
The European steel sector is undergoing a significant transformation in the face of evolving environmental regulations and a need for sustainability. This shift from traditional blast furnace- (BF-) based operations to electric arc furnace (EAF) methods marks a pivotal change in the region’s steel production and aligns with the EU’s ambitious climate goals.
The driving force
The European Green Deal has a goal for the EU to become carbon neutral by 2050, pushing steelmakers toward more sustainable practices by encouraging the use of scrap. The region eyes an 80 to 95 percent reduction in CO2 emissions by 2050 compared with 1990 levels. These measures also aim to lower emissions from current levels to between 62 million to 15 million tons in the time frame under consideration.
Alongside the Green Deal, carbon taxes and environmental regulations make emitting carbon more expensive, incentivizing companies to switch to cleaner steelmaking methods. BF technology, which uses coke and coal to smelt iron ore, is energy-intensive and produces significant carbon emissions. EAFs, however, use scrap and electricity, reducing energy consumption and emissions.
The introduction of carbon taxes across Europe adds a financial dimension to the environmental imperative, making the transition to EAF technology not just an environmental decision but an economic one. These taxes are poised to have a profound impact on the steel industry, altering cost structures and influencing production decisions.
EAFs in the making
Steel companies across the EU have embraced these directives, and some are at the forefront of adopting EAF technology and other clean methods to produce low-carbon steel.
ArcelorMittal, based in Luxembourg, and Thyssenkrupp, based in Germany, are among the pioneers in this shift, demonstrating the viability and benefits of EAF use. Their success has set a benchmark, encouraging others to plan for a similar transition, and this widespread movement toward EAF technology highlights the steel industry’s collective effort to achieve sustainable production.
By 2030, India-based Tata Steel plans to operate one direct-reduced iron (DRI) unit and one EAF, with a goal to phase out all BF and coke plants by 2037, aiming for carbon neutrality. Tata Steel’s strategy includes maintaining its annual 5 million-ton production capacity while transitioning to green steel, with an initial goal to shift 40 percent of its production to green steel by 2030 and achieve 100 percent by the end of Phase 2, according to Martin van de Velde, a spokesperson at Tata Steel Netherlands.
The company also aims to boost its use of scrap from 15 percent to 30 percent posttransition, enhancing its circularity and integration within the local economy by sourcing from regional suppliers.
Tata Steel UK also has plans to decommission its BFs and transition to an EAF that is expected to start production in 2027. It also plans to replace its two BFs at Port Talbot with an EAF, which will have annual crude capacity of 3 million metric tons. This change is expected to cut the facility’s listed crude capacity by 40 percent. The blast furnaces at Port Talbot currently produce about 4.8 million metric tons of pig iron and have two basic oxygen furnaces (BOFs) with an annual capacity of 5 million metric tons of crude steel. This move is part of a broader strategy to cut CO2 emissions and achieve net-zero steel production by 2045. The new EAF will notably reduce carbon emissions by using local scrap.
Salzgitter’s SALCOS project in Germany focuses on replacing BFs with DRI plants, marking a major investment toward green steel production. The first stage of the project includes a DRI plant with 2 million metric tons of annual capacity, an EAF with 1.9 million metric tons of crude steel capacity per year and an electrolysis unit to produce up to 200 normal meters cubed per hour of hydrogen with a nominal output of 720 kilowatts alternating current.
Similarly, the HYBRIT project, a collaboration between Swedish companies SSAB, LKAB and Vattenfall, is pioneering hydrogen-based steel production, with test production underway. The HYBRIT demonstration project plans to realize the breakthrough of fossil-free steel production by developing a complete, new value chain based on fossil-free hydrogen, resulting in annual production of 1.2 million metric tons of crude steel.

H2 Green Steel, also of Sweden, aims to establish a DRI unit powered by green hydrogen, setting a benchmark for the future.
London-based Liberty Steel’s plans to install EAFs at its Czech and Romanian plants further signify the shift toward carbon-neutral operations. Liberty Steel’s plants in the Czech Republic have an annual liquid steel production capacity of 3.6 million metric tons, and its Ostrava mill will install two hybrid EAFs with a combined annual production capacity of 3.5 million metric tons. The Romanian plant can produce 4 million metric tons per year, and Liberty plans to install two EAFs with a combined production capacity of 3 million metric tons of unrefined steel per year.
