator Murphy Road Recycling worked with on the original MRF redesign, the AI-enabled Greyparrot Analyzers are positioned above conveyor belts in the MRF and use cameras to capture images and produce data on material flows. The Greyparrot Analyzers are installed on all the outbound commodity lines as well as on the two infeed lines and the outbound trash line.
Antonacci says the units help the company understand the composition of incoming material and make it easier to see when something is amiss.
“If an eddy current’s down, and we’re starting to see more contamination in our aluminum, we’re going to know it right away instead of seeing it in a week, two weeks [or] a month when we start seeing those types of reports,” he says.
With the scale of All American’s operations, processing up to 1,000 tons per day, decreased efficiency and losing materials such as old corrugated containers (OCC) to downgraded commodity streams like mixed paper compound quickly.
The All American MRF processes material from Connecticut and Massachusetts—both bottle bill states. However, Antonacci says the program in Connecticut is more expansive than in Massachusetts, with a 10-cent deposit versus a 5-cent one and covering a a broader range of beverage types. He adds that by using the Greyparrot Analyzers, the MRF can better understand differences in the material streams from its customers in those two states and learn whether it’s better from a processing standpoint to blend those loads or keep them separated.
“It gives us a little bit more insight while we’re still running a high-input and -output facility,” Antonacci says.
In the future, he says, Murphy Road can use data gleaned by the AI to alert third-party haulers and communities about contamination in incoming loads of recyclables more quickly than it can now, allowing the company to get in front of potential problems rather than having to reverse engineer the source of an issue months later.
“But I think the biggest opportunity is knowing if a machine is falling out of tune someplace,” Antonacci says. “If you think about it, when you’re dealing with 250,000 tons a year and you have more OCC going in with mixed paper—a 5 percent increase in that over even one day is a meaningful dollar amount.”
Before the addition of the AI, Antonacci says it could have taken the MRF’s operators a week or more to see outbound reports that would reveal such an issue.
“But if we could see it in real-time in the data from the Greyparrots, it’s a huge opportunity for us to say, ‘OK, we have to go optimize that optical’, or ‘We’ve got to look at those screens; they need to be changed out,’ or ‘There’s a jam someplace that’s purging material in the wrong place,’” he says.
Murphy Road still is learning how to tap into all the data from its Greyparrots, with Antonacci saying, “You have all this data—how do you best utilize it? That’s a work in progress.”
He adds that while equipment manufacturers and vendors have ideas about the data MRF operators want to see, it’s important for operators to talk about their expectations with them.
“Seventy-five percent of the time, that might be the case, but what we’ve found is that if you’re not having dialogs on what’s really important, you might not get exactly what you need,” he says.
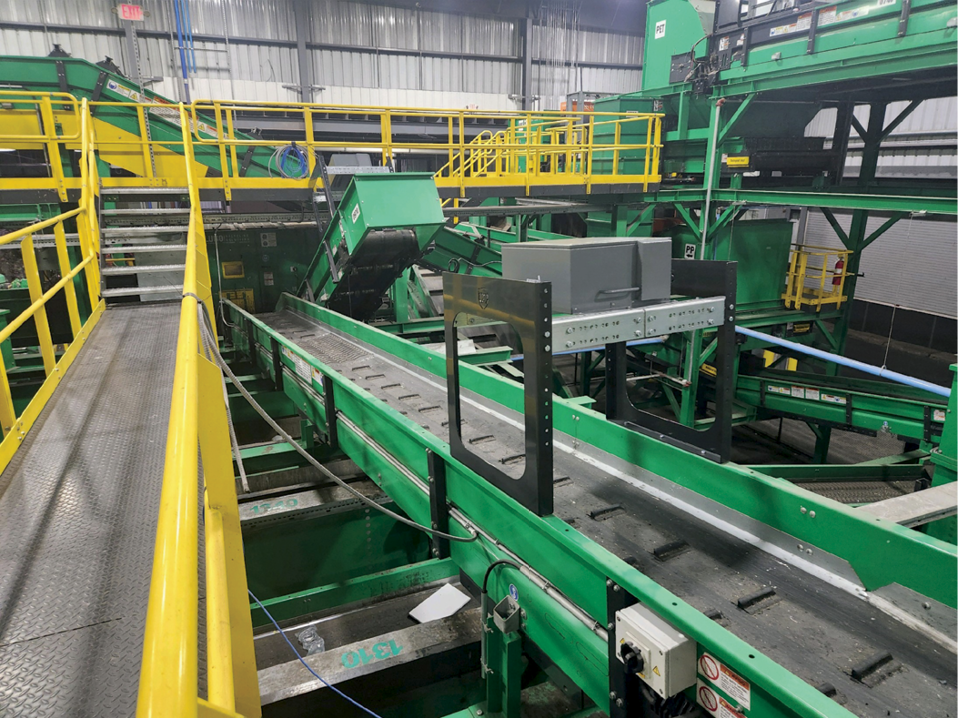
Modifications and additional opticals
With the recent upgrades, Murphy Road installed three optical sorters to add to the 11 it already operated, enabling it to get more OCC out of the mixed paper and to recover small paper from the glass system to put back into the paper stream instead of losing it as contamination.