ArcelorMittal is investing heavily in hydrogen-based steelmaking in Germany, including a new DRI and EAF plant at its Bremen site, showcasing the company’s commitment to green steel. It plans to use green hydrogen made using renewable energy to produce up to 3.5 million metric tons of steel annually at the Bremen and Eisenhuttenstadt sites by 2030, with significantly lower CO2 emissions.
Austria-based Voestalpine’s plan to transition to EAF technology by 2027 highlights the broader industry trend toward sustainable steel production. The new EAF at its Donawitz, Austria, plant will produce 850,000 metric tons of green steel annually. This is part of the company’s Voestalpine Greentec Steel plan, which aims to reduce emissions by approximately 30 percent by transitioning to this technology. Voestalpine also is applying a mix of EAF, BF/BOF and DRI technologies at its Linz, Austria, site. This facility will have 1.6 million metric tons of green steel capacity per year, with the new EAF commissioning in 2027.
Others are following suit. For example, the Celsa Group in Barcelona, Spain, focuses on projects like Steellowcarbon and Circular Steel to reduce resource use and promote a circular economy within steelmaking. Acerinox Europa in Andalucía, Spain, also is transitioning to green hydrogen, replacing natural gas in its stainless-steel production.
Italy-based Tenova S.p.A. is set to supply a DRI tower and EAF for Italian multinational consulting engineering research, development, inspection and certification company RINA’s Italian steel project. The project aims for hydrogen-powered steel production by 2025, targeting up to 7 tons of steel per hour, or 61,320 metric tons per year.
This collective move toward EAF technology and green steel production underlines the steel industry’s dedication to environmental sustainability and its proactive response to global climate change challenges.
Andre Esterhuizen, general manager of sales and marketing at Italy-based Tenova Pyromet, notes the challenges of this transition, including economic pressures, raw material shortages and geopolitical tensions affecting gas availability. He says moving away from the conventional BF/BOF route, which contributes a large portion of the industry’s CO2 emissions, has major emissions reduction potential.
“Transitioning to a gas-based direct reduction and EAF route, coupled with the use of hydrogen, offers a promising path for substantial emissions reduction,” he says. “Tenova’s efforts in developing productive DRI-fed EAFs highlight the industry’s proactive approach to embracing cleaner steel production technologies.”
Near-term challenges
However, the transition to EAF-based steelmaking, given the tight timeline, is cost-intensive and includes substantial technical adjustments. Moreover, EAFs require more electricity with estimates pointing to a need for around 400 trillion watt hours of CO2-free energy yearly for this region. Energy needs and fluctuating costs of raw materials like ferrous scrap could raise operating costs for steelmakers by 10 to 35 percent.
According to 2021 research by New York-based McKinsey & Co., Europe’s steel sector faces three challenges in its journey toward decarbonization:
- structural overcapacity as COVID-19 impacts and industry shifts could lead to a long-term capacity utilization of only 70 percent to 75 percent.
- rising CO2 costs, potentially reaching 50 to 100 euros per metric ton by 2030, meaning steelmakers must invest in new technologies; and
- investments in decarbonization that could require as much as 100 billion euros by 2050.
Still, transitioning to EAFs offers opportunities to meet Europe’s growing demand for sustainable steel, improve the industry’s environmental reputation and attract green investment.
European policies and incentives, including renewable energy subsidies, tax breaks for green investments and support for the circular economy, encourage the adoption of EAFs.Despite challenges, the transition to EAF technology in Europe’s steel industry represents a crucial step toward increased sustainability. With policy support and industry innovation, this transition will offer a pathway to reduced CO2 emissions, greater economic efficiency and a more sustainable future.
Get curated news on YOUR industry.
Enter your email to receive our newsletters.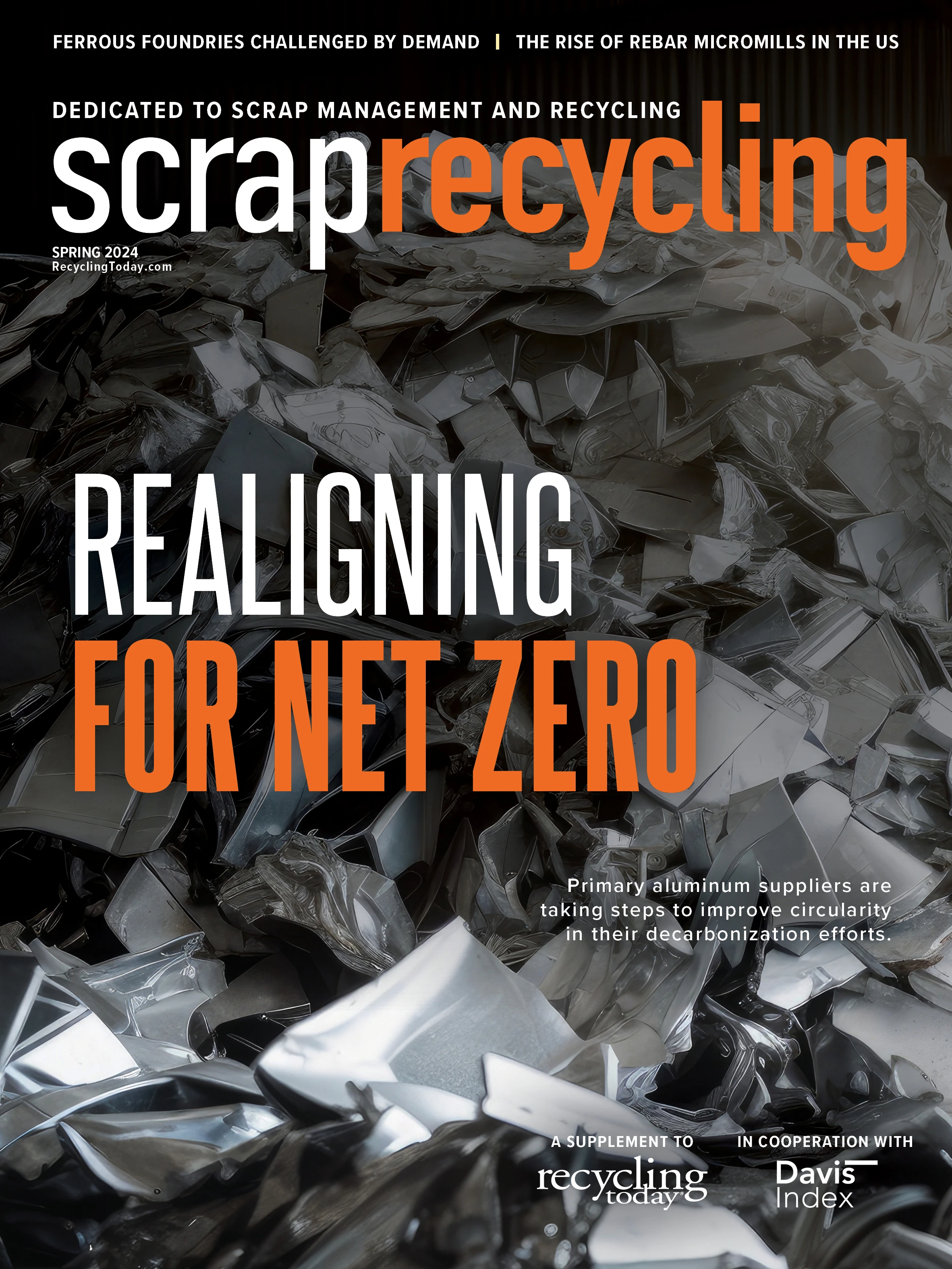
Explore the Spring 2024 Scrap Recycling Issue
Check out more from this issue and find your next story to read.
Latest from Recycling Today
- Athens Services terminates contract with San Marino, California
- Partners develop specialty response vehicles for LIB fires
- Sonoco cites OCC shortage for price hike in Europe
- British Steel mill’s future up in the air
- Tomra applies GAINnext AI technology to upgrade wrought aluminum scrap
- Redwood Materials partners with Isuzu Commercial Truck
- The push for more supply
- ReMA PSI Chapter adds 7 members