“It’s been very successful, and it’s actually helped clean up the glass,” Antonacci says of these additions. “It just has a lot of knock-on positive results.”
An optical sorter, Optical Unit No. 12, was added on the container line to remove fiber that ends up blended with the backs from the 330 screens to ensure recovery of that fiber prior to sending the bottles and cans to the ballistic sorting unit.
“By removing the fiber, we were able to reduce the amount of the material being sent to the elliptical sorting unit to increase the efficiency of the elliptical sorting unit,” he says.
The second optical sorter, Optical Unit No. 13, was added to process ejects from the two optical units that process recyclables after the large paper screens, ejecting OCC, which is sent to the OCC bunker.
Optical Unit No. 13 is followed by Optical 14, which is fed using a new disc spreader to ensure proper presentation of the material. This optical unit processes the recyclables that remain after the OCC has been removed by Optical Unit No. 13.
“Optical Unit No. 14 ejects all the fiber, allowing for the production of a high-quality mixed paper, and sends the remaining recyclables, mostly bottles and cans, to the bottle and can sorting lines for further processing,” Antonacci says.
The All American MRF also modified two of its existing Tomra optical sorters that process overs from the larger paper screens, adding Deep Laiser, a laser sensor that works in concert with the machine’s other sensors to detect items on the conveyor belt that the near-infrared technology cannot identify, such as black plastics and glass.
“The reason for these additions was to allow the optical sorting units to recognize any black plastic that might have carried over the 440 screens,” Antonacci says. “Prior to the retrofit, these ... units were programmed to eject everything but newspaper/white paper but could not see any black plastic without Deep Laiser. With the addition of the Deep Laisers, the opticals can now recognize black plastic and eject it for further processing. This reduces the amount of the nonfiber that needs to be removed manually by QC [quality control] personnel, ensuring a clean commodity for end markets.”
Problems solved
The new technology has enabled the All American MRF to sort items that previously presented challenges, such as Fairlife milk bottles—white polyethylene terephthalate (PET) that is covered by a full multilayer plastic sleeve to protect the milk from light and degradation.
Before the recent upgrades, these bottles were sent to the recirculation line because the opticals couldn’t figure out what kind of plastic they were.
“We were able to train our opticals on the specific packaging by name,” Antonacci says, effectively sorting them with the PET. “Those kinds of wrapped plastic bottles are very confusing for the machines … because a lot of times the wrap is different than the actual material of the bottle.”
In addition to allowing the sorting of these bottles, black plastics and improving OCC and paper recovery, the All American MRF has seen other benefits since its November retrofit.
“It has definitely decreased the amount of quality control that we need to do manually,” Antonacci says.
“We have great quality. We’re not getting any kind of leakage from higher-value commodities to lower-value ones, so I think we’re getting more full value for this stream” and ensuring that materials go to their highest and best use.

Explore the March 2025 Issue
Check out more from this issue and find your next story to read.
Latest from Recycling Today
- Radius to be acquired by Toyota subsidiary
- Algoma EAF to start in April
- Erema sees strong demand for high-volume PET systems
- Eastman Tritan product used in cosmetics packaging
- Canada initiates WTO dispute complaint regarding US steel, aluminum duties
- Indianapolis awards solid waste contract, updates recycling drop-off program
- Novelis produces first aluminum coil made fully from recycled end-of-life automotive scrap
- GPR’s hubbIT platform recognized in Georgia State University’s Marketing Awards for Excellence in Innovation